Blog
How to operate hydraulic test fittings safely?
How to operate hydraulic test fittings safely?
Hydraulic test fittings are essential components in hydraulic systems, widely utilized in fields such as construction machinery, industrial equipment, aerospace, automotive manufacturing, and oil and gas.
Their primary role is to measure and monitor system pressure, ensuring stable operation and safety. However, improper use or poor maintenance can lead to system failures and potentially severe safety incidents.
Therefore, mastering the safe operation guidelines for pressure measuring joints is crucial. This paper delves into the correct operation and maintenance practices for pressure measurement joints to ensure their safety and reliability in practical applications.
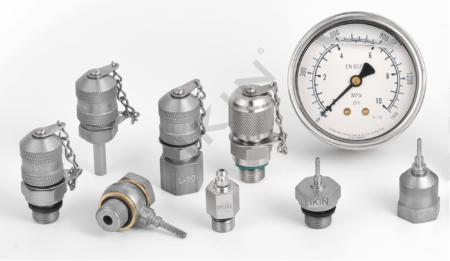
1. Basic structure and operation principle of pressure-measuring connectors
A pressure measuring fitting typically comprises a body, seals, and connecting components. Its function is to detect pressure fluctuations within a hydraulic system, delivering real-time data that allows operators to monitor and adjust the system’s performance accordingly. Hydraulic test fittings are engineered for optimal tightness and stability in high-pressure environments, effectively preventing fluid leaks and potential system failures.
2. Basic principles of safe operation
2.1 Knowledge of equipment
Before operating a pressure measuring fitting, it’s essential to thoroughly understand its structure, working principles, and operating instructions. Familiarize yourself with the equipment’s performance parameters, including maximum working pressure, temperature range, and suitable media. This knowledge ensures that the equipment operates within its design limits, preventing any operational issues.
2.2 Wear appropriate protective equipment
Always utilize suitable protective equipment, such as gloves, goggles, and protective clothing, when operating pressure-measuring fittings. This gear is crucial for preventing injuries from high-pressure fluid leaks and ensures operator safety.
2.3 Checking the status of equipment
Before operation, thoroughly inspect the condition of the pressure measuring fitting to ensure there are no signs of damage or wear. Pay special attention to the seals, which must be intact to prevent leaks. Additionally, check the connecting parts for tightness to ensure a secure and reliable connection.
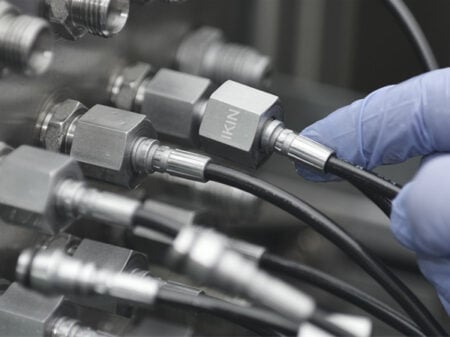
3. Safe practices for installation and dismantling
3.1 Installation of hydraulic test fittings
-Selecting an Appropriate Location: Choose a suitable spot within the hydraulic system for installation to ensure the measurement point accurately reflects the system’s operating pressure.
– Cleaning Connecting Parts: Prior to installation, thoroughly clean both the pressure measuring fitting and the system’s connecting parts to remove any impurities or contaminants that might compromise the seal.
– Using the Right Tools: Employ the correct tools for installation and avoid applying excessive force to prevent damage to the fittings or connecting components. Adhere to the equipment manufacturer’s installation instructions to ensure proper setup.
3.2 Disassembly of hydraulic test fittings
– Pressure Relief: Before removing the pressure measurement fitting, ensure that the system is fully depressurized to eliminate any residual pressure and prevent injuries from fluid discharge.
– Equipment Protection: During disassembly, carefully protect the pressure measurement fittings and connecting parts from impacts and damage. After removal, store the connectors properly to prevent contamination and damage.
4. Safety precautions in operation
Monitoring System Pressure: During operation, continuously monitor the system pressure in real-time to ensure it remains within a safe range. Avoid overpressure conditions to prevent damage to the pressure measuring fitting and the hydraulic system.
Avoiding Sudden Pressure Changes: Prevent sudden pressure changes during operation to avoid shocks to the pressure measuring fitting and the hydraulic system. Adjust the system pressure gradually to ensure a smooth transition.
Compliance with Operating Procedures: Adhere strictly to the operating procedures and avoid unauthorized actions. If any abnormal conditions arise during operation, stop immediately, identify the cause, and address it to ensure system safety.
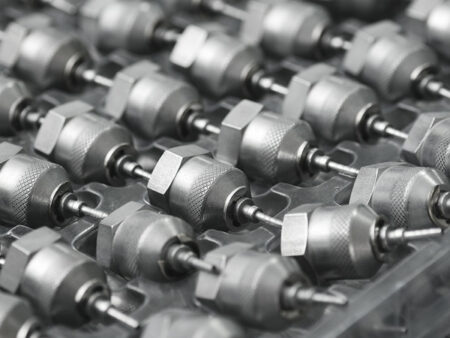
5. Safe practices for maintenance and upkeep
5.1 Regular inspection and maintenance
– Inspection of seals: Regularly inspect the seals of the pressure measuring joints, and replace them in time if they are found to be aged or damaged. Select high-performance sealing materials to improve the sealing effect and service life.
– Cleaning the equipment: Clean the pressure measurement fitting regularly to prevent dust, impurities and corrosive substances from entering the inside of the fitting. Use appropriate cleaning agents and tools to ensure that both the inside and outside of the fitting are kept clean.
5.2 Lubrication and fastening
– Lubrication: For pressure-measuring fittings that require frequent operation, lubricate regularly to reduce wear and operating resistance. Select a suitable lubricant and avoid lubricants that are harmful to the sealing material.
– TIGHTENING: Periodically check the tightness of the joints to ensure that they are securely connected. For loose joints, tighten them with appropriate tools to prevent leakage and system instability.
5.3 RAM
– Maintenance records: Detailed records of each maintenance and servicing, including inspection items, problems found and treatment measures. Through the maintenance records, the history of equipment use can be traced, potential problems can be found and dealt with in a timely manner.
– File management: Establish a file management system for the pressure measuring joints, keep the technical data, operation instructions and maintenance records of the equipment, etc., so as to facilitate the daily management and maintenance.
6. Emergency response measures
Regular Inspection and Maintenance:
- Seal Inspection: Regularly examine the seals of pressure measuring joints and promptly replace any that are aged or damaged. Use high-performance sealing materials to enhance sealing effectiveness and extend service life.
- Equipment Cleaning: Routinely clean the pressure measuring fitting to prevent dust, impurities, and corrosive substances from entering. Use appropriate cleaning agents and tools to ensure both the interior and exterior of the fitting remain clean.
Lubrication and Fastening:
- Lubrication: For pressure measuring fittings that require frequent operation, lubricate regularly to minimize wear and operational resistance. Choose a suitable lubricant and avoid those that could harm the sealing material.
- Tightening: Periodically check the tightness of the joints to ensure secure connections. Use appropriate tools to tighten any loose joints, preventing leaks and system instability.
Record and Maintenance (RAM):
- Maintenance Records: Keep detailed records of each maintenance session, including inspection items, identified issues, and corrective actions taken. These records help trace the equipment’s usage history and identify potential problems early.
- File Management: Establish a file management system for pressure measuring joints, maintaining technical data, operation instructions, and maintenance records. This system facilitates daily management and maintenance activities.
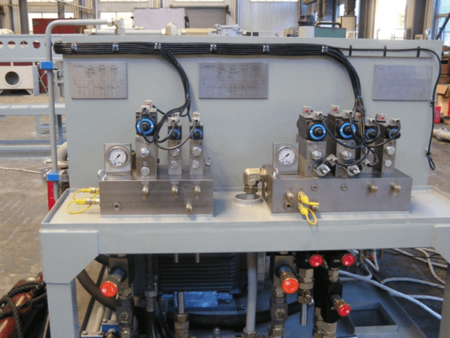
7. Case studies
Case 1: Safe Operation of hydraulic test fittings in a Chemical Plant
In a chemical plant, numerous hydraulic test fittings were utilized within the hydraulic system. An incident occurred when an operator failed to perform the necessary pressure relief operation, resulting in a high-pressure liquid spray during disassembly and causing injury.
Following an investigation, the chemical plant developed detailed operating procedures and provided comprehensive training to the operators. These measures significantly improved the operational safety of the pressure measuring joints and prevented similar incidents from occurring.
Case 2: Maintenance of pressure-measuring fittings at a manufacturing company
A manufacturing company employed high-pressure hydraulic test fittings in its hydraulic press equipment. Due to neglect in timely maintenance and repair, the seals of the pressure-measuring fittings deteriorated and became damaged, leading to system leaks.
To address the issue, the company took the following actions: replaced all deteriorated seals with high-performance sealing materials; regularly inspected and cleaned the pressure-measuring fittings to ensure optimal condition; and trained operators to enhance their maintenance and operation skills. These measures effectively resolved the leakage problem and improved both the operational efficiency and safety of the equipment.
Hydraulic test fittings are crucial components in hydraulic systems, and their safe operation and maintenance are directly linked to the stability and safety of the system. By understanding the equipment’s structure, wearing appropriate protective gear, checking the equipment’s condition, installing and removing it correctly, monitoring system pressure, avoiding sudden pressure changes, adhering to operating procedures, conducting regular inspections and maintenance, maintaining thorough records and files, and implementing emergency response measures, you can ensure the safety and reliability of pressure-testing fittings in practical applications.
Real-world case studies demonstrate that following scientific operation and maintenance protocols not only enhances the service life and performance of pressure measuring joints but also effectively prevents safety incidents. Therefore, attention to the safe operation specifications of pressure measuring joints is essential for ensuring the stable operation of hydraulic systems and the safety of operators.
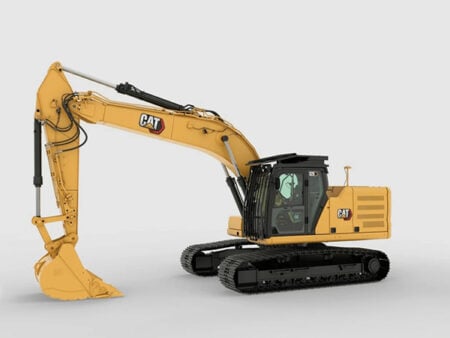
Common problems and solutions during pressure testing
Common problems and solutions during pressure testing
Pressure testing is essential for ensuring the proper operation and safety of hydraulic systems and equipment. It helps detect weaknesses, verify design pressures, and identify potential leaks within the system.
However, various issues may arise during pressure testing. If these problems are not addressed promptly and effectively, they can affect test results and even jeopardize system safety.
This article provides an in-depth analysis of common problems encountered during pressure testing and offers practical solutions. We will also discuss these issues through real-world examples. By offering detailed analysis and discussion, this article aims to provide practical guidance to ensure the stability and safety of hydraulic systems.
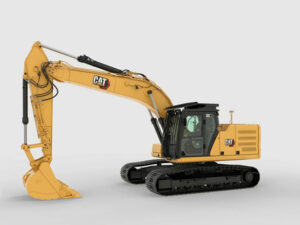
**1. Common problems during pressure testing**
**1.1 Leakage**
Leaks are among the most common issues encountered during pressure testing. They can occur at system connections, seals, or along piping. The causes of leaks are varied and may include deteriorated seals, improper installation, or defective materials.
**Solutions:**
Inspection and Replacement of Seals: Regularly inspect the condition of seals. Any seals that are deteriorated or damaged should be promptly replaced to prevent potential leakage.
Correct Installation: Ensure that all connections and piping are installed correctly, using appropriate methods and tools. Proper tightening and sealing of each component are essential to prevent leaks.
Material Selection: Choose materials that are corrosion-resistant and capable of withstanding high pressures. Selecting the right materials for the system’s working environment enhances the overall reliability of the system.
By implementing these solutions, the likelihood of leaks can be significantly reduced, ensuring the integrity and safety of the hydraulic system during pressure testing.
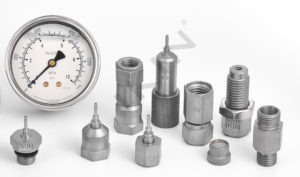
**1.2 Pressure fluctuations**
Pressure fluctuation refers to unstable pressure during testing, which can be caused by poor system design, unstable pressure sources, or equipment failure.
**Solutions:**
Optimized System Design: Ensure that the system is well-designed to prevent sudden changes in pressure. A robust design minimizes the likelihood of pressure fluctuations and significantly reduces associated problems.
Stable Pressure Source: Utilize a reliable pressure source that can provide continuous and stable pressure, ensuring the system operates normally and efficiently.
Equipment Maintenance: Conduct regular inspections and maintenance of pressure source equipment. Timely identification and resolution of potential issues are crucial to maintaining optimal working conditions and preventing pressure instability.
Implementing these solutions will help stabilize pressure during testing, ensuring the system’s reliability and accuracy.
**1.3 Inaccurate meter readings**
During pressure testing, inaccurate meter readings can compromise the accuracy of the test results. This issue may arise due to improper calibration of the gauge, incorrect mounting position, or gauge malfunction.
**Solutions:**
Periodic Calibration of Meters: Calibrate the meters at regular intervals to maintain accurate readings and ensure the reliability of the test data.
Select an Appropriate Mounting Location: Install the meter in a suitable location that minimizes vibration and interference, which can affect the accuracy of the readings.
Replacement of Malfunctioning Meters: Promptly replace any malfunctioning meters to maintain the accuracy and integrity of the test results.
By addressing these factors, the accuracy of meter readings can be ensured, thereby enhancing the reliability of the pressure test outcomes.
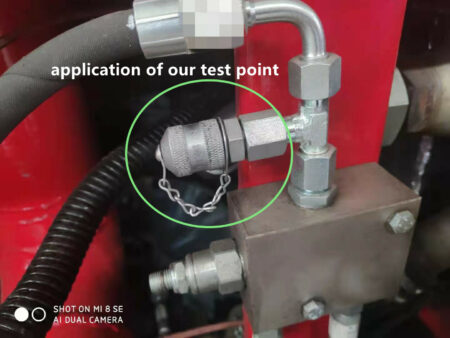
**1.4 Temperature effects**
Temperature variations can significantly impact pressure test results, particularly in extreme high or low-temperature environments. These fluctuations can cause materials to expand or contract, affecting the system’s sealing and pressure stability.
**Solutions:**
Selection of Temperature-Resistant Materials: Choose materials that are resistant to temperature changes based on the system’s working environment. This ensures that the system maintains stable performance under extreme temperature conditions.
Implement Temperature Compensation Mechanism: Introduce a temperature compensation mechanism during testing to minimize the impact of temperature fluctuations on the results. This helps ensure the accuracy and reliability of the pressure tests.
By addressing temperature-related issues, the stability and accuracy of pressure test results can be significantly improved.
**1.5 Connectivity issues**
Connection problems are a common challenge during pressure testing, often caused by mismatched fitting types, improper installation, or loose connections.
**Solutions:**
Selecting the Appropriate Fitting Type: Choose fittings that are compatible with the system design and suitable for the working environment to ensure proper matching with the rest of the system.
Correct Installation of Fittings: Follow standard methods and procedures for installing fittings to ensure a secure and reliable connection.
Regular Inspection and Tightening: Conduct periodic inspections of connection points and promptly tighten any loose parts to maintain a solid and dependable connection.
By addressing these connection issues, the reliability and effectiveness of pressure testing can be significantly enhanced.
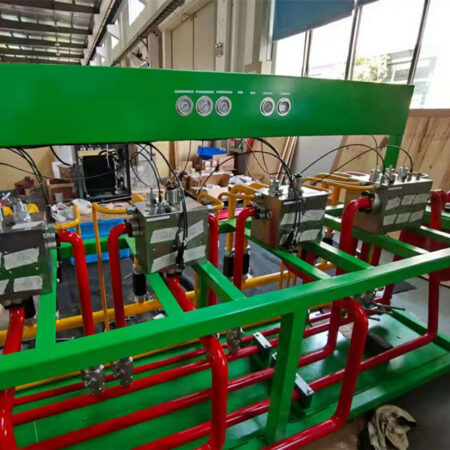
**2. Solutions for pressure testing**
**2.1 Development of a Detailed Test Plan**
Before conducting a pressure test, it is crucial to develop a comprehensive test plan that outlines the purpose, scope, methodology, steps, and expected outcomes. A detailed test plan helps clarify the objectives and ensures that the testing process is systematic and organized.
**2.2 Use of High-Quality Test Equipment**
Using high-quality test equipment is essential for obtaining accurate and reliable results. Select certified and calibrated equipment, and ensure that it is in optimal working condition before use.
**2.3 Training and Education**
Provide thorough training and education for operators to equip them with the necessary knowledge and skills for pressure testing. Training should cover the use of test equipment, execution of test procedures, and identification and resolution of common issues.
