Blog
How to operate hydraulic test fittings safely?
How to operate hydraulic test fittings safely?
Hydraulic test fittings are essential components in hydraulic systems, widely utilized in fields such as construction machinery, industrial equipment, aerospace, automotive manufacturing, and oil and gas.
Their primary role is to measure and monitor system pressure, ensuring stable operation and safety. However, improper use or poor maintenance can lead to system failures and potentially severe safety incidents.
Therefore, mastering the safe operation guidelines for pressure measuring joints is crucial. This paper delves into the correct operation and maintenance practices for pressure measurement joints to ensure their safety and reliability in practical applications.
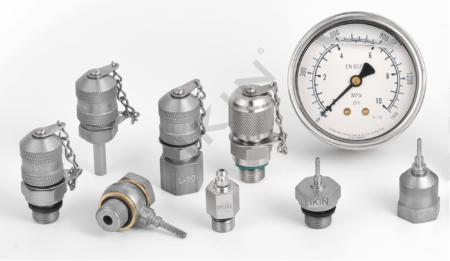
1. Basic structure and operation principle of pressure-measuring connectors
A pressure measuring fitting typically comprises a body, seals, and connecting components. Its function is to detect pressure fluctuations within a hydraulic system, delivering real-time data that allows operators to monitor and adjust the system’s performance accordingly. Hydraulic test fittings are engineered for optimal tightness and stability in high-pressure environments, effectively preventing fluid leaks and potential system failures.
2. Basic principles of safe operation
2.1 Knowledge of equipment
Before operating a pressure measuring fitting, it’s essential to thoroughly understand its structure, working principles, and operating instructions. Familiarize yourself with the equipment’s performance parameters, including maximum working pressure, temperature range, and suitable media. This knowledge ensures that the equipment operates within its design limits, preventing any operational issues.
2.2 Wear appropriate protective equipment
Always utilize suitable protective equipment, such as gloves, goggles, and protective clothing, when operating pressure-measuring fittings. This gear is crucial for preventing injuries from high-pressure fluid leaks and ensures operator safety.
2.3 Checking the status of equipment
Before operation, thoroughly inspect the condition of the pressure measuring fitting to ensure there are no signs of damage or wear. Pay special attention to the seals, which must be intact to prevent leaks. Additionally, check the connecting parts for tightness to ensure a secure and reliable connection.
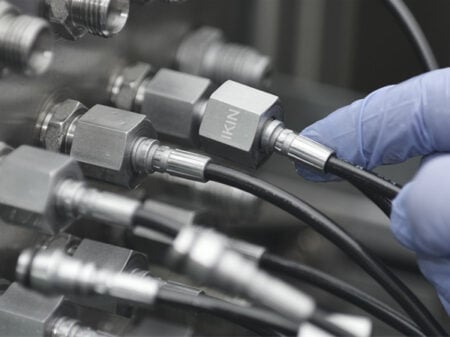
3. Safe practices for installation and dismantling
3.1 Installation of hydraulic test fittings
-Selecting an Appropriate Location: Choose a suitable spot within the hydraulic system for installation to ensure the measurement point accurately reflects the system’s operating pressure.
– Cleaning Connecting Parts: Prior to installation, thoroughly clean both the pressure measuring fitting and the system’s connecting parts to remove any impurities or contaminants that might compromise the seal.
– Using the Right Tools: Employ the correct tools for installation and avoid applying excessive force to prevent damage to the fittings or connecting components. Adhere to the equipment manufacturer’s installation instructions to ensure proper setup.
3.2 Disassembly of hydraulic test fittings
– Pressure Relief: Before removing the pressure measurement fitting, ensure that the system is fully depressurized to eliminate any residual pressure and prevent injuries from fluid discharge.
– Equipment Protection: During disassembly, carefully protect the pressure measurement fittings and connecting parts from impacts and damage. After removal, store the connectors properly to prevent contamination and damage.
4. Safety precautions in operation
Monitoring System Pressure: During operation, continuously monitor the system pressure in real-time to ensure it remains within a safe range. Avoid overpressure conditions to prevent damage to the pressure measuring fitting and the hydraulic system.
Avoiding Sudden Pressure Changes: Prevent sudden pressure changes during operation to avoid shocks to the pressure measuring fitting and the hydraulic system. Adjust the system pressure gradually to ensure a smooth transition.
Compliance with Operating Procedures: Adhere strictly to the operating procedures and avoid unauthorized actions. If any abnormal conditions arise during operation, stop immediately, identify the cause, and address it to ensure system safety.
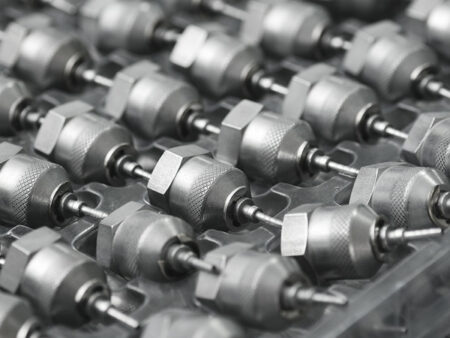
5. Safe practices for maintenance and upkeep
5.1 Regular inspection and maintenance
– Inspection of seals: Regularly inspect the seals of the pressure measuring joints, and replace them in time if they are found to be aged or damaged. Select high-performance sealing materials to improve the sealing effect and service life.
– Cleaning the equipment: Clean the pressure measurement fitting regularly to prevent dust, impurities and corrosive substances from entering the inside of the fitting. Use appropriate cleaning agents and tools to ensure that both the inside and outside of the fitting are kept clean.
5.2 Lubrication and fastening
– Lubrication: For pressure-measuring fittings that require frequent operation, lubricate regularly to reduce wear and operating resistance. Select a suitable lubricant and avoid lubricants that are harmful to the sealing material.
– TIGHTENING: Periodically check the tightness of the joints to ensure that they are securely connected. For loose joints, tighten them with appropriate tools to prevent leakage and system instability.
5.3 RAM
– Maintenance records: Detailed records of each maintenance and servicing, including inspection items, problems found and treatment measures. Through the maintenance records, the history of equipment use can be traced, potential problems can be found and dealt with in a timely manner.
– File management: Establish a file management system for the pressure measuring joints, keep the technical data, operation instructions and maintenance records of the equipment, etc., so as to facilitate the daily management and maintenance.
6. Emergency response measures
Regular Inspection and Maintenance:
- Seal Inspection: Regularly examine the seals of pressure measuring joints and promptly replace any that are aged or damaged. Use high-performance sealing materials to enhance sealing effectiveness and extend service life.
- Equipment Cleaning: Routinely clean the pressure measuring fitting to prevent dust, impurities, and corrosive substances from entering. Use appropriate cleaning agents and tools to ensure both the interior and exterior of the fitting remain clean.
Lubrication and Fastening:
- Lubrication: For pressure measuring fittings that require frequent operation, lubricate regularly to minimize wear and operational resistance. Choose a suitable lubricant and avoid those that could harm the sealing material.
- Tightening: Periodically check the tightness of the joints to ensure secure connections. Use appropriate tools to tighten any loose joints, preventing leaks and system instability.
Record and Maintenance (RAM):
- Maintenance Records: Keep detailed records of each maintenance session, including inspection items, identified issues, and corrective actions taken. These records help trace the equipment’s usage history and identify potential problems early.
- File Management: Establish a file management system for pressure measuring joints, maintaining technical data, operation instructions, and maintenance records. This system facilitates daily management and maintenance activities.
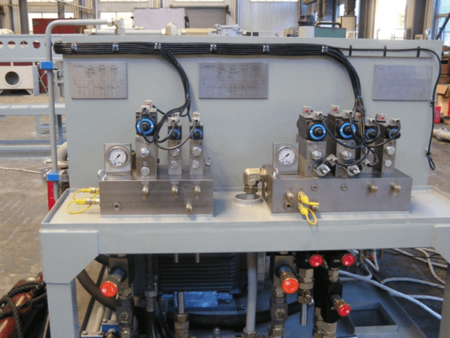
7. Case studies
Case 1: Safe Operation of hydraulic test fittings in a Chemical Plant
In a chemical plant, numerous hydraulic test fittings were utilized within the hydraulic system. An incident occurred when an operator failed to perform the necessary pressure relief operation, resulting in a high-pressure liquid spray during disassembly and causing injury.
Following an investigation, the chemical plant developed detailed operating procedures and provided comprehensive training to the operators. These measures significantly improved the operational safety of the pressure measuring joints and prevented similar incidents from occurring.
Case 2: Maintenance of pressure-measuring fittings at a manufacturing company
A manufacturing company employed high-pressure hydraulic test fittings in its hydraulic press equipment. Due to neglect in timely maintenance and repair, the seals of the pressure-measuring fittings deteriorated and became damaged, leading to system leaks.
To address the issue, the company took the following actions: replaced all deteriorated seals with high-performance sealing materials; regularly inspected and cleaned the pressure-measuring fittings to ensure optimal condition; and trained operators to enhance their maintenance and operation skills. These measures effectively resolved the leakage problem and improved both the operational efficiency and safety of the equipment.
Hydraulic test fittings are crucial components in hydraulic systems, and their safe operation and maintenance are directly linked to the stability and safety of the system. By understanding the equipment’s structure, wearing appropriate protective gear, checking the equipment’s condition, installing and removing it correctly, monitoring system pressure, avoiding sudden pressure changes, adhering to operating procedures, conducting regular inspections and maintenance, maintaining thorough records and files, and implementing emergency response measures, you can ensure the safety and reliability of pressure-testing fittings in practical applications.
Real-world case studies demonstrate that following scientific operation and maintenance protocols not only enhances the service life and performance of pressure measuring joints but also effectively prevents safety incidents. Therefore, attention to the safe operation specifications of pressure measuring joints is essential for ensuring the stable operation of hydraulic systems and the safety of operators.
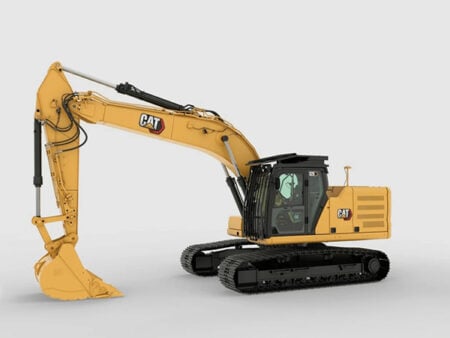
Common problems and solutions during pressure testing
Common problems and solutions during pressure testing
Pressure testing is essential for ensuring the proper operation and safety of hydraulic systems and equipment. It helps detect weaknesses, verify design pressures, and identify potential leaks within the system.
However, various issues may arise during pressure testing. If these problems are not addressed promptly and effectively, they can affect test results and even jeopardize system safety.
This article provides an in-depth analysis of common problems encountered during pressure testing and offers practical solutions. We will also discuss these issues through real-world examples. By offering detailed analysis and discussion, this article aims to provide practical guidance to ensure the stability and safety of hydraulic systems.
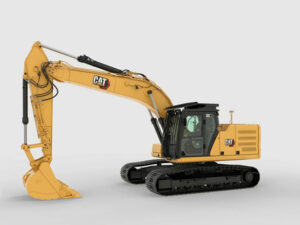
**1. Common problems during pressure testing**
**1.1 Leakage**
Leaks are among the most common issues encountered during pressure testing. They can occur at system connections, seals, or along piping. The causes of leaks are varied and may include deteriorated seals, improper installation, or defective materials.
**Solutions:**
Inspection and Replacement of Seals: Regularly inspect the condition of seals. Any seals that are deteriorated or damaged should be promptly replaced to prevent potential leakage.
Correct Installation: Ensure that all connections and piping are installed correctly, using appropriate methods and tools. Proper tightening and sealing of each component are essential to prevent leaks.
Material Selection: Choose materials that are corrosion-resistant and capable of withstanding high pressures. Selecting the right materials for the system’s working environment enhances the overall reliability of the system.
By implementing these solutions, the likelihood of leaks can be significantly reduced, ensuring the integrity and safety of the hydraulic system during pressure testing.
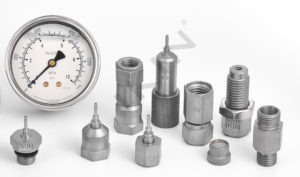
**1.2 Pressure fluctuations**
Pressure fluctuation refers to unstable pressure during testing, which can be caused by poor system design, unstable pressure sources, or equipment failure.
**Solutions:**
Optimized System Design: Ensure that the system is well-designed to prevent sudden changes in pressure. A robust design minimizes the likelihood of pressure fluctuations and significantly reduces associated problems.
Stable Pressure Source: Utilize a reliable pressure source that can provide continuous and stable pressure, ensuring the system operates normally and efficiently.
Equipment Maintenance: Conduct regular inspections and maintenance of pressure source equipment. Timely identification and resolution of potential issues are crucial to maintaining optimal working conditions and preventing pressure instability.
Implementing these solutions will help stabilize pressure during testing, ensuring the system’s reliability and accuracy.
**1.3 Inaccurate meter readings**
During pressure testing, inaccurate meter readings can compromise the accuracy of the test results. This issue may arise due to improper calibration of the gauge, incorrect mounting position, or gauge malfunction.
**Solutions:**
Periodic Calibration of Meters: Calibrate the meters at regular intervals to maintain accurate readings and ensure the reliability of the test data.
Select an Appropriate Mounting Location: Install the meter in a suitable location that minimizes vibration and interference, which can affect the accuracy of the readings.
