Blog
How to operate hydraulic test fittings safely?
How to operate hydraulic test fittings safely?
Hydraulic test fittings are essential components in hydraulic systems, widely utilized in fields such as construction machinery, industrial equipment, aerospace, automotive manufacturing, and oil and gas.
Their primary role is to measure and monitor system pressure, ensuring stable operation and safety. However, improper use or poor maintenance can lead to system failures and potentially severe safety incidents.
Therefore, mastering the safe operation guidelines for pressure measuring joints is crucial. This paper delves into the correct operation and maintenance practices for pressure measurement joints to ensure their safety and reliability in practical applications.
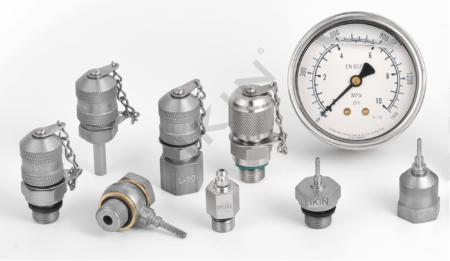
1. Basic structure and operation principle of pressure-measuring connectors
A pressure measuring fitting typically comprises a body, seals, and connecting components. Its function is to detect pressure fluctuations within a hydraulic system, delivering real-time data that allows operators to monitor and adjust the system’s performance accordingly. Hydraulic test fittings are engineered for optimal tightness and stability in high-pressure environments, effectively preventing fluid leaks and potential system failures.
2. Basic principles of safe operation
2.1 Knowledge of equipment
Before operating a pressure measuring fitting, it’s essential to thoroughly understand its structure, working principles, and operating instructions. Familiarize yourself with the equipment’s performance parameters, including maximum working pressure, temperature range, and suitable media. This knowledge ensures that the equipment operates within its design limits, preventing any operational issues.
2.2 Wear appropriate protective equipment
Always utilize suitable protective equipment, such as gloves, goggles, and protective clothing, when operating pressure-measuring fittings. This gear is crucial for preventing injuries from high-pressure fluid leaks and ensures operator safety.
2.3 Checking the status of equipment
Before operation, thoroughly inspect the condition of the pressure measuring fitting to ensure there are no signs of damage or wear. Pay special attention to the seals, which must be intact to prevent leaks. Additionally, check the connecting parts for tightness to ensure a secure and reliable connection.
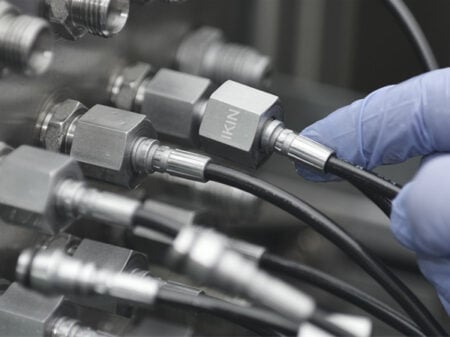
3. Safe practices for installation and dismantling
3.1 Installation of hydraulic test fittings
-Selecting an Appropriate Location: Choose a suitable spot within the hydraulic system for installation to ensure the measurement point accurately reflects the system’s operating pressure.
– Cleaning Connecting Parts: Prior to installation, thoroughly clean both the pressure measuring fitting and the system’s connecting parts to remove any impurities or contaminants that might compromise the seal.
– Using the Right Tools: Employ the correct tools for installation and avoid applying excessive force to prevent damage to the fittings or connecting components. Adhere to the equipment manufacturer’s installation instructions to ensure proper setup.
3.2 Disassembly of hydraulic test fittings
– Pressure Relief: Before removing the pressure measurement fitting, ensure that the system is fully depressurized to eliminate any residual pressure and prevent injuries from fluid discharge.
– Equipment Protection: During disassembly, carefully protect the pressure measurement fittings and connecting parts from impacts and damage. After removal, store the connectors properly to prevent contamination and damage.
4. Safety precautions in operation
Monitoring System Pressure: During operation, continuously monitor the system pressure in real-time to ensure it remains within a safe range. Avoid overpressure conditions to prevent damage to the pressure measuring fitting and the hydraulic system.
Avoiding Sudden Pressure Changes: Prevent sudden pressure changes during operation to avoid shocks to the pressure measuring fitting and the hydraulic system. Adjust the system pressure gradually to ensure a smooth transition.
Compliance with Operating Procedures: Adhere strictly to the operating procedures and avoid unauthorized actions. If any abnormal conditions arise during operation, stop immediately, identify the cause, and address it to ensure system safety.
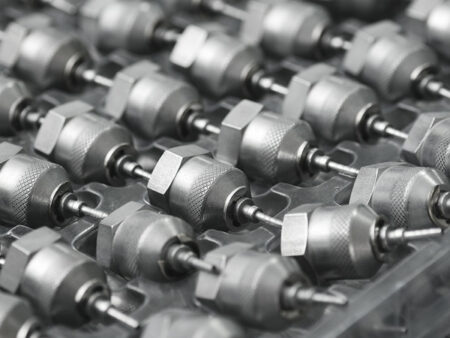
5. Safe practices for maintenance and upkeep
5.1 Regular inspection and maintenance
– Inspection of seals: Regularly inspect the seals of the pressure measuring joints, and replace them in time if they are found to be aged or damaged. Select high-performance sealing materials to improve the sealing effect and service life.
– Cleaning the equipment: Clean the pressure measurement fitting regularly to prevent dust, impurities and corrosive substances from entering the inside of the fitting. Use appropriate cleaning agents and tools to ensure that both the inside and outside of the fitting are kept clean.
5.2 Lubrication and fastening
– Lubrication: For pressure-measuring fittings that require frequent operation, lubricate regularly to reduce wear and operating resistance. Select a suitable lubricant and avoid lubricants that are harmful to the sealing material.
– TIGHTENING: Periodically check the tightness of the joints to ensure that they are securely connected. For loose joints, tighten them with appropriate tools to prevent leakage and system instability.
5.3 RAM
– Maintenance records: Detailed records of each maintenance and servicing, including inspection items, problems found and treatment measures. Through the maintenance records, the history of equipment use can be traced, potential problems can be found and dealt with in a timely manner.
– File management: Establish a file management system for the pressure measuring joints, keep the technical data, operation instructions and maintenance records of the equipment, etc., so as to facilitate the daily management and maintenance.
6. Emergency response measures
Regular Inspection and Maintenance:
- Seal Inspection: Regularly examine the seals of pressure measuring joints and promptly replace any that are aged or damaged. Use high-performance sealing materials to enhance sealing effectiveness and extend service life.
- Equipment Cleaning: Routinely clean the pressure measuring fitting to prevent dust, impurities, and corrosive substances from entering. Use appropriate cleaning agents and tools to ensure both the interior and exterior of the fitting remain clean.
Lubrication and Fastening:
- Lubrication: For pressure measuring fittings that require frequent operation, lubricate regularly to minimize wear and operational resistance. Choose a suitable lubricant and avoid those that could harm the sealing material.
- Tightening: Periodically check the tightness of the joints to ensure secure connections. Use appropriate tools to tighten any loose joints, preventing leaks and system instability.
Record and Maintenance (RAM):
- Maintenance Records: Keep detailed records of each maintenance session, including inspection items, identified issues, and corrective actions taken. These records help trace the equipment’s usage history and identify potential problems early.
- File Management: Establish a file management system for pressure measuring joints, maintaining technical data, operation instructions, and maintenance records. This system facilitates daily management and maintenance activities.
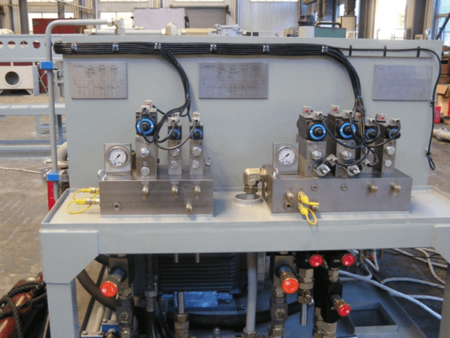
7. Case studies
Case 1: Safe Operation of hydraulic test fittings in a Chemical Plant
In a chemical plant, numerous hydraulic test fittings were utilized within the hydraulic system. An incident occurred when an operator failed to perform the necessary pressure relief operation, resulting in a high-pressure liquid spray during disassembly and causing injury.
Following an investigation, the chemical plant developed detailed operating procedures and provided comprehensive training to the operators. These measures significantly improved the operational safety of the pressure measuring joints and prevented similar incidents from occurring.
Case 2: Maintenance of pressure-measuring fittings at a manufacturing company
A manufacturing company employed high-pressure hydraulic test fittings in its hydraulic press equipment. Due to neglect in timely maintenance and repair, the seals of the pressure-measuring fittings deteriorated and became damaged, leading to system leaks.
To address the issue, the company took the following actions: replaced all deteriorated seals with high-performance sealing materials; regularly inspected and cleaned the pressure-measuring fittings to ensure optimal condition; and trained operators to enhance their maintenance and operation skills. These measures effectively resolved the leakage problem and improved both the operational efficiency and safety of the equipment.
Hydraulic test fittings are crucial components in hydraulic systems, and their safe operation and maintenance are directly linked to the stability and safety of the system. By understanding the equipment’s structure, wearing appropriate protective gear, checking the equipment’s condition, installing and removing it correctly, monitoring system pressure, avoiding sudden pressure changes, adhering to operating procedures, conducting regular inspections and maintenance, maintaining thorough records and files, and implementing emergency response measures, you can ensure the safety and reliability of pressure-testing fittings in practical applications.
Real-world case studies demonstrate that following scientific operation and maintenance protocols not only enhances the service life and performance of pressure measuring joints but also effectively prevents safety incidents. Therefore, attention to the safe operation specifications of pressure measuring joints is essential for ensuring the stable operation of hydraulic systems and the safety of operators.
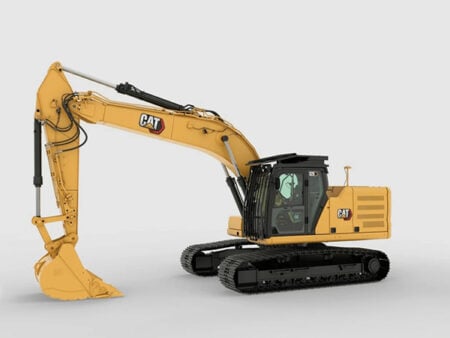
Common problems and solutions during pressure testing
Common problems and solutions during pressure testing
Pressure testing is essential for ensuring the proper operation and safety of hydraulic systems and equipment. It helps detect weaknesses, verify design pressures, and identify potential leaks within the system.
However, various issues may arise during pressure testing. If these problems are not addressed promptly and effectively, they can affect test results and even jeopardize system safety.
This article provides an in-depth analysis of common problems encountered during pressure testing and offers practical solutions. We will also discuss these issues through real-world examples. By offering detailed analysis and discussion, this article aims to provide practical guidance to ensure the stability and safety of hydraulic systems.
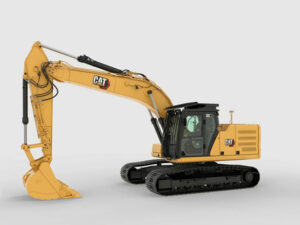
**1. Common problems during pressure testing**
**1.1 Leakage**
Leaks are among the most common issues encountered during pressure testing. They can occur at system connections, seals, or along piping. The causes of leaks are varied and may include deteriorated seals, improper installation, or defective materials.
**Solutions:**
Inspection and Replacement of Seals: Regularly inspect the condition of seals. Any seals that are deteriorated or damaged should be promptly replaced to prevent potential leakage.
Correct Installation: Ensure that all connections and piping are installed correctly, using appropriate methods and tools. Proper tightening and sealing of each component are essential to prevent leaks.
Material Selection: Choose materials that are corrosion-resistant and capable of withstanding high pressures. Selecting the right materials for the system’s working environment enhances the overall reliability of the system.
By implementing these solutions, the likelihood of leaks can be significantly reduced, ensuring the integrity and safety of the hydraulic system during pressure testing.
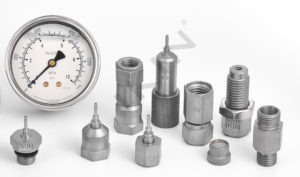
**1.2 Pressure fluctuations**
Pressure fluctuation refers to unstable pressure during testing, which can be caused by poor system design, unstable pressure sources, or equipment failure.
**Solutions:**
Optimized System Design: Ensure that the system is well-designed to prevent sudden changes in pressure. A robust design minimizes the likelihood of pressure fluctuations and significantly reduces associated problems.
Stable Pressure Source: Utilize a reliable pressure source that can provide continuous and stable pressure, ensuring the system operates normally and efficiently.
Equipment Maintenance: Conduct regular inspections and maintenance of pressure source equipment. Timely identification and resolution of potential issues are crucial to maintaining optimal working conditions and preventing pressure instability.
Implementing these solutions will help stabilize pressure during testing, ensuring the system’s reliability and accuracy.
**1.3 Inaccurate meter readings**
During pressure testing, inaccurate meter readings can compromise the accuracy of the test results. This issue may arise due to improper calibration of the gauge, incorrect mounting position, or gauge malfunction.
**Solutions:**
Periodic Calibration of Meters: Calibrate the meters at regular intervals to maintain accurate readings and ensure the reliability of the test data.
Select an Appropriate Mounting Location: Install the meter in a suitable location that minimizes vibration and interference, which can affect the accuracy of the readings.
Replacement of Malfunctioning Meters: Promptly replace any malfunctioning meters to maintain the accuracy and integrity of the test results.
By addressing these factors, the accuracy of meter readings can be ensured, thereby enhancing the reliability of the pressure test outcomes.
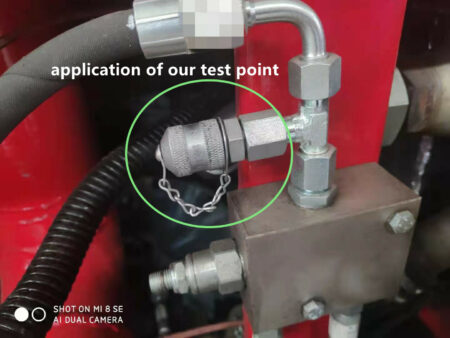
**1.4 Temperature effects**
Temperature variations can significantly impact pressure test results, particularly in extreme high or low-temperature environments. These fluctuations can cause materials to expand or contract, affecting the system’s sealing and pressure stability.
**Solutions:**
Selection of Temperature-Resistant Materials: Choose materials that are resistant to temperature changes based on the system’s working environment. This ensures that the system maintains stable performance under extreme temperature conditions.
Implement Temperature Compensation Mechanism: Introduce a temperature compensation mechanism during testing to minimize the impact of temperature fluctuations on the results. This helps ensure the accuracy and reliability of the pressure tests.
By addressing temperature-related issues, the stability and accuracy of pressure test results can be significantly improved.
**1.5 Connectivity issues**
Connection problems are a common challenge during pressure testing, often caused by mismatched fitting types, improper installation, or loose connections.
**Solutions:**
Selecting the Appropriate Fitting Type: Choose fittings that are compatible with the system design and suitable for the working environment to ensure proper matching with the rest of the system.
Correct Installation of Fittings: Follow standard methods and procedures for installing fittings to ensure a secure and reliable connection.
Regular Inspection and Tightening: Conduct periodic inspections of connection points and promptly tighten any loose parts to maintain a solid and dependable connection.
By addressing these connection issues, the reliability and effectiveness of pressure testing can be significantly enhanced.
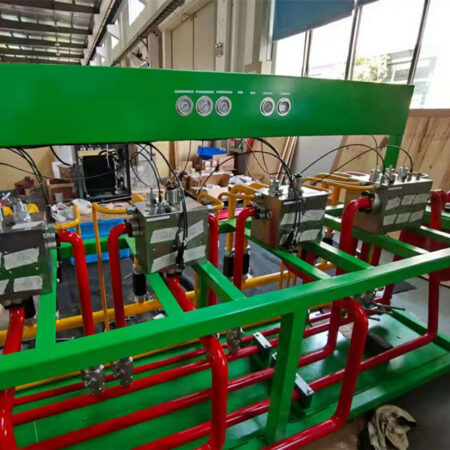
**2. Solutions for pressure testing**
**2.1 Development of a Detailed Test Plan**
Before conducting a pressure test, it is crucial to develop a comprehensive test plan that outlines the purpose, scope, methodology, steps, and expected outcomes. A detailed test plan helps clarify the objectives and ensures that the testing process is systematic and organized.
**2.2 Use of High-Quality Test Equipment**
Using high-quality test equipment is essential for obtaining accurate and reliable results. Select certified and calibrated equipment, and ensure that it is in optimal working condition before use.