**2.4 Recording and Analysis**
During the pressure test, meticulously record all data and results, including pressure, temperature, time, and environmental conditions. Analyzing this data helps identify potential problems and implement timely corrective measures.
**2.5 Development of Contingency Plans**
Develop a comprehensive contingency plan to address any emergencies that may arise during the testing process. The plan should include procedures for handling leaks, equipment failures, and safety measures to ensure the testing process remains safe and efficient.
By implementing these strategies, the reliability and accuracy of pressure testing can be significantly enhanced, ensuring the safe and effective operation of hydraulic systems.
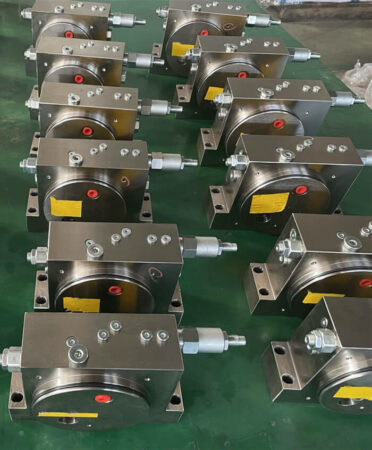
**3. Case Studies**
**Case 1: Pressure Testing in a Chemical Plant**
During the pressure testing of a new piping system at a chemical plant, multiple leaks were detected. Upon investigation, it was determined that the primary causes of the leaks were aging seals and improper installation. To address these issues, the chemical plant implemented the following measures:
– Replaced all deteriorated seals with corrosion-resistant, high-performance sealing materials to enhance durability and reliability.
– Conducted a thorough inspection and tightening of all connections to ensure that the installation complied with relevant codes and standards.
– Provided comprehensive training to operators to enhance their installation and operational skills.
By taking these steps, the chemical plant effectively resolved the leakage issues and ensured the safety and stability of the piping system.
**Case II: Pressure Testing in a Pharmaceutical Company**
During a pressure test of the hydraulic system at a pharmaceutical company, significant pressure fluctuations were detected. Analysis revealed that these fluctuations were caused by an unstable pressure source and poor system design. To address these issues, the pharmaceutical company implemented the following measures:
– Replaced the existing pressure source with more stable equipment to ensure a continuous and stable pressure supply.
– Redesigned the hydraulic system, optimizing the piping layout and connections to enhance overall system stability.
– Introduced an automated control system to monitor and regulate pressure in real-time, ensuring consistent system pressure.
By implementing these measures, the pharmaceutical company successfully resolved the issue of pressure fluctuations, significantly improving the operational efficiency and stability of the hydraulic system.
**Case IV: Pressure Testing at an Aerospace Company**
During pressure testing of an aircraft hydraulic system at an aerospace company, significant effects of temperature variations on the test results were observed. Analysis determined that these temperature changes caused material expansion and contraction, which impacted the system’s sealing and pressure stability. To address this issue, the aerospace company implemented the following measures:
– Selected temperature-resistant materials suitable for both high and low-temperature environments to ensure stable performance despite temperature fluctuations.
– Introduced a temperature compensation mechanism during the testing process to adjust system parameters in real-time, ensuring the accuracy of the test results.
– Controlled the test environment to minimize the impact of temperature variations on the testing process.
By adopting these measures, the aerospace company successfully mitigated the issues caused by temperature variations, significantly enhancing the accuracy and reliability of the pressure tests.
**Case V: Pressure Testing in a Shipping Company**
During a pressure test of a ship’s hydraulic system at a shipping company, issues were identified at multiple joints. Inspection revealed that these problems were due to mismatched joint types and improper installation. To resolve these issues, the shipping company implemented the following measures:
– Selected appropriate fittings that were compatible with the system, ensuring they matched the rest of the hydraulic components.
– Reinstalled the connectors following correct methods and procedures to guarantee a secure and reliable connection.
– Conducted thorough inspections and tightened all connections to ensure system stability and safety.
By taking these steps, the shipping company successfully addressed the connection issues, ensuring the normal operation and reliability of the ship’s hydraulic system.
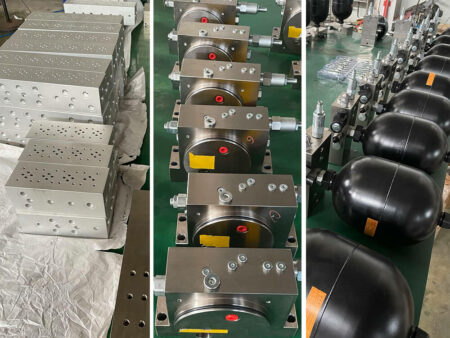
Pressure testing is a vital procedure for ensuring the proper functioning and safety of hydraulic systems and equipment. During testing, issues such as leaks, pressure fluctuations, inaccurate gauge readings, temperature effects, and connection problems can arise. These challenges can be effectively managed through the implementation of detailed test plans, the use of high-quality testing equipment, comprehensive operator training, meticulous recording and analysis of test data, and robust contingency plans. These measures ensure the accuracy and reliability of pressure tests.
Analyzing real-world cases demonstrates that scientific pressure testing methods and strategies not only address issues encountered during testing but also enhance the operational efficiency and safety of hydraulic systems. Therefore, focusing on the identification and resolution of problems during the pressure testing process is crucial for maintaining the stable operation of hydraulic systems.
Hydraulic Pressure Fittings Applied in Various Industries
Hydraulic Pressure Fittings Applied in Various Industries
Pressure measuring fittings are essential hydraulic components. They monitor pressure in hydraulic systems to ensure safety and stability. These fittings are used in many industries, including construction, industrial equipment, aerospace, automotive manufacturing, and oil & gas. Each industry has different performance requirements.
The performance requirements for pressure measuring fittings differ across industries. Specific examples demonstrate the practical importance of these fittings.
In this article, we will explore how pressure-measuring fittings are used across various industries. We’ll analyze their key roles and impacts through specific case studies.
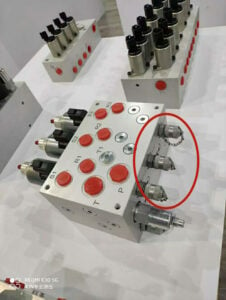
1. In the field of construction machinery
In the construction machinery industry, pressure measuring fittings are indispensable components. Equipment such as excavators, bulldozers, and loaders must endure harsh environments for extended periods, demanding highly reliable hydraulic systems.
Pressure measuring fittings play a critical role by continuously monitoring hydraulic system pressure in real time. This real-time monitoring ensures that the equipment operates within the optimal pressure range, thereby enhancing reliability, preventing system failures, and maintaining peak performance and safety.
Excavators, bulldozers, loaders, and similar equipment often operate in harsh environments for prolonged periods. This demanding usage necessitates exceptional reliability in their hydraulic systems. To achieve this, pressure measuring fittings are employed to monitor the hydraulic system’s pressure in real time. These fittings ensure that the equipment operates within the optimal pressure range, thereby preventing potential system failures and maintaining peak performance and safety standards.
**Case Study: Excavator Application**
A leading construction machinery company incorporates high-performance pressure measuring fittings in the hydraulic systems of its excavators. Given that excavators are required to function in high-intensity work environments, the pressure resistance and durability of these fittings are crucial.
These pressure measuring fittings are crafted from the latest high-strength alloy materials and utilize advanced sealing technology. This design enables them to perform reliably for extended periods under high-pressure and high-temperature conditions, effectively preventing leaks and system failures.
Through regular maintenance and servicing, the company’s excavators have significantly enhanced their operational efficiency and safety. The robust construction of these fittings ensures that the hydraulic systems remain reliable, thereby optimizing performance and reducing downtime. This meticulous approach to equipment maintenance has contributed to the company’s reputation for producing durable and efficient machinery capable of withstanding the rigors of demanding construction environments.
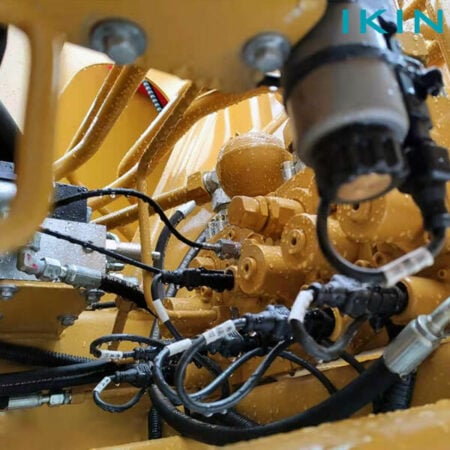
2. **Industrial Equipment Sector**
Industrial equipment such as hydraulic presses, die casting machines, and injection molding machines heavily rely on pressure measuring fittings. These fittings ensure the systems operate smoothly under high pressure and high temperature conditions. They provide accurate pressure data, enabling operators to adjust system parameters in a timely manner. This real-time data optimizes equipment performance and ensures an efficient, stable production process.
**Case Study: Hydraulic Press Application in a Manufacturing Company**
A manufacturing company has implemented new high-pressure gauge fittings in its hydraulic press equipment. Precise pressure control is essential for hydraulic presses during production, making the accuracy and stability of these fittings crucial.
By utilizing high-performance pressure measuring fittings, the company has notably enhanced the quality of its hydraulic products. This improvement has led to a significant reduction in scrap rates and an increase in production efficiency. The reliable performance of these fittings ensures that the hydraulic presses maintain consistent pressure control, thereby optimizing the overall manufacturing process and ensuring high-quality output.
3. **Automobile Manufacturing Sector**
In the automotive manufacturing sector, hydraulic systems play a crucial role in braking, steering, and suspension systems. Pressure measuring fittings are essential for real-time pressure monitoring in these systems, ensuring the vehicle’s safety performance under various operating conditions.
**Case Study: Braking System Application for an Automobile Manufacturer**
A renowned automobile manufacturer has integrated intelligent pressure measurement fittings into the braking system of its latest models. These advanced fittings combine a pressure sensor with data transmission capabilities, allowing real-time pressure data to be sent to the vehicle’s electronic control system. This continuous data stream enables the system to dynamically adjust brake pressure, significantly enhancing braking performance and vehicle safety.
The manufacturer has also conducted extensive testing and validation to ensure these pressure-measuring fittings maintain optimal performance across different climatic conditions and driving environments. This rigorous testing ensures that the fittings provide consistent, reliable data, contributing to a safer and more dependable driving experience for consumers. By incorporating these intelligent fittings, the automaker has improved the overall safety and reliability of its vehicles, reinforcing its commitment to quality and innovation in automotive design.
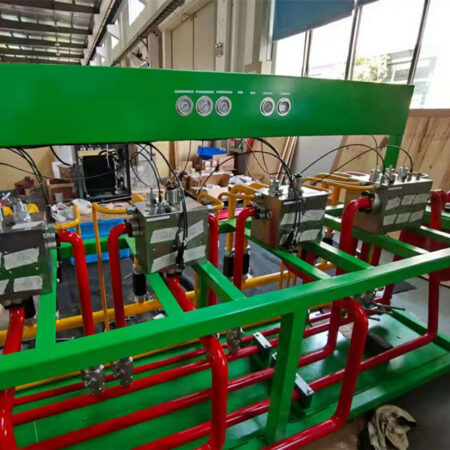
4. **Oil and Gas Sector**
In the oil and gas industry, hydraulic systems must function in complex environments with significant pressure fluctuations and exposure to corrosive media. Pressure measuring fittings are critical in these systems for monitoring the pressure of pipelines and equipment, preventing safety incidents such as leaks and explosions.
**Case Study: High-Pressure Pipeline Application in an Oilfield Project**
An oilfield project implemented high-pressure gauge fittings within its pipeline system. These fittings, constructed from high-strength alloys and featuring multi-layer seals, are engineered to withstand high-pressure and highly corrosive environments over extended periods. Regular inspections and maintenance have enabled the project team to avert numerous potential leakage incidents, ensuring safe production and environmental compliance.
Additionally, these pressure measuring fittings are equipped with remote monitoring technology, allowing operators to observe real-time pressure changes in the pipeline from a central control room. This capability ensures that any abnormalities are quickly addressed, significantly enhancing production efficiency and safety management in the oilfield. The integration of these advanced fittings not only ensures the structural integrity of the pipeline system but also supports the overall safety and efficiency of the oilfield operations.
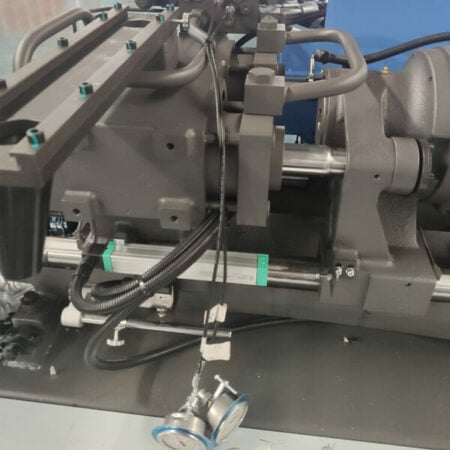
5. **Building Construction Sector**
In the building construction sector, large mechanical equipment such as tower cranes and concrete pump trucks rely on stable hydraulic systems for optimal performance. Pressure measuring fittings are crucial in these hydraulic systems to ensure stability and safety during construction activities5.
**Case Study: Tower Crane Application for a Construction Company**
A construction company has integrated high-precision pressure measurement fittings into the hydraulic systems of its tower cranes. During construction, tower cranes frequently lift heavy loads, demanding extremely stringent pressure requirements for their hydraulic systems. By employing high-performance pressure measuring fittings, the company has significantly enhanced construction efficiency and safety in large-scale projects.
These advanced pressure measuring fittings feature the latest self-locking design, ensuring that the fittings remain secure under high pressure and vibration. This innovation greatly improves the reliability and operational safety of construction equipment, enabling the tower cranes to function seamlessly in demanding environments. Consequently, the construction company has achieved higher productivity and reduced risks, reinforcing the importance of utilizing top-tier pressure measuring fittings in critical construction machinery.
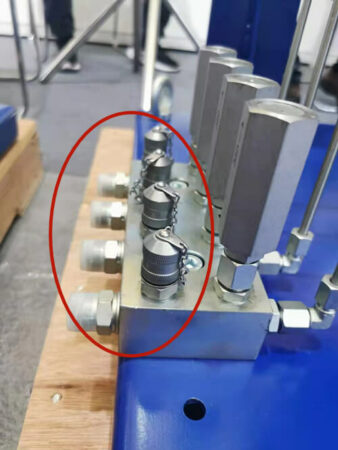
6. **Agricultural Machinery Sector**
In the agricultural machinery sector, equipment such as tractors, harvesters, and planters rely heavily on hydraulic systems. Pressure measuring fittings are essential for monitoring and controlling these hydraulic systems, ensuring the machines’ reliability and efficiency in various farming operations.
**Case Study: Harvester Application for an Agricultural Machinery Company**
An agricultural machinery company has implemented a new type of pressure measuring connector in the hydraulic system of its latest harvester model. These advanced fittings allow operators to monitor the hydraulic system’s status in real time, enabling timely adjustments and maintenance. As a result, the harvester performs reliably in field operations, reducing mechanical failures and enhancing harvesting efficiency.
These pressure measuring fittings feature an anti-fouling design that effectively prevents soil and impurities from entering the system. This design keeps the hydraulic system clean and functioning properly, ultimately improving the efficiency and service life of the agricultural machinery.
By adopting these innovative fittings, the company has ensured that its harvesters deliver optimal performance, contributing to more productive and efficient farming operations.
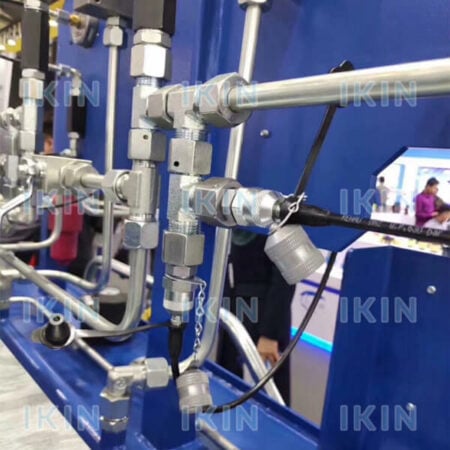
7. **Mining Sector**
The mining industry is highly demanding, and hydraulic systems are crucial for the performance of mining equipment. Pressure measuring fittings are essential for monitoring the hydraulic systems in this sector, ensuring stable operation under high loads, high pressures, and harsh environmental conditions.
**Case Study: Hydraulic Drilling Rig Application for a Mining Company**
A mining company has integrated high-performance pressure measuring couplings into the hydraulic systems of its drilling rigs. These couplings are made with special wear-resistant materials and a multi-layer sealing structure, allowing them to operate reliably for extended periods under high-pressure and high-vibration conditions.
Through regular maintenance and real-time monitoring, the company’s hydraulic drilling rigs perform exceptionally well in deep well drilling and ore extraction. This significantly boosts both efficiency and safety. The use of these advanced pressure measuring couplings not only extends the lifespan of the equipment but also reduces downtime caused by equipment failures, thereby improving overall productivity at the mine. By leveraging these robust fittings, the mining company ensures that its drilling operations are more efficient, reliable, and productive.