Replacement of Malfunctioning Meters: Promptly replace any malfunctioning meters to maintain the accuracy and integrity of the test results.
By addressing these factors, the accuracy of meter readings can be ensured, thereby enhancing the reliability of the pressure test outcomes.
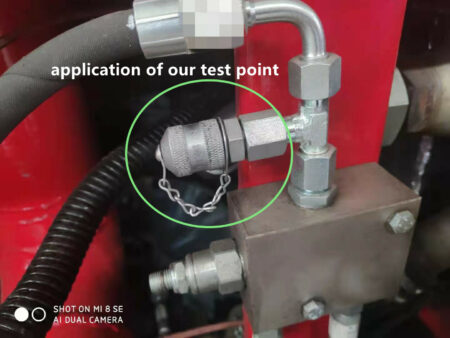
**1.4 Temperature effects**
Temperature variations can significantly impact pressure test results, particularly in extreme high or low-temperature environments. These fluctuations can cause materials to expand or contract, affecting the system’s sealing and pressure stability.
**Solutions:**
Selection of Temperature-Resistant Materials: Choose materials that are resistant to temperature changes based on the system’s working environment. This ensures that the system maintains stable performance under extreme temperature conditions.
Implement Temperature Compensation Mechanism: Introduce a temperature compensation mechanism during testing to minimize the impact of temperature fluctuations on the results. This helps ensure the accuracy and reliability of the pressure tests.
By addressing temperature-related issues, the stability and accuracy of pressure test results can be significantly improved.
**1.5 Connectivity issues**
Connection problems are a common challenge during pressure testing, often caused by mismatched fitting types, improper installation, or loose connections.
**Solutions:**
Selecting the Appropriate Fitting Type: Choose fittings that are compatible with the system design and suitable for the working environment to ensure proper matching with the rest of the system.
Correct Installation of Fittings: Follow standard methods and procedures for installing fittings to ensure a secure and reliable connection.
Regular Inspection and Tightening: Conduct periodic inspections of connection points and promptly tighten any loose parts to maintain a solid and dependable connection.
By addressing these connection issues, the reliability and effectiveness of pressure testing can be significantly enhanced.
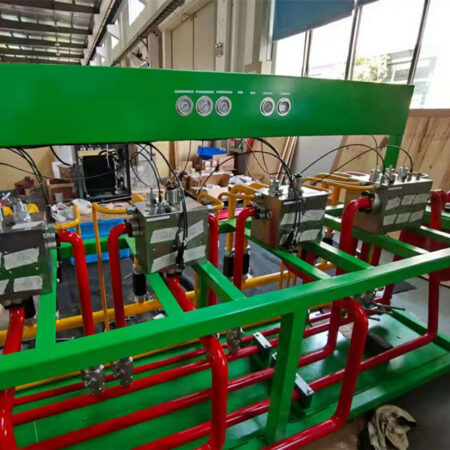
**2. Solutions for pressure testing**
**2.1 Development of a Detailed Test Plan**
Before conducting a pressure test, it is crucial to develop a comprehensive test plan that outlines the purpose, scope, methodology, steps, and expected outcomes. A detailed test plan helps clarify the objectives and ensures that the testing process is systematic and organized.
**2.2 Use of High-Quality Test Equipment**
Using high-quality test equipment is essential for obtaining accurate and reliable results. Select certified and calibrated equipment, and ensure that it is in optimal working condition before use.
**2.3 Training and Education**
Provide thorough training and education for operators to equip them with the necessary knowledge and skills for pressure testing. Training should cover the use of test equipment, execution of test procedures, and identification and resolution of common issues.
**2.4 Recording and Analysis**
During the pressure test, meticulously record all data and results, including pressure, temperature, time, and environmental conditions. Analyzing this data helps identify potential problems and implement timely corrective measures.
**2.5 Development of Contingency Plans**
Develop a comprehensive contingency plan to address any emergencies that may arise during the testing process. The plan should include procedures for handling leaks, equipment failures, and safety measures to ensure the testing process remains safe and efficient.
By implementing these strategies, the reliability and accuracy of pressure testing can be significantly enhanced, ensuring the safe and effective operation of hydraulic systems.
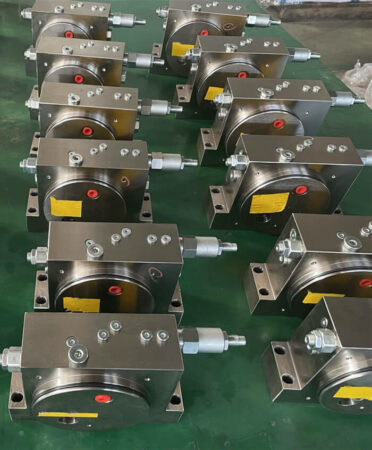
**3. Case Studies**
**Case 1: Pressure Testing in a Chemical Plant**
During the pressure testing of a new piping system at a chemical plant, multiple leaks were detected. Upon investigation, it was determined that the primary causes of the leaks were aging seals and improper installation. To address these issues, the chemical plant implemented the following measures:
– Replaced all deteriorated seals with corrosion-resistant, high-performance sealing materials to enhance durability and reliability.
– Conducted a thorough inspection and tightening of all connections to ensure that the installation complied with relevant codes and standards.
– Provided comprehensive training to operators to enhance their installation and operational skills.
By taking these steps, the chemical plant effectively resolved the leakage issues and ensured the safety and stability of the piping system.
**Case II: Pressure Testing in a Pharmaceutical Company**
During a pressure test of the hydraulic system at a pharmaceutical company, significant pressure fluctuations were detected. Analysis revealed that these fluctuations were caused by an unstable pressure source and poor system design. To address these issues, the pharmaceutical company implemented the following measures:
– Replaced the existing pressure source with more stable equipment to ensure a continuous and stable pressure supply.
– Redesigned the hydraulic system, optimizing the piping layout and connections to enhance overall system stability.
– Introduced an automated control system to monitor and regulate pressure in real-time, ensuring consistent system pressure.
By implementing these measures, the pharmaceutical company successfully resolved the issue of pressure fluctuations, significantly improving the operational efficiency and stability of the hydraulic system.
**Case IV: Pressure Testing at an Aerospace Company**
During pressure testing of an aircraft hydraulic system at an aerospace company, significant effects of temperature variations on the test results were observed. Analysis determined that these temperature changes caused material expansion and contraction, which impacted the system’s sealing and pressure stability. To address this issue, the aerospace company implemented the following measures:
– Selected temperature-resistant materials suitable for both high and low-temperature environments to ensure stable performance despite temperature fluctuations.
– Introduced a temperature compensation mechanism during the testing process to adjust system parameters in real-time, ensuring the accuracy of the test results.
– Controlled the test environment to minimize the impact of temperature variations on the testing process.
By adopting these measures, the aerospace company successfully mitigated the issues caused by temperature variations, significantly enhancing the accuracy and reliability of the pressure tests.
**Case V: Pressure Testing in a Shipping Company**
During a pressure test of a ship’s hydraulic system at a shipping company, issues were identified at multiple joints. Inspection revealed that these problems were due to mismatched joint types and improper installation. To resolve these issues, the shipping company implemented the following measures:
– Selected appropriate fittings that were compatible with the system, ensuring they matched the rest of the hydraulic components.
– Reinstalled the connectors following correct methods and procedures to guarantee a secure and reliable connection.
– Conducted thorough inspections and tightened all connections to ensure system stability and safety.
By taking these steps, the shipping company successfully addressed the connection issues, ensuring the normal operation and reliability of the ship’s hydraulic system.
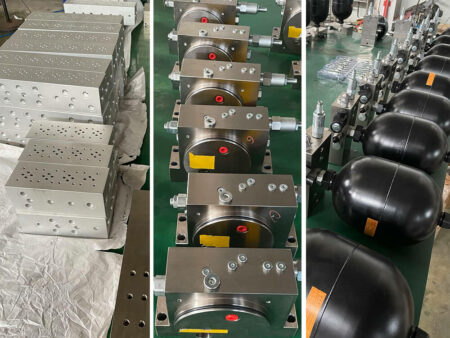
Pressure testing is a vital procedure for ensuring the proper functioning and safety of hydraulic systems and equipment. During testing, issues such as leaks, pressure fluctuations, inaccurate gauge readings, temperature effects, and connection problems can arise. These challenges can be effectively managed through the implementation of detailed test plans, the use of high-quality testing equipment, comprehensive operator training, meticulous recording and analysis of test data, and robust contingency plans. These measures ensure the accuracy and reliability of pressure tests.
Analyzing real-world cases demonstrates that scientific pressure testing methods and strategies not only address issues encountered during testing but also enhance the operational efficiency and safety of hydraulic systems. Therefore, focusing on the identification and resolution of problems during the pressure testing process is crucial for maintaining the stable operation of hydraulic systems.
Hydraulic Pressure Fittings Applied in Various Industries
Hydraulic Pressure Fittings Applied in Various Industries
Pressure measuring fittings are essential hydraulic components. They monitor pressure in hydraulic systems to ensure safety and stability. These fittings are used in many industries, including construction, industrial equipment, aerospace, automotive manufacturing, and oil & gas. Each industry has different performance requirements.
The performance requirements for pressure measuring fittings differ across industries. Specific examples demonstrate the practical importance of these fittings.
In this article, we will explore how pressure-measuring fittings are used across various industries. We’ll analyze their key roles and impacts through specific case studies.
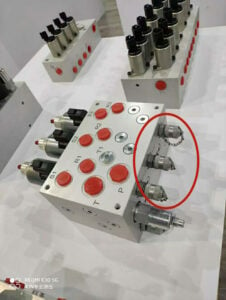
1. In the field of construction machinery
In the construction machinery industry, pressure measuring fittings are indispensable components. Equipment such as excavators, bulldozers, and loaders must endure harsh environments for extended periods, demanding highly reliable hydraulic systems.
Pressure measuring fittings play a critical role by continuously monitoring hydraulic system pressure in real time. This real-time monitoring ensures that the equipment operates within the optimal pressure range, thereby enhancing reliability, preventing system failures, and maintaining peak performance and safety.
Excavators, bulldozers, loaders, and similar equipment often operate in harsh environments for prolonged periods. This demanding usage necessitates exceptional reliability in their hydraulic systems. To achieve this, pressure measuring fittings are employed to monitor the hydraulic system’s pressure in real time. These fittings ensure that the equipment operates within the optimal pressure range, thereby preventing potential system failures and maintaining peak performance and safety standards.
**Case Study: Excavator Application**
A leading construction machinery company incorporates high-performance pressure measuring fittings in the hydraulic systems of its excavators. Given that excavators are required to function in high-intensity work environments, the pressure resistance and durability of these fittings are crucial.
These pressure measuring fittings are crafted from the latest high-strength alloy materials and utilize advanced sealing technology. This design enables them to perform reliably for extended periods under high-pressure and high-temperature conditions, effectively preventing leaks and system failures.
Through regular maintenance and servicing, the company’s excavators have significantly enhanced their operational efficiency and safety. The robust construction of these fittings ensures that the hydraulic systems remain reliable, thereby optimizing performance and reducing downtime. This meticulous approach to equipment maintenance has contributed to the company’s reputation for producing durable and efficient machinery capable of withstanding the rigors of demanding construction environments.
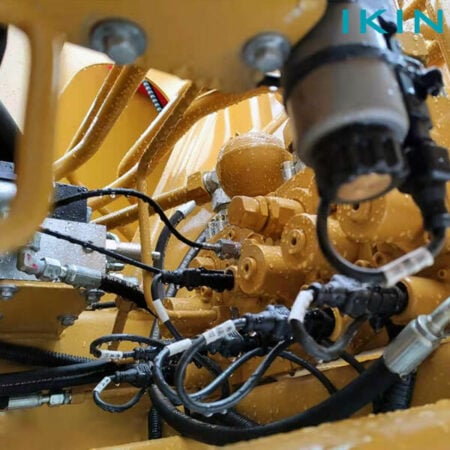
2. **Industrial Equipment Sector**
Industrial equipment such as hydraulic presses, die casting machines, and injection molding machines heavily rely on pressure measuring fittings. These fittings ensure the systems operate smoothly under high pressure and high temperature conditions. They provide accurate pressure data, enabling operators to adjust system parameters in a timely manner. This real-time data optimizes equipment performance and ensures an efficient, stable production process.
**Case Study: Hydraulic Press Application in a Manufacturing Company**
A manufacturing company has implemented new high-pressure gauge fittings in its hydraulic press equipment. Precise pressure control is essential for hydraulic presses during production, making the accuracy and stability of these fittings crucial.
By utilizing high-performance pressure measuring fittings, the company has notably enhanced the quality of its hydraulic products. This improvement has led to a significant reduction in scrap rates and an increase in production efficiency. The reliable performance of these fittings ensures that the hydraulic presses maintain consistent pressure control, thereby optimizing the overall manufacturing process and ensuring high-quality output.
3. **Automobile Manufacturing Sector**
In the automotive manufacturing sector, hydraulic systems play a crucial role in braking, steering, and suspension systems. Pressure measuring fittings are essential for real-time pressure monitoring in these systems, ensuring the vehicle’s safety performance under various operating conditions.
**Case Study: Braking System Application for an Automobile Manufacturer**
A renowned automobile manufacturer has integrated intelligent pressure measurement fittings into the braking system of its latest models. These advanced fittings combine a pressure sensor with data transmission capabilities, allowing real-time pressure data to be sent to the vehicle’s electronic control system. This continuous data stream enables the system to dynamically adjust brake pressure, significantly enhancing braking performance and vehicle safety.