**2.3 Training and Education**
Provide thorough training and education for operators to equip them with the necessary knowledge and skills for pressure testing. Training should cover the use of test equipment, execution of test procedures, and identification and resolution of common issues.
**2.4 Recording and Analysis**
During the pressure test, meticulously record all data and results, including pressure, temperature, time, and environmental conditions. Analyzing this data helps identify potential problems and implement timely corrective measures.
**2.5 Development of Contingency Plans**
Develop a comprehensive contingency plan to address any emergencies that may arise during the testing process. The plan should include procedures for handling leaks, equipment failures, and safety measures to ensure the testing process remains safe and efficient.
By implementing these strategies, the reliability and accuracy of pressure testing can be significantly enhanced, ensuring the safe and effective operation of hydraulic systems.
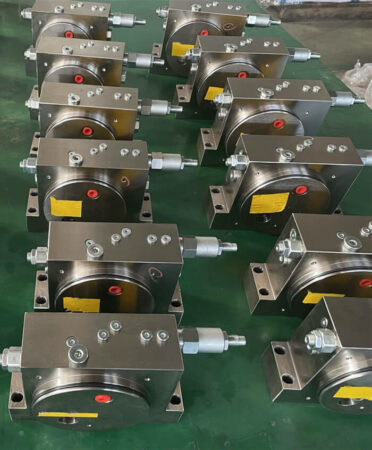
**3. Case Studies**
**Case 1: Pressure Testing in a Chemical Plant**
During the pressure testing of a new piping system at a chemical plant, multiple leaks were detected. Upon investigation, it was determined that the primary causes of the leaks were aging seals and improper installation. To address these issues, the chemical plant implemented the following measures:
– Replaced all deteriorated seals with corrosion-resistant, high-performance sealing materials to enhance durability and reliability.
– Conducted a thorough inspection and tightening of all connections to ensure that the installation complied with relevant codes and standards.
– Provided comprehensive training to operators to enhance their installation and operational skills.
By taking these steps, the chemical plant effectively resolved the leakage issues and ensured the safety and stability of the piping system.
**Case II: Pressure Testing in a Pharmaceutical Company**
During a pressure test of the hydraulic system at a pharmaceutical company, significant pressure fluctuations were detected. Analysis revealed that these fluctuations were caused by an unstable pressure source and poor system design. To address these issues, the pharmaceutical company implemented the following measures:
– Replaced the existing pressure source with more stable equipment to ensure a continuous and stable pressure supply.
– Redesigned the hydraulic system, optimizing the piping layout and connections to enhance overall system stability.
– Introduced an automated control system to monitor and regulate pressure in real-time, ensuring consistent system pressure.
By implementing these measures, the pharmaceutical company successfully resolved the issue of pressure fluctuations, significantly improving the operational efficiency and stability of the hydraulic system.
**Case IV: Pressure Testing at an Aerospace Company**
During pressure testing of an aircraft hydraulic system at an aerospace company, significant effects of temperature variations on the test results were observed. Analysis determined that these temperature changes caused material expansion and contraction, which impacted the system’s sealing and pressure stability. To address this issue, the aerospace company implemented the following measures:
– Selected temperature-resistant materials suitable for both high and low-temperature environments to ensure stable performance despite temperature fluctuations.
– Introduced a temperature compensation mechanism during the testing process to adjust system parameters in real-time, ensuring the accuracy of the test results.
– Controlled the test environment to minimize the impact of temperature variations on the testing process.
By adopting these measures, the aerospace company successfully mitigated the issues caused by temperature variations, significantly enhancing the accuracy and reliability of the pressure tests.
**Case V: Pressure Testing in a Shipping Company**
During a pressure test of a ship’s hydraulic system at a shipping company, issues were identified at multiple joints. Inspection revealed that these problems were due to mismatched joint types and improper installation. To resolve these issues, the shipping company implemented the following measures:
– Selected appropriate fittings that were compatible with the system, ensuring they matched the rest of the hydraulic components.
– Reinstalled the connectors following correct methods and procedures to guarantee a secure and reliable connection.
– Conducted thorough inspections and tightened all connections to ensure system stability and safety.
By taking these steps, the shipping company successfully addressed the connection issues, ensuring the normal operation and reliability of the ship’s hydraulic system.
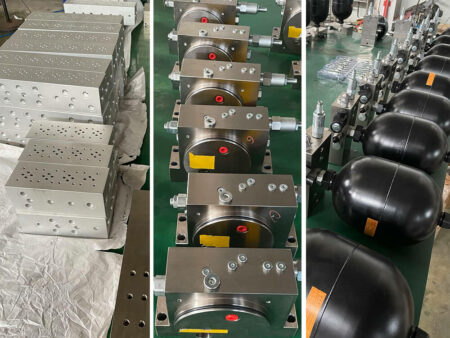
Pressure testing is a vital procedure for ensuring the proper functioning and safety of hydraulic systems and equipment. During testing, issues such as leaks, pressure fluctuations, inaccurate gauge readings, temperature effects, and connection problems can arise. These challenges can be effectively managed through the implementation of detailed test plans, the use of high-quality testing equipment, comprehensive operator training, meticulous recording and analysis of test data, and robust contingency plans. These measures ensure the accuracy and reliability of pressure tests.
Analyzing real-world cases demonstrates that scientific pressure testing methods and strategies not only address issues encountered during testing but also enhance the operational efficiency and safety of hydraulic systems. Therefore, focusing on the identification and resolution of problems during the pressure testing process is crucial for maintaining the stable operation of hydraulic systems.
Hydraulic Pressure Fittings Applied in Various Industries
Hydraulic Pressure Fittings Applied in Various Industries
Pressure measuring fittings are essential hydraulic components. They monitor pressure in hydraulic systems to ensure safety and stability. These fittings are used in many industries, including construction, industrial equipment, aerospace, automotive manufacturing, and oil & gas. Each industry has different performance requirements.
The performance requirements for pressure measuring fittings differ across industries. Specific examples demonstrate the practical importance of these fittings.
In this article, we will explore how pressure-measuring fittings are used across various industries. We’ll analyze their key roles and impacts through specific case studies.
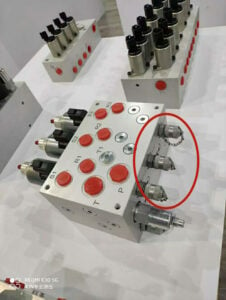
1. In the field of construction machinery
In the construction machinery industry, pressure measuring fittings are indispensable components. Equipment such as excavators, bulldozers, and loaders must endure harsh environments for extended periods, demanding highly reliable hydraulic systems.
Pressure measuring fittings play a critical role by continuously monitoring hydraulic system pressure in real time. This real-time monitoring ensures that the equipment operates within the optimal pressure range, thereby enhancing reliability, preventing system failures, and maintaining peak performance and safety.
Excavators, bulldozers, loaders, and similar equipment often operate in harsh environments for prolonged periods. This demanding usage necessitates exceptional reliability in their hydraulic systems. To achieve this, pressure measuring fittings are employed to monitor the hydraulic system’s pressure in real time. These fittings ensure that the equipment operates within the optimal pressure range, thereby preventing potential system failures and maintaining peak performance and safety standards.
**Case Study: Excavator Application**
A leading construction machinery company incorporates high-performance pressure measuring fittings in the hydraulic systems of its excavators. Given that excavators are required to function in high-intensity work environments, the pressure resistance and durability of these fittings are crucial.
These pressure measuring fittings are crafted from the latest high-strength alloy materials and utilize advanced sealing technology. This design enables them to perform reliably for extended periods under high-pressure and high-temperature conditions, effectively preventing leaks and system failures.
Through regular maintenance and servicing, the company’s excavators have significantly enhanced their operational efficiency and safety. The robust construction of these fittings ensures that the hydraulic systems remain reliable, thereby optimizing performance and reducing downtime. This meticulous approach to equipment maintenance has contributed to the company’s reputation for producing durable and efficient machinery capable of withstanding the rigors of demanding construction environments.
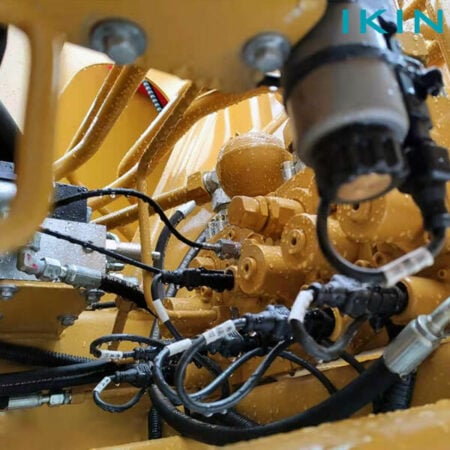
2. **Industrial Equipment Sector**
Industrial equipment such as hydraulic presses, die casting machines, and injection molding machines heavily rely on pressure measuring fittings. These fittings ensure the systems operate smoothly under high pressure and high temperature conditions. They provide accurate pressure data, enabling operators to adjust system parameters in a timely manner. This real-time data optimizes equipment performance and ensures an efficient, stable production process.
**Case Study: Hydraulic Press Application in a Manufacturing Company**
A manufacturing company has implemented new high-pressure gauge fittings in its hydraulic press equipment. Precise pressure control is essential for hydraulic presses during production, making the accuracy and stability of these fittings crucial.
By utilizing high-performance pressure measuring fittings, the company has notably enhanced the quality of its hydraulic products. This improvement has led to a significant reduction in scrap rates and an increase in production efficiency. The reliable performance of these fittings ensures that the hydraulic presses maintain consistent pressure control, thereby optimizing the overall manufacturing process and ensuring high-quality output.
3. **Automobile Manufacturing Sector**
In the automotive manufacturing sector, hydraulic systems play a crucial role in braking, steering, and suspension systems. Pressure measuring fittings are essential for real-time pressure monitoring in these systems, ensuring the vehicle’s safety performance under various operating conditions.
**Case Study: Braking System Application for an Automobile Manufacturer**
A renowned automobile manufacturer has integrated intelligent pressure measurement fittings into the braking system of its latest models. These advanced fittings combine a pressure sensor with data transmission capabilities, allowing real-time pressure data to be sent to the vehicle’s electronic control system. This continuous data stream enables the system to dynamically adjust brake pressure, significantly enhancing braking performance and vehicle safety.
The manufacturer has also conducted extensive testing and validation to ensure these pressure-measuring fittings maintain optimal performance across different climatic conditions and driving environments. This rigorous testing ensures that the fittings provide consistent, reliable data, contributing to a safer and more dependable driving experience for consumers. By incorporating these intelligent fittings, the automaker has improved the overall safety and reliability of its vehicles, reinforcing its commitment to quality and innovation in automotive design.
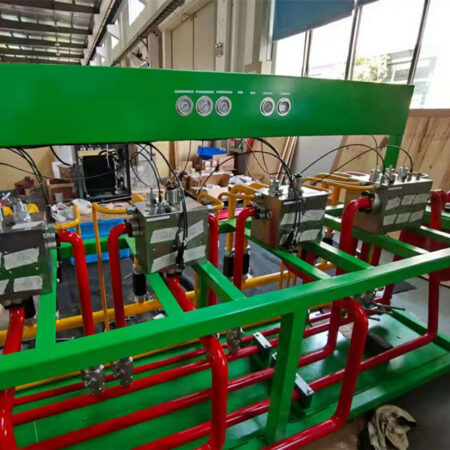
4. **Oil and Gas Sector**
In the oil and gas industry, hydraulic systems must function in complex environments with significant pressure fluctuations and exposure to corrosive media. Pressure measuring fittings are critical in these systems for monitoring the pressure of pipelines and equipment, preventing safety incidents such as leaks and explosions.
**Case Study: High-Pressure Pipeline Application in an Oilfield Project**
An oilfield project implemented high-pressure gauge fittings within its pipeline system. These fittings, constructed from high-strength alloys and featuring multi-layer seals, are engineered to withstand high-pressure and highly corrosive environments over extended periods. Regular inspections and maintenance have enabled the project team to avert numerous potential leakage incidents, ensuring safe production and environmental compliance.
Additionally, these pressure measuring fittings are equipped with remote monitoring technology, allowing operators to observe real-time pressure changes in the pipeline from a central control room. This capability ensures that any abnormalities are quickly addressed, significantly enhancing production efficiency and safety management in the oilfield. The integration of these advanced fittings not only ensures the structural integrity of the pipeline system but also supports the overall safety and efficiency of the oilfield operations.
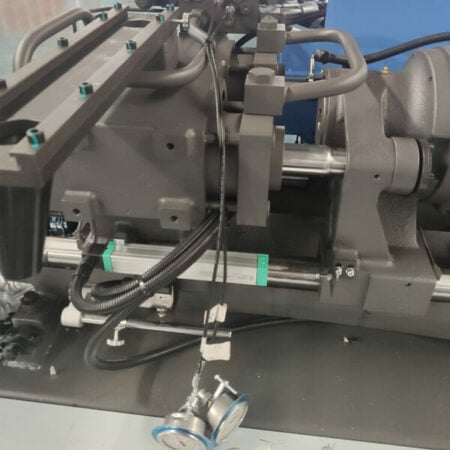
5. **Building Construction Sector**
In the building construction sector, large mechanical equipment such as tower cranes and concrete pump trucks rely on stable hydraulic systems for optimal performance. Pressure measuring fittings are crucial in these hydraulic systems to ensure stability and safety during construction activities5.
**Case Study: Tower Crane Application for a Construction Company**
A construction company has integrated high-precision pressure measurement fittings into the hydraulic systems of its tower cranes. During construction, tower cranes frequently lift heavy loads, demanding extremely stringent pressure requirements for their hydraulic systems. By employing high-performance pressure measuring fittings, the company has significantly enhanced construction efficiency and safety in large-scale projects.
These advanced pressure measuring fittings feature the latest self-locking design, ensuring that the fittings remain secure under high pressure and vibration. This innovation greatly improves the reliability and operational safety of construction equipment, enabling the tower cranes to function seamlessly in demanding environments. Consequently, the construction company has achieved higher productivity and reduced risks, reinforcing the importance of utilizing top-tier pressure measuring fittings in critical construction machinery.
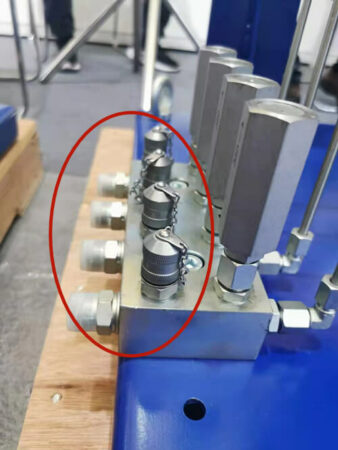
6. **Agricultural Machinery Sector**
In the agricultural machinery sector, equipment such as tractors, harvesters, and planters rely heavily on hydraulic systems. Pressure measuring fittings are essential for monitoring and controlling these hydraulic systems, ensuring the machines’ reliability and efficiency in various farming operations.
**Case Study: Harvester Application for an Agricultural Machinery Company**
An agricultural machinery company has implemented a new type of pressure measuring connector in the hydraulic system of its latest harvester model. These advanced fittings allow operators to monitor the hydraulic system’s status in real time, enabling timely adjustments and maintenance. As a result, the harvester performs reliably in field operations, reducing mechanical failures and enhancing harvesting efficiency.
These pressure measuring fittings feature an anti-fouling design that effectively prevents soil and impurities from entering the system. This design keeps the hydraulic system clean and functioning properly, ultimately improving the efficiency and service life of the agricultural machinery.
By adopting these innovative fittings, the company has ensured that its harvesters deliver optimal performance, contributing to more productive and efficient farming operations.
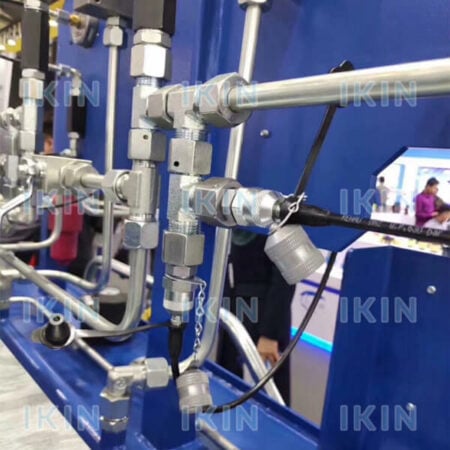
7. **Mining Sector**
The mining industry is highly demanding, and hydraulic systems are crucial for the performance of mining equipment. Pressure measuring fittings are essential for monitoring the hydraulic systems in this sector, ensuring stable operation under high loads, high pressures, and harsh environmental conditions.