The case studies above clearly illustrate the application of pressure measuring fittings across various industrial fields, highlighting their critical role in ensuring the stable operation and safety of hydraulic systems. These fittings help enterprises improve productivity, reduce maintenance costs, and enhance safety.

As technology continues to advance, the performance and functionality of pressure measuring fittings are also improving. This progress will lead to their application and promotion in even more fields in the future, making significant contributions to industrial development and technological progress.
By integrating these advanced fittings, industries can look forward to more efficient, reliable, and safe hydraulic systems, driving further innovation and growth.
Pressure Measuring Fittings in Hydraulic Systems: Types, Applications, and Best Practices
Pressure Measuring Fittings in Hydraulic Systems: Types, Applications, and Best Practices
Hydraulic systems are essential in modern industry, playing a crucial role in fields such as construction machinery, industrial equipment, aerospace, and automotive manufacturing.
At the heart of these systems lies the pressure measuring fitting, which is critical for measuring and monitoring system pressure to ensure stability and safety.
In this comprehensive guide, we will explore the various types of pressure measuring fittings, their application scenarios, selection criteria, installation and maintenance procedures, and real-world case studies demonstrating their importance in hydraulic systems.
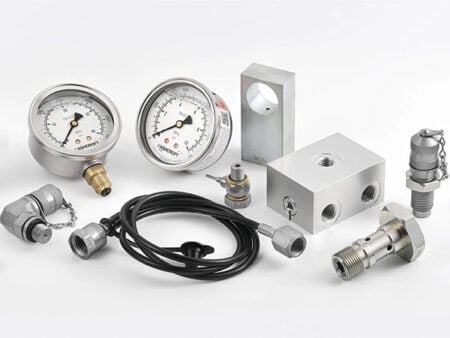
Pressure measuring fittings come in various designs tailored for specific applications, each with unique features:
1. Quick couplings
·Characteristics: Designed for rapid connection and disconnection.
·Applications: Used in hydraulic systems requiring frequent assembly and disassembly, enhancing efficiency through simple insertion and removal.
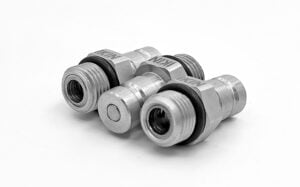
2. Threaded joints
·Characteristics: Secured by threaded connections, suitable for high-pressure environments.
·Applications: Common in systems needing robust connections that can withstand high pressure and vibration.
3. Push-in fittings
·Characteristics: Connect via a simple push-in operation.
·Applications: Ideal for low and medium pressure systems, though caution is needed in high-pressure environments.
4. Flanged joints
·Characteristics: Provide high-strength connections.
·Applications: Used in heavy machinery and high-pressure pipelines due to their strong connections and excellent seismic.
5. Welded joints
·Characteristics: Connected by welding, suitable for high-pressure and high-temperature conditions.
·Applications: Preferred in environments demanding high connection strength, despite more complex installation and maintenance.
When selecting a pressure measurement fitting, a number of factors need to be thoroughly evaluated to ensure optimum performance and long-lasting reliability in a particular application. The main factors to consider include the following:
1. Pressure range
According to the working pressure of the hydraulic system, select the coupling that can withstand the corresponding pressure. Over-pressurization can lead to damage to the couplings and even safety accidents.
When choosing, you need to carefully check the maximum working pressure of the hydraulic system and the rated pressure of the pressure measurement joints to ensure that the joints can withstand the working pressure of the system.
2. Temperature range
Hydraulic systems may operate in high or low temperature environments, requiring the selection of fittings with good temperature resistance.
Pressure gauge fittings made of different materials have different performance in different temperature ranges, and you need to choose the right fittings according to the operating temperature of the hydraulic system.
3. Media type
According to the medium used in the hydraulic system (such as oil, water, etc.) to select the appropriate joint material to prevent corrosion and media leakage.
Different media have different requirements for pressure measurement joint materials, such as oil-based hydraulic media suitable for the use of metal joints, while water-based hydraulic media may require the use of corrosion-resistant materials.
4. Connectivity
According to the design and installation requirements of the system to choose the appropriate connection, such as quick couplings, threaded fittings or push-in fittings. The selection needs to take into account the connection method and operating habits of the hydraulic system to ensure that the fitting is easy to install and use.
In order to ensure that the gauge fitting will operate consistently and efficiently in the hydraulic system for a long period of time, proper installation methods and a systematic maintenance program are essential. Below are some detailed recommendations:
1. Installation steps
– Ensure that the hydraulic system is fully pressurized before installation.
– Select the appropriate installation tool according to the type of fitting.
– Ensure that fittings are clean and free of foreign matter where they connect to the system.
– Install the fitting correctly according to the product instructions to ensure a good seal.
– Pressure test after installation to ensure that the joints are leak-free.
2. Maintenance methods
– Regularly check the sealing of the joints and replace the seals when leaks are detected.
– Clean fittings regularly to prevent dust and contaminants from entering the system.
– Regularly lubricate frequently used joints to ensure smooth operation.
– When used under high pressure or in harsh environments, periodically check the fittings for wear and replace damaged fittings in a timely manner.

In the hydraulic system, the pressure measuring fitting is not only widely used, but also plays a vital role. Through the following case studies of several practical applications, we can have a clearer understanding of the key role and significant results of the pressure measurement joints in various industries.
#Construction machinery
A major construction machinery company has introduced a new type of pressure measurement joint in its excavator hydraulic system. Made with high-precision sensors and durable materials, the connector provides excellent measurement accuracy and durability.
By using this pressure fitting, the company monitors the hydraulic system pressure in real time to ensure that the equipment operates within the optimal pressure range, improving efficiency and safety.
In addition, the corrosion and pressure resistance of the couplings significantly reduces maintenance costs, extends service life, and improves overall productivity.
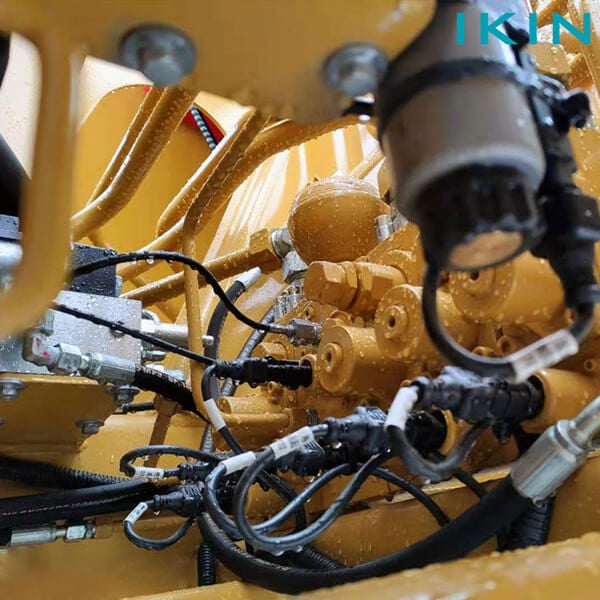
#Oil and gas
In the oil and gas industry, a large oilfield project has adopted a high-pressure and corrosion-resistant pressure measuring fitting to monitor the pressure of high-pressure pipelines. The application of this pressure fitting effectively prevents safety incidents such as pipeline leaks and explosions, and improves the safety and productivity of the project.
Installed at key pipeline nodes, these couplings transmit real-time pressure data to the monitoring center, helping operators adjust system parameters in a timely manner to prevent potential hazards.
#Industrial equipment
An industrial equipment manufacturing company has installed a variety of pressure measurement fittings in its hydraulic presses to monitor the pressure of the equipment’s hydraulic system.
Through accurate pressure monitoring and data analysis, the company identified and resolved potential problems in the hydraulic system and made timely adjustments, significantly improving the equipment’s operational stability and service life.
The real-time data provided by the pressure measurement couplings supports predictive maintenance, reduces equipment failure rates and downtime, and improves overall productivity.
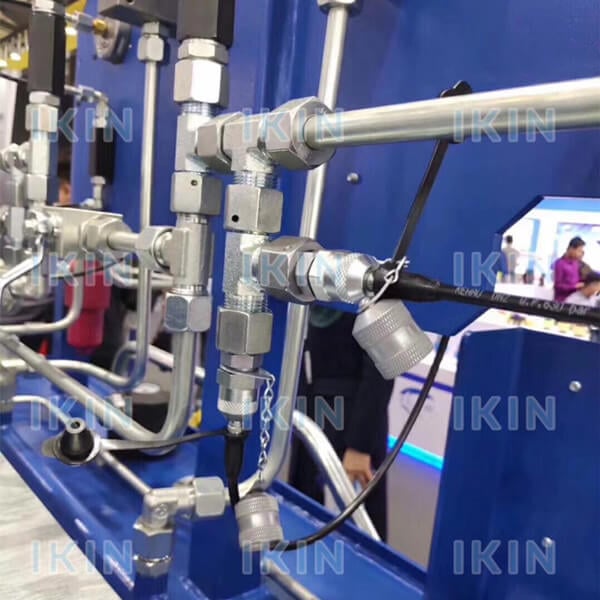
Pressure gauge fittings play a vital role in hydraulic systems, and their proper selection, installation and maintenance are the keys to ensuring the safe and stable operation of hydraulic systems. By understanding the different types of pressure measuring fittings and their application scenarios, and mastering the selection and maintenance methods, the operating efficiency and safety of the hydraulic system can be effectively enhanced.
We hope this article can help you better understand the basics and practical application scenarios of pressure measuring fittings, as well as grasp the key methods of selection and maintenance. We hope this information will be helpful to hydraulic system engineers and technicians in their work to enhance the performance and reliability of hydraulic systems. If you have any questions or need further guidance, please feel free to contact a professional.
qual è la differenza dei giunti di prova idraulica nel mercato?
I 3 migliori produttori in Cina
fornitore di raccordi per prove idrauliche
Approvato SGS
qual è la struttura del punto di prova della pressione nel mercato?
Sebbene il punto di prova della pressione sembri minuscolo e non necessario, il sistema di prova idraulico sarà molto più conveniente con esso.
1. funzione del punto di prova della pressione
Il punto di prova della pressione viene utilizzato principalmente per misurare la pressione del sistema del fluido e all'interno è presente una valvola autosigillante.
Se utilizzato da solo, grazie all'azione della molla, è possibile arrestare la perdita del mezzo di sistema.
La valvola autosigillante può essere aperta dopo essere stata collegata al tubo di misurazione con ditale o sensore di pressione e i parametri di pressione del sistema possono essere visualizzati dal manometro o tester, che viene utilizzato per il rilevamento della pressione del sistema, il debug del sistema e la diagnosi dei guasti di sistema fluido ad alta o bassa pressione.
Se impostati in una posizione speciale, gli adattatori del punto di prova possono essere utilizzati anche per il campionamento del fluido del sistema idraulico, lo scarico della pressione del sistema e lo scarico del sistema.
2. Classificazione dei punti di prova della pressione nel mercato
Poiché il connettore del punto di prova della pressione è appositamente progettato per la misurazione della pressione e il campionamento del fluido ad alta/bassa portata, il design ha considerato completamente il suo intervallo di pressione.
E in base ai diversi ambiti di utilizzo, sono stati progettati punti di prova di diversi tipi e punti di forza e anche questi connettori svolgono un ruolo insostituibile nel lavoro.
In base alla diversa struttura interna, la struttura del punto di prova della pressione può essere suddivisa in guarnizione a sfera, guarnizione a pistone e guarnizione a cono.
2.1 Struttura della tenuta a sfera
Il giunto di prova della pressione della tenuta a sfera è composto principalmente da una sfera d'acciaio e da una molla.
La spinta è generata dalla precompressione della molla, in modo che la sfera d'acciaio venga premuta contro la superficie di accoppiamento del corpo valvola per ottenere la tenuta.
Caratteristiche della struttura della tenuta a sfera: una struttura semplice, una tenuta meccanica, non facile da invecchiare e ha una buona stabilità.
Un'altra caratteristica: la precisione di lavorazione della superficie di contatto del corpo valvola deve essere elevata, la sfera d'acciaio e il corpo valvola sono in linea e l'effetto di tenuta è medio.
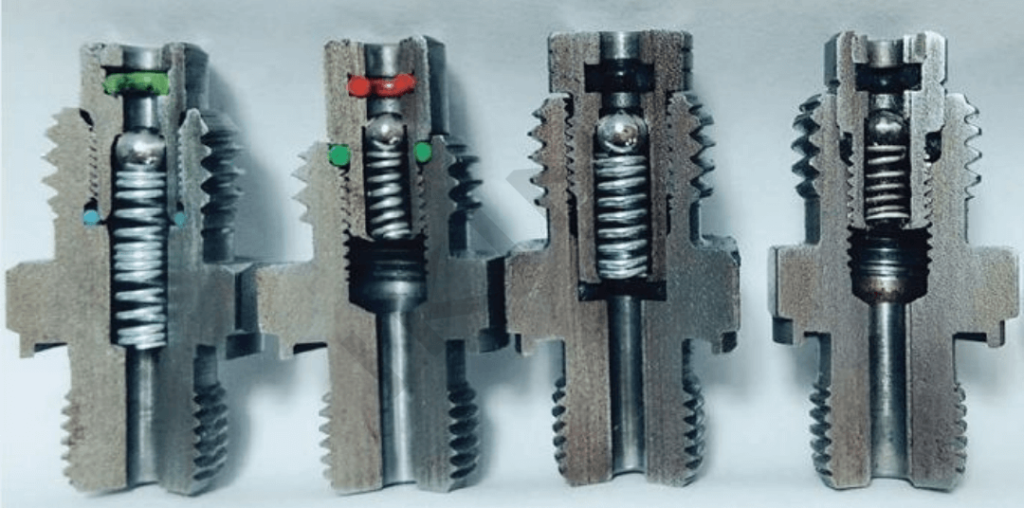
Struttura interna della presa di pressione con guarnizione a sfera
2.2 Struttura della tenuta del pistone
L'adattatore del punto di prova della pressione della guarnizione del pistone è composto principalmente da un pistone, un O-ring e una molla. L'anello di tenuta si trova nella scanalatura del pistone.
Aderire al cono di tenuta (tenuta radiale) o alla superficie piana (tenuta assiale) tramite la spinta di precompressione della molla.
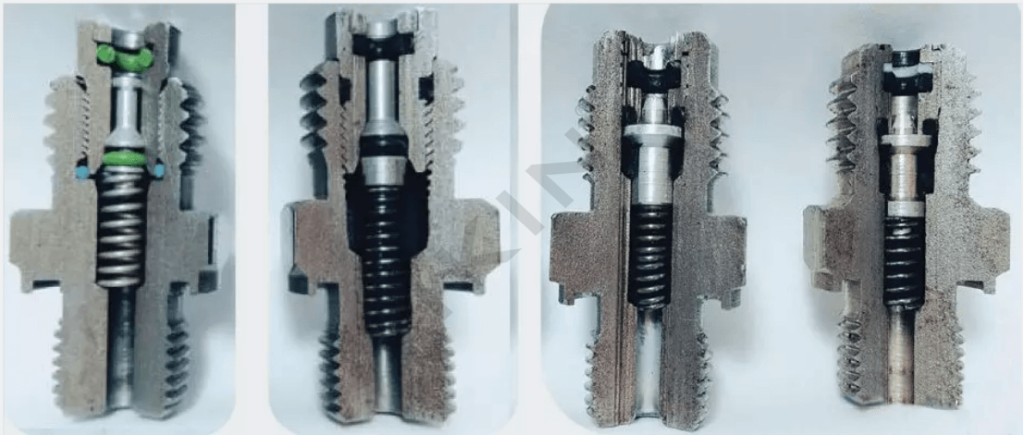
2.3 Struttura di tenuta del cono
Il giunto di prova della pressione della tenuta conica è composto da un nucleo della valvola conica, una tenuta conica e una molla.
La guarnizione conica e il nucleo della valvola conica sono saldamente fissati alla superficie di accoppiamento conica del corpo della valvola sotto la spinta di precompressione della molla.
