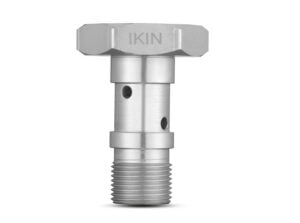
How to Correctly use hydraulic self-sealing connectors and troubleshoot?
With the development of construction machinery, there are more and more types of hydraulic machinery, so it is inevitable that many mechanical failures will be encountered.
Because of the different positions, the required accessories are also different, including hydraulic self-sealing joints.
In the process of using hydraulic self-sealing joints, failures will inevitably occur.
1. Common troubleshooting
(1) One side is conducting and the other side is cut off during operation,The reason is mostly caused by the difference in spring force of the two ball valve springs.
When the oil circuit is connected, the steel ball on the side with the smaller elasticity returns a long distance. The steel ball on the side with greater elasticity is not returned, and the ball valve on this side is still closed.
In addition, this failure can also occur when a side of the steel ball is stuck by debris.
The elimination method is to remove the self-sealing connector. Twist the adjusting bolts to make the springs on both sides consistent;When the steel ball is stuck by sundries, the ball valve should be disassembled to remove sundries, and then reinstalled after washing.
(2) All pipelines on both sides are cut off during operation. The reason is that the elastic force of the springs on both sides is too weak, which makes the steel ball automatically cut off under the action of hydraulic force.
If the oil flow is blocked, or the internal wear of the self-sealing joint is worn, the two steel balls cannot push each other apart during normal installation.
The troubleshooting method is to turn the adjusting screw to increase the spring pre-tightening force or replace the spring;
When installing the self-sealing joint, add a gasket between the two steel balls to push the two steel balls apart.
2. use correctly
(1) The gasket between the self-sealing joint and the hydraulic oil pipe joint should be kept intact. If the gasket is lost, reinstall it in time. To prevent oil leakage and air intake.
(2) When connecting the pipeline, firstly wipe the butt end of the joint body assembly and the joint sleeve assembly clean.
Then push the connecting sleeve inward. Then insert the joint body assembly into the joint sleeve assembly, and finally loosen the coupling sleeve.
The locking steel ball is dropped into the groove of the joint body and locked to ensure that the two ball valves compress the spring at the same time and push each other open to connect the oil circuit.(Note: The sealing ring between the joint body and the joint sleeve should be kept intact.)
(3) When disassembling the pipeline, push the connecting sleeve inward.
Push inward from the joint sleeve and pull out the joint body assembly from the joint sleeve assembly.
The two ball valves simultaneously quickly close the leakage of the joint sleeve assembly and the mixing of air under the action of the spring.
(4) When the self-sealing joint is disconnected, it is strictly forbidden to load the pipeline through the control handle to prevent damage to the joint or bursting of the oil pipe.
(5) In order to prevent the self-sealing joint from being contaminated by dust and muddy water, it is best to wrap the joint with a plastic bag; When the connector is disconnected, cover the connector body and connector tightly with a cloth or plastic bag.
conclusion
When the hydraulic self-sealing joint fails, do not blindly repair it.
Using it in the correct way can greatly reduce the cost of machinery and reduce unnecessary troubles.
IKIN FLUID, your hydraulic test fittings supplier :
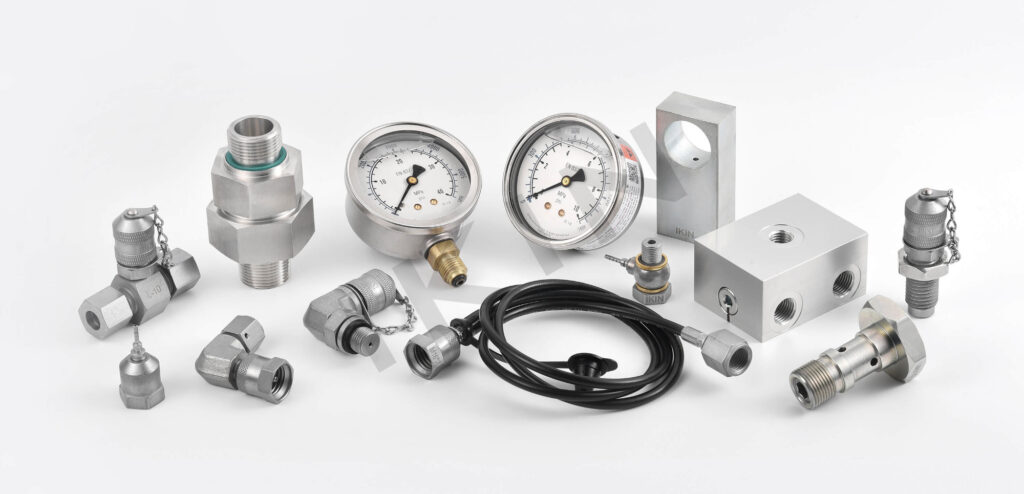