**Case Study: Hydraulic Drilling Rig Application for a Mining Company**
A mining company has integrated high-performance pressure measuring couplings into the hydraulic systems of its drilling rigs. These couplings are made with special wear-resistant materials and a multi-layer sealing structure, allowing them to operate reliably for extended periods under high-pressure and high-vibration conditions.
Through regular maintenance and real-time monitoring, the company’s hydraulic drilling rigs perform exceptionally well in deep well drilling and ore extraction. This significantly boosts both efficiency and safety. The use of these advanced pressure measuring couplings not only extends the lifespan of the equipment but also reduces downtime caused by equipment failures, thereby improving overall productivity at the mine. By leveraging these robust fittings, the mining company ensures that its drilling operations are more efficient, reliable, and productive.
The case studies above clearly illustrate the application of pressure measuring fittings across various industrial fields, highlighting their critical role in ensuring the stable operation and safety of hydraulic systems. These fittings help enterprises improve productivity, reduce maintenance costs, and enhance safety.

As technology continues to advance, the performance and functionality of pressure measuring fittings are also improving. This progress will lead to their application and promotion in even more fields in the future, making significant contributions to industrial development and technological progress.
By integrating these advanced fittings, industries can look forward to more efficient, reliable, and safe hydraulic systems, driving further innovation and growth.
Pressure Measuring Fittings in Hydraulic Systems: Types, Applications, and Best Practices
Pressure Measuring Fittings in Hydraulic Systems: Types, Applications, and Best Practices
Hydraulic systems are essential in modern industry, playing a crucial role in fields such as construction machinery, industrial equipment, aerospace, and automotive manufacturing.
At the heart of these systems lies the pressure measuring fitting, which is critical for measuring and monitoring system pressure to ensure stability and safety.
In this comprehensive guide, we will explore the various types of pressure measuring fittings, their application scenarios, selection criteria, installation and maintenance procedures, and real-world case studies demonstrating their importance in hydraulic systems.
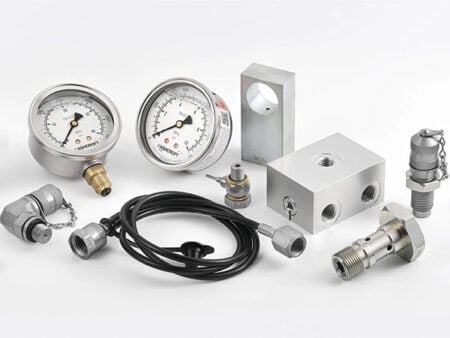
Pressure measuring fittings come in various designs tailored for specific applications, each with unique features:
1. Quick couplings
·Characteristics: Designed for rapid connection and disconnection.
·Applications: Used in hydraulic systems requiring frequent assembly and disassembly, enhancing efficiency through simple insertion and removal.
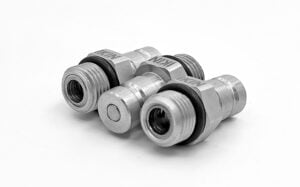
2. Threaded joints
·Characteristics: Secured by threaded connections, suitable for high-pressure environments.
·Applications: Common in systems needing robust connections that can withstand high pressure and vibration.
3. Push-in fittings
·Characteristics: Connect via a simple push-in operation.
·Applications: Ideal for low and medium pressure systems, though caution is needed in high-pressure environments.
4. Flanged joints
·Characteristics: Provide high-strength connections.
·Applications: Used in heavy machinery and high-pressure pipelines due to their strong connections and excellent seismic.
5. Welded joints
·Characteristics: Connected by welding, suitable for high-pressure and high-temperature conditions.
·Applications: Preferred in environments demanding high connection strength, despite more complex installation and maintenance.
When selecting a pressure measurement fitting, a number of factors need to be thoroughly evaluated to ensure optimum performance and long-lasting reliability in a particular application. The main factors to consider include the following:
1. Pressure range
According to the working pressure of the hydraulic system, select the coupling that can withstand the corresponding pressure. Over-pressurization can lead to damage to the couplings and even safety accidents.
When choosing, you need to carefully check the maximum working pressure of the hydraulic system and the rated pressure of the pressure measurement joints to ensure that the joints can withstand the working pressure of the system.
2. Temperature range
Hydraulic systems may operate in high or low temperature environments, requiring the selection of fittings with good temperature resistance.
Pressure gauge fittings made of different materials have different performance in different temperature ranges, and you need to choose the right fittings according to the operating temperature of the hydraulic system.
3. Media type
According to the medium used in the hydraulic system (such as oil, water, etc.) to select the appropriate joint material to prevent corrosion and media leakage.
Different media have different requirements for pressure measurement joint materials, such as oil-based hydraulic media suitable for the use of metal joints, while water-based hydraulic media may require the use of corrosion-resistant materials.
4. Connectivity
According to the design and installation requirements of the system to choose the appropriate connection, such as quick couplings, threaded fittings or push-in fittings. The selection needs to take into account the connection method and operating habits of the hydraulic system to ensure that the fitting is easy to install and use.
In order to ensure that the gauge fitting will operate consistently and efficiently in the hydraulic system for a long period of time, proper installation methods and a systematic maintenance program are essential. Below are some detailed recommendations:
1. Installation steps
– Ensure that the hydraulic system is fully pressurized before installation.
– Select the appropriate installation tool according to the type of fitting.
– Ensure that fittings are clean and free of foreign matter where they connect to the system.
– Install the fitting correctly according to the product instructions to ensure a good seal.
– Pressure test after installation to ensure that the joints are leak-free.
2. Maintenance methods
– Regularly check the sealing of the joints and replace the seals when leaks are detected.
– Clean fittings regularly to prevent dust and contaminants from entering the system.
– Regularly lubricate frequently used joints to ensure smooth operation.
– When used under high pressure or in harsh environments, periodically check the fittings for wear and replace damaged fittings in a timely manner.

In the hydraulic system, the pressure measuring fitting is not only widely used, but also plays a vital role. Through the following case studies of several practical applications, we can have a clearer understanding of the key role and significant results of the pressure measurement joints in various industries.
#Construction machinery
A major construction machinery company has introduced a new type of pressure measurement joint in its excavator hydraulic system. Made with high-precision sensors and durable materials, the connector provides excellent measurement accuracy and durability.
By using this pressure fitting, the company monitors the hydraulic system pressure in real time to ensure that the equipment operates within the optimal pressure range, improving efficiency and safety.
In addition, the corrosion and pressure resistance of the couplings significantly reduces maintenance costs, extends service life, and improves overall productivity.
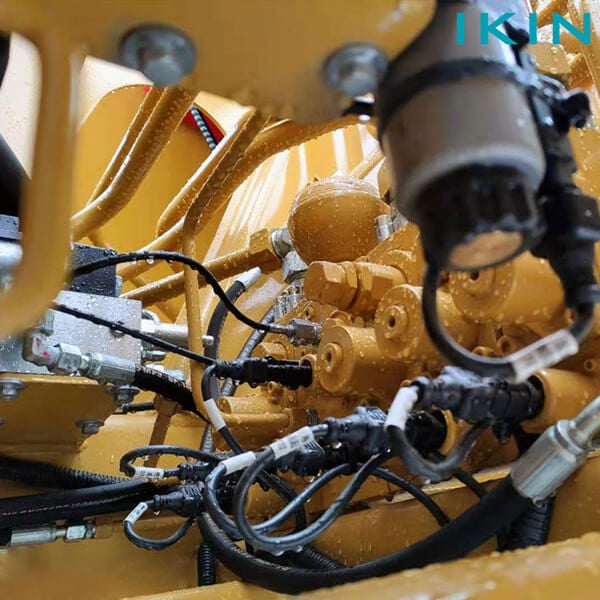
#Oil and gas
In the oil and gas industry, a large oilfield project has adopted a high-pressure and corrosion-resistant pressure measuring fitting to monitor the pressure of high-pressure pipelines. The application of this pressure fitting effectively prevents safety incidents such as pipeline leaks and explosions, and improves the safety and productivity of the project.
Installed at key pipeline nodes, these couplings transmit real-time pressure data to the monitoring center, helping operators adjust system parameters in a timely manner to prevent potential hazards.
#Industrial equipment
An industrial equipment manufacturing company has installed a variety of pressure measurement fittings in its hydraulic presses to monitor the pressure of the equipment’s hydraulic system.
Through accurate pressure monitoring and data analysis, the company identified and resolved potential problems in the hydraulic system and made timely adjustments, significantly improving the equipment’s operational stability and service life.
The real-time data provided by the pressure measurement couplings supports predictive maintenance, reduces equipment failure rates and downtime, and improves overall productivity.
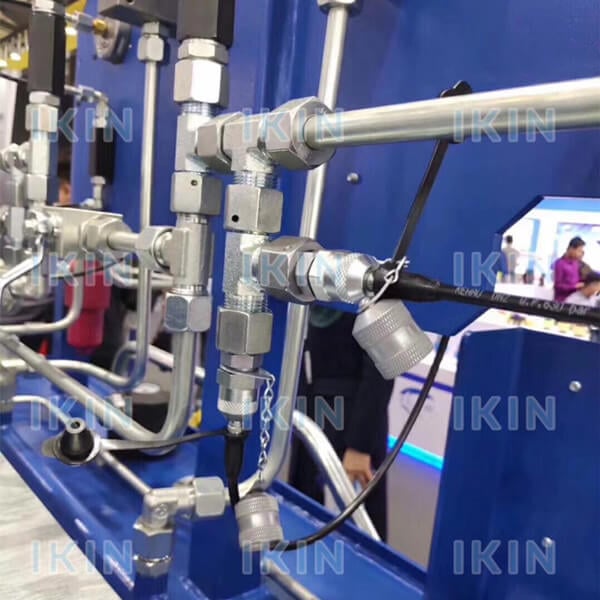
Pressure gauge fittings play a vital role in hydraulic systems, and their proper selection, installation and maintenance are the keys to ensuring the safe and stable operation of hydraulic systems. By understanding the different types of pressure measuring fittings and their application scenarios, and mastering the selection and maintenance methods, the operating efficiency and safety of the hydraulic system can be effectively enhanced.
We hope this article can help you better understand the basics and practical application scenarios of pressure measuring fittings, as well as grasp the key methods of selection and maintenance. We hope this information will be helpful to hydraulic system engineers and technicians in their work to enhance the performance and reliability of hydraulic systems. If you have any questions or need further guidance, please feel free to contact a professional.
¿Cuál es la diferencia de los acoplamientos de prueba hidráulicos en el mercado?
3 principales fabricantes en China
proveedor de accesorios de prueba hidráulica
Aprobado por SGS
¿Cuál es la estructura del punto de prueba de presión en el mercado?
Aunque el punto de prueba de presión parece pequeño e innecesario, el sistema de prueba hidráulico será mucho más conveniente con él.
1. función del punto de prueba de presión
El punto de prueba de presión se utiliza principalmente para medir la presión del sistema de fluidos, y hay una válvula autosellante en el interior.
Cuando se usa solo, debido a la acción del resorte, se puede detener la fuga del medio del sistema.
La válvula autosellante se puede abrir después de conectarse a la manguera de medición con un dedal o sensor de presión, y los parámetros de presión del sistema se pueden mostrar mediante el manómetro o el probador, que se utiliza para la detección de presión del sistema, la depuración del sistema y el diagnóstico de fallas de sistema de fluido de alta o baja presión.
Cuando se colocan en una posición especial, los adaptadores de punto de prueba también se pueden utilizar para el muestreo del medio del sistema hidráulico, el alivio de presión del sistema y el escape del sistema.
2. Clasificación de los puntos de prueba de presión en el mercado
Debido a que el conector del punto de prueba de presión está especialmente diseñado para la medición de presión y el muestreo de fluidos de caudal alto / bajo, el diseño ha considerado completamente su rango de presión.
Y de acuerdo con los diferentes ámbitos de uso, se han diseñado puntos de prueba de diferentes tipos y fortalezas, y estos conectores también juegan un papel insustituible en el trabajo.
Según la estructura interna diferente, la estructura del punto de prueba de presión se puede dividir en sello de bola, sello de pistón y sello de cono.
2.1 Estructura del sello de bola
El acoplamiento de prueba de presión de sello de bola se compone principalmente de una bola de acero y un resorte.
El empuje es generado por la precompresión del resorte, de modo que la bola de acero se presiona contra la superficie de contacto del cuerpo de la válvula para lograr el sellado.
Características de la estructura del sello de bola: una estructura simple, un sello mecánico, no es fácil de envejecer y tiene buena estabilidad.
Otra característica: se requiere que la precisión de mecanizado de la superficie de contacto del cuerpo de la válvula sea alta, la bola de acero y el cuerpo de la válvula estén en contacto en línea y el efecto de sellado sea promedio.
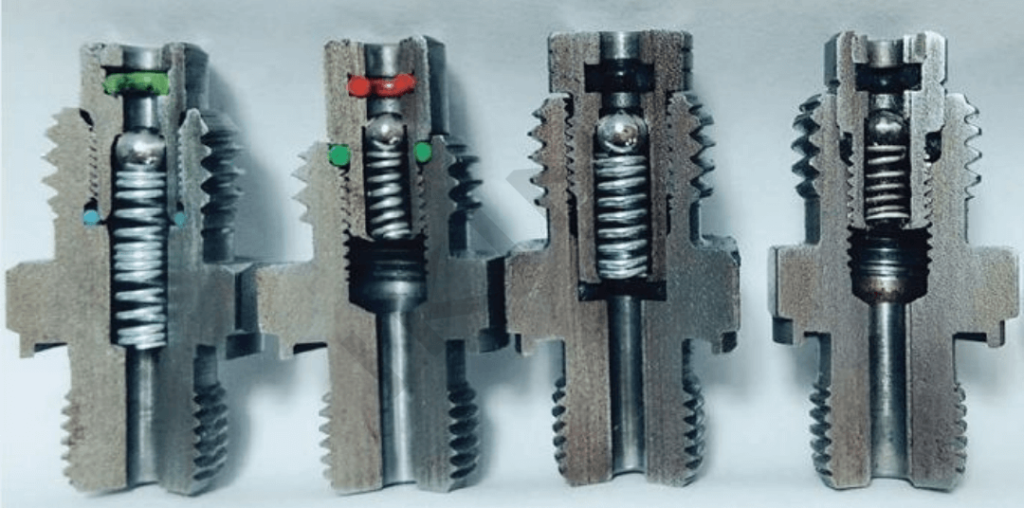
Estructura interna del punto de prueba de presión con sello de bola
2.2 Estructura del sello del pistón
El adaptador del punto de prueba de presión del sello del pistón se compone principalmente de un pistón, una junta tórica y un resorte. El anillo de sellado está en la ranura del pistón.
Adhiera al cono de sellado (sello radial) o superficie plana (sello axial) a través del empuje de precompresión del resorte.
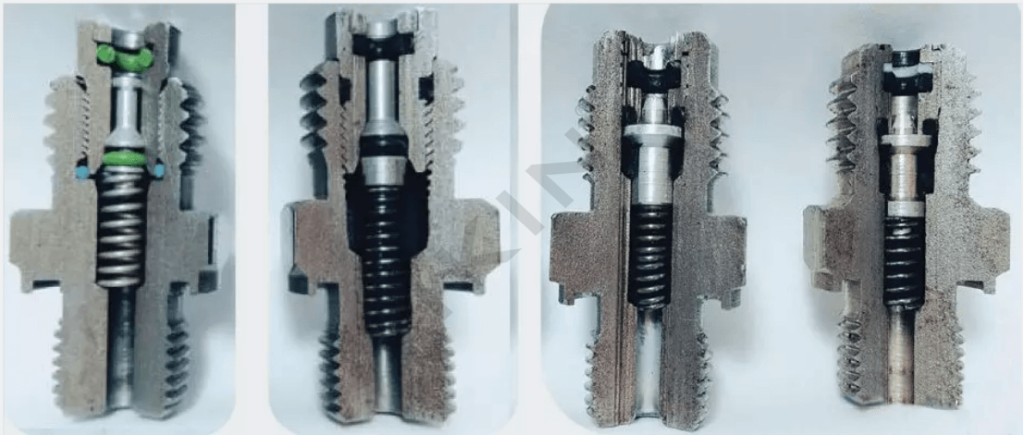
2.3 Estructura de sellado de cono
El acoplamiento de prueba de presión del sello cónico está compuesto por un núcleo de válvula cónico, un sello cónico y un resorte.
El sello cónico y el núcleo cónico de la válvula están firmemente unidos a la superficie de acoplamiento cónica del cuerpo de la válvula bajo el empuje de precompresión del resorte.