The manufacturer has also conducted extensive testing and validation to ensure these pressure-measuring fittings maintain optimal performance across different climatic conditions and driving environments. This rigorous testing ensures that the fittings provide consistent, reliable data, contributing to a safer and more dependable driving experience for consumers. By incorporating these intelligent fittings, the automaker has improved the overall safety and reliability of its vehicles, reinforcing its commitment to quality and innovation in automotive design.
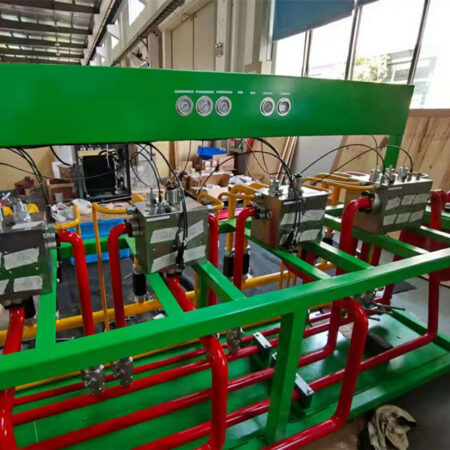
4. **Oil and Gas Sector**
In the oil and gas industry, hydraulic systems must function in complex environments with significant pressure fluctuations and exposure to corrosive media. Pressure measuring fittings are critical in these systems for monitoring the pressure of pipelines and equipment, preventing safety incidents such as leaks and explosions.
**Case Study: High-Pressure Pipeline Application in an Oilfield Project**
An oilfield project implemented high-pressure gauge fittings within its pipeline system. These fittings, constructed from high-strength alloys and featuring multi-layer seals, are engineered to withstand high-pressure and highly corrosive environments over extended periods. Regular inspections and maintenance have enabled the project team to avert numerous potential leakage incidents, ensuring safe production and environmental compliance.
Additionally, these pressure measuring fittings are equipped with remote monitoring technology, allowing operators to observe real-time pressure changes in the pipeline from a central control room. This capability ensures that any abnormalities are quickly addressed, significantly enhancing production efficiency and safety management in the oilfield. The integration of these advanced fittings not only ensures the structural integrity of the pipeline system but also supports the overall safety and efficiency of the oilfield operations.
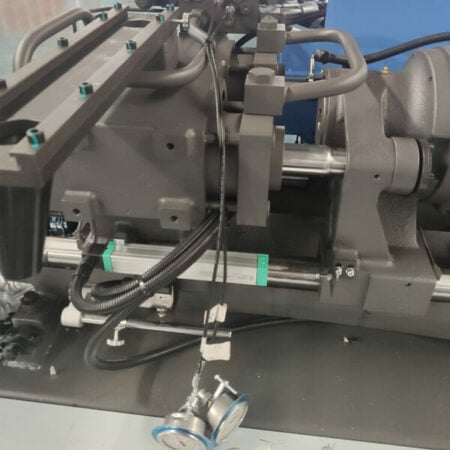
5. **Building Construction Sector**
In the building construction sector, large mechanical equipment such as tower cranes and concrete pump trucks rely on stable hydraulic systems for optimal performance. Pressure measuring fittings are crucial in these hydraulic systems to ensure stability and safety during construction activities5.
**Case Study: Tower Crane Application for a Construction Company**
A construction company has integrated high-precision pressure measurement fittings into the hydraulic systems of its tower cranes. During construction, tower cranes frequently lift heavy loads, demanding extremely stringent pressure requirements for their hydraulic systems. By employing high-performance pressure measuring fittings, the company has significantly enhanced construction efficiency and safety in large-scale projects.
These advanced pressure measuring fittings feature the latest self-locking design, ensuring that the fittings remain secure under high pressure and vibration. This innovation greatly improves the reliability and operational safety of construction equipment, enabling the tower cranes to function seamlessly in demanding environments. Consequently, the construction company has achieved higher productivity and reduced risks, reinforcing the importance of utilizing top-tier pressure measuring fittings in critical construction machinery.
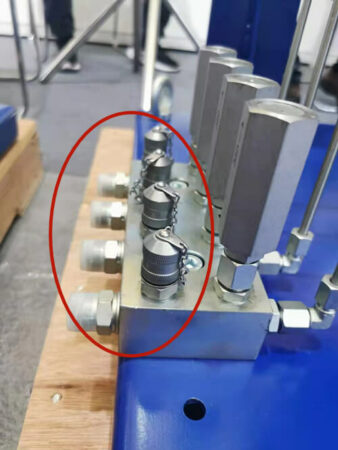
6. **Agricultural Machinery Sector**
In the agricultural machinery sector, equipment such as tractors, harvesters, and planters rely heavily on hydraulic systems. Pressure measuring fittings are essential for monitoring and controlling these hydraulic systems, ensuring the machines’ reliability and efficiency in various farming operations.
**Case Study: Harvester Application for an Agricultural Machinery Company**
An agricultural machinery company has implemented a new type of pressure measuring connector in the hydraulic system of its latest harvester model. These advanced fittings allow operators to monitor the hydraulic system’s status in real time, enabling timely adjustments and maintenance. As a result, the harvester performs reliably in field operations, reducing mechanical failures and enhancing harvesting efficiency.
These pressure measuring fittings feature an anti-fouling design that effectively prevents soil and impurities from entering the system. This design keeps the hydraulic system clean and functioning properly, ultimately improving the efficiency and service life of the agricultural machinery.
By adopting these innovative fittings, the company has ensured that its harvesters deliver optimal performance, contributing to more productive and efficient farming operations.
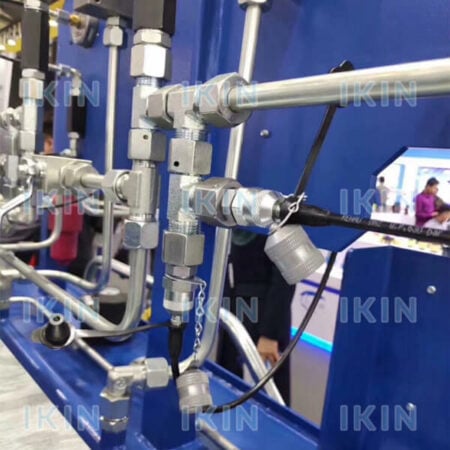
7. **Mining Sector**
The mining industry is highly demanding, and hydraulic systems are crucial for the performance of mining equipment. Pressure measuring fittings are essential for monitoring the hydraulic systems in this sector, ensuring stable operation under high loads, high pressures, and harsh environmental conditions.
**Case Study: Hydraulic Drilling Rig Application for a Mining Company**
A mining company has integrated high-performance pressure measuring couplings into the hydraulic systems of its drilling rigs. These couplings are made with special wear-resistant materials and a multi-layer sealing structure, allowing them to operate reliably for extended periods under high-pressure and high-vibration conditions.
Through regular maintenance and real-time monitoring, the company’s hydraulic drilling rigs perform exceptionally well in deep well drilling and ore extraction. This significantly boosts both efficiency and safety. The use of these advanced pressure measuring couplings not only extends the lifespan of the equipment but also reduces downtime caused by equipment failures, thereby improving overall productivity at the mine. By leveraging these robust fittings, the mining company ensures that its drilling operations are more efficient, reliable, and productive.
The case studies above clearly illustrate the application of pressure measuring fittings across various industrial fields, highlighting their critical role in ensuring the stable operation and safety of hydraulic systems. These fittings help enterprises improve productivity, reduce maintenance costs, and enhance safety.

As technology continues to advance, the performance and functionality of pressure measuring fittings are also improving. This progress will lead to their application and promotion in even more fields in the future, making significant contributions to industrial development and technological progress.
By integrating these advanced fittings, industries can look forward to more efficient, reliable, and safe hydraulic systems, driving further innovation and growth.
Pressure Measuring Fittings in Hydraulic Systems: Types, Applications, and Best Practices
Pressure Measuring Fittings in Hydraulic Systems: Types, Applications, and Best Practices
Hydraulic systems are essential in modern industry, playing a crucial role in fields such as construction machinery, industrial equipment, aerospace, and automotive manufacturing.
At the heart of these systems lies the pressure measuring fitting, which is critical for measuring and monitoring system pressure to ensure stability and safety.
In this comprehensive guide, we will explore the various types of pressure measuring fittings, their application scenarios, selection criteria, installation and maintenance procedures, and real-world case studies demonstrating their importance in hydraulic systems.
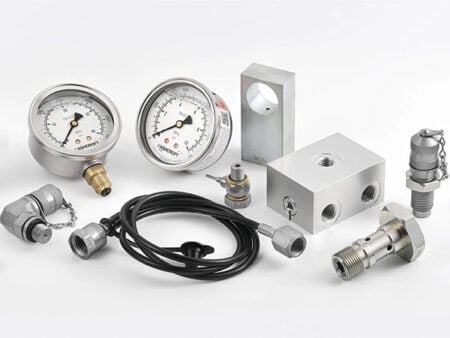
Pressure measuring fittings come in various designs tailored for specific applications, each with unique features:
1. Quick couplings
·Characteristics: Designed for rapid connection and disconnection.
·Applications: Used in hydraulic systems requiring frequent assembly and disassembly, enhancing efficiency through simple insertion and removal.
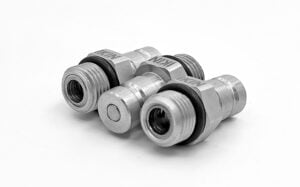
2. Threaded joints
·Characteristics: Secured by threaded connections, suitable for high-pressure environments.
·Applications: Common in systems needing robust connections that can withstand high pressure and vibration.
3. Push-in fittings
·Characteristics: Connect via a simple push-in operation.
·Applications: Ideal for low and medium pressure systems, though caution is needed in high-pressure environments.
4. Flanged joints
·Characteristics: Provide high-strength connections.
·Applications: Used in heavy machinery and high-pressure pipelines due to their strong connections and excellent seismic.
5. Welded joints
·Characteristics: Connected by welding, suitable for high-pressure and high-temperature conditions.
·Applications: Preferred in environments demanding high connection strength, despite more complex installation and maintenance.
When selecting a pressure measurement fitting, a number of factors need to be thoroughly evaluated to ensure optimum performance and long-lasting reliability in a particular application. The main factors to consider include the following:
1. Pressure range
According to the working pressure of the hydraulic system, select the coupling that can withstand the corresponding pressure. Over-pressurization can lead to damage to the couplings and even safety accidents.
When choosing, you need to carefully check the maximum working pressure of the hydraulic system and the rated pressure of the pressure measurement joints to ensure that the joints can withstand the working pressure of the system.
2. Temperature range
Hydraulic systems may operate in high or low temperature environments, requiring the selection of fittings with good temperature resistance.
Pressure gauge fittings made of different materials have different performance in different temperature ranges, and you need to choose the right fittings according to the operating temperature of the hydraulic system.
3. Media type
According to the medium used in the hydraulic system (such as oil, water, etc.) to select the appropriate joint material to prevent corrosion and media leakage.
Different media have different requirements for pressure measurement joint materials, such as oil-based hydraulic media suitable for the use of metal joints, while water-based hydraulic media may require the use of corrosion-resistant materials.
4. Connectivity
According to the design and installation requirements of the system to choose the appropriate connection, such as quick couplings, threaded fittings or push-in fittings. The selection needs to take into account the connection method and operating habits of the hydraulic system to ensure that the fitting is easy to install and use.
In order to ensure that the gauge fitting will operate consistently and efficiently in the hydraulic system for a long period of time, proper installation methods and a systematic maintenance program are essential. Below are some detailed recommendations:
1. Installation steps
– Ensure that the hydraulic system is fully pressurized before installation.
– Select the appropriate installation tool according to the type of fitting.
– Ensure that fittings are clean and free of foreign matter where they connect to the system.
– Install the fitting correctly according to the product instructions to ensure a good seal.
– Pressure test after installation to ensure that the joints are leak-free.
2. Maintenance methods
– Regularly check the sealing of the joints and replace the seals when leaks are detected.
– Clean fittings regularly to prevent dust and contaminants from entering the system.
– Regularly lubricate frequently used joints to ensure smooth operation.
– When used under high pressure or in harsh environments, periodically check the fittings for wear and replace damaged fittings in a timely manner.

In the hydraulic system, the pressure measuring fitting is not only widely used, but also plays a vital role. Through the following case studies of several practical applications, we can have a clearer understanding of the key role and significant results of the pressure measurement joints in various industries.
#Construction machinery
A major construction machinery company has introduced a new type of pressure measurement joint in its excavator hydraulic system. Made with high-precision sensors and durable materials, the connector provides excellent measurement accuracy and durability.
By using this pressure fitting, the company monitors the hydraulic system pressure in real time to ensure that the equipment operates within the optimal pressure range, improving efficiency and safety.
In addition, the corrosion and pressure resistance of the couplings significantly reduces maintenance costs, extends service life, and improves overall productivity.
