What is the common leakage problems and possible causes of Hydraulic Testings?
As an important tool for pressure testing and sampling in hydraulic systems, hydraulic test point are widely used.
However, establishing a reliable and leak-free connection should be the primary goal of any hydraulic system.
There are many different kinds of hydraulic testings on the market can be selected. No matter which type , it will bring inconvenience and trouble to the entire system when leaked.
Common leakage problems and possible causes of hydraulic testings:
How to Avoid Middlemen and Find Quality Pressure Test Fitting / Pressure Test Hose Manufacturers in China
How to Avoid Middlemen and Find Quality Pressure Test Fitting / Pressure Test Hose Manufacturers in China In today’s fast-paced industrial environment, finding the right supplier for hydraulic pressure test
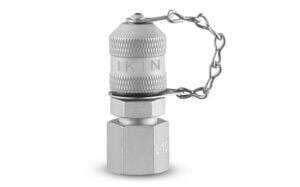
Is test point adaptor necessary for hydraulic system?
Is test point adaptor necessary for hydraulic system? The hydraulic system is very complicated. During the flow of hydraulic oil, the erratic flow direction and flow rate of the liquid
1. When the oil leaks from the inlet end, possible reasons for this region leaks as follows:
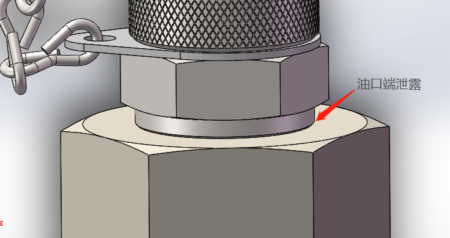
①O-ring/sealing ring is damaged or missing (For O-ring joint / seal ring)
The unreasonable design of the sealing ring and the sealing groove will cause the compression of the sealing ring to be too large or too small; if it is frequently disassembled, the surface of the sealing ring may be worn, slag and not pressed tightly.
When the use time is too long to exceed the shelf life, the ring loses its sealing, elasticity, deformation and cracks, etc., so it is easy to leak.
② The size of the connecting thread of the joint body is poor
The connecting thread of hydraulic testings is selected according to the thread of the oil port end.