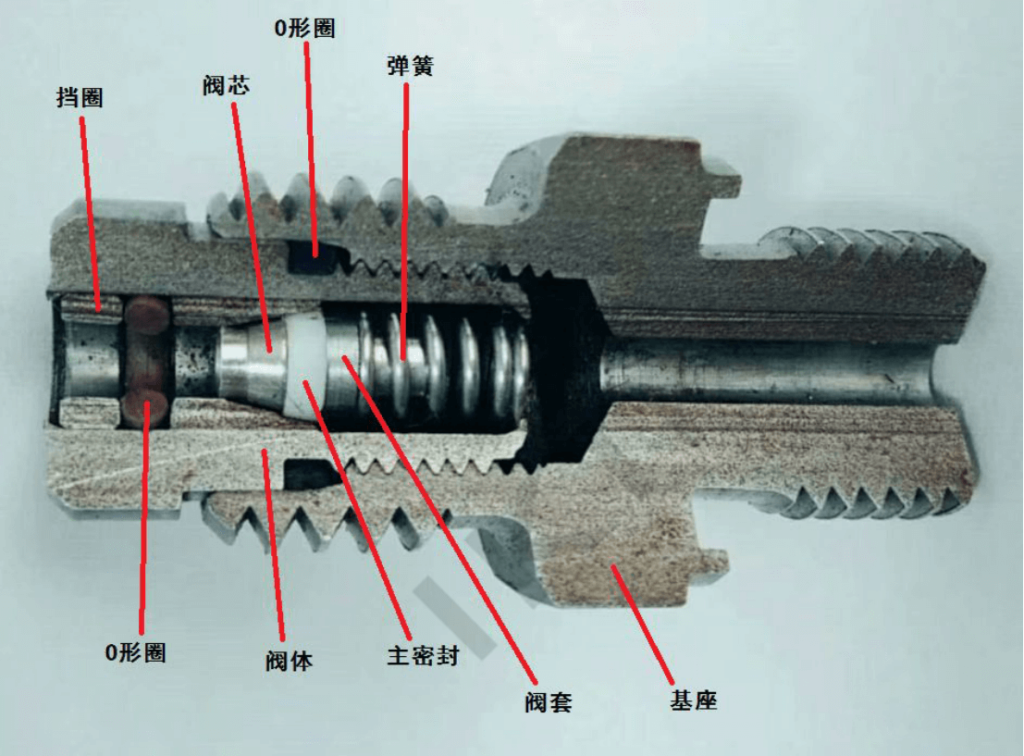
Estructura interna de la prueba de presión sellada con cono
Características del sello cónico: el núcleo de la válvula cónica y el sello cónico funcionan juntos, el sellado es de contacto superficial, el efecto de sellado es mejor y el gas y el líquido son universales;
El resorte está integrado en el cuerpo de la válvula y no es fácil de aflojar; pero la precisión de procesamiento del cuerpo de la válvula y el carrete es relativamente alta.
Como equipo de uso común en la industria, los puntos de prueba de presión de fluido son conocidos por su amplio rango práctico y conexión y muestreo convenientes. Especialmente cuando el fluido se usa a alta presión y caudal, tiene muchas ventajas y muchas comodidades.
Entonces, cuales son sus ventajas:
Ventaja 1: la operación se puede completar manualmente a alta presión
Cuando el fluido está a alta presión, si la operación es descuidada, la presión más alta puede hacer que el líquido se escape fácilmente, provocando accidentes de proceso irreversibles e incluso potencialmente mortales.
Sin embargo, el conector de la manguera de prueba de presión tiene esto en cuenta por completo, de modo que el conector se puede desconectar y cerrar simplemente usando ambas manos a alta presión.
Ventaja 2: estructura pequeña
Debido a que las ubicaciones de muestreo y prueba de presión a menudo no son fijas, el trabajo debe realizarse de acuerdo con condiciones y requisitos específicos.
Por lo tanto, la forma compacta brinda una gran comodidad en la ingeniería de transporte y operación.
Luego está la capacidad de conectarse fácilmente con el medidor.
Debido a su propósito único, la conexión con el instrumento se considera completamente en el diseño, por lo que la operación es fácil y la conexión es firme.
3. Resumen
Los adaptadores de punto de prueba son un componente muy pequeño en el sistema hidráulico, pero juegan un papel importante en la depuración, prueba y diagnóstico del sistema hidráulico.
A través del manómetro o sensor, se pueden completar varias pruebas de presión sin desmontaje y montaje y sin fugas.
El ajuste razonable de los accesorios de los puntos de prueba de presión en el sistema hidráulico aporta mucha comodidad a la depuración, prueba y diagnóstico.
Para garantizar un buen efecto de aplicación, es muy importante elegir un producto fiable y de alta calidad.
La evaluación actual del punto de prueba de presión es muy buena y el diseño del producto es excelente.
Al tiempo que garantiza una gran salida de flujo, también puede garantizar estrictos estándares de detección de calidad, de modo que los productos puedan tener un mejor valor de uso.
A juzgar por la situación actual, los acoplamientos de prueba de presión también se aplican principalmente de manera flexible a varios sistemas de fluidos.
Sin embargo, el cableado interno de los diferentes sistemas de fluidos y el tamaño de los conectores son diferentes, por lo que debe realizar el control de flujo con anticipación antes de comprar el punto de prueba de presión correspondiente.
Si el tamaño no coincide, también es un problema.
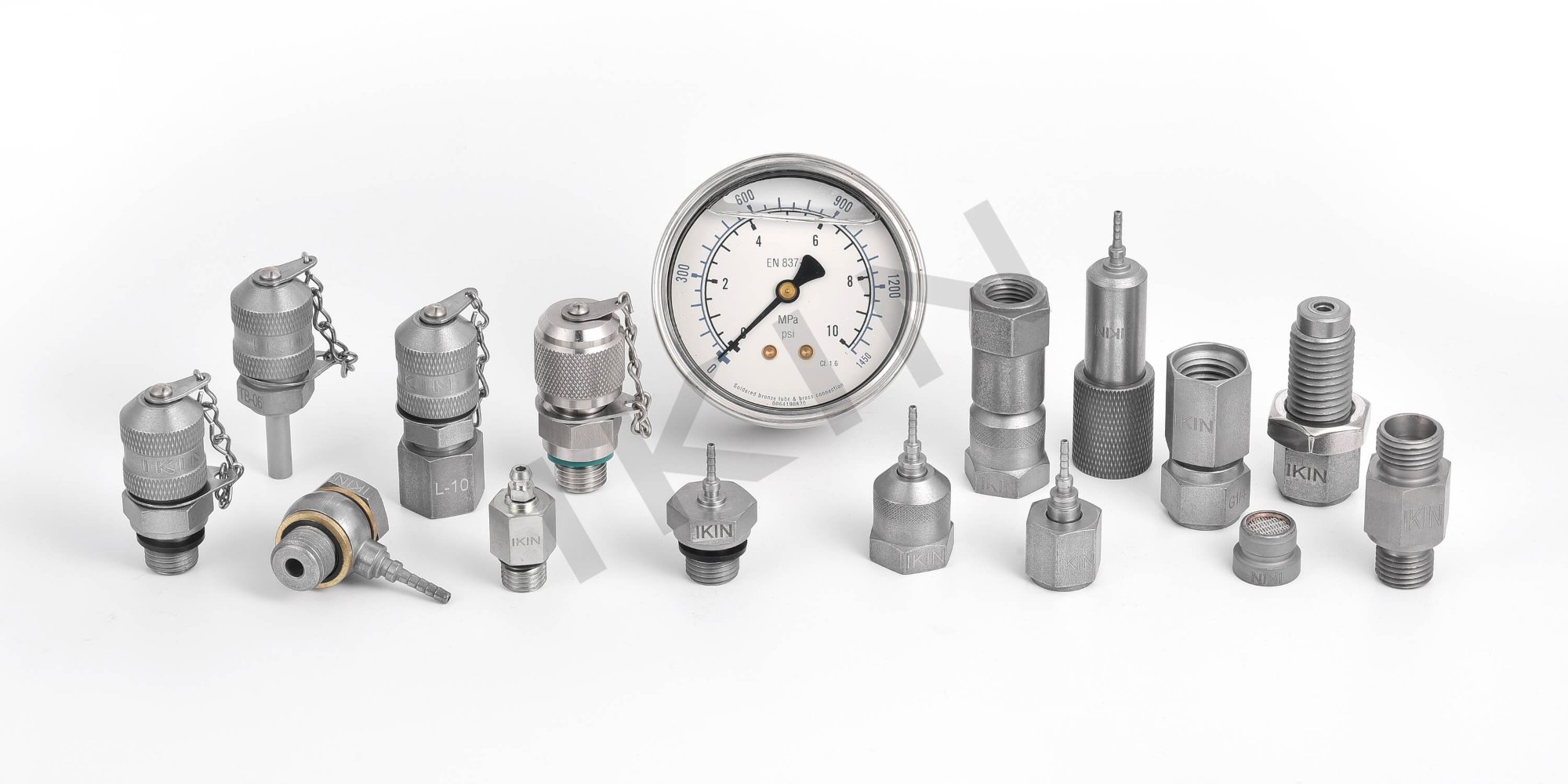
Fluido Ikin
—— Los 3 principales fabricantes en China, se especializan en puntos de prueba hidráulicos
Beneficios que puede encontrar En Ikin
precio de fábrica y moq bajo
calidad confiable, proveedor de Eaton, Hawee, etc.
Inspección de fugas 100% Antes de terminar
3 años de garantía
10 días hábiles para envíos a granel
coincidir con otros accesorios como minimess, stauff, etc.
Estructura de diseño de sello de cono, estable y de larga duración.
Obtenga su muestra gratis
en 2 días
* Respetamos su confidencialidad y toda la información está protegida.
Ikin Fluid asistió a la Bauma China 2020
Mira hacia atrás el 2020 Bauma China, Shanghai
El 27 de noviembre finalizó con éxito el Bauma China Shanghai 2020 de 4 días.
A pesar del impacto de la pandemia de covid, así como de cuatro días consecutivos de lluvia, el entusiasmo de la industria de maquinaria de construcción aún no se puede detener.
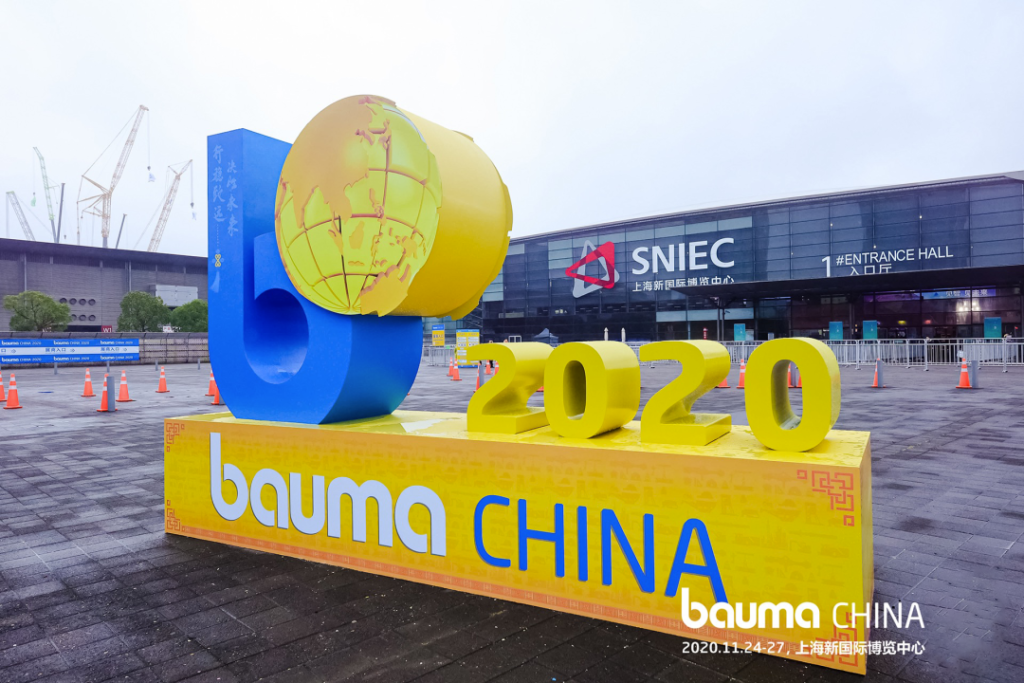
Las principales empresas de maquinaria de construcción mostraron sus habilidades y la creatividad del evento dominó a los asistentes.
Los expositores mostraron una sorpresa más grata, con muchos puntos brillantes.
¡El "Online Bauma Show" de Sany se convierte en una nueva IP 23,5 mil millones de pedidos firmados!
El debut del nuevo producto fue testigo de la fuerza del "Trinity Steel Corps".
- Nuevo camión bomba de la serie C10 con regulaciones completas y la pluma más larga
La nueva excavadora grande de cien toneladas SY1250H
46 modelos de los últimos equipos de Sany desde 25 toneladas hasta 800 toneladas de grúas
Apisonadora no tripulada sin cabina
La primera extendedora híbrida enchufable del mundo
Las primeras excavadoras eléctricas fabricadas en serie del mundo y otras docenas de los productos más vanguardistas, todo en pleno ataque, ¡asombrando a la audiencia!
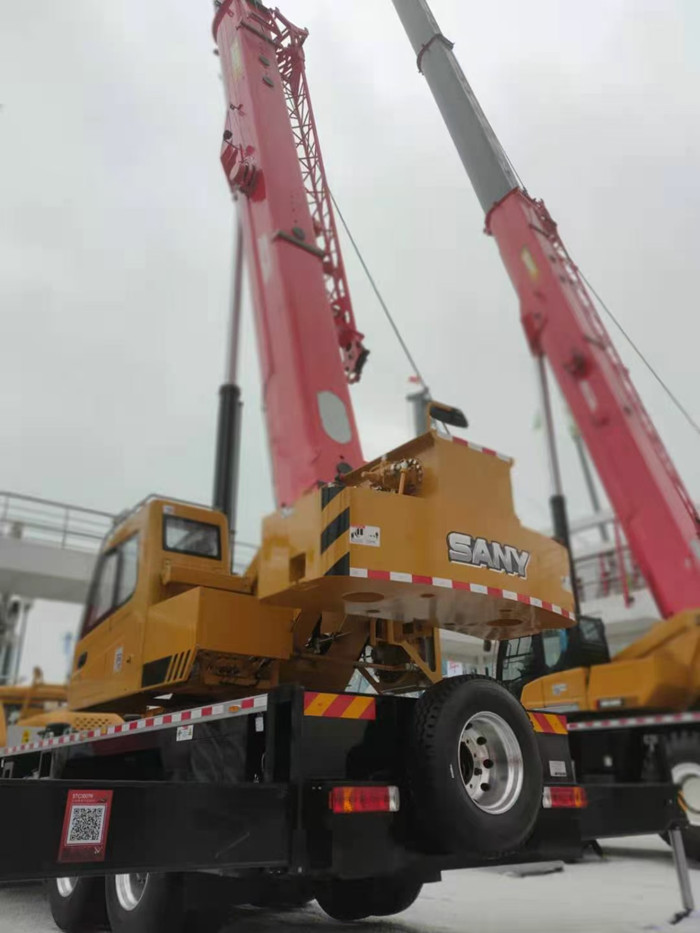
Y la imagen de abajo muestra el acoplamiento de prueba de IKIN utilizado en el sistema hidráulico de la grúa Sany en la Exposición de Bauma.
Lo siguiente es el rodaje en vivo en el stand de Sany. Es nuestro IKIN acoplamiento de prueba hidráulica usó en la grúa Sany.
Wmi IKIN LÍQUIDO son serios en el diseño y la fabricación hidráulico prueba puntos.
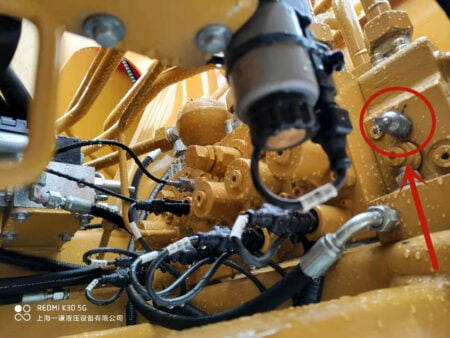
XCMG "Steel Corps" convergencia llena de "sabiduría china"
XCMG Group lanzó el sistema de información de servicio de repuestos digital global (XCMG-Global Service System, denominado X-GSS) ”.
Promueva la transformación y actualización digital, inteligente y no tripulada.
Nuevamente, el punto de prueba de control de presión de IKIN FLUID se utiliza en el Stand de XCMG.
