Top 3 Manufacturer in China
hydraulic test point hose supplier
SGS Approved
what are the types of Hydraulic hose assembly and fittings?
With the rapid development of China’s construction machinery, the reliability of hydraulic hose assemblies has become one of the most concerned issues in the industry.
The hydraulic hose assembly is a basic element in the hydraulic transmission system. The quality of the hose assembly directly affects the performance of the hydraulic system and the main engine. Part of the failure of the hose assembly comes from the structure of the joint core.
The hose connector core is mainly divided into two parts, one is the connection structure, mostly based on SAE standards, ISO standards and KES standards; The other part is the structure of the crimping part (tail structure), which is matched with the outer jacket and the inner and outer rubber layers of the hose to form a reliable crimping deformation to meet the performance of the hose assembly.
If the structure of the joint core crimping part is unreasonable in the design of different types of hoses, product quality problems will occur to a large extent.
Therefore, the types of (designed) joint cores selected for hoses in different working environments are also different, and a reasonable design can avoid or reduce the occurrence of failures.
1. Types and characteristics of hose fittings
Throughout the entire hose assembly industry, there are mainly two types of reliable connections between hose joints and hoses: full withhold hose joints and detachable hose joints.
The full crimping joint is a process in which the eight-part crimping module of the crimping machine uniformly squeezes the hose joint to a certain extent after assembling the joint core, hose and outer jacket, so that the hose joint and the hose become a whole.
The detachable hose connector compresses the hose through the connector core with the outer cone and the connector core, so that the hose is close to the inner cone of the connector sleeve, forming a connection with a greater binding force.
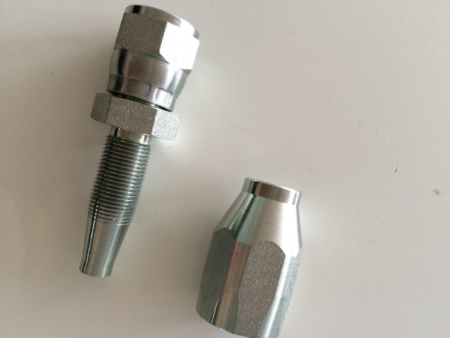
1.1 Hose crimping form and characteristics
The type of withholding of the hose mainly depends on the type of hose (or the size of the inner and outer rubber) and the pressure environment of the hose assembly.
It is mainly divided into three categories: non-peeling rubber crimping, peeling outer rubber crimping, and inner and outer rubber peeling crimping.
The characteristics of each type are:
(1) Non-peeling and crimping: The inner and outer rubber of the hose does not need to be stripped, and the product can be completed by crimping after the hose is installed. The processing technology is simple.
This type of crimping is often used for steel wire braided hoses with relatively thin outer rubber layers such as GB/T3683, EN853 and SAE standards.
(2) Stripping and crimping: It is necessary to strip off the outer rubber layer of the hose to a certain length (the outer rubber layer is thicker), which is used to better make the steel wire reinforcement layer contact with the tooth groove of the jacket.
When the jacket shrinks and deforms under external force, it will firmly buckle the steel wire, thereby preventing the joint from pulling out when subjected to high pressure impact.
This type of crimping is mainly applicable to steel wire wound hoses such as GB/T10544, EN856, and SAE standards.
(3) Internal and external rubber stripping and crimping: the inner and outer rubber layers need to be stripped to a certain length (the thickness of the inner and outer rubber), the steel wire layer and the inner rubber layer are extruded into a wave shape, generally suitable for GB/T10544, EN856-R13, R15, etc. Specifications (32 or more including 32) ultra-high pressure steel wire spiral hose.
1.2. Withholding type hose connector
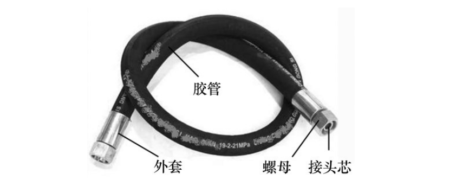
Withholding type hose joint is mainly composed of joint core, outer jacket (nut is an optional part) and other parts.