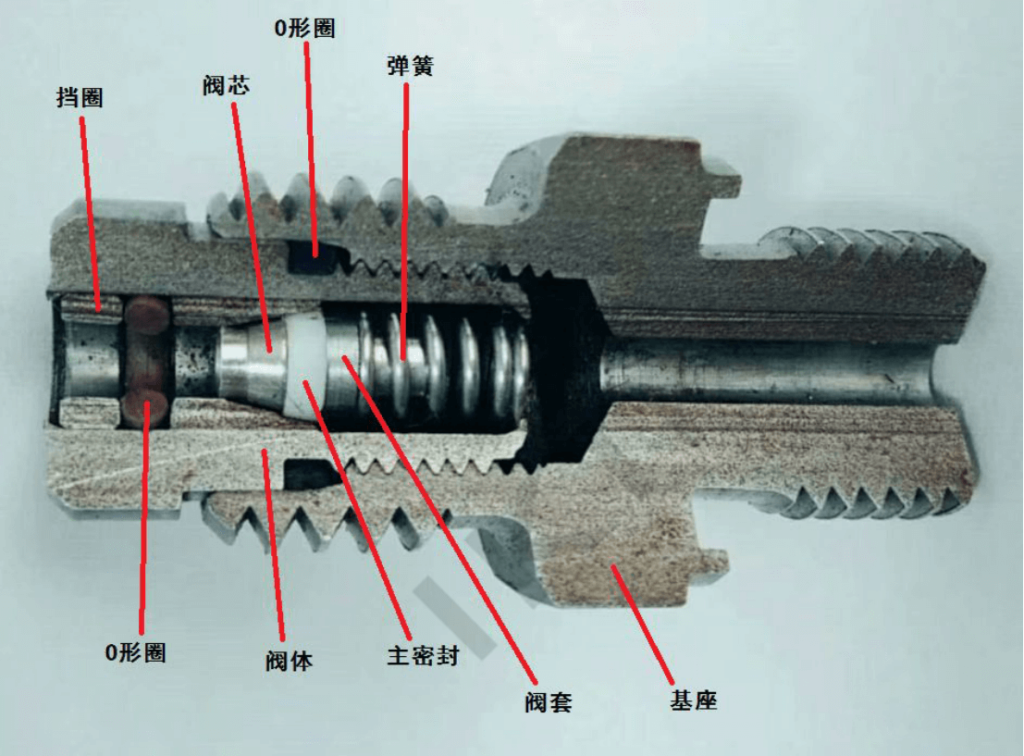
Struttura interna del test di pressione a tenuta conica
Caratteristiche della tenuta a cono: il nucleo della valvola conica e la tenuta conica lavorano insieme, la tenuta è a contatto con la superficie, l'effetto di tenuta è migliore e il gas e il liquido sono universali;
La molla è integrata nel corpo valvola e non è facile da allentare; ma la precisione di elaborazione del corpo valvola e della bobina è relativamente elevata.
Essendo un'apparecchiatura comunemente utilizzata nell'industria, i punti di prova della pressione del fluido sono noti per la loro ampia gamma pratica e per il comodo collegamento e campionamento. Soprattutto quando il fluido viene utilizzato ad alta pressione e portata, presenta molti vantaggi e molte comodità.
Quindi quali sono i suoi vantaggi:
Vantaggio 1: l'operazione può essere completata manualmente ad alta pressione
Quando il fluido è ad alta pressione, se l'operazione è negligente, la pressione più elevata può facilmente causare la fuoriuscita del liquido, causando incidenti di processo irreversibili e persino pericolose per la vita.
Tuttavia, il connettore del tubo di prova della pressione tiene pienamente conto di questo, in modo che il connettore possa essere scollegato e chiuso semplicemente usando entrambe le mani ad alta pressione.
Vantaggio 2: piccola struttura
Poiché le posizioni di campionamento e prova di pressione spesso non sono fisse, il lavoro deve essere svolto in base a condizioni e requisiti specifici.
Pertanto, la forma compatta offre una grande comodità nel trasporto e nell'ingegneria operativa.
Poi c'è la possibilità di connettersi facilmente con il contatore.
A causa del suo scopo unico, la connessione con lo strumento è completamente considerata nella progettazione, quindi l'operazione è facile e la connessione è stabile.
3. Riepilogo
Gli adattatori per punti di prova sono un componente molto piccolo nel sistema idraulico, ma svolgono un ruolo importante nella messa a punto, test e diagnosi del sistema idraulico.
Attraverso il manometro o il sensore, è possibile completare vari test di pressione senza smontaggio e montaggio e senza perdite.
L'impostazione ragionevole dei raccordi del punto di prova della pressione nel sistema idraulico offre molta comodità per il debug, il test e la diagnosi.
Per garantire un buon effetto applicativo, è infatti molto importante scegliere un prodotto di alta qualità e affidabile.
L'attuale valutazione del punto di prova della pressione è molto buona e il design del prodotto è eccellente.
Pur garantendo un'elevata portata in uscita, può anche garantire rigorosi standard di screening della qualità, in modo che i prodotti possano avere un valore d'uso migliore.
A giudicare dalla situazione attuale, i giunti per test di pressione sono principalmente applicati in modo flessibile anche a vari sistemi di fluidi.
Tuttavia, il cablaggio interno di diversi sistemi di fluidi e le dimensioni dei connettori sono diversi, quindi è necessario eseguire il controllo del flusso in anticipo prima di acquistare il punto di prova della pressione corrispondente.
Se la taglia non corrisponde, è anche una cosa fastidiosa.
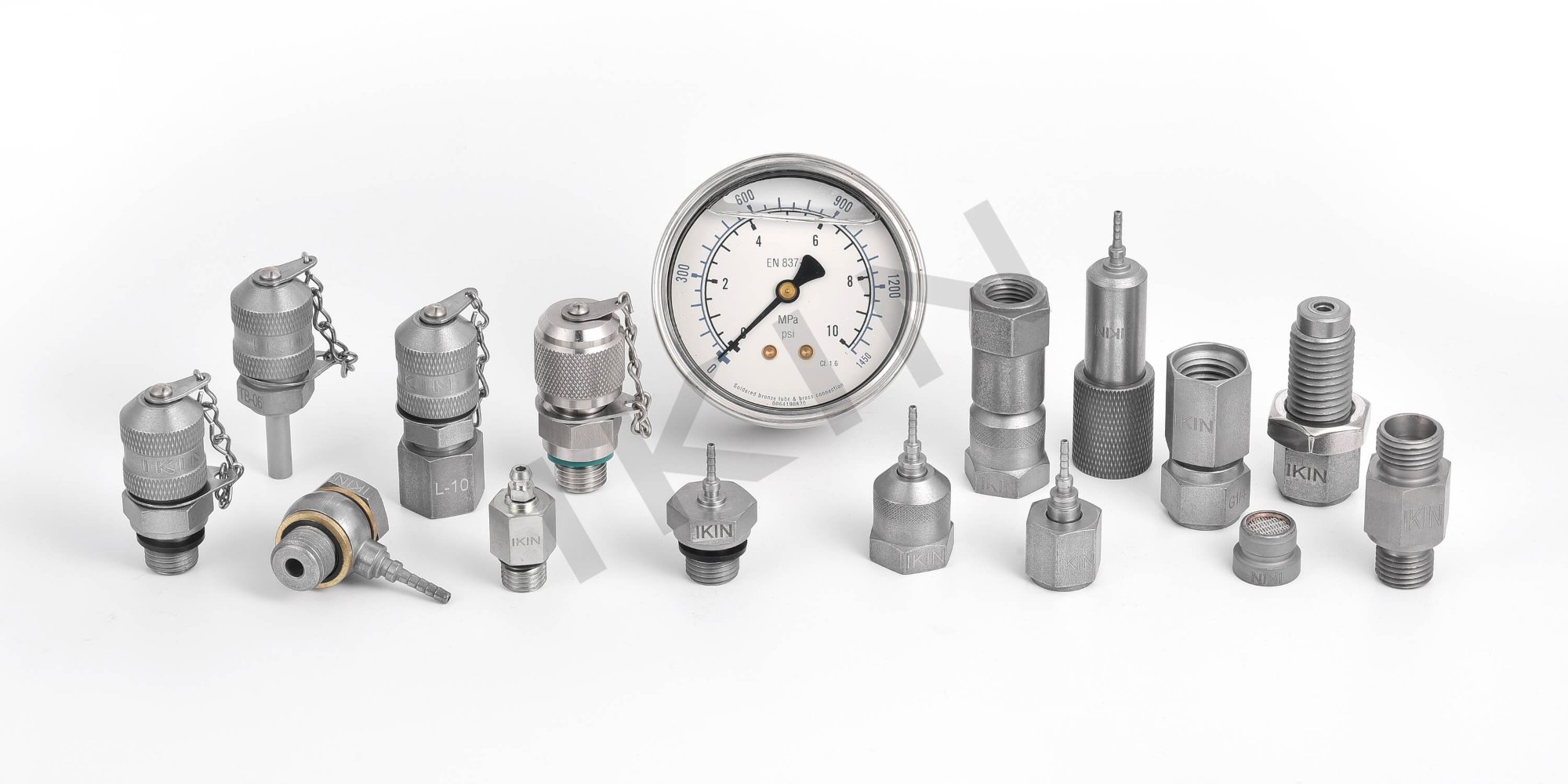
Ikin Fluido
—— I primi 3 produttori in Cina, specializzati in punti di prova idraulici
Vantaggi che puoi trovare a Ikin
Prezzo di fabbrica e moq basso
qualità affidabile, fornitore per Eaton, Hawee e così via
Ispezione perdite 100% Prima della fine
3 anni di garanzia
10 giorni lavorativi per la spedizione all'ingrosso
abbinare altri accessori come minimess, stauff e così via
struttura del design della guarnizione a cono, stabile e di lunga durata
Ottieni il tuo campione gratuito
tra 2 giorni
*Rispettiamo la tua riservatezza e tutte le informazioni sono protette.
Ikin Fluid ha partecipato al Bauma China 2020
Guarda indietro al Bauma China 2020, Shanghai
Il 27 novembre si è conclusa con successo la 4 giorni Bauma China Shanghai 2020.
Nonostante l'impatto della pandemia di covid, così come quattro giorni consecutivi di pioggia, l'entusiasmo del settore delle macchine edili non può ancora essere fermato.
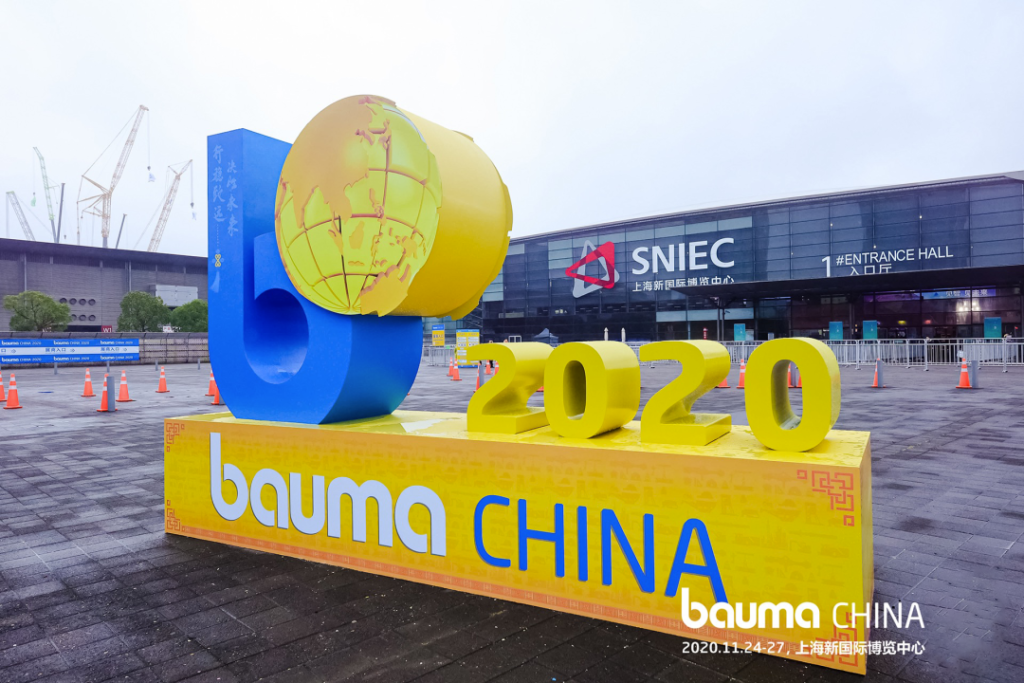
Le maggiori aziende di macchine edili hanno mostrato le loro capacità e la creatività dell'evento ha dominato il pubblico.
Gli espositori hanno mostrato più piacevolmente sorpresa, con molti punti luminosi.
"Online Bauma Show" di Sany diventa un nuovo IP 23,5 miliardi di ordini firmati!
Il debutto del nuovo prodotto ha testimoniato la forza del “Trinity Steel Corps”.
- Nuovo autopompa serie C10 con normative complete e il braccio più lungo
Il nuovo grande escavatore da cento tonnellate SY1250H
46 modelli delle ultime attrezzature Sany da 25 tonnellate a 800 tonnellate di gru
Rullo compressore senza cabina
La prima finitrice ibrida plug-in al mondo
I primi escavatori elettrici prodotti in serie al mondo e altre dozzine dei prodotti più all'avanguardia, tutti in pieno attacco, sorprendendo il pubblico!
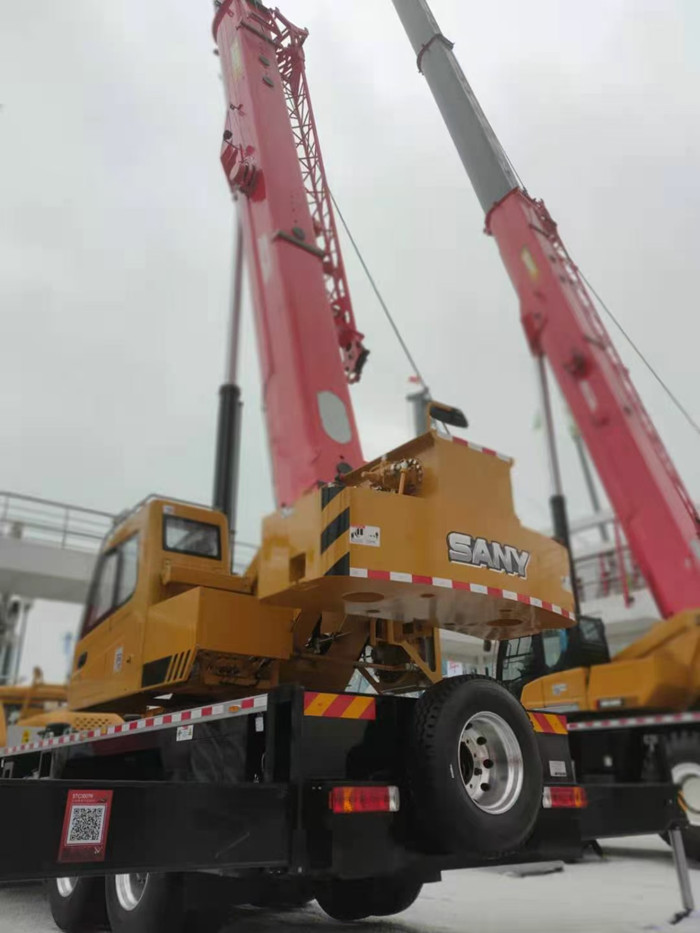
E l'immagine sotto mostra l'accoppiamento di prova di IKIN utilizzato nel sistema idraulico della gru Sany alla fiera Bauma.
Quella che segue è la ripresa dal vivo presso lo stand di Sany. È il nostro IKIN giunto di prova idraulico Usato sulla gru Sany.
We IKIN FLUIDO sono seri alla progettazione e produzione idraulico test puntoS.
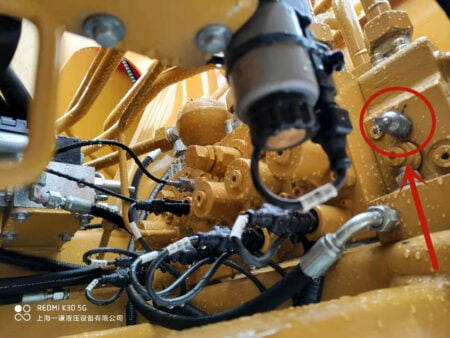
Convergenza XCMG "Steel Corps" Piena di "Saggezza cinese"
Il Gruppo XCMG ha lanciato il sistema informativo globale del servizio ricambi digitali (XCMG-Global Service System, denominato X-GSS)”.
Promuove la trasformazione e l'aggiornamento digitali, intelligenti e non presidiati.
Anche in questo caso, il punto di controllo della pressione IKIN FLUID viene utilizzato nel Lo stand di XCMG.