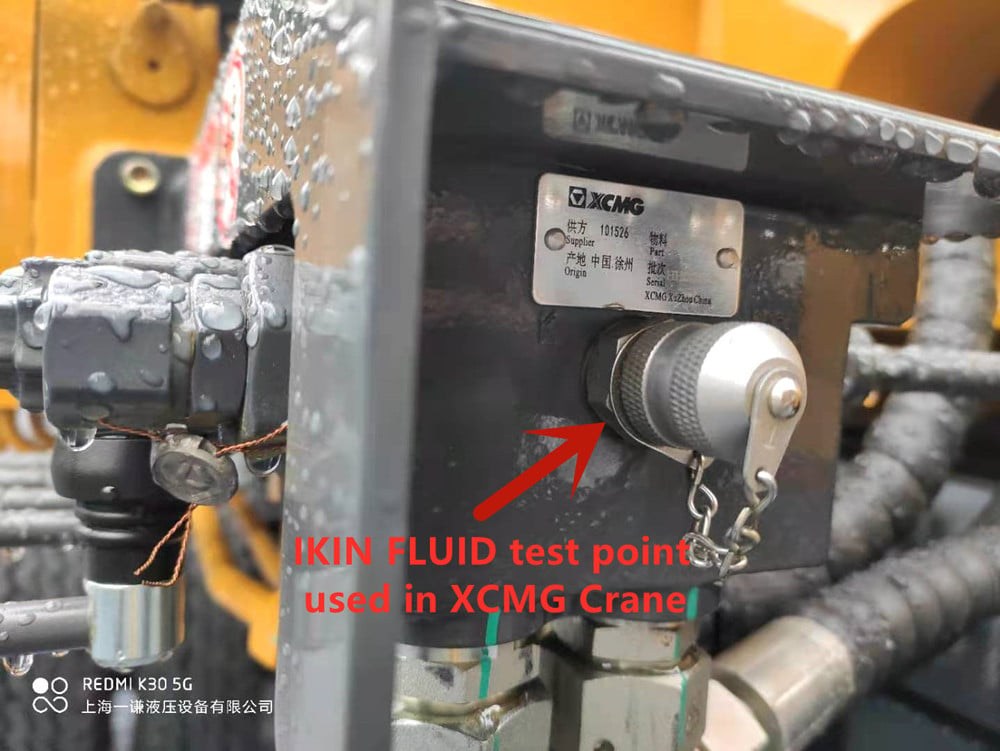
Zoomlion firmó más de 9 mil millones de RMB el primer día, el nuevo producto más visto en el mundo.
- La plataforma de trabajo aéreo de brazo recto autopropulsada más alta del mundo de Zoomlion ZT68J
- Zoomlion exhibió muchos productos de "tecnología negra"
- Los nuevos productos de alta tecnología de Zoomlion, todos demuestran fuertes capacidades de I + D e innovación.
La siguiente imagen muestra la aplicación de los puntos de prueba de presión IKIN, tomada en el stand de Zoomlion:
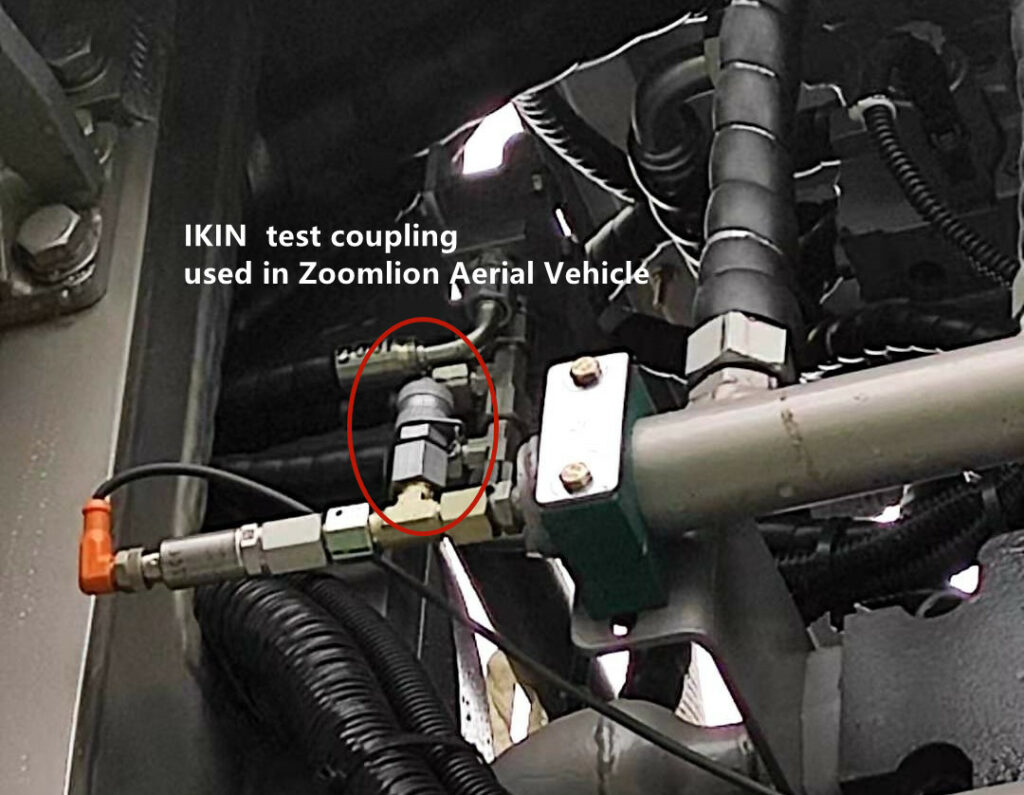
Además, a continuación se muestra el acoplamiento de prueba de presión utilizado en muchas otras exhibiciones de los stands de los clientes.
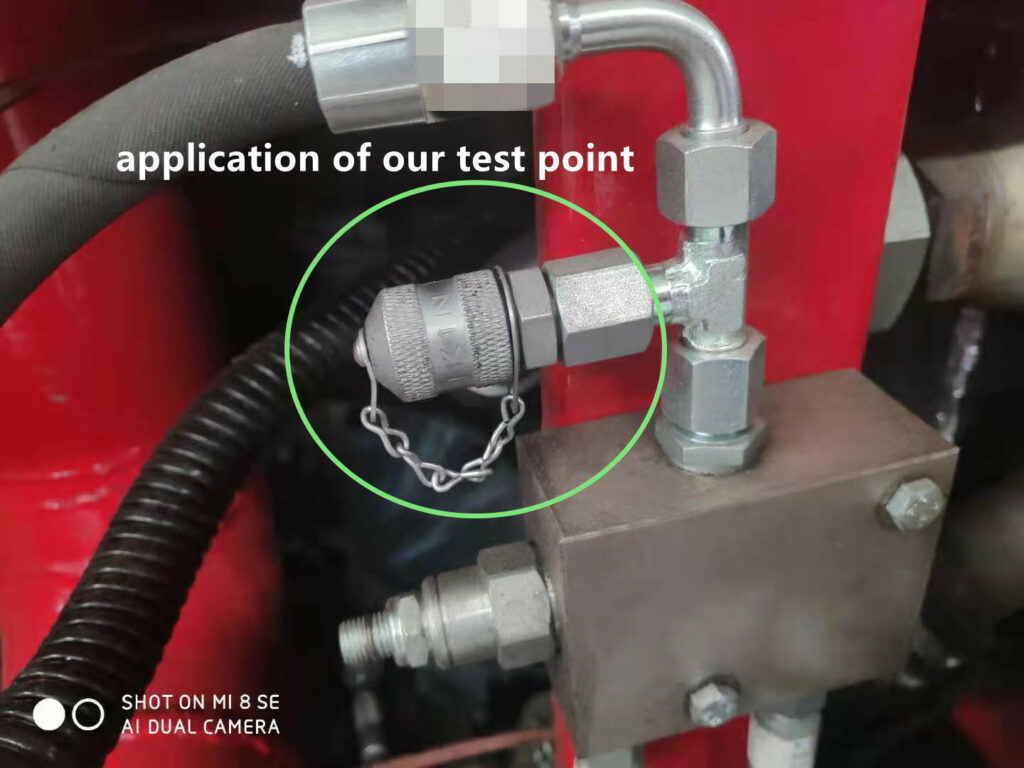
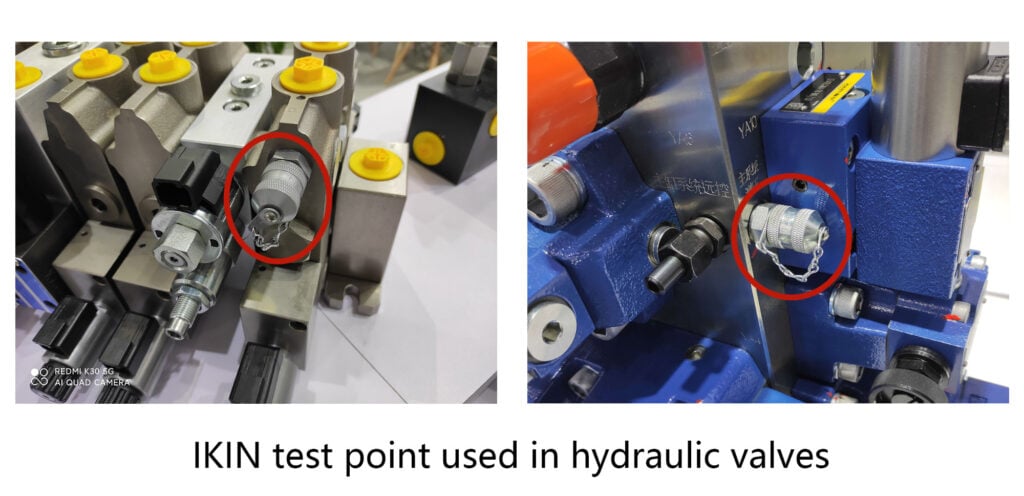
Afectados por la epidemia, la cantidad de clientes que participaron en el programa que en el año 2018 ha disminuido, pero muchos clientes aún asisten a la fiesta.
Las exhibiciones profesionales, con un sentido de la ciencia y la tecnología cuidadosamente preparadas por IKIN, han atraído la atención de muchos clientes.
Stand de IKIN
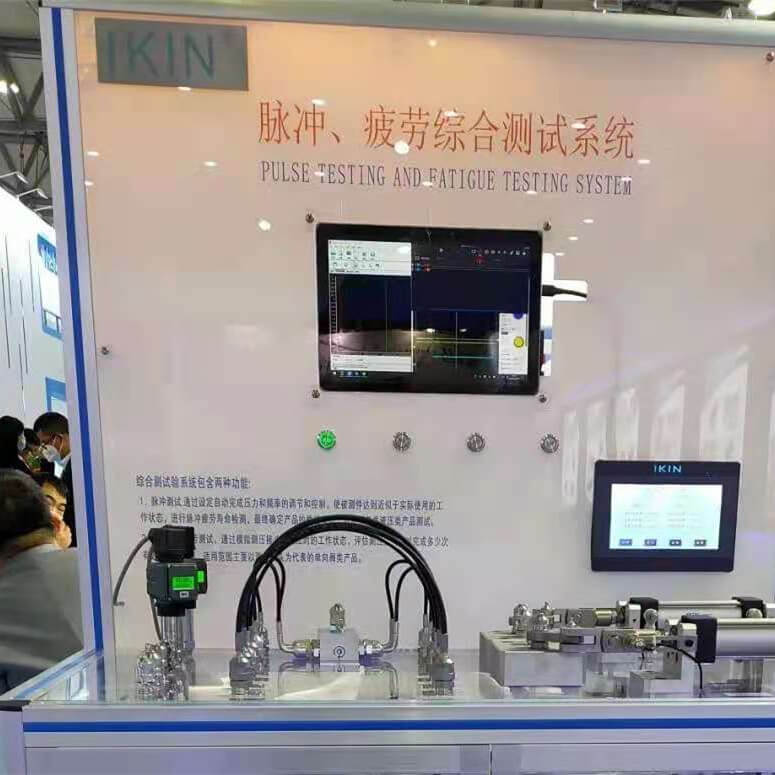
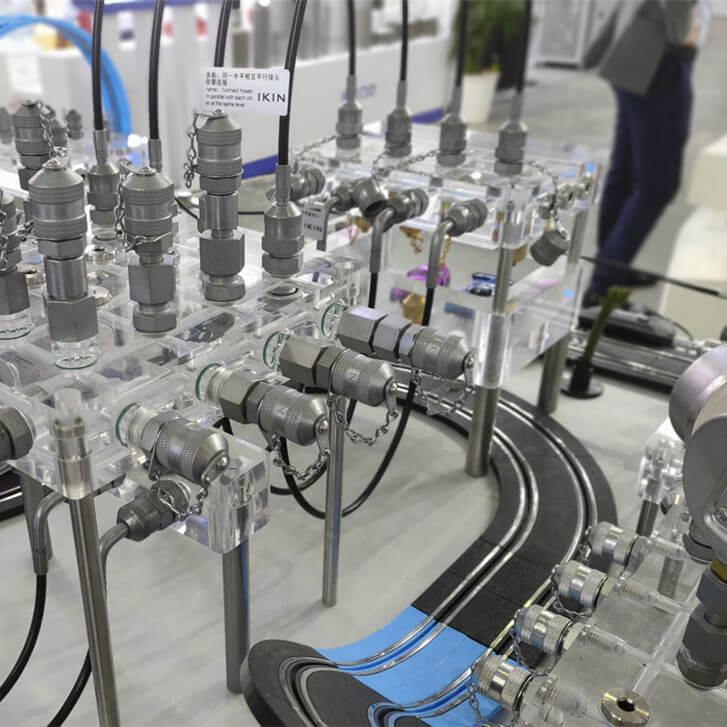
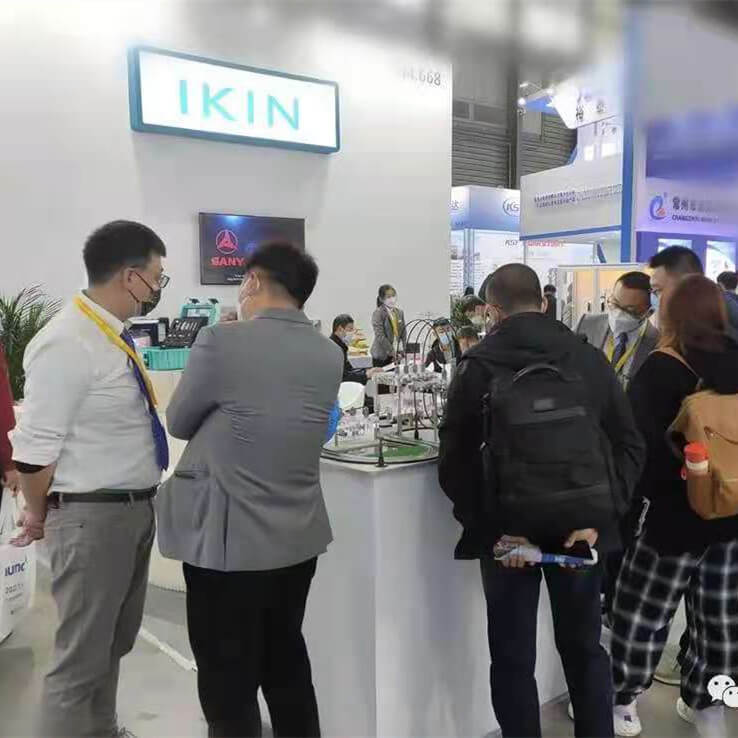
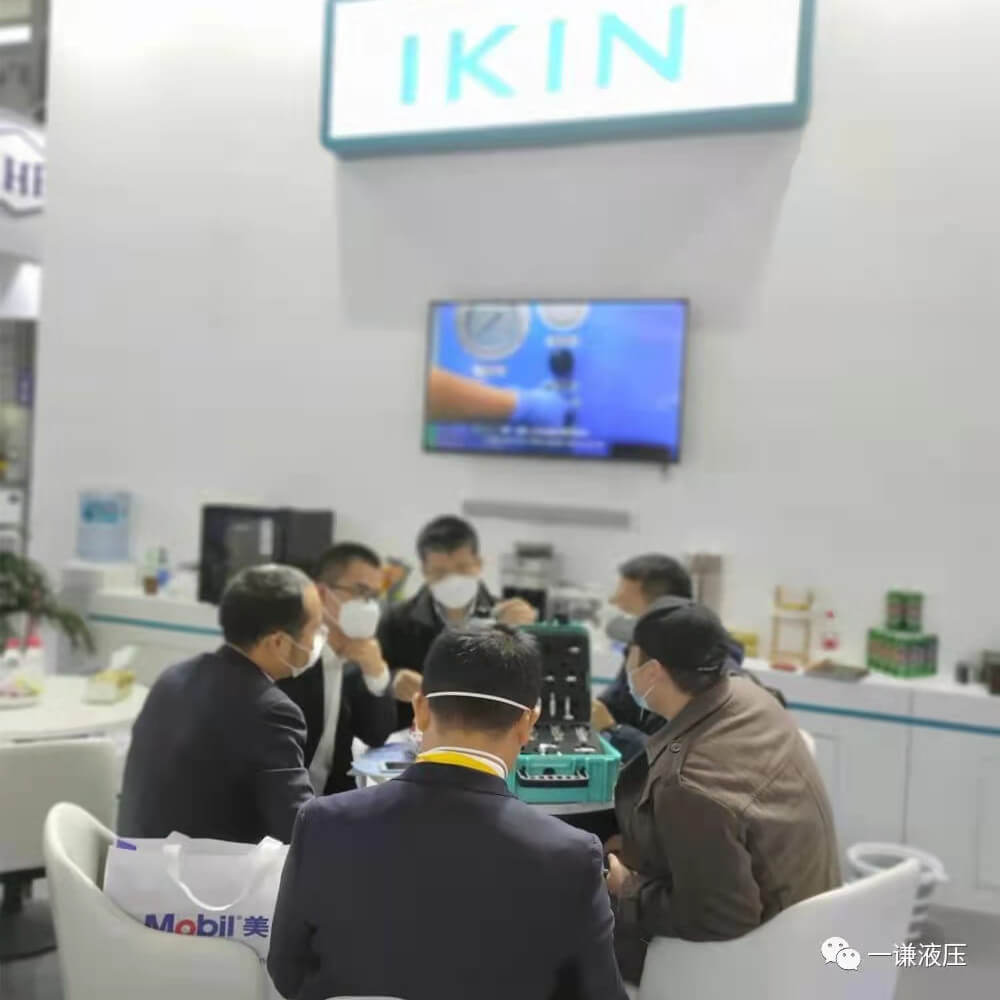
- Fabricante de China
- proveedor de Sany Crane, XCMG Group, Zoomlion, GE, etc.