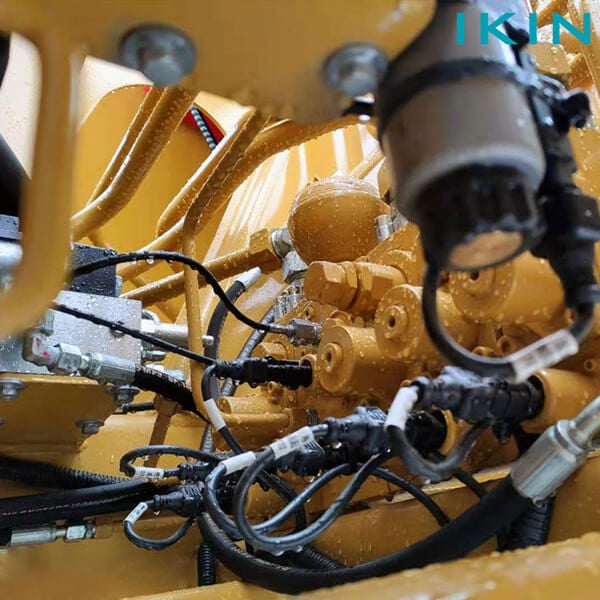
#Oil and gas
In the oil and gas industry, a large oilfield project has adopted a high-pressure and corrosion-resistant pressure measuring fitting to monitor the pressure of high-pressure pipelines. The application of this pressure fitting effectively prevents safety incidents such as pipeline leaks and explosions, and improves the safety and productivity of the project.
Installed at key pipeline nodes, these couplings transmit real-time pressure data to the monitoring center, helping operators adjust system parameters in a timely manner to prevent potential hazards.
#Industrial equipment
An industrial equipment manufacturing company has installed a variety of pressure measurement fittings in its hydraulic presses to monitor the pressure of the equipment’s hydraulic system.
Through accurate pressure monitoring and data analysis, the company identified and resolved potential problems in the hydraulic system and made timely adjustments, significantly improving the equipment’s operational stability and service life.
The real-time data provided by the pressure measurement couplings supports predictive maintenance, reduces equipment failure rates and downtime, and improves overall productivity.
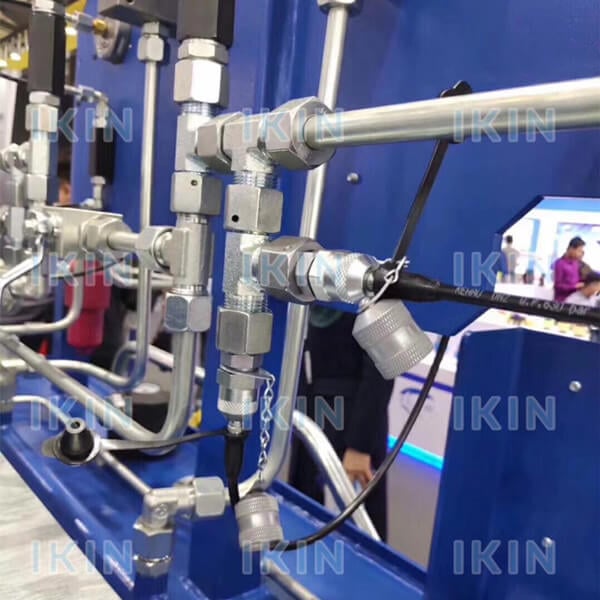
Pressure gauge fittings play a vital role in hydraulic systems, and their proper selection, installation and maintenance are the keys to ensuring the safe and stable operation of hydraulic systems. By understanding the different types of pressure measuring fittings and their application scenarios, and mastering the selection and maintenance methods, the operating efficiency and safety of the hydraulic system can be effectively enhanced.
We hope this article can help you better understand the basics and practical application scenarios of pressure measuring fittings, as well as grasp the key methods of selection and maintenance. We hope this information will be helpful to hydraulic system engineers and technicians in their work to enhance the performance and reliability of hydraulic systems. If you have any questions or need further guidance, please feel free to contact a professional.
Was ist der Unterschied zu hydraulischen Testkupplungen auf dem Markt?
Top 3 Hersteller in China
Lieferant für hydraulische Prüfarmaturen
SGS-zugelassen
Wie ist die Struktur des Druckprüfpunkts auf dem Markt?
Obwohl der Drucktestpunkt winzig und unnötig aussieht, ist das hydraulische Testsystem damit viel bequemer.
1. Funktion des Druckmesspunktes
Der Druckmesspunkt wird hauptsächlich verwendet, um den Druck des Flüssigkeitssystems zu messen, und im Inneren befindet sich ein selbstdichtendes Ventil.
Bei alleiniger Verwendung kann durch die Wirkung der Feder das Austreten des Systemmediums gestoppt werden.
Das selbstdichtende Ventil kann nach Anschluss an den Messschlauch mit Kausche oder Drucksensor geöffnet werden und die Systemdruckparameter können vom Manometer oder Tester angezeigt werden, der zur Systemdruckerkennung, Systemdiagnose und Fehlerdiagnose von Hochdruck- oder Niederdruck-Flüssigkeitssystem.
In einer speziellen Position können Prüfpunktadapter auch für die Medienentnahme im Hydrauliksystem, die Systemdruckentlastung und die Systementlüftung verwendet werden.
2. Klassifizierung von Druckprüfpunkten im Markt
Da der Druckmesspunktanschluss speziell für Druckmessungen und Flüssigkeitsproben mit hoher/niedriger Durchflussrate entwickelt wurde, wurde bei der Konstruktion der Druckbereich vollständig berücksichtigt.
Und je nach Einsatzbereich wurden Prüfpunkte unterschiedlicher Art und Stärke konzipiert, und auch diese Verbinder spielen bei der Arbeit eine unersetzliche Rolle.
Entsprechend der unterschiedlichen internen Struktur kann die Druckprüfpunktstruktur in Kugeldichtung, Kolbendichtung und Kegeldichtung unterteilt werden.
2.1 Aufbau der Kugeldichtung
Die Kugeldichtungs-Druckprüfkupplung besteht hauptsächlich aus einer Stahlkugel und einer Feder.
Der Schub wird durch die Federvorspannung erzeugt, so dass die Stahlkugel dichtend gegen die Passfläche des Ventilkörpers gedrückt wird.
Merkmale der Kugeldichtungsstruktur: eine einfache Struktur, eine Gleitringdichtung, nicht leicht zu altern und hat eine gute Stabilität.
Ein weiteres Merkmal: Die Bearbeitungsgenauigkeit der Kontaktfläche des Ventilkörpers muss hoch sein, die Stahlkugel und der Ventilkörper stehen in Linienkontakt und die Dichtwirkung ist durchschnittlich.
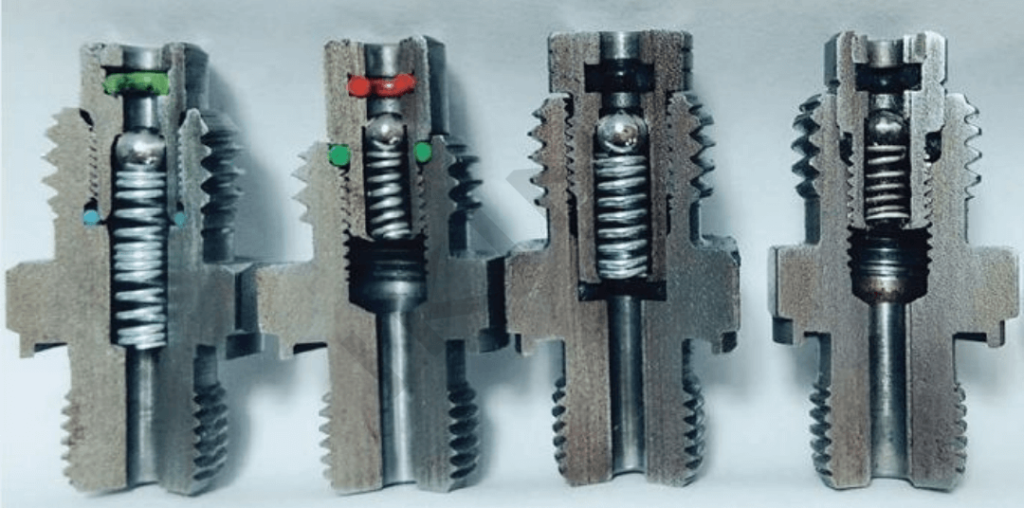
Innenaufbau Druckmessstelle mit Kugeldichtung
2.2 Aufbau der Kolbendichtung
Der Kolbendichtungs-Druckprüfpunktadapter besteht hauptsächlich aus einem Kolben, einem O-Ring und einer Feder. Der Dichtring befindet sich in der Kolbennut.
Festhalten am Dichtkegel (Radialdichtung) bzw. Planfläche (Axialdichtung) durch Federvorspannkraft.
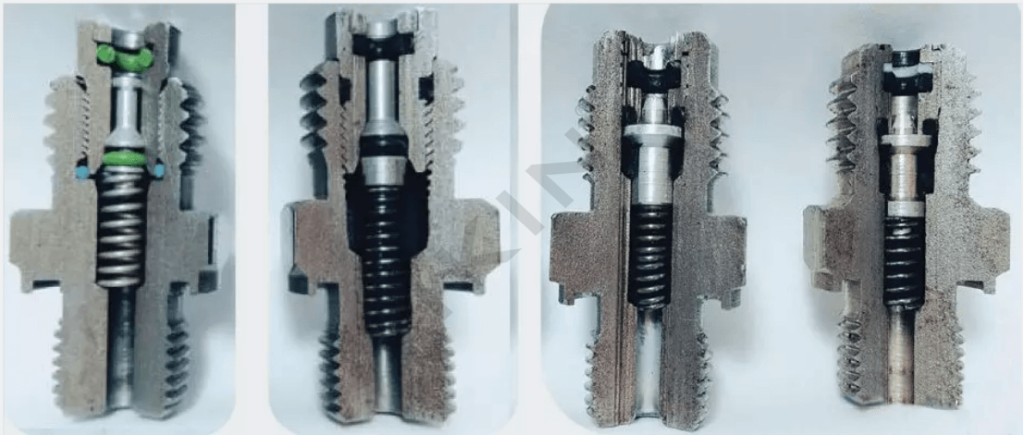
2.3 Konus-Dichtungsstruktur
Die Kegeldichtungs-Druckprüfkupplung besteht aus einem Kegelventileinsatz, einer Kegeldichtung und einer Feder.
Die konische Dichtung und der konische Ventilkern sind unter dem Vordruck der Feder fest mit der konischen Gegenfläche des Ventilkörpers verbunden.
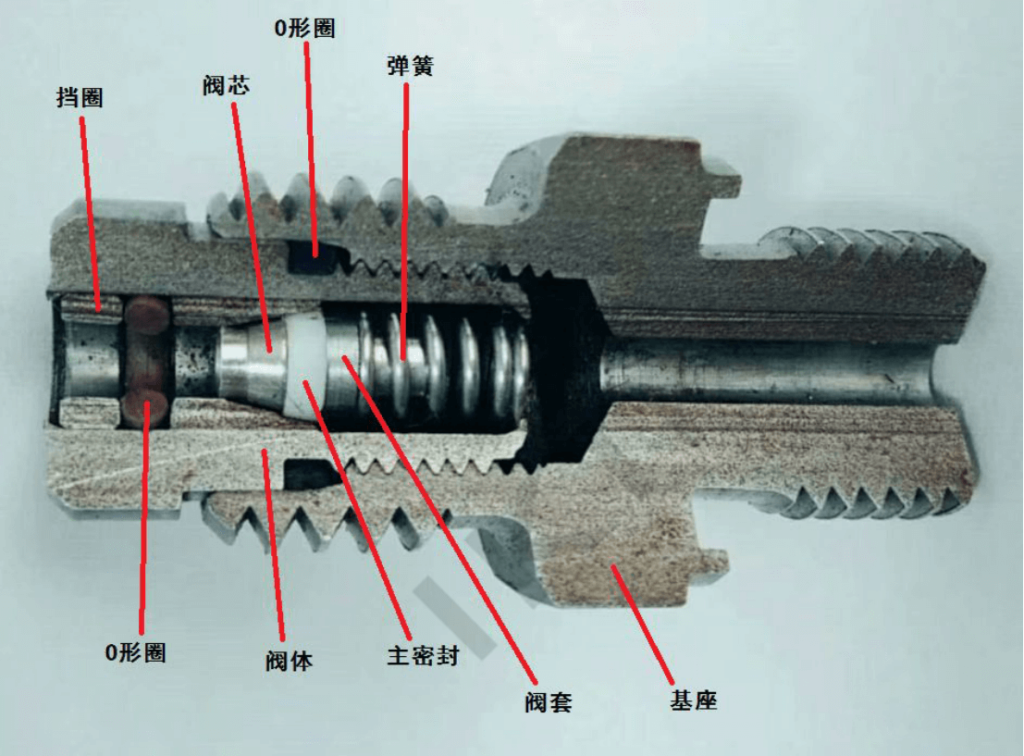
Interner Aufbau des kegeldichten Drucktests
Eigenschaften der Kegeldichtung: Der konische Ventilkern und die konische Dichtung arbeiten zusammen, die Dichtung ist Oberflächenkontakt, die Dichtwirkung ist besser und das Gas und die Flüssigkeit sind universell;
Die Feder ist im Ventilkörper integriert und lässt sich nicht leicht lösen; aber die Bearbeitungsgenauigkeit von Ventilkörper und Schieber ist relativ hoch.
Als gängige Ausrüstung in der Industrie sind Flüssigkeitsdruckprüfpunkte bekannt für ihren großen praktischen Bereich und ihre bequemen Anschlüsse und Probenahmen. Besonders wenn das Fluid unter hohem Druck und hoher Durchflussmenge verwendet wird, hat es viele Vorteile und viele Annehmlichkeiten.