The external thread connection length of hydraulic testings should be less than the full thread depth of the internal thread of the oil port end. Otherwise, the thread of the column end will not be screwed to the bottom, resulting in leakage of the threaded end.
③ The oil port end is damaged
Scratches on the sealing surface of the O-ring at the port end will prevent the O-ring from effectively sealing, resulting in leakage; the edge of the O-ring sealing surface is too sharp or burrs, and it is easy to cut the O-ring during installation and cause leakage;
④ Improper torque / improper assembly
After torque assembly, make sure that the end face of the joint seal is in full contact with the end face of the oil port. If there is a slight gap, the O-ring is likely to be squeezed out during the system’s long-term pressurization process, resulting in leakage.
IKIN hydrauic test point, 100% leakage testing before package.
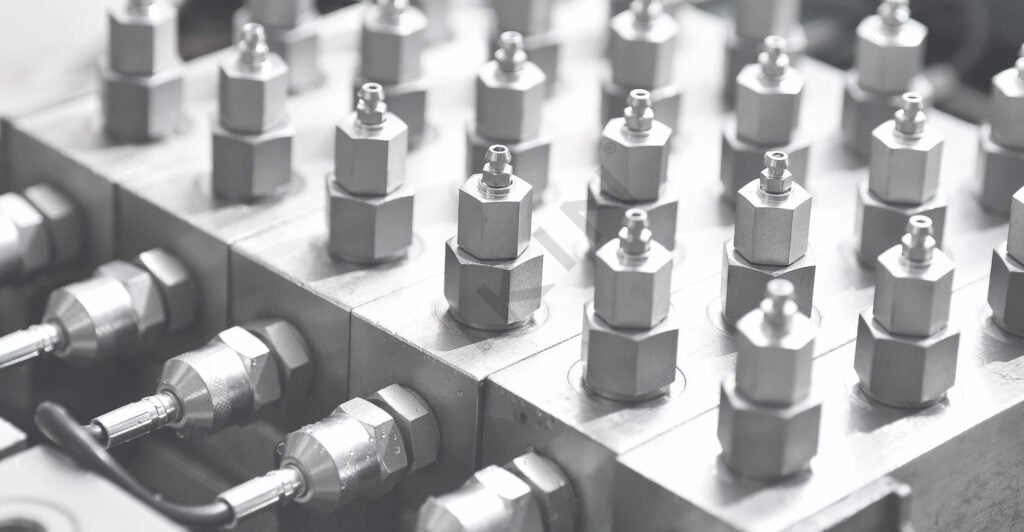
2. Leakage in the center of the spool. The possible causes of leakage in this area are as follows:
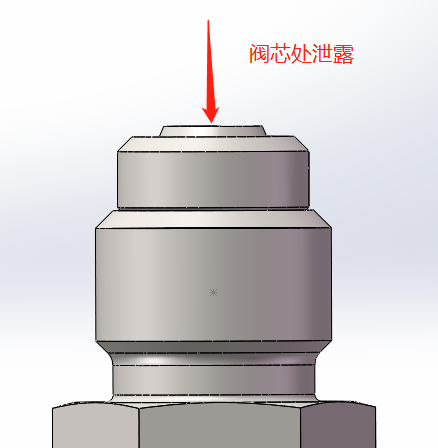
① Excessive pressure
According to the international standard ISO 15171-2, the maximum working pressure of hydraulic testings is 63Mpa (630bar). If the system pressure is too high (the maximum pressure exceeds the limit), the valve core will be damaged by a huge impact, which will cause hydraulic testings to leak.
② Damage of internal seal
When impurities enter the hydraulic system and the pressure is tested, these impurities will damage the internal seals of hydraulic testings, and will also affect the service life of the entire hydraulic system.
IKIN FLUID is manufacturer in China, specizlize in test fittings, 100% leakage testing before package
ODM/OEM/customized accepted.
click the below links to get more specification