- especializarse en accesorios de prueba hydrauli
- rendimiento confiable y de alto costo
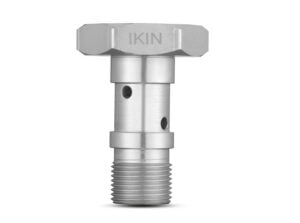
accesorios hidráulicos, personalizados para sistema de presión
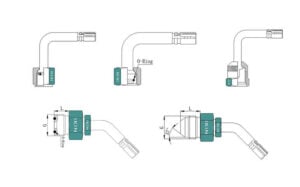
Conexión de manguera de 90 ° y 45 °
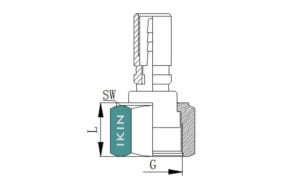
racores de manguera de micro calibre, con rosca hembra ORFS
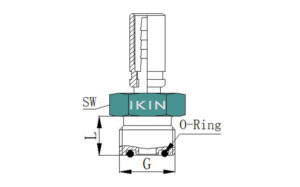
racores de manguera de micro calibre, con rosca exterior ORFS
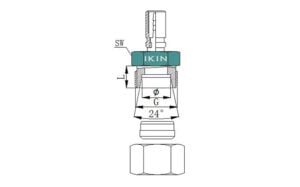
racores de manguera de prueba, racor cónico de 24 °, con rosca exterior
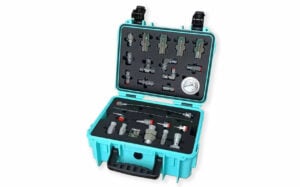
kit de prueba de presión
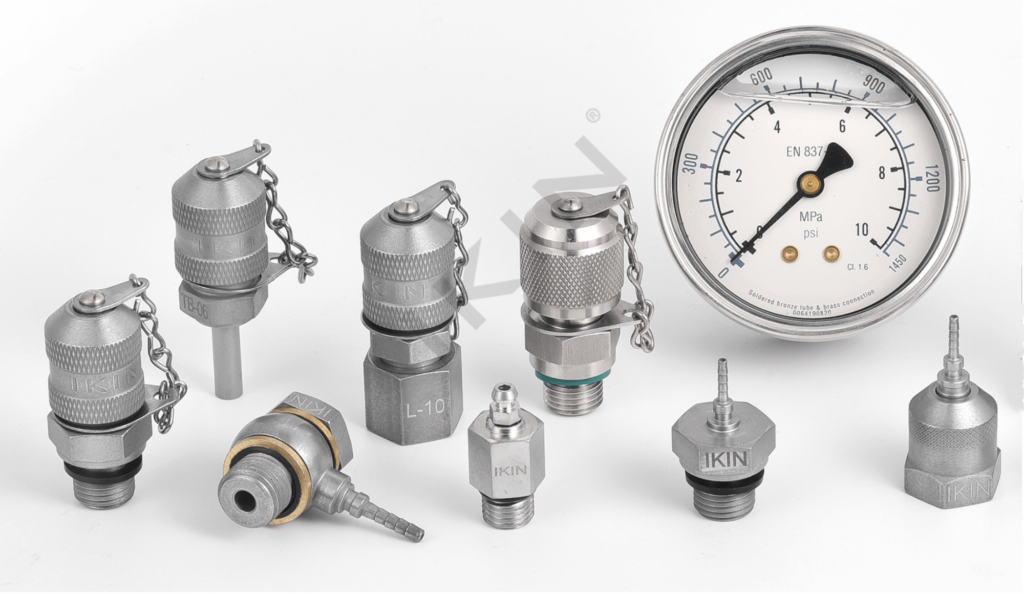
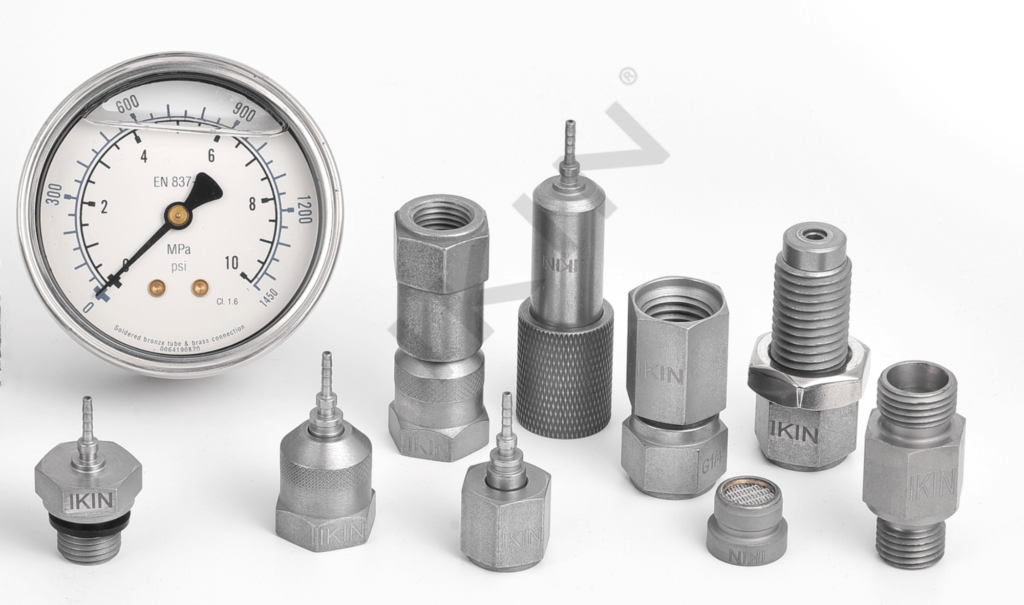
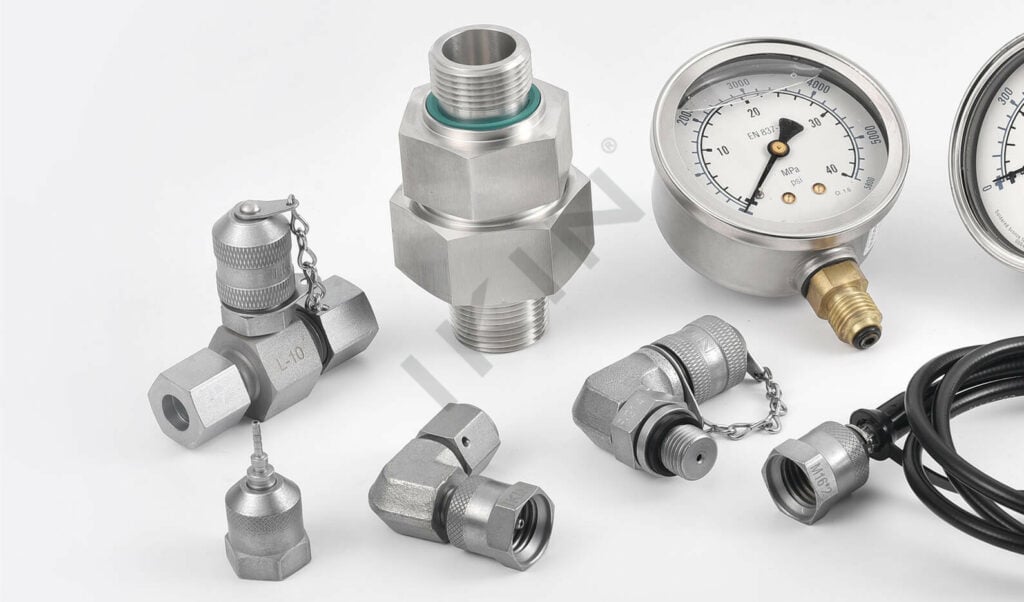
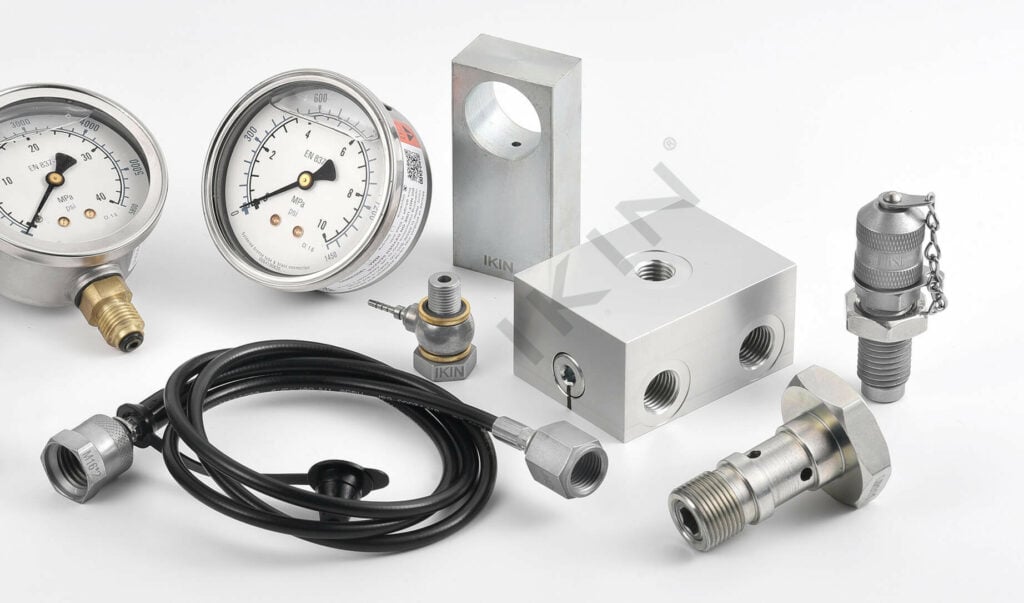
¿Cuáles son los tipos de accesorios de manguera hidráulica y análisis de fallas?
3 principales fabricantes en China
proveedor de mangueras de punto de prueba hidráulica
Aprobado por SGS
¿Cuáles son los tipos de accesorios y conjuntos de mangueras hidráulicas?
Con el rápido desarrollo de la maquinaria de construcción de China, la confiabilidad de los conjuntos de mangueras hidráulicas se ha convertido en uno de los temas más preocupantes de la industria.
El conjunto de la manguera hidráulica es un elemento básico en el sistema de transmisión hidráulica. La calidad del conjunto de mangueras afecta directamente el rendimiento del sistema hidráulico y el motor principal. Parte de la falla del conjunto de la manguera proviene de la estructura del núcleo de la junta.
El núcleo del conector de la manguera se divide principalmente en dos partes, una es la estructura de conexión, basada principalmente en las normas SAE, ISO y KES; La otra parte es la estructura de la parte de engarzado (estructura de la cola), que se combina con la chaqueta exterior y las capas de goma interior y exterior de la manguera para formar una deformación de engarzado confiable para cumplir con el rendimiento del conjunto de la manguera.
Si la estructura de la pieza de engarzado del núcleo de la junta no es razonable en el diseño de diferentes tipos de mangueras, se producirán problemas de calidad del producto en gran medida.
Por lo tanto, los tipos de núcleos de unión (diseñados) seleccionados para mangueras en diferentes entornos de trabajo también son diferentes, y un diseño razonable puede evitar o reducir la aparición de fallas.
1. Tipos y características de los racores de manguera
En toda la industria del ensamblaje de mangueras, existen principalmente dos tipos de conexiones confiables entre las juntas de manguera y las mangueras: juntas de manguera de retención total y juntas de manguera desmontables.
La junta de engarzado completo es un proceso en el que el módulo de engarzado de ocho partes de la máquina engarzadora aprieta uniformemente la junta de la manguera hasta cierto punto después de ensamblar el núcleo de la junta, la manguera y la camisa exterior, de modo que la junta de la manguera y la manguera se conviertan en un todo .
El conector de manguera desmontable comprime la manguera a través del núcleo del conector con el cono exterior y el núcleo del conector, de modo que la manguera está cerca del cono interior del manguito del conector, formando una conexión con una mayor fuerza de unión.
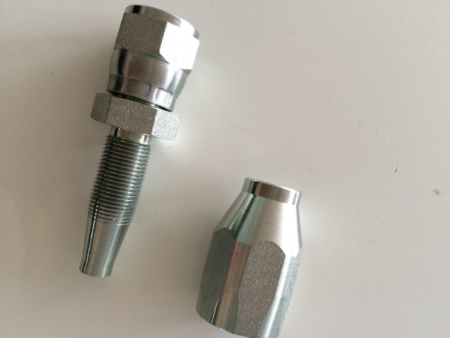
1.1 Forma y características del engarzado de la manguera
El tipo de retención de la manguera depende principalmente del tipo de manguera (o del tamaño de la goma interior y exterior) y el entorno de presión del conjunto de la manguera.
Se divide principalmente en tres categorías: engarzado de caucho que no se despega, engarzado de caucho exterior que se despega y engarzado de caucho interior y exterior.
Las características de cada tipo son:
(1) No se pela ni se engarza: no es necesario pelar el caucho interior y exterior de la manguera, y el producto se puede completar engarzando después de instalar la manguera. La tecnología de procesamiento es simple.
Este tipo de engarzado se utiliza a menudo para mangueras trenzadas de alambre de acero con capas externas de caucho relativamente delgadas, como las normas GB / T3683, EN853 y SAE.
(2) Pelado y prensado: es necesario quitar la capa de goma exterior de la manguera a una cierta longitud (la capa de goma exterior es más gruesa), que se utiliza para hacer que la capa de refuerzo de alambre de acero entre en contacto con la ranura del diente de la chaqueta.
Cuando la chaqueta se contrae y se deforma bajo una fuerza externa, doblará firmemente el alambre de acero, evitando así que la junta se salga cuando se somete a un impacto de alta presión.
Este tipo de engarzado se aplica principalmente a mangueras enrolladas con alambre de acero, como las normas GB / T10544, EN856 y SAE.
(3) Pelado y engarzado de caucho interno y externo: las capas de caucho interna y externa deben pelarse a una cierta longitud (el grosor del caucho interno y externo), la capa de alambre de acero y la capa de caucho interna se extruyen en una onda forma, generalmente adecuada para GB / T10544, EN856-R13, R15, etc. Especificaciones (32 o más incluyendo 32) manguera espiral de alambre de acero de ultra alta presión.
1.2. Conector de manguera tipo retención
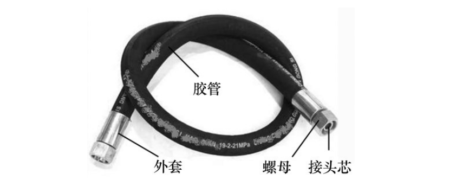
La junta de manguera de tipo de retención se compone principalmente de un núcleo de junta, una camisa exterior (la tuerca es una parte opcional) y otras partes.