Was sind also seine Vorteile:
Vorteil 1: Der Vorgang kann manuell unter Hochdruck abgeschlossen werden
Wenn die Flüssigkeit unter hohem Druck steht und unachtsam vorgegangen wird, kann der höhere Druck leicht dazu führen, dass Flüssigkeit austritt, was zu irreversiblen Prozessunfällen und sogar lebensbedrohlich führen kann.
Der Druckprüfschlauchverbinder berücksichtigt dies jedoch vollständig, sodass der Verbinder einfach mit beiden Händen unter hohem Druck gelöst und geschlossen werden kann.
Vorteil 2: Kleine Struktur
Da Probenahme- und Druckprüfungsorte oft nicht festgelegt sind, muss nach bestimmten Bedingungen und Anforderungen gearbeitet werden.
Daher bringt die kompakte Form großen Komfort in der Trage- und Bedientechnik.
Dann gibt es die Möglichkeit, sich einfach mit dem Messgerät zu verbinden.
Aufgrund seines einzigartigen Zwecks wurde die Verbindung mit dem Instrument vollständig im Design berücksichtigt, so dass die Bedienung einfach ist und die Verbindung fest ist.
3. Zusammenfassung
Der Testpunktadapter ist eine sehr kleine Komponente im Hydrauliksystem, spielt jedoch eine wichtige Rolle bei der Fehlersuche, Prüfung und Diagnose des Hydrauliksystems.
Durch das Manometer oder den Sensor können verschiedene Druckprüfungen ohne Demontage und Montage und ohne Leckage durchgeführt werden.
Eine sinnvolle Einstellung der Druckmesspunktanschlüsse im Hydrauliksystem bringt viel Komfort bei der Fehlersuche, Prüfung und Diagnose.
Um eine gute Anwendungswirkung zu gewährleisten, ist es in der Tat sehr wichtig, ein hochwertiges und zuverlässiges Produkt zu wählen.
Die aktuelle Bewertung des Druckmesspunktes ist sehr gut und das Produktdesign hervorragend.
Neben einer großen Durchflussleistung kann es auch strenge Qualitätsprüfungsstandards gewährleisten, damit die Produkte einen besseren Gebrauchswert haben.
Aus heutiger Sicht werden Druckprüfkupplungen vor allem auch flexibel auf verschiedene Fluidsysteme angewendet.
Die interne Verdrahtung der verschiedenen Fluidsysteme und die Größe der Anschlüsse sind jedoch unterschiedlich, sodass Sie die Durchflusskontrolle im Voraus durchführen müssen, bevor Sie den entsprechenden Druckmesspunkt kaufen.
Wenn die Größe nicht passt, ist es auch eine lästige Sache.
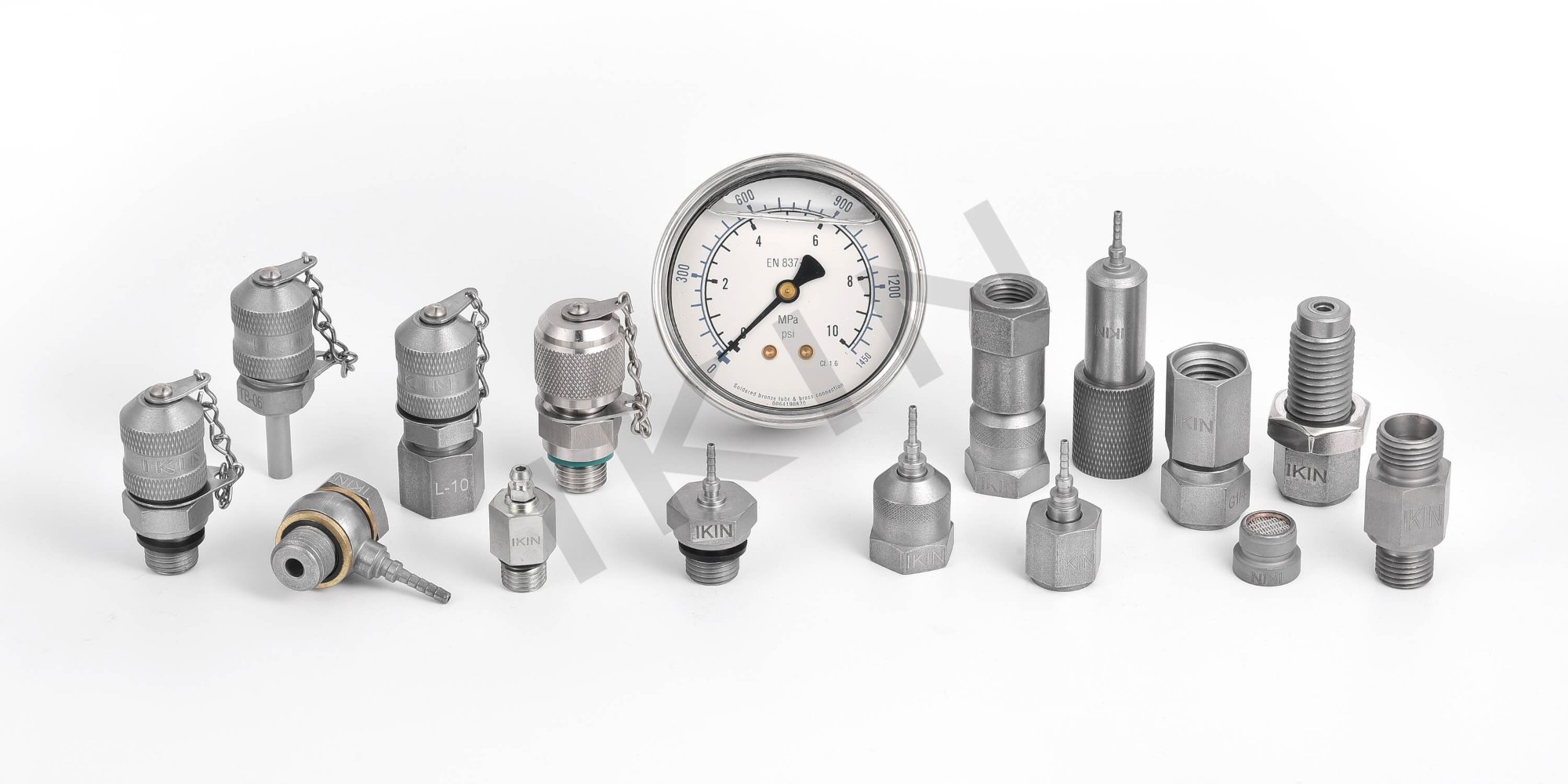
Ikin-Fluid
—— Top-3-Hersteller in China, spezialisiert auf hydraulische Testpunkte
Vorteile, die Sie finden können In Ikin
Fabrikpreis und niedriges moq
zuverlässige Qualität, Lieferant für Eaton, Hawee und so weiter
100% Leckageinspektion Bevor Sie fertig sind
3 Jahre Garantie
10 Werktage für Massenversand
passend zu anderen Ausstattungen wie Minimess, Stauff und so weiter
Konusdichtungsdesignstruktur, stabile und lange Lebensdauer
Holen Sie sich Ihre kostenlose Probe
in 2 Tagen
*Wir respektieren Ihre Vertraulichkeit und alle Informationen sind geschützt.
Ikin Fluid nahm an der Bauma China 2020 teil
Rückblick auf die Bauma China 2020 in Shanghai
Am 27. November ging die 4-tägige Bauma China Shanghai 2020 erfolgreich zu Ende.
Trotz der Auswirkungen der Covid-Pandemie sowie vier aufeinanderfolgenden Regentagen ist die Begeisterung der Baumaschinenbranche immer noch nicht aufzuhalten.
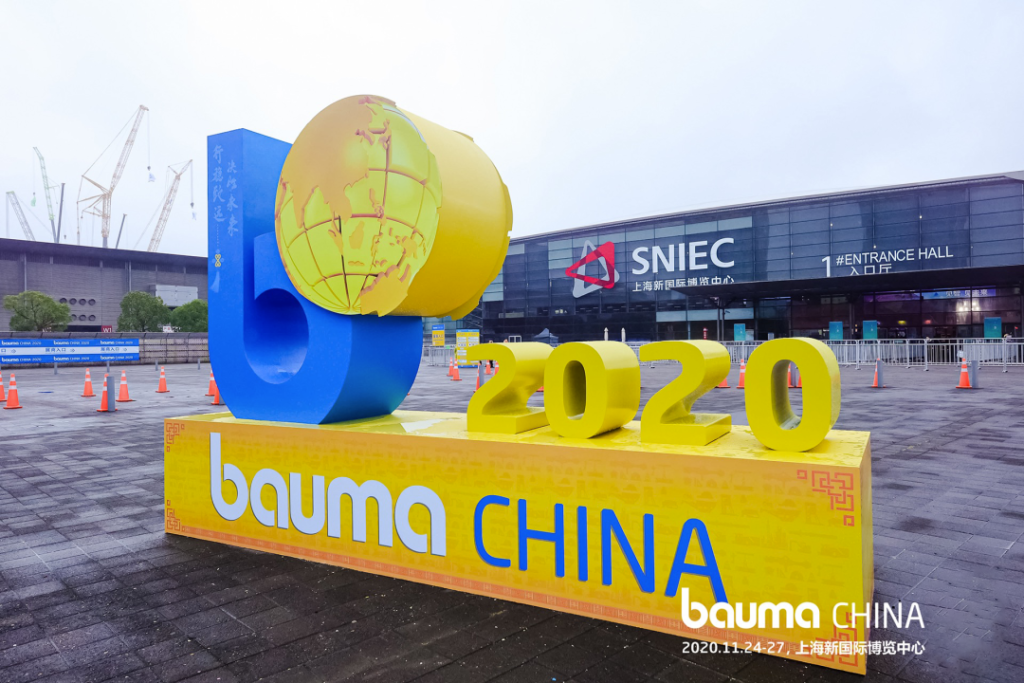
Die großen Baumaschinenhersteller zeigten ihr Können und die Kreativität der Veranstaltung dominierte das Publikum.
Angenehm überrascht zeigten sich die Aussteller mit vielen Lichtblicken.
Sanys "Online Bauma Show" wird zu einem neuen IP 23,5 Milliarden unterzeichnete Bestellungen!
Das Debüt des neuen Produkts zeugte von der Stärke des „Trinity Steel Corps“.
- Neuer Pumpenwagen der C10-Serie mit umfassenden Vorschriften und dem längsten Ausleger
Der neue Hundert-Tonnen-Großbagger SY1250H
46 Modelle der neuesten Geräte von Sany von 25 Tonnen bis 800 Tonnen Kränen
Unbemannte Straßenwalze ohne Kabine
Der weltweit erste Plug-in-Hybrid-Fertiger
Die weltweit ersten in Massenproduktion hergestellten Elektrobagger und Dutzende der modernsten Produkte, alle in voller Attacke, verblüffen das Publikum!
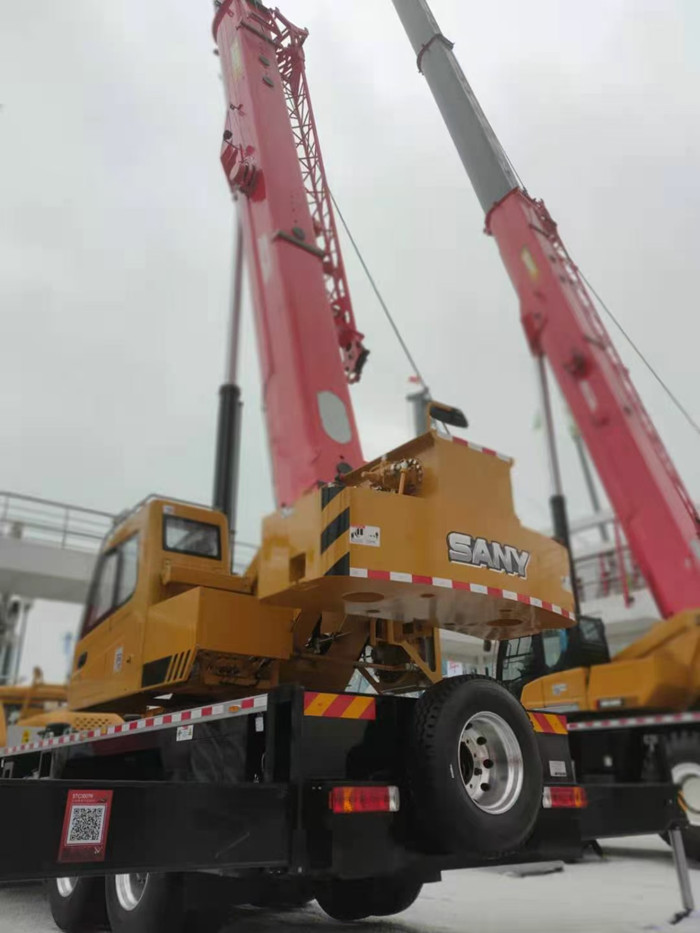
Und das Bild unten zeigt die Testkupplung von IKIN im Sany-Kranhydrauliksystem auf der Bauma.
Das Folgende ist das Live-Shooting am Stand von Sany. Es ist unser IKIN hydraulische Prüfkupplung benutzt auf Sany Kran.
We IKIN FLÜSSIGKEIT sind ernst bei der Konstruktion und Fertigung hydraulisch Prüfung Punkts.