1) Joint core materials, types and characteristics
Commonly materials used for joint cores are 20, 35, and 45 steels. For straight joint cores, 35 and 45 steels are often used, which have strong resistance to deformation. Considering the manufacturability of bending joint cores, 20 or 35 steels are generally used.
With the popularization of hot bending technology, 35 and 45 steels can also be used for elbow joint cores.
The structural characteristics of the joint core are closely related to the hose crimping form, and according to the regularity of the structure, the types of joint cores are roughly divided into: zigzag structure, rectangular structure, internal locking structure, etc.
(1) Sawtooth structure joint core, commonly known as barbed type, is mainly composed of sawtooth grooves, and the angle between the hypotenuse and the axis is generally not more than 20°.
The top of the serration is arc-shaped or flat, and the plane and the short side of the serration are smooth rounded corners (0.2~0.5mm) to prevent damage to the inner rubber layer of the hose during assembly and crimping.
The joint core of this structure has strong sealing and pull-off resistance, and is mainly used for steel wire-wound rubber hoses.
(2) Rectangular structure joint core: mainly composed of several rectangular grooves, 5~7 groove bodies form a sealing groove, and the groove depth is generally 0.3~0.6mm.
The transition surface between the top of the groove and the bottom of the groove is generally smooth with rounded corners, with a radius of 0.1mm~0.3mm.
Prevent damage to the inner rubber layer of the hose during assembly and crimping. The overall structure is simple, with good sealing performance, but low pull-out resistance. This structure is often used for resin hoses, steel wire braided hoses and other types of hoses.
Commonly materials used for joint cores are 20, 35, and 45 steels. For straight joint cores, 35 and 45 steels are often used, which have strong resistance to deformation. Considering the manufacturability of bending joint cores, 20 or 35 steels are generally used.
With the popularization of hot bending technology, 35 and 45 steels can also be used for elbow joint cores.
The structural characteristics of the joint core are closely related to the hose crimping form, and according to the regularity of the structure, the types of joint cores are roughly divided into: zigzag structure, rectangular structure, internal locking structure, etc.
With the rapid development of China’s construction machinery, the reliability of hydraulic hose assemblies has become one of the most concerned issues in the industry.
The hydraulic hose assembly is a basic element in the hydraulic transmission system. The quality of the hose assembly directly affects the performance of the hydraulic system and the main engine. Part of the failure of the hose assembly comes from the structure of the joint core.
The hose connector core is mainly divided into two parts, one is the connection structure, mostly based on SAE standards, ISO standards and KES standards; The other part is the structure of the crimping part (tail structure), which is matched with the outer jacket and the inner and outer rubber layers of the hose to form a reliable crimping deformation to meet the performance of the hose assembly.
If the structure of the joint core crimping part is unreasonable in the design of different types of hoses, product quality problems will occur to a large extent.
Therefore, the types of (designed) joint cores selected for hoses in different working environments are also different, and a reasonable design can avoid or reduce the occurrence of failures.
With the rapid development of China’s construction machinery, the reliability of hydraulic hose assemblies has become one of the most concerned issues in the industry.
The hydraulic hose assembly is a basic element in the hydraulic transmission system. The quality of the hose assembly directly affects the performance of the hydraulic system and the main engine. Part of the failure of the hose assembly comes from the structure of the joint core.
The hose connector core is mainly divided into two parts, one is the connection structure, mostly based on SAE standards, ISO standards and KES standards; The other part is the structure of the crimping part (tail structure), which is matched with the outer jacket and the inner and outer rubber layers of the hose to form a reliable crimping deformation to meet the performance of the hose assembly.
If the structure of the joint core crimping part is unreasonable in the design of different types of hoses, product quality problems will occur to a large extent.
Therefore, the types of (designed) joint cores selected for hoses in different working environments are also different, and a reasonable design can avoid or reduce the occurrence of failures.
(3) Internal locking structure joint core, also known as anti-pull-out structure.
This type of structure is specially designed to prevent the hose from being pulled out of the hose joint, and the tightness is ensured by the rectangular structure.