1) Materiales, tipos y características del núcleo de la junta
Los materiales comúnmente utilizados para núcleos de juntas son aceros 20, 35 y 45. Para núcleos de juntas rectas, a menudo se utilizan aceros 35 y 45, que tienen una gran resistencia a la deformación. Teniendo en cuenta la capacidad de fabricación de los núcleos de juntas por flexión, generalmente se utilizan aceros 20 o 35.
Con la popularización de la tecnología de doblado en caliente, los aceros 35 y 45 también se pueden utilizar para núcleos de articulaciones de codo.
Las características estructurales del núcleo de la junta están estrechamente relacionadas con la forma de engarzado de la manguera y, según la regularidad de la estructura, los tipos de núcleos de la junta se dividen a grandes rasgos en: estructura en zigzag, estructura rectangular, estructura de bloqueo interno, etc.
(1) El núcleo de la articulación con estructura de diente de sierra, comúnmente conocido como tipo de púas, se compone principalmente de ranuras en diente de sierra, y el ángulo entre la hipotenusa y el eje generalmente no supera los 20 °.
La parte superior del dentado tiene forma de arco o plana, y el plano y el lado corto del dentado son esquinas redondeadas lisas (0,2 ~ 0,5 mm) para evitar daños en la capa de goma interior de la manguera durante el montaje y el engarzado.
El núcleo de la junta de esta estructura tiene una fuerte resistencia al sellado y al arrancamiento, y se utiliza principalmente para mangueras de caucho enrolladas con alambre de acero.
(2) Núcleo de junta de estructura rectangular: compuesto principalmente de varias ranuras rectangulares, los cuerpos de 5 ~ 7 ranuras forman una ranura de sellado y la profundidad de la ranura es generalmente de 0,3 ~ 0,6 mm.
La superficie de transición entre la parte superior de la ranura y la parte inferior de la ranura es generalmente lisa con esquinas redondeadas, con un radio de 0,1 mm ~ 0,3 mm.
Evite que se dañe la capa de goma interior de la manguera durante el montaje y el engarzado. La estructura general es simple, con buen rendimiento de sellado, pero baja resistencia a la extracción. Esta estructura se usa a menudo para mangueras de resina, mangueras trenzadas de alambre de acero y otros tipos de mangueras.
Los materiales comúnmente utilizados para núcleos de juntas son aceros 20, 35 y 45. Para núcleos de juntas rectas, a menudo se utilizan aceros 35 y 45, que tienen una gran resistencia a la deformación. Teniendo en cuenta la capacidad de fabricación de los núcleos de juntas por flexión, generalmente se utilizan aceros 20 o 35.
Con la popularización de la tecnología de doblado en caliente, los aceros 35 y 45 también se pueden utilizar para núcleos de articulaciones de codo.
Las características estructurales del núcleo de la junta están estrechamente relacionadas con la forma de engarzado de la manguera y, según la regularidad de la estructura, los tipos de núcleos de la junta se dividen a grandes rasgos en: estructura en zigzag, estructura rectangular, estructura de bloqueo interno, etc.
Con el rápido desarrollo de la maquinaria de construcción de China, la confiabilidad de los conjuntos de mangueras hidráulicas se ha convertido en uno de los temas más preocupantes de la industria.
El conjunto de la manguera hidráulica es un elemento básico en el sistema de transmisión hidráulica. La calidad del conjunto de mangueras afecta directamente el rendimiento del sistema hidráulico y el motor principal. Parte de la falla del conjunto de la manguera proviene de la estructura del núcleo de la junta.
El núcleo del conector de la manguera se divide principalmente en dos partes, una es la estructura de conexión, basada principalmente en las normas SAE, ISO y KES; La otra parte es la estructura de la parte de engarzado (estructura de la cola), que se combina con la chaqueta exterior y las capas de goma interior y exterior de la manguera para formar una deformación de engarzado confiable para cumplir con el rendimiento del conjunto de la manguera.
Si la estructura de la pieza de engarzado del núcleo de la junta no es razonable en el diseño de diferentes tipos de mangueras, se producirán problemas de calidad del producto en gran medida.
Por lo tanto, los tipos de núcleos de unión (diseñados) seleccionados para mangueras en diferentes entornos de trabajo también son diferentes, y un diseño razonable puede evitar o reducir la aparición de fallas.
Con el rápido desarrollo de la maquinaria de construcción de China, la confiabilidad de los conjuntos de mangueras hidráulicas se ha convertido en uno de los temas más preocupantes de la industria.
El conjunto de la manguera hidráulica es un elemento básico en el sistema de transmisión hidráulica. La calidad del conjunto de mangueras afecta directamente el rendimiento del sistema hidráulico y el motor principal. Parte de la falla del conjunto de la manguera proviene de la estructura del núcleo de la junta.
El núcleo del conector de la manguera se divide principalmente en dos partes, una es la estructura de conexión, basada principalmente en las normas SAE, ISO y KES; La otra parte es la estructura de la parte de engarzado (estructura de la cola), que se combina con la chaqueta exterior y las capas de goma interior y exterior de la manguera para formar una deformación de engarzado confiable para cumplir con el rendimiento del conjunto de la manguera.
Si la estructura de la pieza de engarzado del núcleo de la junta no es razonable en el diseño de diferentes tipos de mangueras, se producirán problemas de calidad del producto en gran medida.
Por lo tanto, los tipos de núcleos de unión (diseñados) seleccionados para mangueras en diferentes entornos de trabajo también son diferentes, y un diseño razonable puede evitar o reducir la aparición de fallas.
(3) Núcleo de la junta de la estructura de bloqueo interno, también conocida como estructura anti-extracción.
Este tipo de estructura está especialmente diseñada para evitar que la manguera se salga de la junta de la manguera, y la estanqueidad está asegurada por la estructura rectangular.
Por lo tanto, el núcleo de la junta de la estructura de bloqueo interior es en realidad una combinación de la estructura anti-extracción y la estructura rectangular.
Este tipo de junta tiene las características de alta confiabilidad y larga vida útil. Se utiliza principalmente para mangueras de bobinado de alambre de acero de gran diámetro y presión ultra alta y ensambles de mangueras de bobinado de alambre de acero dinámicas en condiciones de trabajo duras.
2) Material, tipo y características de la tapa exterior
El material de la camisa exterior es generalmente acero 20, y la buena deformación plástica del material se utiliza para hacer que el tubo de caucho extruido con dientes de la camisa exterior y el núcleo de la junta se ajusten.
También hay muchos tipos de tapas exteriores, principalmente para diferentes núcleos de juntas, diferentes entornos de trabajo, diferentes condiciones de trabajo específicas y diferentes formas estructurales requeridas.
Por lo general, el lado interior de la chaqueta está formado por algunas ranuras o estrías. Hay ranuras cuadradas, trapezoides, zigzags, etc., que deben usarse junto con diferentes tipos de núcleos de juntas.
Los tipos de estructura de tapas exteriores comúnmente utilizados se dividen aproximadamente en los siguientes tres tipos:
(1) Revestimiento de ranura de diente en forma de onda. La superficie exterior de la chaqueta ondulada es principalmente un cilindro liso, y el ángulo entre la hipotenusa del diente interior y el eje es de 25 ° ~ 45 °.
El lado radial y la hipotenusa están conectados por esquinas redondeadas de 0,2 ~ 0,5 mm, generalmente compuestas por 3 ~ 5 dientes internos. Principalmente adecuado para conjuntos de mangueras de presión media y baja que no se pelan, como tubos de resina y mangueras trenzadas de alambre de acero; Se puede usar junto con la estructura de diente de sierra y el núcleo de la junta de la estructura rectangular, con una débil resistencia a la extracción y una tecnología de procesamiento simple.
(2) Revestimiento de ranura de diente trapezoidal. La superficie exterior es un cilindro liso y la superficie interior es una ranura con un cierto número de dientes trapezoidales.
El ángulo entre la hipotenusa y el eje es de 25 ° ~ 45 °, y cada dentado es una ranura rectangular. La parte superior del dentado es un plano con un ancho de 1 a 2 mm, y las esquinas afiladas tienen una transición con una esquina redondeada de 0,2 mm.
Se puede utilizar junto con un núcleo de junta de estructura rectangular para formar una resistencia de extracción efectiva, adecuada para pelar tuberías trenzadas de media y alta presión y tuberías enrolladas.
(3) Cubierta alveolar compuesta. La superficie exterior es una ranura en forma de T correspondiente a la dislocación del diente interno, y la superficie interna es una ranura con un cierto número de dientes trapezoidales bilaterales.
Es adecuado para su uso con el núcleo de la junta de la estructura de bloqueo interno y se usa para el ensamblaje de mangueras de alta presión y gran caudal.
Con el desarrollo gradual de la maquinaria de construcción a gran escala, el sistema hidráulico también se desarrolla constantemente en la dirección de alta presión, y la aplicación de esta forma estructural se está volviendo cada vez más extensa.
2. Selección de la cantidad de prensado de juntas
De acuerdo con los diferentes tipos de mangueras y tipos de juntas, la cantidad adecuada de prensado también es un factor clave para garantizar que el conjunto de mangueras no presente problemas.
La cantidad de prensado afecta directamente el rendimiento del sellado, la resistencia al arrancamiento y la vida útil.
Generalmente, al juzgar la calidad de la deformación por engaste, observe si el espacio entre la superficie del diente interno del manguito externo y la ranura del diente del núcleo de la junta se llena con el tubo de goma.
Solo cuando se satisface la deformación se puede garantizar la resistencia a la extracción y el rendimiento de sellado.
En términos generales, la cantidad de prensado de la manguera de goma interior, como el caucho de nitrilo, debe hacer que la capa de goma interior se comprima (40% ~ 45% para manguera trenzada de alambre de acero, 50% ~ 55% para manguera enrollada de alambre de acero de cuatro y seis capas); La cantidad de prensado del tubo de resina y la manguera de PTFE asegura que la cantidad de compresión de la capa de caucho interior sea de 25% a 30%.
En el caso de asegurar el precinto, cuanto menor sea la retención, mejor. Mediante cálculo y verificación, se selecciona una cierta cantidad de retención.
3. Conclusión
El artículo analiza los tipos de núcleos de unión y tapas exteriores que se utilizan en el conjunto de manguera de retención.
Cuando el engarzado de la manguera tiene problemas de calidad y los tipos de fallas.
Analicé las razones y cómo utilizar una configuración de prensado razonable y juntas de prensado, para evitar el problema del bajo rendimiento del ensamblaje de la manguera causado por una estructura de prensado de manguera irrazonable.
Mejore y controle de manera efectiva la confiabilidad del conjunto de mangueras, y también brinde un fuerte apoyo para el rápido desarrollo de diversas maquinarias de ingeniería hidráulica.
Fluido Ikin
—— Los 3 principales fabricantes en China, se especializan en puntos de prueba hidráulicos
Beneficios que puede encontrar En Ikin
precio de fábrica y moq bajo
calidad confiable, proveedor de Eaton, Hawee, etc.
Inspección de fugas 100% Antes de terminar
3 años de garantía
10 días hábiles para envíos a granel
coincidir con otros accesorios como minimess, stauff, etc.
Estructura de diseño de sello de cono, estable y de larga duración.
Obtenga su muestra gratis
en 2 días
* Respetamos su confidencialidad y toda la información está protegida.
Cómo mantener y administrar el sistema hidráulico de la prensa de extrusión
Cómo mantener y administrar el sistema hidráulico de la prensa de extrusión
Las prensas de extrusión de aluminio grandes se pueden utilizar para producir productos de extrusión de aluminio de alta especificación, como perfiles industriales, perfiles de tránsito ferroviario y radiadores grandes.
Se puede utilizar en la industria aeroespacial, transporte ferroviario, automóviles, barcos, construcción, fabricación de maquinaria, energía electrónica y otros campos. En el proceso de trabajo de la prensa de extrusión de aluminio grande, para garantizar la precisión de trabajo y el alto rendimiento, la premisa es tener un cierto grado de estabilidad. Una vez que la estabilidad de la extrusora no cumpla con los estándares de producción, la calidad de los productos producidos se verá comprometida en gran medida. Y las empresas también sufrirán enormes pérdidas económicas.
一. Problemas comunes del sistema hidráulico de las grandes prensas de extrusión de aluminio y sus soluciones.
(一) Fuga de tubería:
Es más probable que la posición de soldadura de la tubería y la brida cause fugas en la tubería. Además, es muy probable que la superficie de instalación de la brida de la tubería y la posición del tornillo provoquen fugas en la tubería.
La aparición de fugas en la tubería se debe principalmente al aflojamiento de los tornillos y las uniones de la tubería debido a la operación a largo plazo. Al mismo tiempo, después de que el sello de la superficie de montaje de la brida esté envejeciendo, el anillo de sellado se dañará.
La soldadura inadecuada causó poros y grietas, y se produjeron fugas. Además, el tiempo de uso fue demasiado largo, la conciencia de seguridad no fue fuerte y no se llevó a cabo un mantenimiento oportuno, lo que provocó que la situación se expandiera y eventualmente causara fugas. Podemos eliminar la vibración de la tubería y mejorar la estabilidad agregando abrazaderas y soportes para tubería.
Si la operación de soldadura no está estandarizada, hay poros o grietas, podemos pulir en la posición original, y luego de remover los escombros, podemos soldar nuevamente.
(二) Fuga de aceite en el cilindro:
1. La tasa de aparición de fugas en los cilindros de aceite es relativamente alta. Debido a las condiciones de trabajo a largo plazo, inevitablemente causará una gran cantidad de partículas abrasivas. Al mismo tiempo, debido a que la posición expuesta del vástago del pistón está expuesta al aire durante mucho tiempo, es inevitable que haya una gran cantidad de polvo y polvo de aluminio adherido.
En tales situaciones, generalmente se usa un anillo de polvo para raspar. Sin embargo, en vista del efecto del anillo de polvo, es difícil rasparlo por completo, por lo que el sello del vástago del pistón se daña, lo que a su vez provoca fugas. Por lo tanto, generalmente se adoptan dos métodos de tratamiento para las fugas del cilindro de aceite: Primero, limpie el cilindro de aceite y reemplace los sellos; En segundo lugar, confirme si la capa superficial del vástago del pistón está desgastada o no,
2. El eje del cilindro no es paralelo al riel guía y el error excede el rango estándar: 0.04-0.08 mm / m. A su vez, los pernos de fijación de la tapa del extremo se aflojaron y el sello falló. Entonces necesitamos mantener el paralelismo y controlar el error dentro del rango estándar.
3. El sello está roto y la fuga de aceite ocurre debido a la contrapresión y el ajuste de presión es demasiado alto. A su vez, el sello está expuesto a una presión excesiva y el sello se rompe. Esto requiere restablecer la presión del sistema hidráulico y probar los componentes de la válvula de control hidráulico.
4. Los sellos están muy desgastados y fallan porque el aceite hidráulico está muy contaminado y produce muchas impurezas. Cuando la temperatura del aceite es alta durante mucho tiempo, el aceite hidráulico se oxida gradualmente, lo que resulta en la producción de depósitos coloidales. Cuando la temperatura del aceite está en un estado de baja temperatura durante mucho tiempo, se perderá la elasticidad del sello. El envejecimiento del sello se debe a la acumulación de una gran cantidad de residuos de aceite.
Entonces necesitamos fortalecer la gestión del aceite hidráulico y controlar estrictamente la intrusión de fuentes de contaminación; Confirmar el estado de funcionamiento del sistema de refrigeración del equipo hidráulico y garantizar su funcionamiento normal. La temperatura más adecuada es 30-45 ℃.
5. Cuando no se selecciona el sello apropiado para el tratamiento de sellado, al seleccionar el sello. Para tener en cuenta el material, el modelo y la rugosidad del sello, se producen fugas de aceite. Por lo tanto, al seleccionar sellos, identifique cuidadosamente las características de los sellos y seleccione los sellos razonables correspondientes.
(三) Fuga de los componentes de la válvula de control:
La fuga interna es la más común en la fuga de los componentes de la válvula de control. La causa principal de las fugas internas es la gran acumulación de impurezas hidráulicas, que a su vez bloquea los componentes de la válvula de control; Además, el desgaste excesivo del núcleo de la válvula y el cierre inadecuado pueden causar fugas.
Una presión excesiva provocará la sujeción hidráulica del carrete, lo que también provocará fugas. Se recomienda limpiar la válvula de control repetidamente después del desmontaje o pulir los componentes de la válvula de control. Para mejorar su precisión y restaurarlo a su aspecto original.