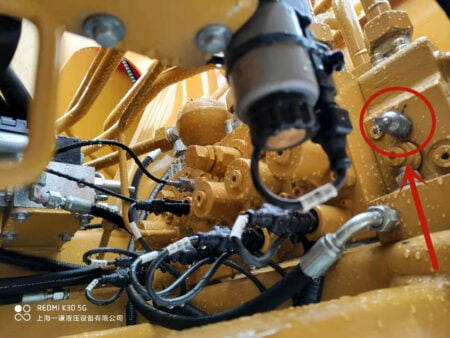
XCMG "Steel Corps" Konvergenz voller "chinesischer Weisheit"
Die XCMG Group hat das globale digitale Ersatzteilservice-Informationssystem (XCMG-Global Service System, kurz X-GSS) eingeführt.“
Fördern Sie die digitale, intelligente und unbemannte Transformation und Aufrüstung.
Auch hier wird der IKIN FLUID-Druckprüfpunkt in der XCMG-Stand.
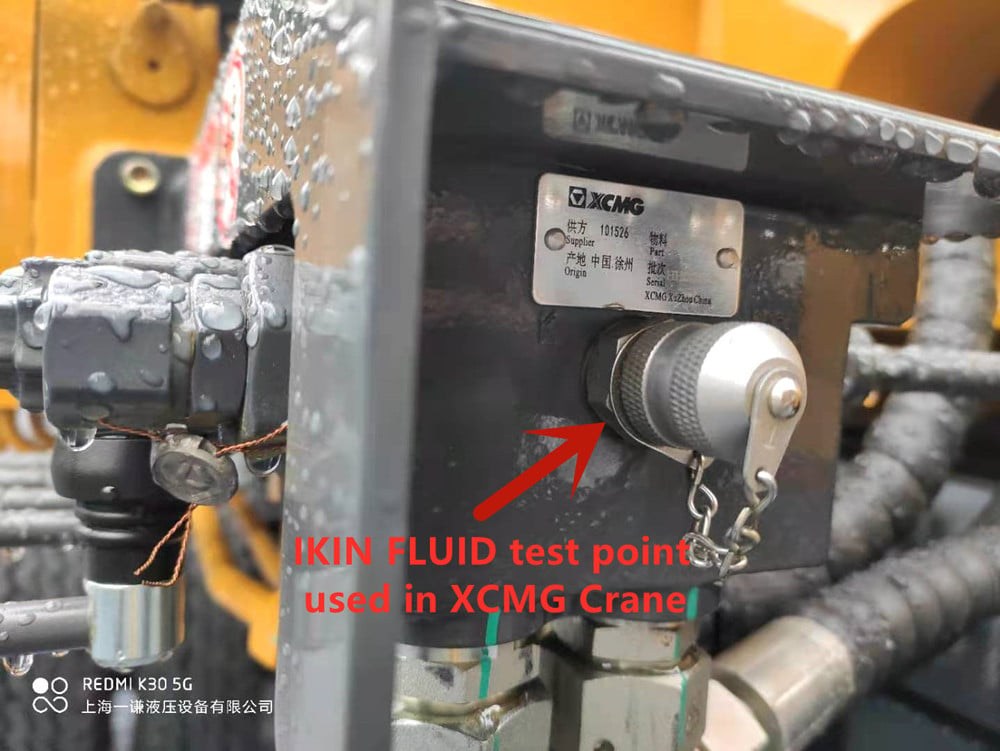
Zoomlion unterzeichnete am ersten Tag über 9 Milliarden RMB, das neue Produkt wurde weltweit am meisten erlebt.
- Zoomlions weltweit höchste selbstfahrende Hubarbeitsbühne mit geradem Arm ZT68J
- Zoomlion stellte viele Produkte der „schwarzen Technologie“ aus
- Neue High-Tech-Produkte von Zoomlion – alle demonstrieren starke F&E- und Innovationsfähigkeiten.
Das folgende Bild zeigt die Anwendung von IKIN-Druckprüfpunkten, aufgenommen am Stand von Zoomlion:
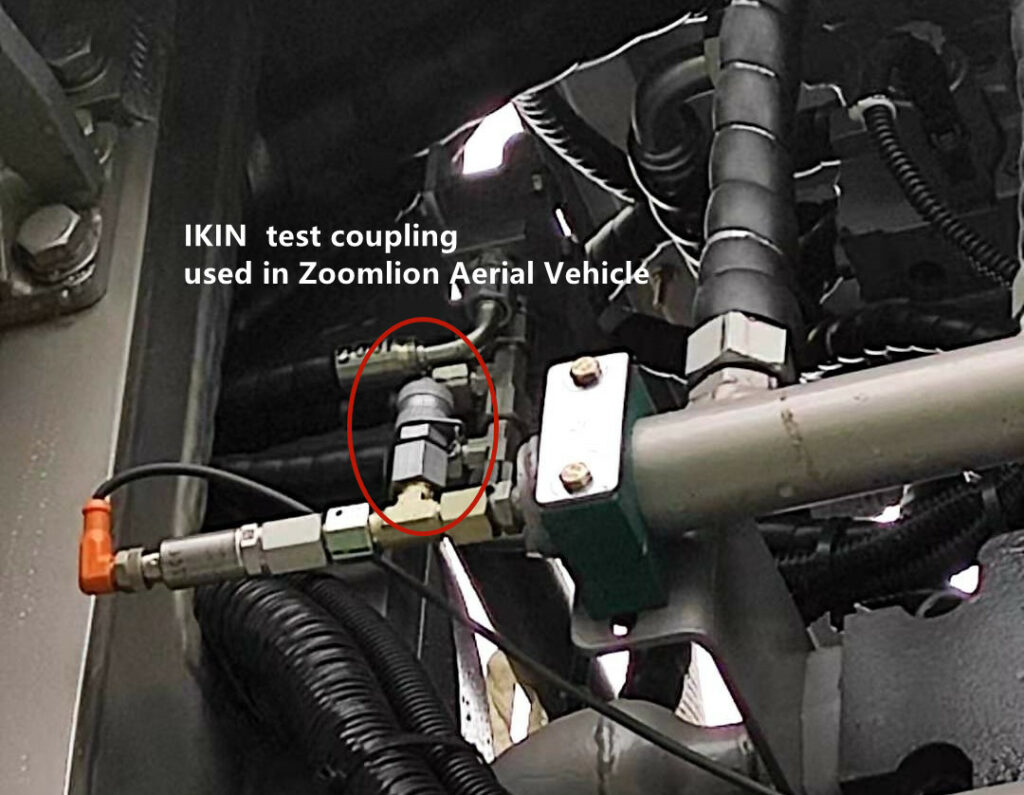
Darüber hinaus finden Sie unten die Druckprüfkupplung, die in vielen anderen Standausstellungen von Kunden verwendet wird.
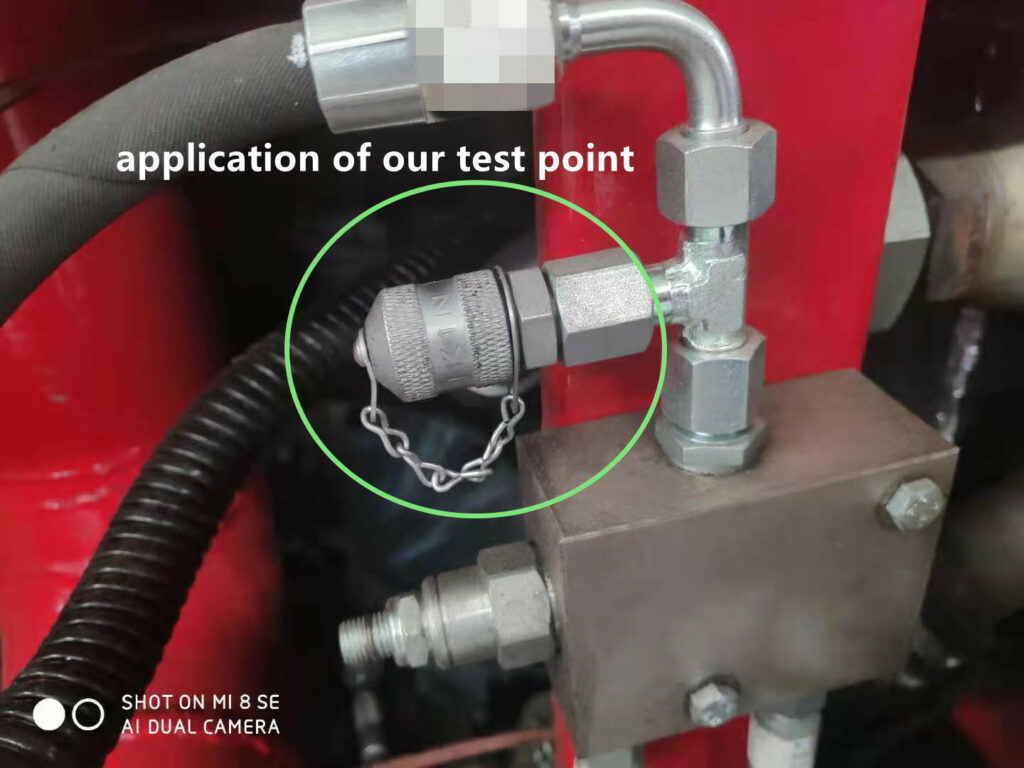
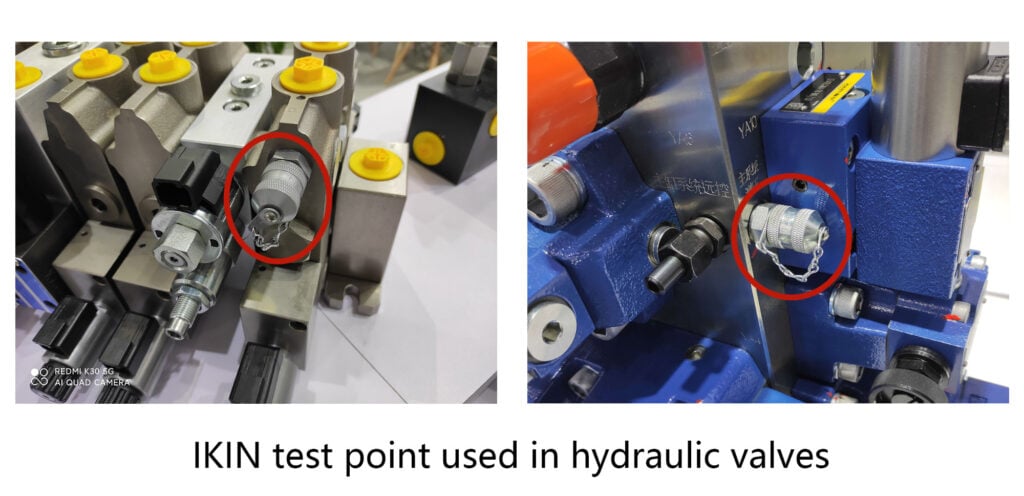
Betroffen von der Epidemie ist die Zahl der Kunden, die an der Show teilnehmen, als im 2018-Jahr gesunken, aber viele Kunden kommen immer noch zur Party.
Die von IKIN sorgfältig vorbereiteten professionellen Exponate mit Sinn für Wissenschaft und Technik haben die Aufmerksamkeit vieler Kunden auf sich gezogen.