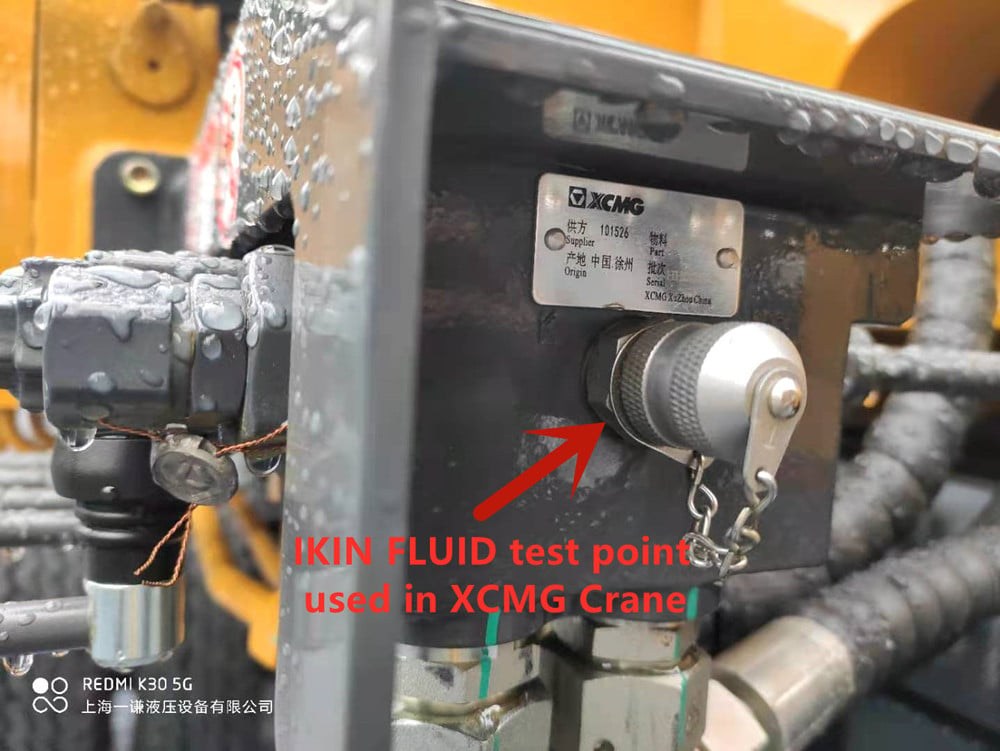
Zoomlion ha firmato oltre 9 miliardi di RMB il primo giorno, il nuovo prodotto ha visto di più al mondo.
- La piattaforma di lavoro aereo semovente a braccio dritto più alta al mondo di Zoomlion ZT68J
- Zoomlion ha esposto molti prodotti di "tecnologia nera"
- I nuovi prodotti high-tech di Zoomlion, dimostrano tutti forti capacità di ricerca e sviluppo e innovazione.
L'immagine seguente mostra l'applicazione delle prese di pressione IKIN, scattata presso lo stand di Zoomlion:
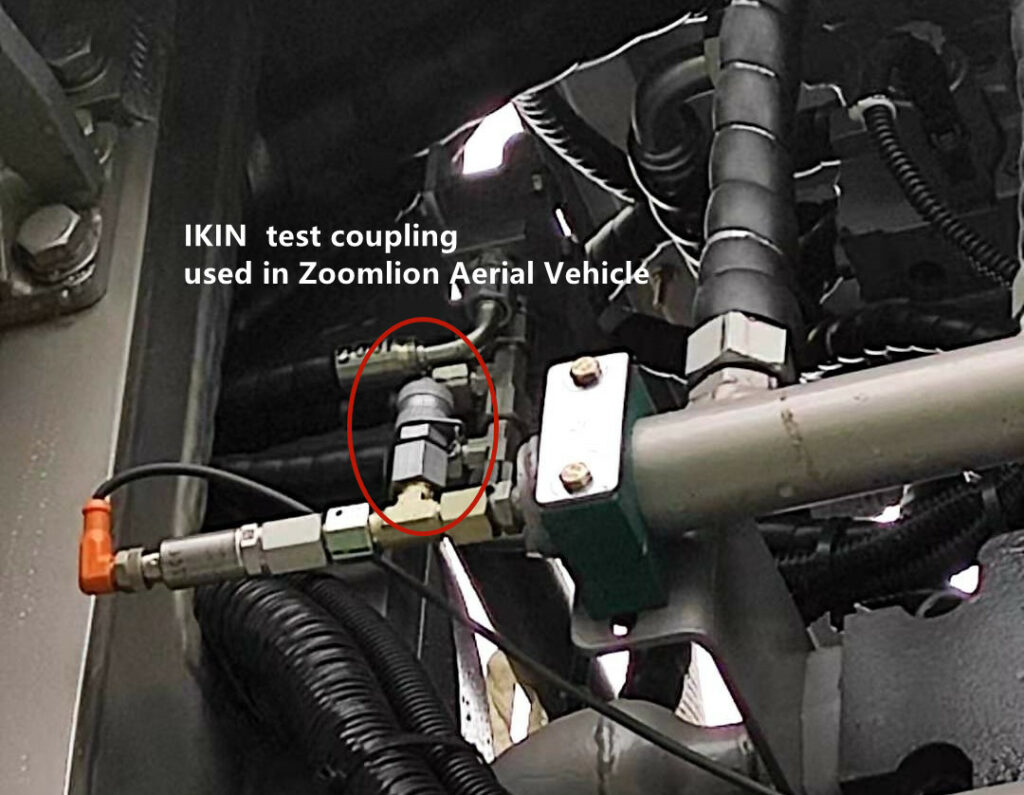
Inoltre, di seguito è riportato il giunto per il test di pressione utilizzato in molti altri stand di clienti.
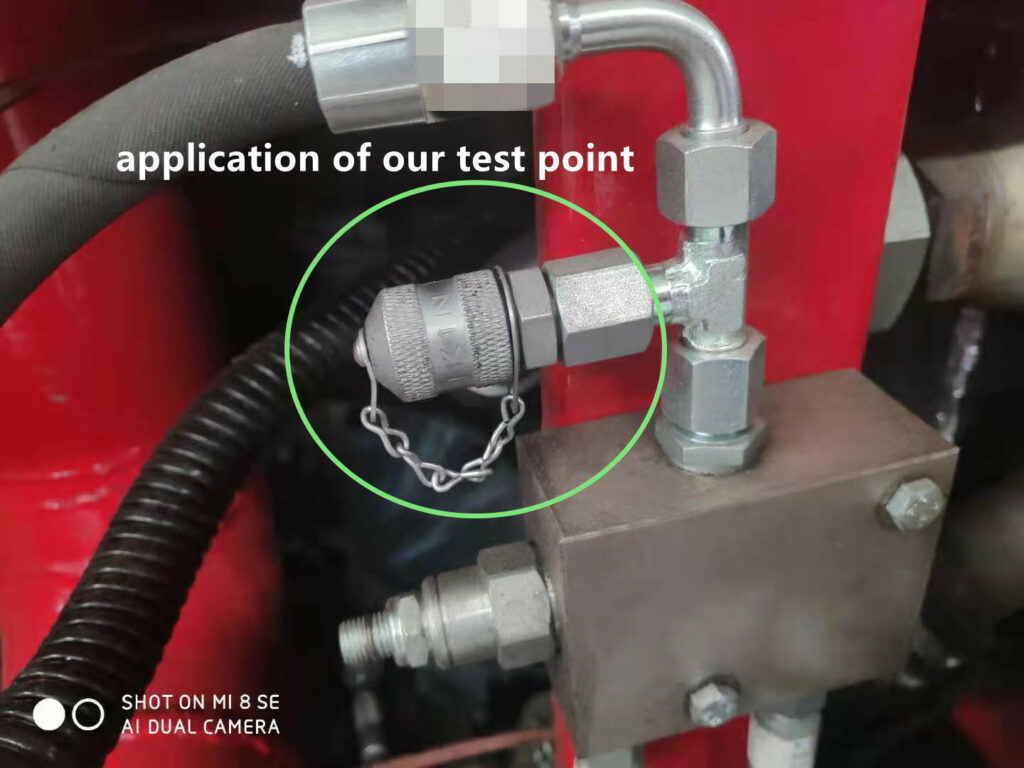
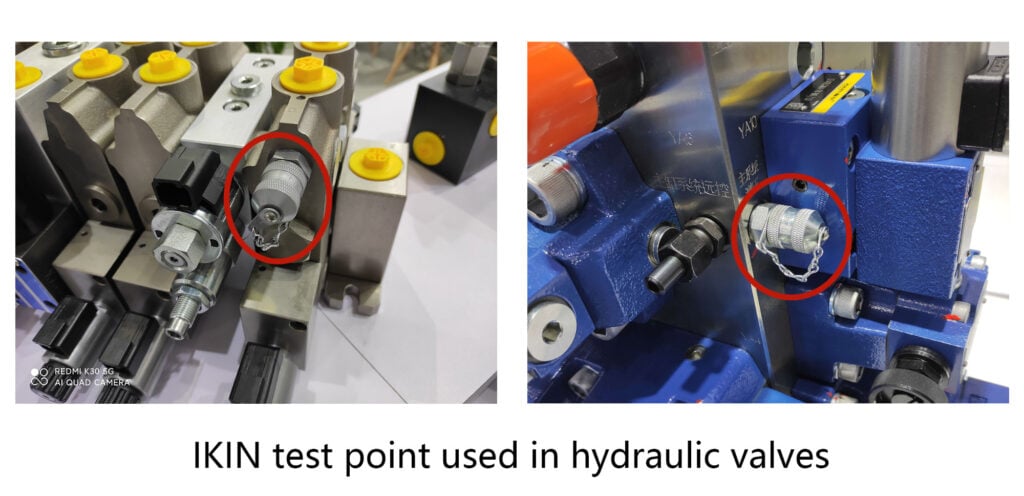
Colpito dall'epidemia, il numero di clienti che partecipano allo spettacolo rispetto all'anno 2018 è diminuito, ma molti clienti vengono ancora alla festa.
Le mostre professionali, con un senso di scienza e tecnologia accuratamente preparate da IKIN, hanno attirato l'attenzione di molti clienti.
Stand di IKIN
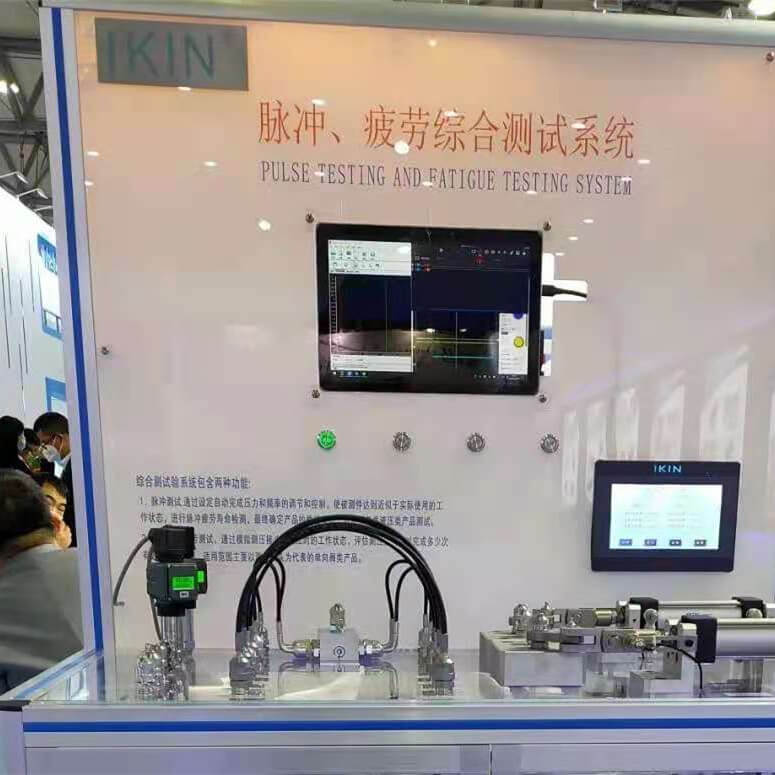
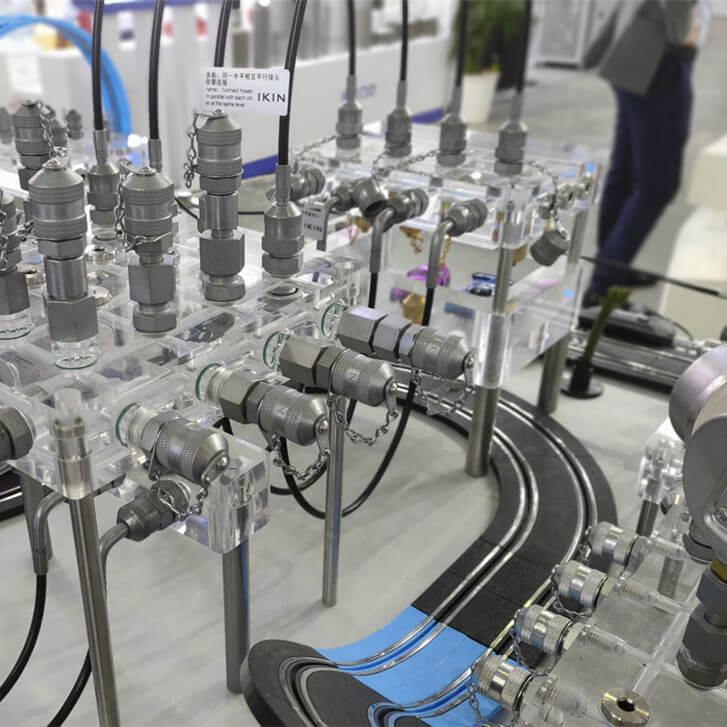
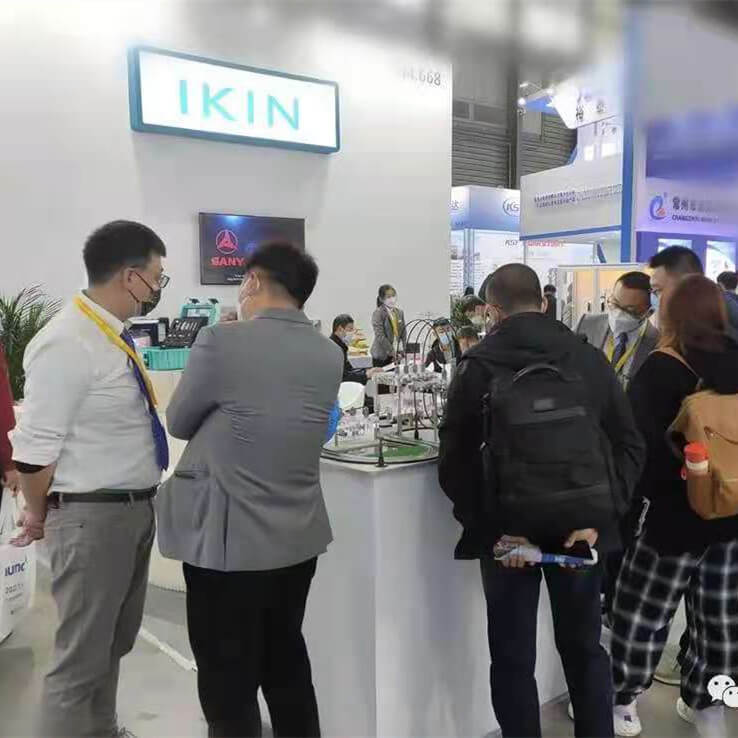
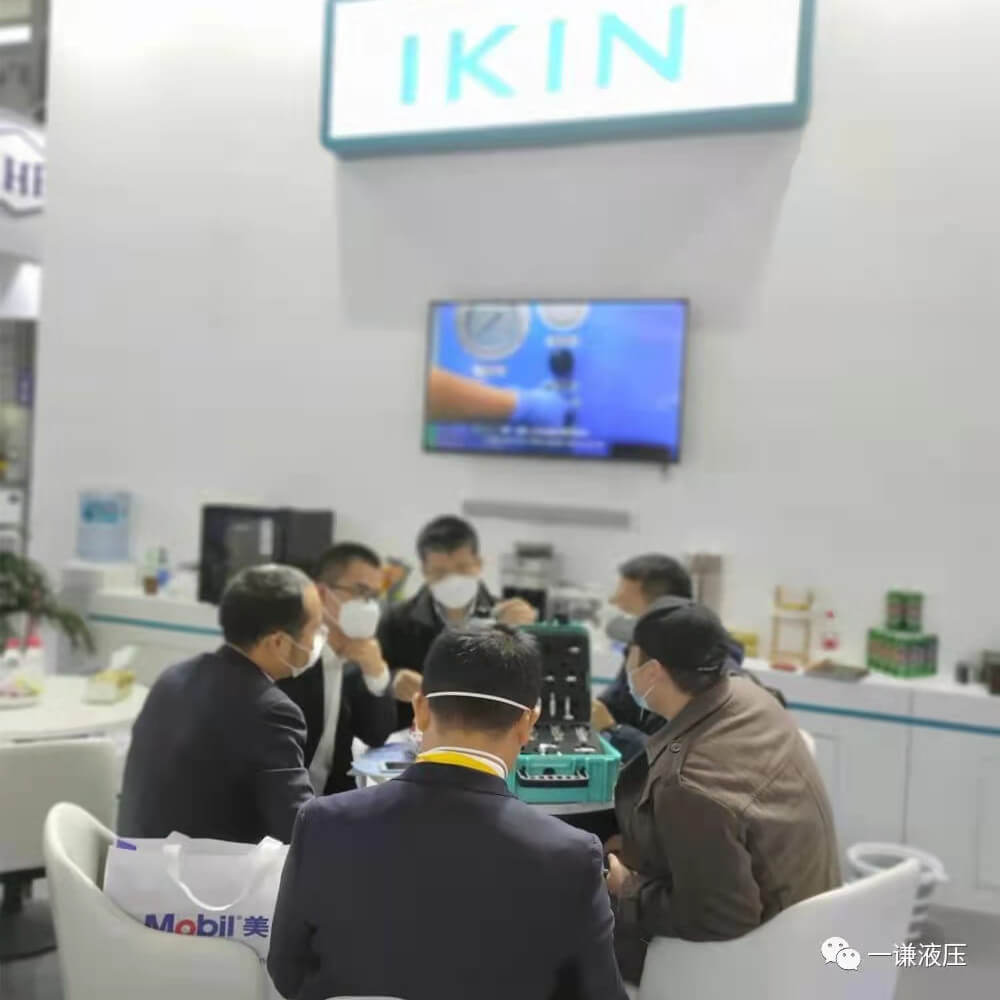
- Produttore cinese
- fornitore per Sany Crane, XCMG Group, Zoomlion, GE e così via all'estero
- specializzati in raccordi di prova idraulici
- affidabile, ad alto costo performanc
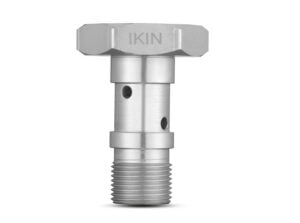
raccordi idraulici, personalizzati per sistema a pressione
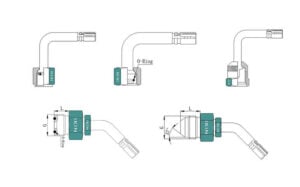
Raccordo per tubo a 90° e 45°
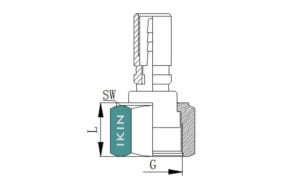
raccordi per tubi microbore, con filettatura femmina ORFS
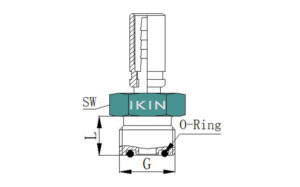
raccordi per tubi microfori, con filettatura maschio ORFS
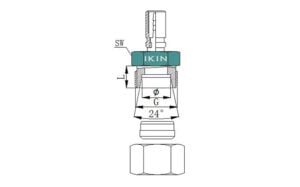
raccordi per tubi di prova, raccordo conico 24°, con filettatura maschio
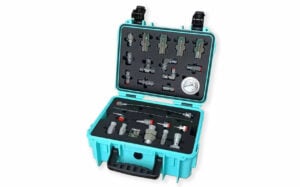
kit di prova della pressione
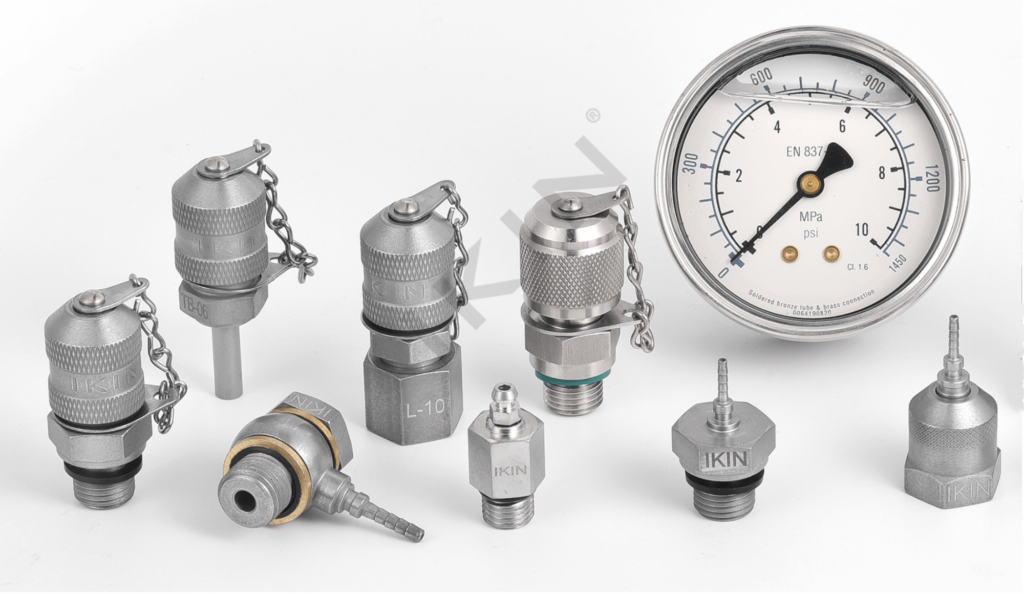
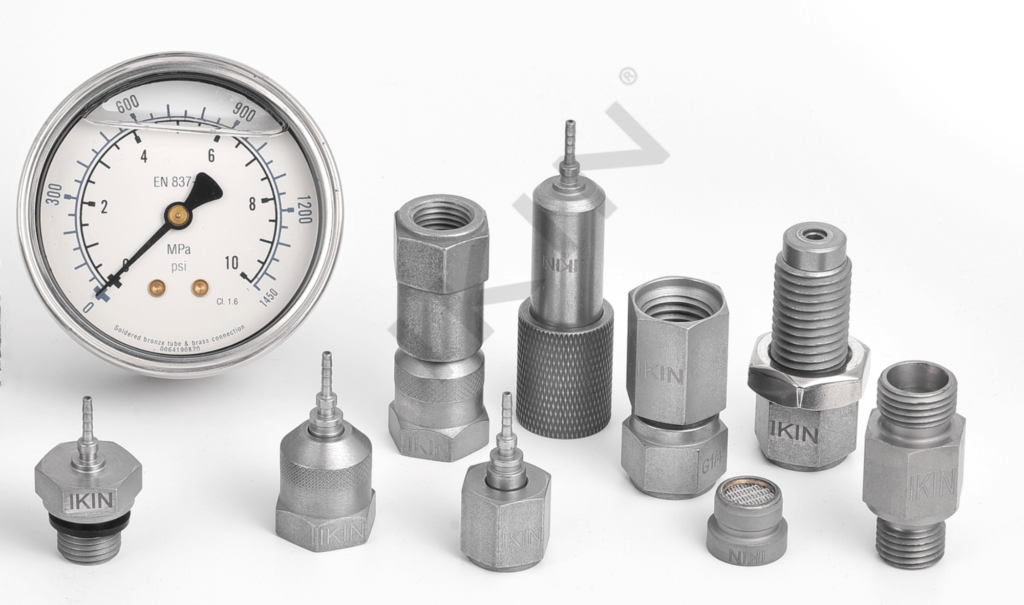
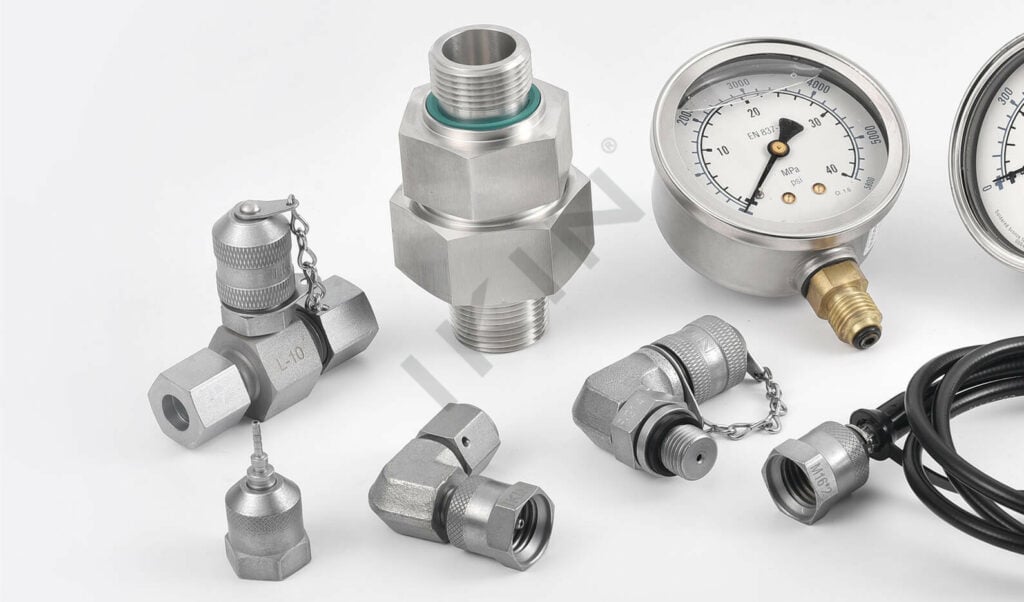
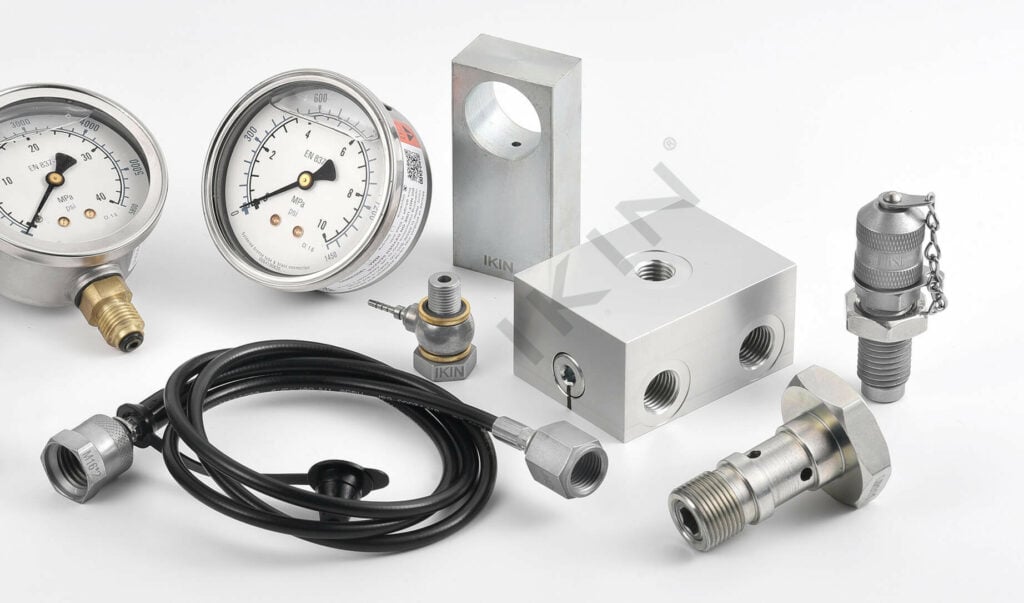
quali sono i tipi di raccordi per tubi idraulici e analisi dei guasti?
I 3 migliori produttori in Cina
fornitore di tubi per punti di prova idraulici
Approvato SGS
quali sono i tipi di tubi flessibili idraulici e raccordi?
Con il rapido sviluppo delle macchine edili cinesi, l'affidabilità dei tubi flessibili idraulici è diventata una delle questioni più preoccupanti del settore.
Il tubo flessibile idraulico è un elemento fondamentale nel sistema di trasmissione idraulica. La qualità del tubo assemblato influisce direttamente sulle prestazioni del sistema idraulico e del motore principale. Parte del guasto del tubo assemblato proviene dalla struttura del nucleo del giunto.
Il nucleo del connettore del tubo è principalmente diviso in due parti, una è la struttura di connessione, per lo più basata su standard SAE, standard ISO e standard KES; L'altra parte è la struttura della parte di crimpatura (struttura della coda), che è abbinata al rivestimento esterno e agli strati di gomma interni ed esterni del tubo per formare una deformazione di crimpatura affidabile per soddisfare le prestazioni del gruppo tubo.
Se la struttura della parte di crimpatura del nucleo del giunto è irragionevole nella progettazione di diversi tipi di tubi flessibili, si verificheranno in larga misura problemi di qualità del prodotto.
Pertanto, anche i tipi di nuclei di giunzione (progettati) selezionati per i tubi in diversi ambienti di lavoro sono diversi e una progettazione ragionevole può evitare o ridurre il verificarsi di guasti.
1. Tipi e caratteristiche dei raccordi per tubi