TP Direct Pressure Gauge Connector for Hydraulic
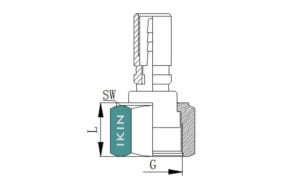
microbore hose fittings, with ORFS female thread

hydraulic test hose

check coupling, with stand pipe

Test Coupling with Stud
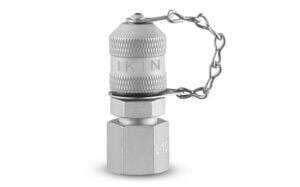
Test Point Coupling with Male Cone DKO-24°

Hose Connector Fittings, JIC 37°, with Male Thread

Hydraulic Hose Coupling, with Banjo Fitting Connection
3. Leakage caused by cracks. The possible reasons for leakage in this area are as follows:
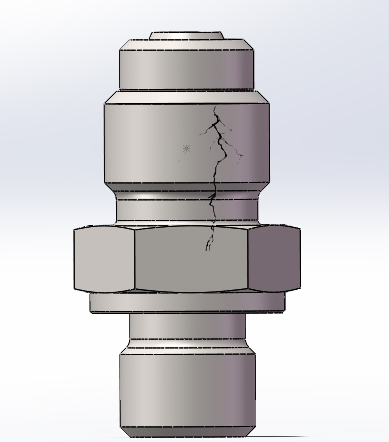
① The wall thickness is too thin
When the design wall thickness of some parts of the hydraulic test point joint is too thin, and there is stress concentration, the thin-walled part will be broken or cracks will cause leakage.
② Inferior quality materials
Choosing low-quality materials may cause small cracks in the joint body, but these cracks will be difficult to find after electroplating.
Therefore, hydraulic testings body will expand and crack under the constant pressure of the system, resulting in leakage.
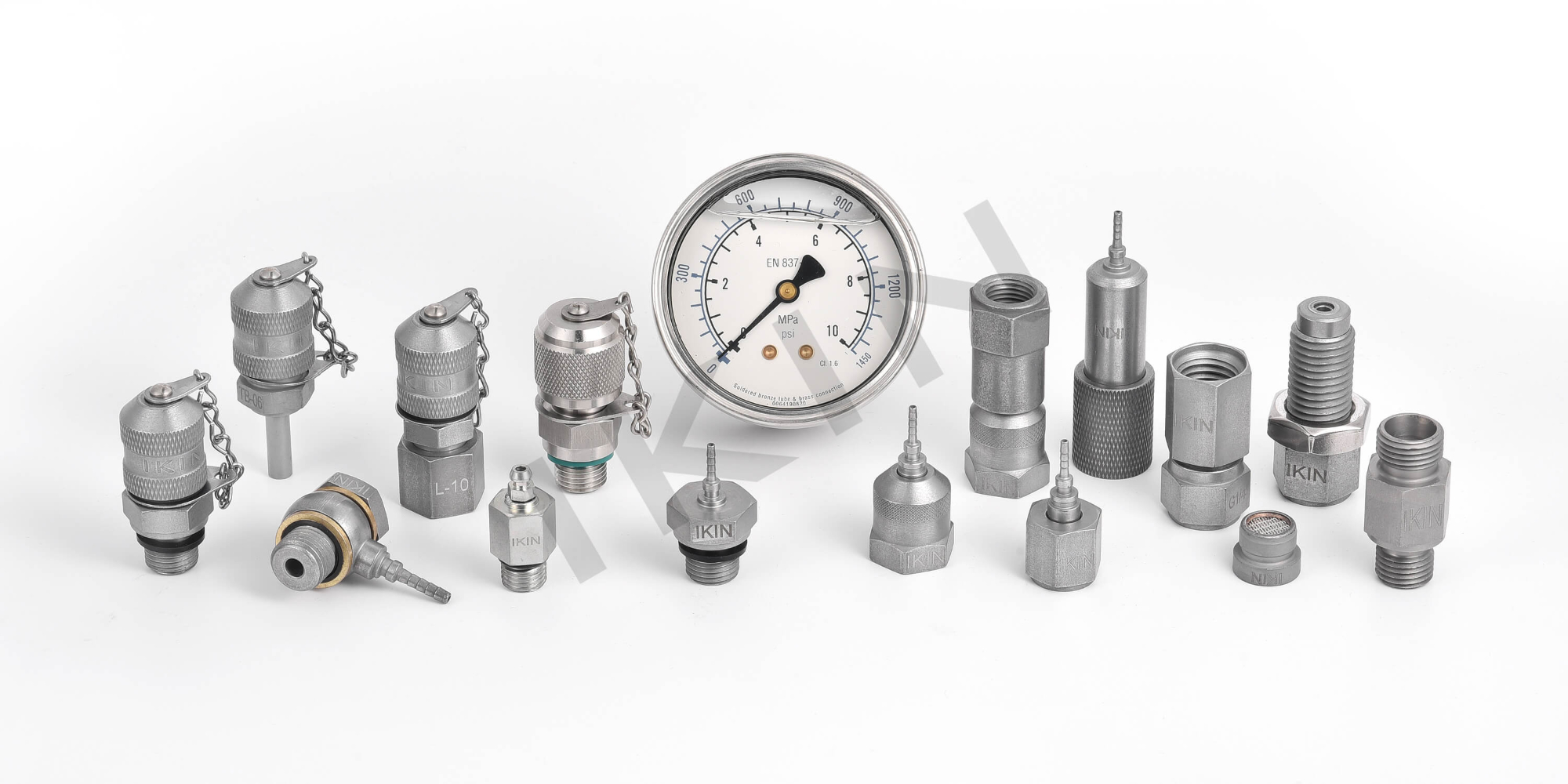
Conclusion
The above is a summary of hydraulic testings in the hydraulic system application practice, and several reasons are prone to leakage.
In practice. The possible causes of leakage should be analyzed and found in combination with the actual situation, and the problem should be quickly eliminated by searching for it in an orderly manner.