Stand von IKIN
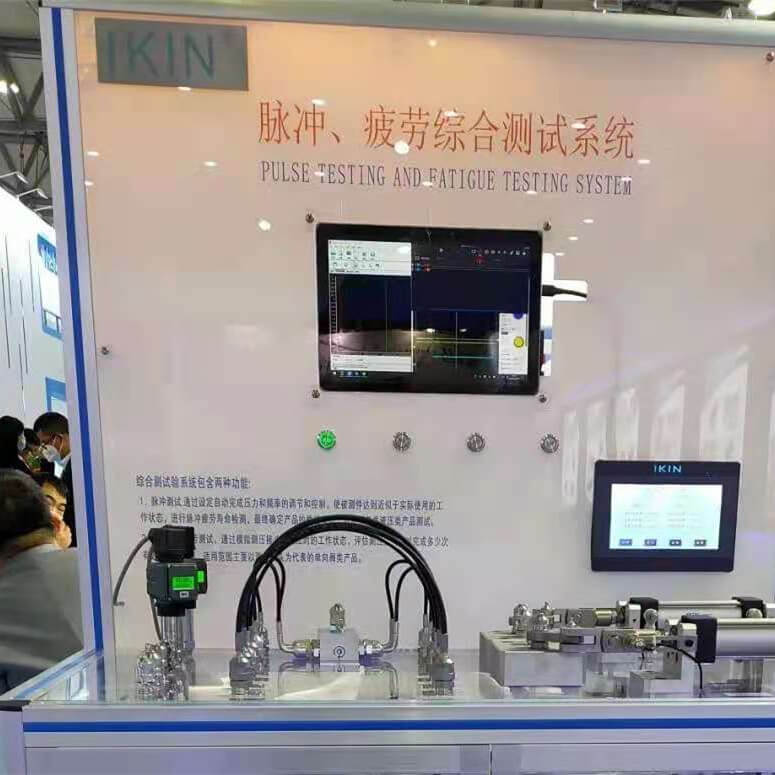
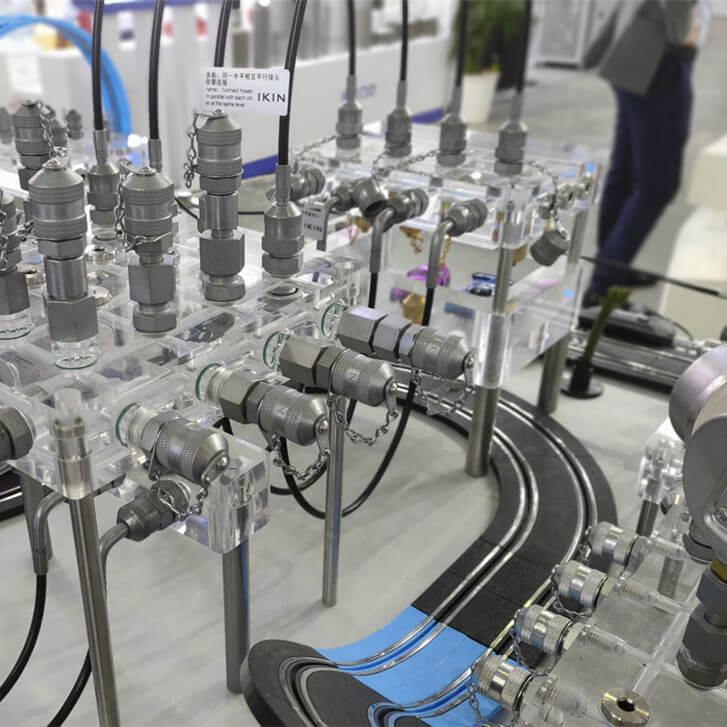
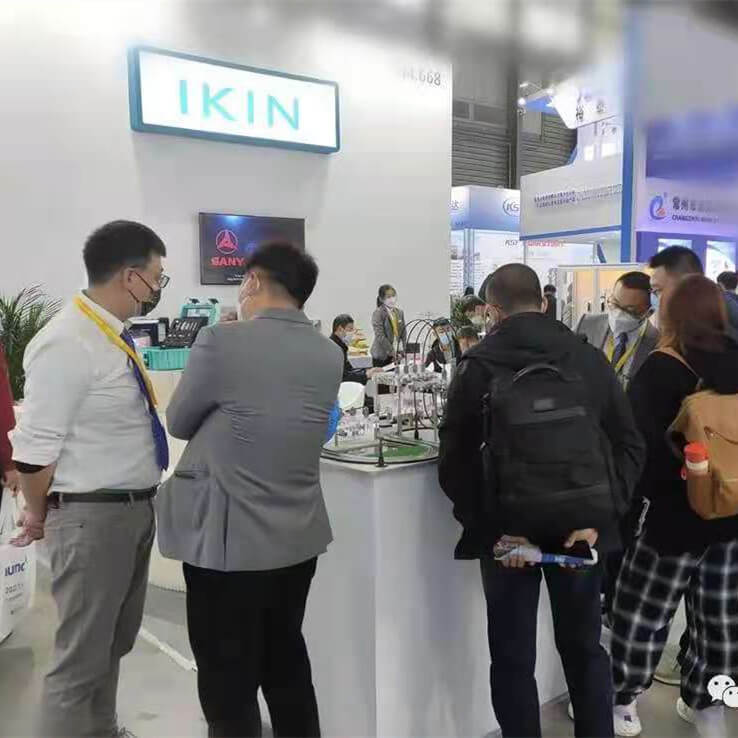
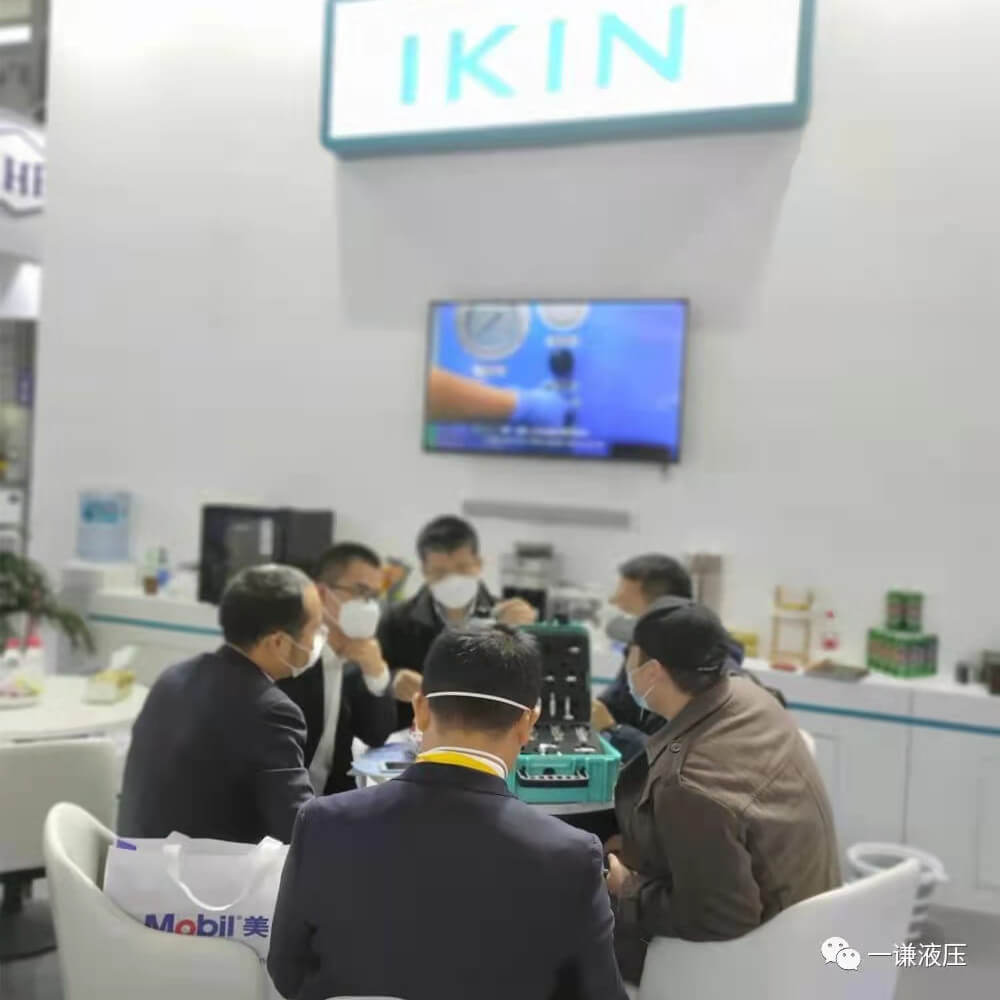
- China-Hersteller
- Lieferant für Sany Crane, XCMG Group, Zoomlion, GE usw
- spezialisiert auf hydraulische Prüfarmaturen
- zuverlässig, hohe Kostenleistung
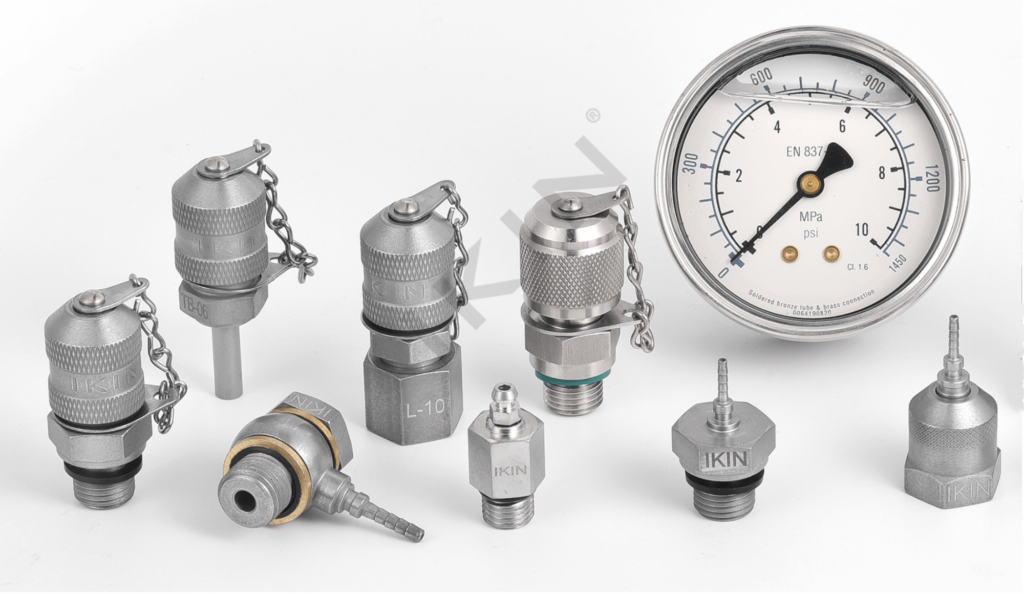
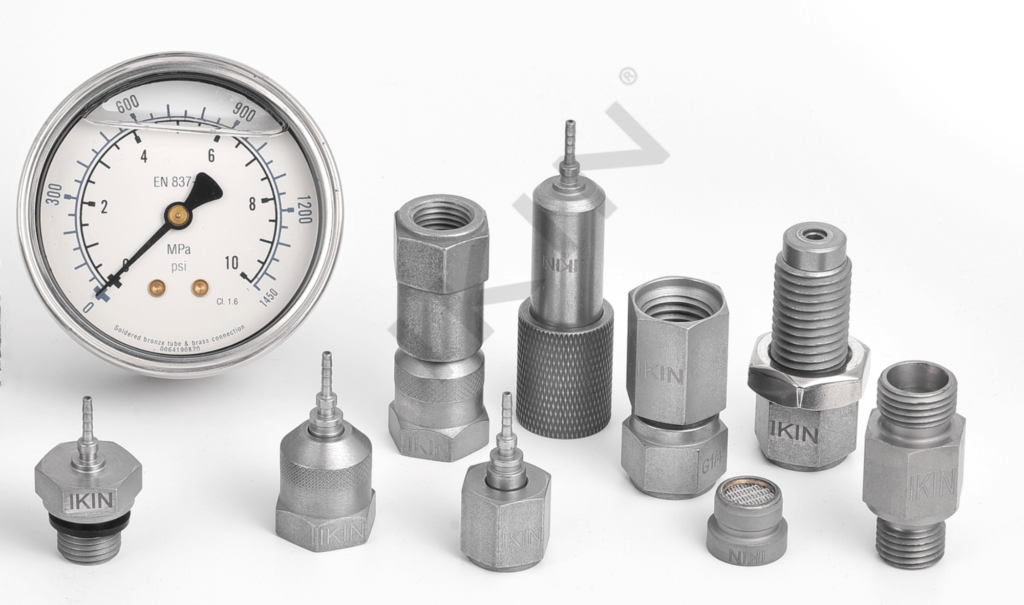
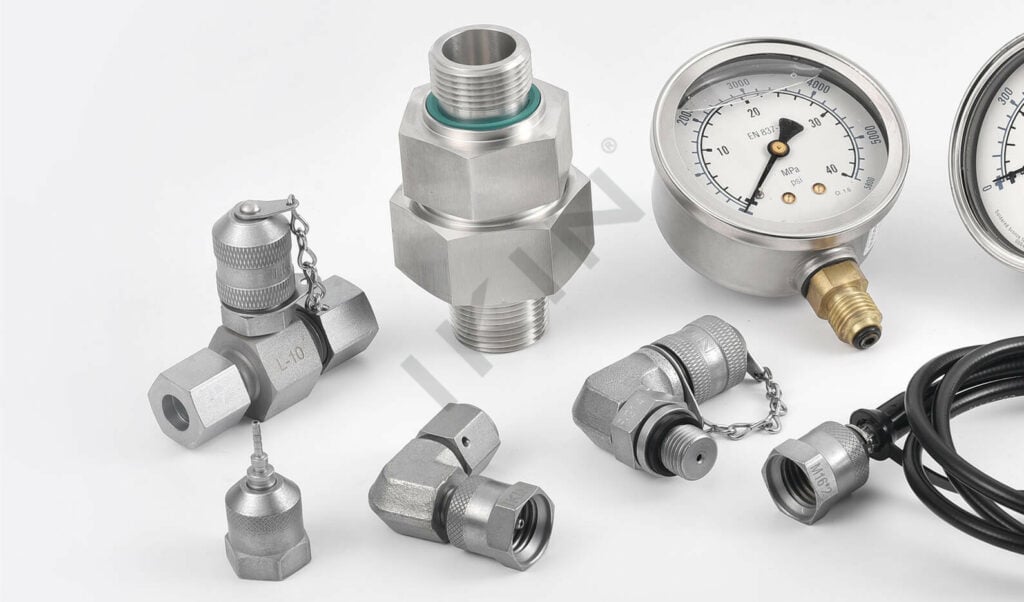
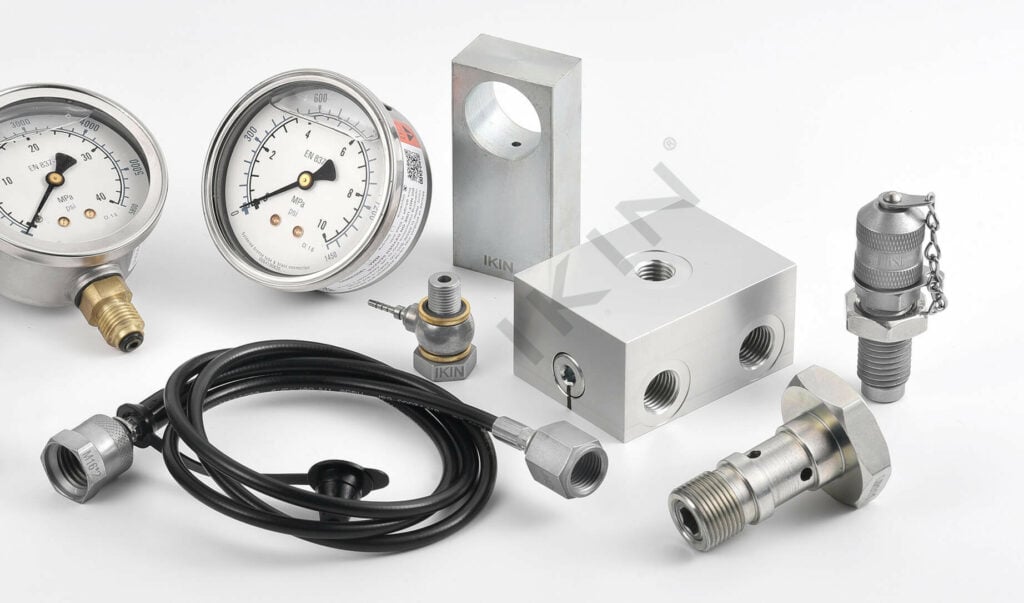
Welche Arten von Hydraulikschlaucharmaturen und Fehleranalysen gibt es?