In tutto il settore dell'assemblaggio di tubi flessibili, ci sono principalmente due tipi di collegamenti affidabili tra giunti di tubi flessibili e tubi flessibili: giunti di tubi flessibili con ritenuta totale e giunti di tubi flessibili staccabili.
Il giunto di crimpatura completo è un processo in cui il modulo di crimpatura in otto parti della macchina di crimpatura schiaccia uniformemente il giunto del tubo flessibile in una certa misura dopo aver assemblato il nucleo del giunto, il tubo flessibile e il rivestimento esterno, in modo che il giunto del tubo flessibile e il tubo flessibile diventino un tutt'uno .
Il connettore del tubo staccabile comprime il tubo attraverso il nucleo del connettore con il cono esterno e il nucleo del connettore, in modo che il tubo si trovi vicino al cono interno del manicotto del connettore, formando un collegamento con una forza di legatura maggiore.
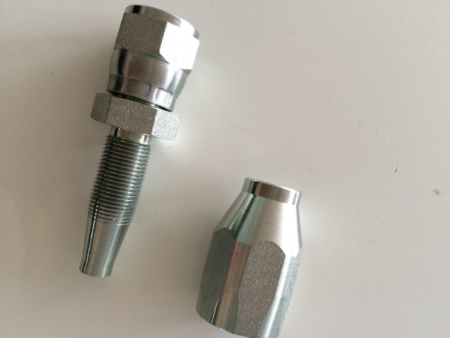
1.1 Forma e caratteristiche di aggraffatura del tubo
Il tipo di ritenuta del tubo dipende principalmente dal tipo di tubo (o dalle dimensioni della gomma interna ed esterna) e dall'ambiente di pressione del tubo assemblato.
Si divide principalmente in tre categorie: aggraffatura in gomma non pelabile, aggraffatura in gomma esterna e aggraffatura in gomma interna ed esterna.
Le caratteristiche di ogni tipologia sono:
(1) Non pelabile e aggraffatura: la gomma interna ed esterna del tubo non deve essere spogliata e il prodotto può essere completato aggraffandolo dopo l'installazione del tubo. La tecnologia di elaborazione è semplice.
Questo tipo di crimpatura viene spesso utilizzato per tubi intrecciati in filo di acciaio con strati di gomma esterni relativamente sottili come gli standard GB / T3683, EN853 e SAE.
(2) Spelatura e aggraffatura: è necessario rimuovere lo strato di gomma esterno del tubo fino a una certa lunghezza (lo strato di gomma esterno è più spesso), che viene utilizzato per rendere migliore il contatto dello strato di rinforzo del filo di acciaio con la scanalatura del dente di la giacca.
Quando la giacca si restringe e si deforma sotto la forza esterna, si deformerà saldamente il filo di acciaio, impedendo così al giunto di estrarsi se sottoposto a un impatto ad alta pressione.
Questo tipo di aggraffatura è applicabile principalmente ai tubi avvolti in filo di acciaio come gli standard GB / T10544, EN856 e SAE.
(3) Spelatura e aggraffatura della gomma interna ed esterna: gli strati di gomma interni ed esterni devono essere spelati a una certa lunghezza (lo spessore della gomma interna ed esterna), lo strato di filo di acciaio e lo strato di gomma interno vengono estrusi in un'onda forma, generalmente adatto per GB / T10544, EN856-R13, R15, ecc. Specifiche (32 o più inclusi 32) tubo a spirale in filo di acciaio ad altissima pressione.
1.2. Raccordo portagomma di tipo ritenuta
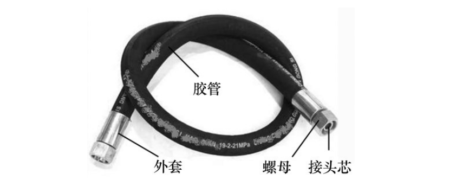
Il giunto del tubo flessibile di tipo ritenuta è composto principalmente dal nucleo del giunto, dal rivestimento esterno (il dado è una parte opzionale) e da altre parti.
1) Materiali, tipi e caratteristiche del nucleo del giunto
I materiali comunemente usati per le anime dei giunti sono gli acciai 20, 35 e 45. Per le anime a giunti diritti, vengono spesso utilizzati acciai 35 e 45, che hanno una forte resistenza alla deformazione. Considerando la producibilità delle anime di giunzione a flessione, vengono generalmente utilizzati 20 o 35 acciai.
Con la diffusione della tecnologia di piegatura a caldo, gli acciai 35 e 45 possono essere utilizzati anche per le anime dei giunti a gomito.
Le caratteristiche strutturali del nucleo del giunto sono strettamente correlate alla forma di aggraffatura del tubo flessibile e, in base alla regolarità della struttura, i tipi di anime del giunto sono approssimativamente suddivisi in: struttura a zigzag, struttura rettangolare, struttura di bloccaggio interna, ecc.