(四) Fallo de la válvula solenoide: El fallo de la válvula solenoide se puede dividir en los siguientes tipos:
1. El carrete no se mueve: (1) Fallo del electroimán, combinado con la detección de vibración y campo magnético, se puede ver que el carrete no se mueve; (2) El núcleo de la válvula está sujeto, el aceite cambia y el resorte de retorno está defectuoso. Después de la detección de vibración, se puede ver la falla atascada del núcleo de la válvula;
2. Gran pérdida de presión: (1) El flujo es demasiado grande y el tamaño es incorrecto, lo que se puede ver mediante la inspección conjunta de la vibración y el campo magnético; (2) El carrete no se mueve en su lugar y la falla de atasco del carrete se puede ver a través de la detección de vibraciones;
3. Fuga de flujo magnético: aparecen defectos en la superficie de la bobina electromagnética, que se pueden ver mediante la detección del campo magnético.
4. Choque (vibración): la velocidad de cierre del carrete es demasiado rápida y los tornillos están flojos, lo que se puede ver mediante la detección de vibraciones.
En vista de las causas de los problemas anteriores, tome las medidas correspondientes para resolver el problema.
二. Mantenimiento y gestión del sistema hidráulico de una gran prensa extrusora de aluminio.
(一) Elaborar plan de mantenimiento diario
(1) Para algunos equipos expuestos al aire durante mucho tiempo, límpielos regularmente para mantener las partes expuestas del equipo limpias y libres de impurezas;
(2) Mantener el entorno operativo limpio y ordenado para evitar la intrusión de polvo y escombros y contaminar el sistema hidráulico;
(3) Realizar inspecciones de patrulla en cualquier momento donde la tasa de fuga de aceite sea relativamente alta, y una vez encontrada, tomar las medidas correspondientes para solucionarlas inmediatamente;
(4) Estandarizar el proceso de inspección. Delimite la ruta de inspección y la parte más alta del punto de derrame de petróleo. Una vez finalizada una determinada etapa del trabajo de inspección, se entregará al personal de la etapa siguiente y se explicará en detalle el avance del trabajo de la etapa anterior;
(5) Registre el estado operativo original en detalle. Comprender las condiciones normales de trabajo del sistema hidráulico puede ayudar a descubrir y resolver problemas a tiempo durante el proceso de inspección, mejorar la eficiencia del trabajo y evitar riesgos de seguridad.
(二) Desarrollar un sistema de inspección y mantenimiento regular y programar una fecha para calibrar varios instrumentos del sistema hidráulico. Asegúrese de que el medidor funcione correctamente y tenga un alto grado de precisión.
Al mismo tiempo, se debe probar la presión del sistema hidráulico para establecer un valor de presión razonable para mantener la temperatura normal. Para evitar un desequilibrio de presión, la temperatura es demasiado baja o demasiado alta, lo que provoca fugas. Limpie y reemplace regularmente el elemento del filtro para determinar la composición de los desechos y la contaminación del aceite hidráulico.
Confirme el grado de desgaste y desgaste del sistema hidráulico, y muestree y pruebe el aceite hidráulico de la extrusora cada tres meses. Compruebe la viscosidad del aceite hidráulico, el índice de acidez, la humedad, las partículas y otros elementos para poder tomar las medidas razonables para solucionarlos.
三. Conclusión
A través del análisis, se puede confirmar que la fuga del sistema hidráulico de la prensa de extrusión de aluminio se debe principalmente a la falta de estabilidad del sistema hidráulico. Entonces tenemos que tomar las medidas correspondientes.
Sin embargo, las soluciones siempre se pueden atribuir a medidas correctivas y no pueden tener un efecto preventivo.
Por lo tanto, es de gran importancia tomar el mantenimiento y la gestión necesarios del sistema hidráulico en el trabajo diario.
bridas de válvulas productos de diseño de fluidos accesorios de brida hidráulica accesorios hidráulicos bspp bridas de válvula acoplamientos de desconexión rápida válvula de fluido american fluid power acoplamientos de conexión rápida accesorios de prueba hidráulica accesorios de prueba de presión hidráulica manguera de prueba hidráulica accesorios de prueba hidráulica accesorios de puerto de prueba hidráulica accesorios de prueba hidráulica cat accesorios de prueba hidráulica john deere accesorios de manómetro de prueba hidráulica accesorios de manguera de prueba hidráulica accesorios de prueba hidráulica hitachi accesorios de prueba hidráulica jcb accesorios de prueba hidráulica jic kit de accesorios de prueba hidráulica accesorios de prueba hidráulica komatsu accesorios de prueba hidráulica métrica accesorios de punto de prueba hidráulica conectores de punto de prueba hidráulica oruga ar accesorios de puerto de prueba hidráulica parker accesorios de puerto de prueba hidráulica parker accesorios de prueba hidráulica parker accesorios de prueba hidráulica stauff accesorios de prueba hidráulica accesorios en T de prueba hidráulica accesorios de prueba hidráulica volvo conexión de manómetro punto de prueba de fluido hidráulico accesorios de Parker roscas de conexión punto de prueba accesorios de puerto de prueba hidráulica acoplamiento hidráulico y Prueba de mangueras Punto de prueba de presión de acoplamiento Accesorios hidráulicos Ensambles de prueba de mangueras Conexiones de punto de prueba Punto de prueba Mangueras Conexiones de manómetro Acoplamientos de prueba para verificación de presión
¿Cuál es la aplicación del punto giratorio hidráulico?
¿Cuál es la aplicación del punto giratorio hidráulico?
El sistema de energía hidráulica se usa ampliamente en el campo industrial en virtud de sus muchas ventajas. Cuando el equipo giratorio necesita utilizar un medio hidráulico como potencia de transmisión, existen requisitos estrictos sobre la precisión de la presión y el control del medio hidráulico, generalmente una presión superior a 30 MP, y un funcionamiento confiable.
Para el desarrollo y aplicación de puntos rotativos, es necesario simplificar la estructura del equipo logrando una mejor función de conversión. La aplicación más extensa y típica de los puntos rotativos hidráulicos se encuentra en las bobinadoras de banda ancha de acero laminadas en caliente de equipos de laminación de acero. Y en los cilindros de expansión y contracción de desenrolladores, bobinadoras y otros equipos en la línea de producción de bandas laminadas en frío.
1. Análisis del principio estructural del punto giratorio hidráulico.
1.1 Estructura y principio
El punto giratorio hidráulico tiene dos puertos de control de aceite y un puerto de drenaje, que están conectados respectivamente a las tuberías fijas del sistema hidráulico. Cada tubería externa está conectada estáticamente a la carcasa del punto giratorio.
La carcasa del punto giratorio hidráulico se fija en la carcasa del equipo principal correspondiente y se mantiene relativamente estática con la base del equipo principal, conectada con el equipo principal a través del mandril. La holgura entre el diámetro exterior del mandril y el diámetro interior de la junta rotativa hidráulica. Se requiere que el espacio entre el cilindro del cilindro y el pistón sea el mismo que el del cilindro hidráulico, generalmente 0.04 mm ~ 0.07 mm. Cuando las condiciones lo permitan, reduzca el límite tanto como sea posible. Cada vez que se pone en marcha el sistema hidráulico, se formará una película de aceite de presión estática en el espacio correspondiente, que protege el mandril y la junta rotativa hidráulica del desgaste y juega un papel de sellado.
El sello giratorio se instala en el mandril del equipo, y su función principal es aislar la cavidad de entrada de aceite y la cavidad de retorno de aceite para formar dos espacios sellados independientes. La mayoría de los materiales son materiales compuestos resistentes al desgaste o materiales metálicos. Los sellos giratorios deben soportar altas presiones por encima de 30 MP, y deben ser resistentes a golpes de alta presión, no se deforman fácilmente y tienen pequeñas fugas. El sello giratorio y la pared interior de la junta giratoria no están en contacto y existe una fricción de fluido entre los dos.
La vibración y el impacto generado por el funcionamiento a alta velocidad del equipo principal se transmiten a la junta rotativa hidráulica a través del mandril, dando como resultado un cierto balanceo de la junta rotativa. Se utilizan dos cojinetes para soportar la fuerza axial y la fuerza radial generadas por la oscilación de la carcasa de la junta giratoria y para realizar el posicionamiento preciso del eje central del equipo y la junta giratoria.
El sello de la cara del extremo adopta un sello de labio esqueleto, que se utiliza para sellar el aceite que se escapa del sello giratorio. La presión del aceite con fugas generalmente no excede los 0.3MP. Una vez que aumenta la fuga, es fácil dañar el sello del extremo y hacer que el aceite hidráulico se escape al exterior. El puerto de aceite de la carcasa de la junta rotativa está empalmado con el puerto de aceite en el mandril del equipo.
1.2 Análisis de la estructura de sellado interna
Hay dos tipos principales de sellos giratorios para puntos giratorios, sellos compuestos y sellos mecánicos. El rendimiento de sellado del sello de material compuesto es relativamente mejor y se utiliza donde el cilindro hidráulico tiene un posicionamiento intermedio. El punto giratorio sellado con materiales compuestos puede hacer que el punto giratorio sea más compacto y exquisito debido al pequeño tamaño del sello en sí. El costo del sello compuesto en sí es mucho más económico que el del sello mecánico.
El sello giratorio compuesto se compone de dos partes, una combinación de un anillo exterior de PTFE y una junta tórica de NBR. La junta tórica desempeña la función de soportar el anillo exterior, lo que hace que todo el sello giratorio sea más fácil de instalar, deslizándose entre el anillo exterior y la carcasa de la junta giratoria. La fabricación de sellos mecánicos es más complicada, los requisitos de precisión también son relativamente altos y el precio relativo es relativamente alto.
2. Instalación y mantenimiento de puntos rotativos hidráulicos
Al instalar el punto giratorio hidráulico en el mandril del equipo principal, asegúrese de que la cavidad de la junta giratoria y el mandril del equipo principal tengan una buena coaxialidad. Generalmente se requiere que la coaxialidad entre el eje de la junta rotativa y el eje del equipo se controle dentro de ± 1 mm / m. La falta de concentricidad hará que el punto giratorio hidráulico produzca oscilaciones radiales relativamente grandes durante la rotación a alta velocidad. La fuerza radial hace que la junta rotatoria y el mandril se deslicen periódicamente en la dirección axial. No solo se destruye la película de aceite dinámico y aumenta el desgaste de la superficie de contacto, sino que también se desgasta la cara del extremo del sello. Al mismo tiempo, el rodamiento puede soportar un mayor impacto externo. Por lo tanto, una mala coaxialidad causará un gran daño al sello giratorio interno y a los cojinetes, y afectará la vida útil.
La carcasa de la junta rotativa está fija para evitar que gire sincrónicamente con el husillo, siempre que se pueda evitar que gire en círculo.
No use más restricciones. La fuerza radial o axial que actúa sobre el armazón se transmitirá al cojinete de la junta rotativa hidráulica y al sello giratorio interno a través del armazón, lo que obligará al cojinete o sello a desgastarse o dañarse.
Al conectar tuberías de aceite externas, respete estrictamente las especificaciones de instalación del equipo hidráulico. En particular, es necesario verificar estrictamente la limpieza de cada puerto de aceite para evitar que se introduzcan contaminantes externos y rebabas mecanizadas en la junta rotativa. Debido a la compleja estructura interna de la junta rotativa hidráulica y al pequeño espacio libre correspondiente, una vez que los contaminantes externos ingresan a la junta rotativa hidráulica, es fácil dañar la película de aceite, los sellos mecánicos y los atascos de los cojinetes, y fugas graves.
El sello de aceite esquelético de la junta rotatoria se usa para sellar el mandril giratorio, de modo que el aceite que se escapa del sello rotatorio se drene del tubo de aceite con fugas al tanque de aceite. La resistencia a la presión del sello de aceite no suele ser superior a 3 bar, por lo que el tubo de aceite con fugas debe devolverse al aceite sin problemas.
Durante la instalación, el puerto de aceite con fugas de la junta rotativa no debe bloquearse. Si hay una válvula en el tubo de aceite con fugas, debe abrirse antes de introducir el medio; de lo contrario, el sello de aceite se saldrá inevitablemente. Tampoco es posible incorporar el tubo de aceite con fugas en el tubo de retorno de aceite, porque la presión del tubo de retorno de aceite suele superar los 3 bar. No instale un filtro en la tubería de aceite con fugas. Las juntas rotativas generalmente tienen fugas, por lo que no se pueden usar en ocasiones en las que se requiere presión. La fuga de los cierres mecánicos es mayor.
Se puede considerar el servocontrol cuando se requiere controlar la carrera del cilindro hidráulico para compensar la fuga. Cuando el cilindro hidráulico no está posicionado en el medio, el problema será más simple, siempre y cuando el cilindro hidráulico continúe suministrando el medio después de que el cilindro hidráulico se mueva a la posición límite.
Las juntas rotativas generalmente se lubrican y enfrían con medio, por lo que no es posible probar o conducir sin pasar el medio. Asegúrese de abrir la tubería de aceite con fugas después de revisar la junta rotativa o el equipo relacionado. El desgaste o daño de las juntas rotativas hidráulicas se puede estimar midiendo la fuga. La fuga de las juntas rotativas se debe monitorear y rastrear regularmente para monitorear las condiciones de operación de las juntas rotativas.
3. Fallos habituales de las juntas rotativas hidráulicas
En el uso real, las juntas rotativas hidráulicas tienen principalmente dos tipos de fallas. Una falla se manifiesta como el daño del cojinete interno de la junta giratoria y la otra es la fuga externa de la junta giratoria.
Analice las causas del daño interno de los rodamientos, hay tres puntos principales:
1) El aceite hidráulico tiene poca limpieza y granularidad durante la instalación o durante el uso, lo que resulta en un serio desgaste y falla de los elementos rodantes del rodamiento;
2) Cuando se instala la junta rotativa, no se cumplen los requisitos de precisión de la instalación, lo que genera una fuerza desigual en el estado de carga estática del rodamiento y un valor de vibración excesivo en el estado de carga dinámica, lo que daña el rodamiento;
3) El diseño de la junta rotativa hidráulica seleccionada y la calidad de fabricación no cumplen con los requisitos de las condiciones de trabajo del equipo. Las razones de la fuga fuera de la junta rotativa son:
La precisión de mecanizado de la superficie de contacto del sello de instalación es baja, lo que no puede cumplir con los requisitos de precisión del sello;
La selección e instalación del sello no son adecuadas para los requisitos de las condiciones de trabajo;
La precisión de la instalación de la junta rotativa es pobre, lo que provoca una vibración excesiva y daña el sello.
4. Conclusión
En aplicaciones prácticas, debido a las complejas condiciones de trabajo del equipo principal y al entorno cambiante. Al seleccionar una aplicación específica, se debe seleccionar una junta giratoria adecuada para una amplia gama de cargas de acuerdo con las condiciones de trabajo específicas. Para cumplir con los requisitos del equipo principal, desde baja presión y baja velocidad hasta alta presión y alta velocidad en una amplia gama de condiciones de trabajo. La junta rotativa hidráulica de sello mecánico de alta precisión puede realizar mejor el propósito de pequeñas fugas, operación confiable y duradera.
Al mejorar la precisión del procesamiento y los requisitos técnicos de las piezas, y mejorar la precisión de la instalación, la capacidad de la junta giratoria para adaptarse a alta velocidad y alta presión se puede mejorar enormemente y se puede prolongar la vida útil.
punto de prueba hidráulico acoplamiento de prueba hidráulica ACOPLADOR DE PRUEBA DE PRESIÓN Acoplamientos Parker EMA Acoplamientos de puerto de prueba Conector de prueba hidráulica Kit de adaptador de prueba hidráulica Kit de prueba hidráulica Punto de prueba de presión de prueba accesorios hidráulicos Ensambles de prueba de mangueras Accesorios de punto de prueba Mangueras de punto de prueba Conexiones de manómetro de prueba Acoplamientos de prueba para comprobación de presión Portátil Instrumentos hidráulicos para prueba de presión Manguera para accesorios de alta presión Accesorios de extremo de manguera ACOPLAMIENTO DE PUNTO DE PRUEBA HIDRÁULICA Accesorios hidráulicos Fabricante de accesorios hidráulicos accesorios hidráulicos estándar conector de prueba hidráulica accesorios en T de prueba hidráulica punto de prueba JIC ajuste hidráulico catálogo de tings accesorios hidráulicos conexión de manómetro JIC punto de prueba de fluido hidráulico accesorios de Parker punto de conexión de roscas de prueba accesorios de puerto de prueba hidráulica acoplamiento hidráulico y manguera mini prensas hidráulicas válvulas de choque válvulas de presión punto de prueba de válvula de brida hidráulica de fluido conectores de fluido accesorios de desconexión rápida hidráulica