Therefore, the inner locking structure joint core is actually a combination of the anti-pull-out structure and the rectangular structure.
This kind of joint has the characteristics of high reliability and long service life. It is mainly used for ultra-high pressure and large diameter steel wire winding hose and dynamic steel wire winding hose assembly under harsh working conditions.
2) Outer cap material, type and characteristics
The material of the outer jacket is generally 20 steel, and the good plastic deformation of the material is used to make the outer jacket tooth extruded rubber tube and the joint core sealing fit.
There are also many types of outer caps, mainly for different joint cores, different working environments, different specific working conditions, and different structural forms required.
Usually the inner side of the jacket is made up of some grooves or serrations. There are square grooves, trapezoids, zigzags, etc., which need to be used in conjunction with different types of joint cores.
The commonly used structure types of outer caps are roughly divided into the following three types:
(1) Wave-shaped tooth groove jacket. The outer surface of the wavy jacket is mainly a smooth cylinder, and the angle between the hypotenuse of the inner tooth and the axis is 25°~45°.
The radial side and the hypotenuse are connected by rounded corners of 0.2~0.5mm, generally composed of 3~5 internal teeth. Mainly suitable for non-peeling medium and low pressure hose assemblies, such as resin tubes and steel wire braided hoses; It can be used in conjunction with sawtooth structure and rectangular structure joint core, with weak pull-out resistance and simple processing technology.
(2) Trapezoidal tooth groove jacket. The outer surface is a smooth cylinder, and the inner surface is a groove with a certain number of trapezoidal teeth.
The angle between the hypotenuse and the axis is 25°~45°, and each serration is a rectangular groove. The top of the serration is a plane with a width of 1 to 2mm, and the sharp corners are transitioned with a rounded corner of 0.2mm.
It can be used in conjunction with a rectangular structure joint core to form an effective pull-out resistance, suitable for stripping medium and high pressure braided pipes and winding pipes.
(3) Compound alveolar cover. The outer surface is a T-shaped groove corresponding to the internal tooth dislocation, and the inner surface is a groove with a certain number of bilateral trapezoidal teeth.
It is suitable for use with the inner locking structure joint core and is used for ultra-high pressure and big flow rate hose assembly.
With the gradual development of large-scale construction machinery, the hydraulic system is also constantly developing in the direction of high pressure, and the application of this structural form is becoming more and more extensive.
2. Selection of the amount of joint crimping
According to different hose types and joint types, the appropriate crimping amount is also a key factor to ensure that the hose assembly is trouble-free.
The amount of crimping directly affects the sealing performance, pull-off strength and service life.
Generally, when judging the quality of the crimping deformation, see whether the gap between the inner tooth surface of the outer sleeve and the tooth groove of the joint core is filled by the rubber tube.
Only when the deformation is satisfied can the pull-out resistance and sealing performance be guaranteed.
Generally speaking, the crimping amount of inner rubber hose such as nitrile rubber should make the inner rubber layer compression (40%~45% for steel wire braided hose, 50%~55% for four-layer and six-layer steel wire wound hose); The crimping amount of the resin tube and the PTFE hose ensures that the compression amount of the inner rubber layer is 25% to 30%.
In the case of ensuring the seal, the smaller the amount of withholding, the better. Through calculation and verification, a certain amount of withholding is selected.
3. Conclusion
The article discusses the types of joint cores and outer caps used in the withholding hose assembly.
When the hose crimping has quality problems and the types of failures.
Analyzed the reasons and how to use reasonable crimping configuration and crimping joints, in order to avoid the problem of low hose assembly performance caused by unreasonable hose crimping structure.
Effectively improve and control the reliability of the hose assembly, and also provide strong support for the rapid development of various hydraulic engineering machinery.
Benefits You Can Find In Ikin
factory Price and low moq
reliable quality, supplier for Eaton, Hawee and so on
100% leakage Inspection Before finished
3 years warranty
10 working days for bulk shipping
match other fittings like minimess, stauff and so on
cone seal design structure, stable and long life
Get Your Free Sample
in 2 days
*We respect your confidentiality and all information are protected.