(1) Il nucleo articolare della struttura a dente di sega, comunemente noto come tipo spinato, è composto principalmente da scanalature a dente di sega e l'angolo tra l'ipotenusa e l'asse non è generalmente superiore a 20 °.
La parte superiore della dentatura è a forma di arco o piatta e il piano e il lato corto della dentatura sono angoli arrotondati e lisci (0,2 ~ 0,5 mm) per evitare danni allo strato di gomma interno del tubo durante l'assemblaggio e l'aggraffatura.
Il nucleo del giunto di questa struttura ha una forte tenuta e resistenza allo strappo e viene utilizzato principalmente per tubi in gomma avvolti in filo di acciaio.
(2) Nucleo del giunto a struttura rettangolare: composto principalmente da diverse scanalature rettangolari, i corpi di 5 ~ 7 scanalature formano una scanalatura di tenuta e la profondità della scanalatura è generalmente di 0,3 ~ 0,6 mm.
La superficie di transizione tra la parte superiore della scanalatura e la parte inferiore della scanalatura è generalmente liscia con angoli arrotondati, con un raggio di 0,1 mm ~ 0,3 mm.
Evitare danni allo strato di gomma interno del tubo durante l'assemblaggio e la crimpatura. La struttura complessiva è semplice, con buone prestazioni di tenuta, ma bassa resistenza allo strappo. Questa struttura viene spesso utilizzata per tubi in resina, tubi intrecciati in filo di acciaio e altri tipi di tubi.
I materiali comunemente usati per le anime dei giunti sono gli acciai 20, 35 e 45. Per le anime a giunti diritti, vengono spesso utilizzati acciai 35 e 45, che hanno una forte resistenza alla deformazione. Considerando la producibilità delle anime di giunzione a flessione, vengono generalmente utilizzati 20 o 35 acciai.
Con la diffusione della tecnologia di piegatura a caldo, gli acciai 35 e 45 possono essere utilizzati anche per le anime dei giunti a gomito.
Le caratteristiche strutturali del nucleo del giunto sono strettamente correlate alla forma di aggraffatura del tubo flessibile e, in base alla regolarità della struttura, i tipi di anime del giunto sono approssimativamente suddivisi in: struttura a zigzag, struttura rettangolare, struttura di bloccaggio interna, ecc.
Con il rapido sviluppo delle macchine edili cinesi, l'affidabilità dei tubi flessibili idraulici è diventata una delle questioni più preoccupanti del settore.
Il tubo flessibile idraulico è un elemento fondamentale nel sistema di trasmissione idraulica. La qualità del tubo assemblato influisce direttamente sulle prestazioni del sistema idraulico e del motore principale. Parte del guasto del tubo assemblato proviene dalla struttura del nucleo del giunto.
Il nucleo del connettore del tubo è principalmente diviso in due parti, una è la struttura di connessione, per lo più basata su standard SAE, standard ISO e standard KES; L'altra parte è la struttura della parte di crimpatura (struttura della coda), che è abbinata al rivestimento esterno e agli strati di gomma interni ed esterni del tubo per formare una deformazione di crimpatura affidabile per soddisfare le prestazioni del gruppo tubo.
Se la struttura della parte di crimpatura del nucleo del giunto è irragionevole nella progettazione di diversi tipi di tubi flessibili, si verificheranno in larga misura problemi di qualità del prodotto.
Pertanto, anche i tipi di nuclei di giunzione (progettati) selezionati per i tubi in diversi ambienti di lavoro sono diversi e una progettazione ragionevole può evitare o ridurre il verificarsi di guasti.
Con il rapido sviluppo delle macchine edili cinesi, l'affidabilità dei tubi flessibili idraulici è diventata una delle questioni più preoccupanti del settore.
Il tubo flessibile idraulico è un elemento fondamentale nel sistema di trasmissione idraulica. La qualità del tubo assemblato influisce direttamente sulle prestazioni del sistema idraulico e del motore principale. Parte del guasto del tubo assemblato proviene dalla struttura del nucleo del giunto.
Il nucleo del connettore del tubo è principalmente diviso in due parti, una è la struttura di connessione, per lo più basata su standard SAE, standard ISO e standard KES; L'altra parte è la struttura della parte di crimpatura (struttura della coda), che è abbinata al rivestimento esterno e agli strati di gomma interni ed esterni del tubo per formare una deformazione di crimpatura affidabile per soddisfare le prestazioni del gruppo tubo.
Se la struttura della parte di crimpatura del nucleo del giunto è irragionevole nella progettazione di diversi tipi di tubi flessibili, si verificheranno in larga misura problemi di qualità del prodotto.
Pertanto, anche i tipi di nuclei di giunzione (progettati) selezionati per i tubi in diversi ambienti di lavoro sono diversi e una progettazione ragionevole può evitare o ridurre il verificarsi di guasti.
(3) Nucleo del giunto della struttura di chiusura interna, noto anche come struttura anti-pull-out.
Questo tipo di struttura è appositamente progettato per evitare che il tubo venga estratto dal giunto del tubo e la tenuta è assicurata dalla struttura rettangolare.
Pertanto, il nucleo del giunto della struttura di bloccaggio interna è in realtà una combinazione della struttura antiestrazione e della struttura rettangolare.
Questo tipo di giunto ha le caratteristiche di alta affidabilità e lunga durata. Viene utilizzato principalmente per tubi di avvolgimento in filo di acciaio ad altissima pressione e di grande diametro e assemblaggio di tubi flessibili di avvolgimento in filo di acciaio dinamico in condizioni di lavoro difficili.
2) Materiale, tipo e caratteristiche del cappuccio esterno
Il materiale del rivestimento esterno è generalmente acciaio 20 e la buona deformazione plastica del materiale viene utilizzata per rendere il tubo di gomma estruso del dente del rivestimento esterno e la tenuta a tenuta del nucleo del giunto.
Esistono anche molti tipi di calotte esterne, principalmente per diversi nuclei di giunti, diversi ambienti di lavoro, diverse condizioni di lavoro specifiche e diverse forme strutturali richieste.
Di solito il lato interno della giacca è costituito da alcune scanalature o dentellature. Sono presenti scanalature quadrate, trapezi, zigzag, ecc., Che devono essere utilizzate insieme a diversi tipi di anime di giunzione.
I tipi di struttura comunemente usati dei cappucci esterni sono approssimativamente suddivisi nei seguenti tre tipi:
(1) Rivestimento della scanalatura del dente a forma di onda. La superficie esterna della giacca ondulata è principalmente un cilindro liscio e l'angolo tra l'ipotenusa del dente interno e l'asse è di 25 ° ~ 45 °.
Il lato radiale e l'ipotenusa sono collegati da angoli arrotondati di 0,2 ~ 0,5 mm, generalmente composti da 3 ~ 5 denti interni. Adatto principalmente per tubi assemblati a media e bassa pressione non pelabili, come tubi in resina e tubi intrecciati in filo di acciaio; Può essere utilizzato in combinazione con struttura a dente di sega e nucleo di giunzione a struttura rettangolare, con debole resistenza allo strappo e tecnologia di lavorazione semplice.
(2) Rivestimento trapezoidale della scanalatura del dente. La superficie esterna è un cilindro liscio e la superficie interna è una scanalatura con un certo numero di denti trapezoidali.
L'angolo tra l'ipotenusa e l'asse è di 25 ° ~ 45 ° e ciascuna dentatura è una scanalatura rettangolare. La parte superiore della dentatura è un piano con una larghezza da 1 a 2 mm e gli angoli acuti sono sottoposti a transizione con un angolo arrotondato di 0,2 mm.
Può essere utilizzato in combinazione con un'anima di giunzione a struttura rettangolare per formare un'efficace resistenza allo strappo, adatta per la spelatura di tubi in treccia di media e alta pressione e tubi di avvolgimento.
(3) Copertura alveolare composta. La superficie esterna è una scanalatura a forma di T corrispondente alla dislocazione interna del dente e la superficie interna è una scanalatura con un certo numero di denti trapezoidali bilaterali.
È adatto per l'uso con il nucleo del giunto della struttura di bloccaggio interna e viene utilizzato per l'assemblaggio di tubi flessibili ad altissima pressione e grande portata.
Con il graduale sviluppo di macchine edili su larga scala, anche il sistema idraulico si sviluppa costantemente in direzione dell'alta pressione e l'applicazione di questa forma strutturale sta diventando sempre più ampia.
2. Selezione della quantità di aggraffatura del giunto
A seconda dei diversi tipi di tubi e giunti, anche la quantità di aggraffatura appropriata è un fattore chiave per garantire che l'assieme tubo flessibile sia senza problemi.
La quantità di aggraffatura influisce direttamente sulle prestazioni di tenuta, sulla resistenza allo strappo e sulla durata.
Generalmente, quando si valuta la qualità della deformazione di crimpatura, vedere se lo spazio tra la superficie interna del dente del manicotto esterno e la scanalatura del dente del nucleo del giunto è riempito dal tubo di gomma.
Solo quando la deformazione è soddisfatta si possono garantire la resistenza allo sfilamento e le prestazioni di tenuta.
In generale, la quantità di aggraffatura del tubo di gomma interno come la gomma nitrilica dovrebbe rendere la compressione dello strato di gomma interno (40% ~ 45% per tubo intrecciato in filo di acciaio, 50% ~ 55% per tubo avvolto in filo di acciaio a quattro e sei strati); La quantità di crimpatura del tubo di resina e del tubo in PTFE garantisce che la quantità di compressione dello strato di gomma interno sia compresa tra 25% e 30%.
Nel caso di garantire il sigillo, minore è l'importo della ritenuta, meglio è. Attraverso il calcolo e la verifica, viene selezionato un determinato importo di ritenuta.
3. Conclusione
L'articolo discute i tipi di nuclei di giunzione e cappucci esterni utilizzati nell'assemblaggio del tubo flessibile di ritenuta.
Quando la piegatura del tubo presenta problemi di qualità e tipi di guasti.
Ha analizzato le ragioni e come utilizzare una configurazione di crimpatura ragionevole e giunti a crimpare, al fine di evitare il problema delle basse prestazioni di assemblaggio del tubo causato da una struttura di crimpatura del tubo irragionevole.
Migliora e controlla efficacemente l'affidabilità del tubo assemblato e fornisce anche un forte supporto per il rapido sviluppo di vari macchinari di ingegneria idraulica.
Ikin Fluido
—— I primi 3 produttori in Cina, specializzati in punti di prova idraulici
Vantaggi che puoi trovare a Ikin
Prezzo di fabbrica e moq basso
qualità affidabile, fornitore per Eaton, Hawee e così via
Ispezione perdite 100% Prima della fine
3 anni di garanzia
10 giorni lavorativi per la spedizione all'ingrosso
abbinare altri accessori come minimess, stauff e così via
struttura del design della guarnizione a cono, stabile e di lunga durata
Ottieni il tuo campione gratuito
tra 2 giorni
*Rispettiamo la tua riservatezza e tutte le informazioni sono protette.
Come mantenere e gestire il sistema idraulico della pressa per estrusione
Come mantenere e gestire il sistema idraulico della pressa per estrusione
Le presse per estrusione di alluminio di grandi dimensioni possono essere utilizzate per produrre prodotti di estrusione di alluminio ad alta specifica come profili industriali, profili di transito ferroviario e radiatori di grandi dimensioni.
Può essere utilizzato in aerospaziale, transito ferroviario, automobili, navi, edilizia, produzione di macchinari, energia elettronica e altri campi. Nel processo di lavorazione della pressa per estrusione di alluminio di grandi dimensioni, per garantire la precisione di lavoro e le alte prestazioni, la premessa è di avere un certo grado di stabilità. Una volta che la stabilità dell'estrusore non riesce a soddisfare gli standard di produzione, la qualità dei prodotti realizzati sarà notevolmente compromessa. E le imprese subiranno anche enormi perdite economiche.
一. Problemi comuni del sistema idraulico di grandi presse per estrusione di alluminio e loro soluzioni
(一) Perdita nel tubo:
È molto probabile che la posizione di saldatura del tubo e della flangia provochi perdite dal tubo. Inoltre, è estremamente probabile che la superficie di installazione della flangia del tubo e la posizione della vite causino perdite dal tubo.
Il verificarsi di perdite nei tubi è causato principalmente dall'allentamento delle viti e dei giunti dei tubi causato dal funzionamento a lungo termine. Allo stesso tempo, dopo che la guarnizione della superficie di montaggio della flangia sta invecchiando, l'anello di tenuta verrà danneggiato.
Una saldatura impropria ha causato pori e crepe e si sono verificate perdite. Inoltre, il tempo di utilizzo era troppo lungo, la consapevolezza della sicurezza non era forte e la manutenzione tempestiva non era stata eseguita, il che ha causato l'espansione della situazione e alla fine la perdita. Possiamo eliminare le vibrazioni del tubo e migliorare la stabilità aggiungendo fascette e staffe per tubi.
Se l'operazione di saldatura non è standardizzata, ci sono pori o crepe, possiamo lucidare nella posizione originale e dopo che i detriti sono stati rimossi, possiamo saldare di nuovo.
(二) Perdita di olio nel cilindro:
1. La percentuale di perdite dal cilindro dell'olio è relativamente alta. A causa delle condizioni di lavoro a lungo termine, causerà inevitabilmente una grande quantità di particelle abrasive. Allo stesso tempo, poiché la posizione esposta dello stelo del pistone è esposta all'aria per lungo tempo, è inevitabile che ci sia una grande quantità di polvere e polvere di alluminio attaccata.
In tali situazioni, di solito viene utilizzato un anello antipolvere per raschiare. Tuttavia, in considerazione dell'effetto dell'anello parapolvere, è difficile raschiare completamente via, in modo che la guarnizione dello stelo del pistone sia danneggiata, il che a sua volta provoca perdite. Pertanto, di solito vengono adottati due metodi di trattamento per le perdite dal cilindro dell'olio: in primo luogo, pulire il cilindro dell'olio e sostituire le guarnizioni; In secondo luogo, confermare se lo strato superficiale dello stelo del pistone è usurato o meno,
2. L'asse del cilindro non è parallelo al binario di guida e l'errore supera l'intervallo standard: 0,04-0,08 mm / m. A loro volta, i bulloni di fissaggio del coperchio di estremità sono stati allentati e la guarnizione non è riuscita. Quindi dobbiamo mantenere il parallelismo e controllare l'errore entro l'intervallo standard.
3. La guarnizione è rotta e la perdita di olio si verifica a causa della contropressione e l'impostazione della pressione è troppo alta. A sua volta, il sigillo è esposto a una pressione eccessiva e il sigillo si rompe. Ciò richiede il ripristino della pressione del sistema idraulico e il test dei componenti della valvola di controllo idraulico.
4. Le guarnizioni sono molto usurate e si guastano perché l'olio idraulico è gravemente inquinato e produce molte impurità. Quando la temperatura dell'olio rimane a lungo ad alta temperatura, l'olio idraulico viene gradualmente ossidato, determinando la produzione di depositi colloidali. Quando la temperatura dell'olio rimane a lungo in uno stato di bassa temperatura, l'elasticità della guarnizione andrà persa. L'invecchiamento della guarnizione è causato dall'accumulo di una grande quantità di residui d'olio.
Quindi dobbiamo rafforzare la gestione dell'olio idraulico e controllare rigorosamente l'intrusione delle fonti di inquinamento; Confermare le condizioni di lavoro del sistema di raffreddamento dell'attrezzatura idraulica e garantirne il normale funzionamento. La temperatura più adatta è 30-45 ℃.
5. Quando la guarnizione appropriata non è selezionata per il trattamento di sigillatura, quando si seleziona la guarnizione. Per tenere conto del materiale, del modello e della rugosità della tenuta, si verifica una perdita di olio. Pertanto, quando si selezionano i sigilli, identificare attentamente le caratteristiche dei sigilli e selezionare i sigilli ragionevoli corrispondenti.
(三) Perdita di componenti della valvola di controllo:
La perdita interna è la più comune nelle perdite dei componenti della valvola di controllo. La causa principale delle perdite interne è il grande accumulo di impurità idrauliche, che a sua volta blocca i componenti della valvola di controllo; Inoltre, un'usura eccessiva del nucleo della valvola e una chiusura impropria possono causare perdite.
Una pressione eccessiva causerà il bloccaggio idraulico della bobina, che causerà anche perdite. Si consiglia di pulire ripetutamente la valvola di controllo dopo lo smontaggio o di lucidare i componenti della valvola di controllo. Al fine di migliorarne la precisione e riportarlo al suo aspetto originale.
(四) Guasto dell'elettrovalvola: il guasto dell'elettrovalvola può essere suddiviso nei seguenti tipi:
1. La bobina non si muove: (1) Il guasto dell'elettromagnete, combinato con la vibrazione e il rilevamento del campo magnetico, si può vedere che la bobina non si muove; (2) Il nucleo della valvola è bloccato, l'olio cambia e la molla di ritorno è difettosa. Dopo il rilevamento delle vibrazioni, è possibile vedere il guasto bloccato nel nucleo della valvola;
2. Grande perdita di pressione: (1) il flusso è troppo grande e la dimensione è errata, il che può essere visto dall'ispezione congiunta delle vibrazioni e del campo magnetico; (2) La bobina non si muove in posizione e il guasto di inceppamento della bobina può essere visto attraverso il rilevamento delle vibrazioni;
3. Perdita di flusso magnetico: i difetti compaiono sulla superficie della bobina elettromagnetica, che possono essere visti dal rilevamento del campo magnetico.
4. Urto (vibrazione): la velocità di chiusura della bobina è troppo elevata e le viti sono allentate, il che può essere visto dal rilevamento delle vibrazioni.
In considerazione delle cause dei problemi di cui sopra, adottare le misure corrispondenti per risolvere il problema.
二. Manutenzione e gestione impianto idraulico di presse per estrusione alluminio di grandi dimensioni
(一) Redigere un piano di manutenzione giornaliera
(1) Per alcune apparecchiature esposte all'aria per lungo tempo, pulirle regolarmente per mantenere le parti esposte dell'apparecchiatura pulite e prive di impurità;
(2) Mantenere l'ambiente operativo pulito e ordinato per evitare l'intrusione di polvere e detriti e inquinare il sistema idraulico;
(3) Effettuare ispezioni di pattuglia in qualsiasi momento in cui il tasso di perdite d'olio è relativamente alto e, una volta trovate, adottare le misure corrispondenti per risolverle immediatamente;
(4) Standardizzare il processo di ispezione. Delinea il percorso di ispezione e la parte più alta del punto di fuoriuscita di petrolio. Dopo che una certa fase del lavoro di ispezione è stata completata, deve essere consegnato al personale della fase successiva e lo stato di avanzamento del lavoro della fase precedente deve essere spiegato in dettaglio;
(5) Registrare lo stato operativo originale in dettaglio. Comprendere le normali condizioni di lavoro del sistema idraulico può aiutare a scoprire e risolvere i problemi in tempo durante il processo di ispezione, migliorare l'efficienza del lavoro ed evitare rischi per la sicurezza.
(二) Sviluppare un sistema di ispezione e manutenzione regolare e programmare una data per tarare i vari strumenti del sistema idraulico. Assicurarsi che lo strumento funzioni correttamente e abbia un alto grado di precisione.
Allo stesso tempo, il sistema idraulico deve essere sottoposto a prova di pressione per impostare un valore di pressione ragionevole per mantenere la temperatura normale. Per evitare squilibri di pressione, la temperatura è troppo bassa o troppo alta, con conseguenti perdite. Pulire e sostituire regolarmente l'elemento filtrante per determinare la composizione dei detriti e l'inquinamento dell'olio idraulico.
Confermare il grado di usura e usura del sistema idraulico e campionare e testare l'olio idraulico dell'estrusore ogni tre mesi. Controllare la viscosità dell'olio idraulico, il valore di acidità, l'umidità, le particelle e altri elementi in modo che sia possibile adottare misure ragionevoli per risolverli.
三. Conclusione
Attraverso l'analisi, si può confermare che la perdita del sistema idraulico della pressa per estrusione di alluminio è principalmente causata dalla mancanza di stabilità del sistema idraulico. Quindi dobbiamo prendere le misure corrispondenti.
Tuttavia, le soluzioni sono sempre attribuibili a misure correttive e non possono avere un effetto preventivo.
Pertanto, è di grande importanza prendere la necessaria manutenzione e gestione del sistema idraulico nel lavoro quotidiano.
flange delle valvole prodotti di progettazione dei fluidi raccordi a flangia idraulica raccordi idraulici bspp flange delle valvole raccordi a scollegamento rapido valvola del fluido raccordi a collegamento rapido di potenza del fluido americano raccordi di prova idraulica raccordi di prova della pressione idraulica tubo di prova idraulico raccordi di prova idraulica raccordi porta di prova idraulica raccordi di prova idraulica cat raccordi di prova idraulica john deere raccordi per manometri idraulici raccordi per tubi di prova idraulici raccordi per test idraulici hitachi raccordi per test idraulici jcb raccordi per test idraulici jic kit di raccordi per test idraulici raccordi per test idraulici komatsu raccordi per test idraulici metrici raccordi per punti di prova idraulici connettori per punti di prova idraulici caterpill raccordi per porta di prova idraulica ar raccordi per porta di prova idraulica parker raccordi per prova idraulica parker raccordi per prova idraulica parker raccordi per prova idraulica stauff raccordi per test idraulici raccordi per test idraulici volvo collegamento manometro punto di prova del fluido idraulico raccordi parker filettature di collegamento punto di prova raccordi per porta di prova idraulica accoppiamento idraulico e tubo di prova raccordi punto di prova pressione accessori idraulici tubi di prova assemblaggi punto di prova raccordi punto di prova tubi flessibili raccordi manometro accoppiamenti di prova per il controllo della pressione
Qual è l'applicazione del punto rotante idraulico
Qual è l'applicazione del punto rotante idraulico
Il sistema di alimentazione idraulica è ampiamente utilizzato in campo industriale in virtù dei suoi numerosi vantaggi. Quando l'attrezzatura rotante deve utilizzare il mezzo idraulico come potenza di trasmissione, ci sono requisiti rigorosi sulla pressione e sulla precisione di controllo del mezzo idraulico, solitamente una pressione superiore a 30 MP, e un funzionamento affidabile.
Per lo sviluppo e l'applicazione di punti rotanti, è necessario semplificare la struttura dell'attrezzatura ottenendo una migliore funzione di conversione. L'applicazione più ampia e tipica dei punti rotanti idraulici è negli avvolgitori di acciaio per nastri larghi laminati a caldo delle apparecchiature di laminazione dell'acciaio. E sui cilindri di espansione e contrazione di svolgitori, avvolgitori e altre apparecchiature sulla linea di produzione di nastri laminati a freddo.
1. Analisi del principio strutturale del punto rotante idraulico
1.1 Struttura e principio
Il punto rotante idraulico ha due porte dell'olio di controllo e una porta di scarico, che sono rispettivamente collegate alle tubazioni fisse del sistema idraulico. Ogni pipeline esterna è collegata staticamente al guscio del punto rotante.
Il guscio del punto rotante idraulico è fissato sul guscio dell'attrezzatura principale corrispondente e rimane relativamente statico con la base dell'attrezzatura principale, collegata all'attrezzatura principale attraverso il mandrino. La distanza tra il diametro esterno del mandrino e il diametro interno del giunto rotante idraulico. Lo spazio tra la canna del cilindro e il pistone deve essere uguale a quello del cilindro idraulico, generalmente 0,04 mm ~ 0,07 mm. Quando le condizioni lo consentono, abbassare il limite il più possibile. Ogni volta che si avvia il sistema idraulico, si forma una pellicola d'olio a pressione statica nello spazio corrispondente, che protegge il mandrino e il giunto rotante idraulico dall'usura e svolge un ruolo di tenuta.
La guarnizione rotante è installata sul mandrino dell'attrezzatura e la sua funzione principale è quella di isolare la cavità di ingresso dell'olio e la cavità di ritorno dell'olio per formare due spazi sigillati indipendenti. La maggior parte dei materiali sono materiali compositi resistenti all'usura o materiali metallici. Le tenute rotanti devono resistere a pressioni elevate superiori a 30 MP e devono essere resistenti agli urti ad alta pressione, non facili da deformare e avere piccole perdite. La tenuta rotante e la parete interna del giunto rotante non sono in contatto e tra i due vi è attrito fluido.
La vibrazione e l'impatto generati dal funzionamento ad alta velocità dell'attrezzatura principale vengono trasmessi al giunto rotante idraulico attraverso il mandrino, determinando una certa oscillazione del giunto rotante. Due cuscinetti vengono utilizzati per supportare la forza assiale e la forza radiale generata dall'oscillazione dell'alloggiamento del giunto rotante e per realizzare il posizionamento preciso dell'albero centrale dell'attrezzatura e del giunto rotante.
La guarnizione frontale adotta una guarnizione a labbro scheletrata, che viene utilizzata per sigillare l'olio che fuoriesce dalla guarnizione rotante. La pressione dell'olio che perde generalmente non supera 0,3 MP. Una volta che la perdita aumenta, è facile danneggiare la guarnizione terminale e causare la fuoriuscita di olio idraulico. La porta dell'olio del guscio del giunto rotante è accoppiata alla porta dell'olio sul mandrino dell'attrezzatura.
1.2 Analisi della struttura di tenuta interna
Esistono due tipi principali di tenute rotanti per punti rotanti, tenute composite e tenute meccaniche. Le prestazioni di tenuta della guarnizione in materiale composito sono relativamente migliori e vengono utilizzate dove il cilindro idraulico ha un posizionamento intermedio. Il punto rotante sigillato con materiali compositi può rendere il punto rotante più compatto e raffinato a causa delle piccole dimensioni della guarnizione stessa. Il costo della tenuta composita stessa è molto più economico di quello della tenuta meccanica.
La tenuta rotante composita è composta da due parti, una combinazione di un anello esterno in PTFE e un O-ring in NBR. L'O-ring svolge la funzione di supportare l'anello esterno, rendendo l'intera tenuta rotante più facile da installare, scorrendo tra l'anello esterno e l'alloggiamento del giunto rotante. La produzione di tenute meccaniche è più complicata, anche i requisiti di precisione sono relativamente alti e il prezzo relativo è relativamente alto.
2. Installazione e manutenzione di punti rotanti idraulici
Quando si installa la punta rotante idraulica sul mandrino dell'attrezzatura principale, assicurarsi che la cavità del giunto rotante e il mandrino dell'attrezzatura principale abbiano una buona coassialità. È generalmente richiesto che la coassialità tra l'asse del giunto rotante e l'asse dell'attrezzatura sia controllata entro ± 1 mm / m. Una fuori concentricità farà sì che il punto rotante idraulico produca oscillazioni radiali relativamente ampie durante la rotazione ad alta velocità. La forza radiale fa sì che il giunto rotante e il mandrino scivolino periodicamente in direzione assiale. Non solo il film d'olio dinamico viene distrutto e l'usura della superficie di accoppiamento è aumentata, ma anche la faccia terminale della tenuta è usurata. Allo stesso tempo, il cuscinetto può sopportare un maggiore impatto esterno. Pertanto, una scarsa coassialità causerà gravi danni alla tenuta rotante interna e ai cuscinetti e influirà sulla durata.
L'alloggiamento del giunto rotante è fissato per impedirne la rotazione sincrona con il mandrino, in modo che possa essere impedito di ruotare in cerchio.
Non utilizzare più vincoli. La forza radiale o assiale che agisce sul guscio verrà trasmessa al cuscinetto del giunto rotante idraulico e alla tenuta rotante interna attraverso il guscio, costringendo il cuscinetto o la guarnizione a usurarsi o danneggiarsi.
Quando si collegano tubi dell'olio esterni, attenersi scrupolosamente alle specifiche di installazione dell'attrezzatura idraulica. In particolare, è necessario controllare rigorosamente la pulizia di ciascuna porta dell'olio per evitare che contaminanti esterni e bave lavorate vengano introdotte nel giunto rotante. A causa della complessa struttura interna del giunto rotante idraulico e del piccolo gioco di accoppiamento, una volta che i contaminanti esterni entrano nel giunto rotante idraulico, è facile causare danni al film d'olio, alle tenute meccaniche e agli inceppamenti dei cuscinetti e gravi perdite.
Il paraolio scheletrato del giunto rotante viene utilizzato per sigillare il mandrino rotante, in modo che l'olio che fuoriesce dalla tenuta rotante venga scaricato dal tubo dell'olio che perde al serbatoio dell'olio. La resistenza alla pressione del paraolio di solito non supera i 3 bar, quindi il tubo dell'olio che perde deve essere restituito all'olio senza problemi.
Durante l'installazione, la porta dell'olio che perde del giunto rotante non deve essere ostruita. Se è presente una valvola sul tubo dell'olio che perde, deve essere aperta prima dell'introduzione del fluido, altrimenti il paraolio verrà inevitabilmente schiacciato. Inoltre, non è possibile incorporare il tubo dell'olio che perde nel tubo di ritorno dell'olio, poiché la pressione del tubo di ritorno dell'olio normalmente supera i 3 bar. Non installare un filtro sul tubo dell'olio che perde. I giunti rotanti di solito hanno perdite, quindi non possono essere utilizzati in occasioni in cui è richiesta pressione. La perdita delle tenute meccaniche è maggiore.
Il servocomando può essere preso in considerazione quando è necessario controllare la corsa del cilindro idraulico per compensare la perdita. Quando il cilindro idraulico non è posizionato al centro, il problema sarà più semplice, a condizione che il cilindro idraulico continui a fornire il mezzo dopo che il cilindro idraulico si è spostato nella posizione limite.
I giunti rotanti sono generalmente lubrificati e raffreddati dal fluido, quindi non è possibile testare o guidare senza passare il fluido. Assicurarsi di aprire il tubo dell'olio che perde dopo la revisione del giunto rotante o dell'attrezzatura correlata. L'usura o il danneggiamento dei giunti rotanti idraulici può essere stimata misurando la perdita. La perdita dei giunti rotanti deve essere monitorata e tracciata regolarmente per monitorare le condizioni operative dei giunti rotanti.
3. Difetti comuni dei giunti rotanti idraulici
Nell'uso effettivo, i giunti rotanti idraulici presentano principalmente due tipi di guasti. Un difetto si manifesta come il danneggiamento del cuscinetto interno del giunto rotante e l'altro è la perdita esterna del giunto rotante.
Analizza le cause dei danni interni ai cuscinetti, ci sono tre punti principali:
1) L'olio idraulico ha scarsa pulizia e granulosità durante l'installazione o durante l'uso, con conseguente grave usura e rottura degli elementi volventi del cuscinetto;
2) Quando il giunto rotante è installato, i requisiti di precisione dell'installazione non sono soddisfatti, con conseguente forza irregolare sotto lo stato di carico statico del cuscinetto e un valore di vibrazione eccessivo sotto lo stato di carico dinamico, causando danni al cuscinetto;
3) Il design del giunto rotante idraulico selezionato e la qualità di produzione non soddisfano i requisiti delle condizioni di lavoro dell'attrezzatura. Le ragioni della perdita al di fuori del giunto rotante sono:
La precisione di lavorazione della superficie di accoppiamento della guarnizione di installazione è bassa, il che non può soddisfare i requisiti di precisione della guarnizione;
La scelta e l'installazione della guarnizione non sono adatte ai requisiti delle condizioni di lavoro;
La precisione di installazione del giunto rotante è scarsa, causando vibrazioni eccessive e danni alla guarnizione.
4. Conclusione
Nelle applicazioni pratiche, a causa delle complesse condizioni di lavoro delle apparecchiature principali e dell'ambiente mutevole. Quando si seleziona un'applicazione specifica, è necessario selezionare un giunto rotante adatto a un'ampia gamma di carichi in base alle condizioni di lavoro specifiche. Al fine di soddisfare i requisiti delle apparecchiature principali da bassa pressione e bassa velocità ad alta pressione e alta velocità in un'ampia gamma di condizioni di lavoro. Il giunto rotante idraulico della tenuta meccanica ad alta precisione può realizzare meglio lo scopo di piccole perdite, funzionamento affidabile e durevole.
Migliorando l'accuratezza dell'elaborazione e i requisiti tecnici delle parti e la precisione dell'installazione, la capacità del giunto rotante di adattarsi all'alta velocità e all'alta pressione può essere notevolmente migliorata e la durata può essere prolungata.
presa di prova idraulica accoppiamento di prova idraulica ACCOPPIATORE DI PROVA DI PRESSIONE Accoppiamenti Parker EMA Raccordi porta di prova Connettore di prova idraulico Kit adattatore di prova idraulica Kit di prova idraulico Test di accoppiamento punto di prova pressione accessori idraulici Assiemi di prova tubi flessibili punto di prova raccordi Raccordi manometro Raccordi di prova per controllo pressione Portatile Strumenti idraulici per prove di pressione Tubo per raccordi ad alta pressione Raccordi terminali per tubi ACCOPPIAMENTO PUNTO DI PROVA IDRAULICO Accessori idraulici Produttore di raccordi idraulici Raccordi idraulici standard Connettore di prova idraulico Raccordi a T per test idraulico Raccordi a T del punto di prova JIC Raccordi idraulici catalogo raccordi raccordi idraulici attacco manometro JIC punto di prova del fluido idraulico raccordi parker filettature di collegamento punto di prova raccordi porta di prova idraulica accoppiamento idraulico e tubo mini presse idrauliche valvole antiurto valvole di pressatura valvola flangiata punto di prova fluido idraulico connettori del fluido raccordi idraulici a sgancio rapido