Top 3 Hersteller in China
Lieferant für Hydraulikprüfpunktschlauch
SGS-zugelassen
Welche Arten von Hydraulikschlauchleitungen und -armaturen gibt es?
Mit der rasanten Entwicklung der chinesischen Baumaschinen ist die Zuverlässigkeit von Hydraulikschlauchleitungen zu einem der am meisten besorgniserregenden Themen in der Branche geworden.
Die Hydraulikschlauchanordnung ist ein Grundelement im Hydraulikgetriebesystem. Die Qualität der Schlauchleitung wirkt sich direkt auf die Leistung des Hydrauliksystems und des Hauptmotors aus. Ein Teil des Versagens der Schlauchleitung beruht auf der Struktur des Verbindungskerns.
Der Schlauchverbindungskern besteht hauptsächlich aus zwei Teilen. Einer ist die Verbindungsstruktur, die hauptsächlich auf SAE-Standards, ISO-Standards und KES-Standards basiert. Der andere Teil ist die Struktur des Crimpteils (Heckstruktur), die mit dem Außenmantel und den inneren und äußeren Gummischichten des Schlauchs abgestimmt ist, um eine zuverlässige Crimpverformung zu bilden, um die Leistung der Schlauchanordnung zu erfüllen.
Wenn die Struktur des Crimpteils des Verbindungskerns bei der Konstruktion verschiedener Schlauchtypen nicht zumutbar ist, treten weitgehend Probleme mit der Produktqualität auf.
Daher sind auch die Arten von (entworfenen) Verbindungskernen, die für Schläuche in verschiedenen Arbeitsumgebungen ausgewählt werden, unterschiedlich, und eine vernünftige Konstruktion kann das Auftreten von Fehlern vermeiden oder verringern.
1. Arten und Eigenschaften von Schlaucharmaturen
In der gesamten Schlauchmontageindustrie gibt es hauptsächlich zwei Arten zuverlässiger Verbindungen zwischen Schlauchverbindungen und Schläuchen: Schlauchverbindungen mit vollem Rückhalt und abnehmbare Schlauchverbindungen.
Die vollständige Crimpverbindung ist ein Vorgang, bei dem das achtteilige Crimpmodul der Crimpmaschine die Schlauchverbindung nach dem Zusammenbau des Verbindungskerns, des Schlauchs und des Außenmantels bis zu einem gewissen Grad gleichmäßig zusammendrückt, so dass die Schlauchverbindung und der Schlauch zu einem Ganzen werden .
Der abnehmbare Schlauchverbinder drückt den Schlauch durch den Verbinderkern mit dem äußeren Kegel und dem Verbinderkern, so dass sich der Schlauch nahe am inneren Kegel der Verbindungshülse befindet und eine Verbindung mit einer größeren Bindungskraft bildet.
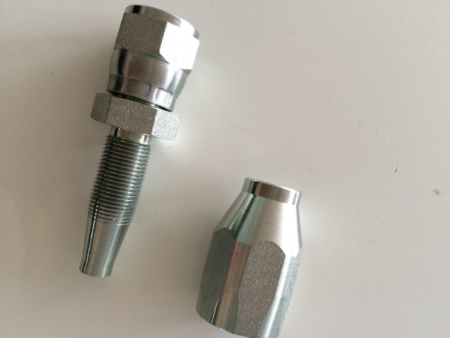
1.1 Form und Eigenschaften der Schlauchcrimpung
Die Art des Zurückhaltens des Schlauchs hängt hauptsächlich von der Art des Schlauchs (oder der Größe des inneren und äußeren Gummis) und der Druckumgebung der Schlauchanordnung ab.
Es ist hauptsächlich in drei Kategorien unterteilt: nicht schälendes Gummi-Crimpen, schälendes äußeres Gummi-Crimpen und inneres und äußeres Gummi-Peeling-Crimpen.
Die Eigenschaften jedes Typs sind:
(1) Nicht abblättern und crimpen: Der innere und äußere Gummi des Schlauchs muss nicht abgezogen werden, und das Produkt kann durch Crimpen nach der Installation des Schlauchs vervollständigt werden. Die Verarbeitungstechnologie ist einfach.
Diese Art des Crimpen wird häufig für geflochtene Stahldrahtschläuche mit relativ dünnen äußeren Gummischichten wie den Standards GB / T3683, EN853 und SAE verwendet.
(2) Abisolieren und Crimpen: Es ist erforderlich, die äußere Gummischicht des Schlauchs bis zu einer bestimmten Länge abzustreifen (die äußere Gummischicht ist dicker), um die Stahldrahtverstärkungsschicht besser mit der Zahnnut von in Kontakt zu bringen die Jacke.
Wenn der Mantel unter äußerer Kraft schrumpft und sich verformt, knickt er den Stahldraht fest ein, wodurch verhindert wird, dass sich die Verbindung herauszieht, wenn sie einem Aufprall unter hohem Druck ausgesetzt wird.
Diese Art des Crimpen ist hauptsächlich auf Stahldrahtschläuche wie GB / T10544, EN856 und SAE anwendbar.
(3) Internes und externes Abisolieren und Crimpen von Gummi: Die innere und äußere Gummischicht müssen auf eine bestimmte Länge (die Dicke des inneren und äußeren Gummis) abgestreift werden, die Stahldrahtschicht und die innere Gummischicht werden zu einer Welle extrudiert Form, allgemein geeignet für GB / T10544, EN856-R13, R15 usw. Technische Daten (32 oder mehr einschließlich 32) Ultrahochdruck-Stahldraht-Spiralschlauch.
1.2. Quellenschlauchanschluss
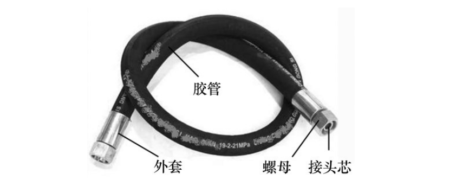
Die Schlauchverbindung mit Quellensteuer besteht hauptsächlich aus dem Verbindungskern, dem Außenmantel (Mutter ist ein optionales Teil) und anderen Teilen.
1) Materialien, Typen und Eigenschaften des Verbindungskerns
Üblicherweise werden für Verbindungskerne 20, 35 und 45 Stähle verwendet. Für gerade Verbindungskerne werden häufig 35 und 45 Stähle verwendet, die eine starke Verformungsbeständigkeit aufweisen. In Anbetracht der Herstellbarkeit von Biegeverbindungskernen werden im Allgemeinen 20 oder 35 Stähle verwendet.
Mit der Verbreitung der Heißbiegetechnologie können 35- und 45-Stähle auch für Ellbogengelenkkerne verwendet werden.
Die strukturellen Eigenschaften des Verbindungskerns hängen eng mit der Crimpform des Schlauchs zusammen, und gemäß der Regelmäßigkeit der Struktur werden die Arten von Verbindungskernen grob unterteilt in: Zickzackstruktur, rechteckige Struktur, interne Verriegelungsstruktur usw.
(1) Der Fugenkern der Sägezahnstruktur, allgemein als Stacheltyp bekannt, besteht hauptsächlich aus Sägezahnrillen, und der Winkel zwischen der Hypotenuse und der Achse beträgt im Allgemeinen nicht mehr als 20 °.
Die Oberseite der Verzahnung ist bogenförmig oder flach, und die Ebene und die kurze Seite der Verzahnung sind glatte, abgerundete Ecken (0,2 bis 0,5 mm), um eine Beschädigung der inneren Gummischicht des Schlauchs während des Zusammenbaus und des Crimpen zu verhindern.
Der Verbindungskern dieser Struktur weist eine starke Dichtungs- und Abziehfestigkeit auf und wird hauptsächlich für stahldrahtgewickelte Gummischläuche verwendet.
(2) Verbindungskern mit rechteckiger Struktur: Bestehend hauptsächlich aus mehreren rechteckigen Rillen, bilden 5 bis 7 Rillenkörper eine Dichtungsnut, und die Rillentiefe beträgt im Allgemeinen 0,3 bis 0,6 mm.
Die Übergangsfläche zwischen der Oberseite der Nut und der Unterseite der Nut ist im Allgemeinen glatt mit abgerundeten Ecken mit einem Radius von 0,1 mm bis 0,3 mm.
Vermeiden Sie Beschädigungen der inneren Gummischicht des Schlauchs beim Zusammenbau und beim Crimpen. Die Gesamtstruktur ist einfach, mit guter Dichtleistung, aber geringem Auszugswiderstand. Diese Struktur wird häufig für Harzschläuche, geflochtene Stahldrahtschläuche und andere Arten von Schläuchen verwendet.
Üblicherweise werden für Verbindungskerne 20, 35 und 45 Stähle verwendet. Für gerade Verbindungskerne werden häufig 35 und 45 Stähle verwendet, die eine starke Verformungsbeständigkeit aufweisen. In Anbetracht der Herstellbarkeit von Biegeverbindungskernen werden im Allgemeinen 20 oder 35 Stähle verwendet.
Mit der Verbreitung der Heißbiegetechnologie können 35- und 45-Stähle auch für Ellbogengelenkkerne verwendet werden.
Die strukturellen Eigenschaften des Verbindungskerns hängen eng mit der Crimpform des Schlauchs zusammen, und gemäß der Regelmäßigkeit der Struktur werden die Arten von Verbindungskernen grob unterteilt in: Zickzackstruktur, rechteckige Struktur, interne Verriegelungsstruktur usw.
Mit der rasanten Entwicklung der chinesischen Baumaschinen ist die Zuverlässigkeit von Hydraulikschlauchleitungen zu einem der am meisten besorgniserregenden Themen in der Branche geworden.
Die Hydraulikschlauchanordnung ist ein Grundelement im Hydraulikgetriebesystem. Die Qualität der Schlauchleitung wirkt sich direkt auf die Leistung des Hydrauliksystems und des Hauptmotors aus. Ein Teil des Versagens der Schlauchleitung beruht auf der Struktur des Verbindungskerns.
Der Schlauchverbindungskern besteht hauptsächlich aus zwei Teilen. Einer ist die Verbindungsstruktur, die hauptsächlich auf SAE-Standards, ISO-Standards und KES-Standards basiert. Der andere Teil ist die Struktur des Crimpteils (Heckstruktur), die mit dem Außenmantel und den inneren und äußeren Gummischichten des Schlauchs abgestimmt ist, um eine zuverlässige Crimpverformung zu bilden, um die Leistung der Schlauchanordnung zu erfüllen.
Wenn die Struktur des Crimpteils des Verbindungskerns bei der Konstruktion verschiedener Schlauchtypen nicht zumutbar ist, treten weitgehend Probleme mit der Produktqualität auf.
Daher sind auch die Arten von (entworfenen) Verbindungskernen, die für Schläuche in verschiedenen Arbeitsumgebungen ausgewählt werden, unterschiedlich, und eine vernünftige Konstruktion kann das Auftreten von Fehlern vermeiden oder verringern.
Mit der rasanten Entwicklung der chinesischen Baumaschinen ist die Zuverlässigkeit von Hydraulikschlauchleitungen zu einem der am meisten besorgniserregenden Themen in der Branche geworden.
Die Hydraulikschlauchanordnung ist ein Grundelement im Hydraulikgetriebesystem. Die Qualität der Schlauchleitung wirkt sich direkt auf die Leistung des Hydrauliksystems und des Hauptmotors aus. Ein Teil des Versagens der Schlauchleitung beruht auf der Struktur des Verbindungskerns.
Der Schlauchverbindungskern besteht hauptsächlich aus zwei Teilen. Einer ist die Verbindungsstruktur, die hauptsächlich auf SAE-Standards, ISO-Standards und KES-Standards basiert. Der andere Teil ist die Struktur des Crimpteils (Heckstruktur), die mit dem Außenmantel und den inneren und äußeren Gummischichten des Schlauchs abgestimmt ist, um eine zuverlässige Crimpverformung zu bilden, um die Leistung der Schlauchanordnung zu erfüllen.
Wenn die Struktur des Crimpteils des Verbindungskerns bei der Konstruktion verschiedener Schlauchtypen nicht zumutbar ist, treten weitgehend Probleme mit der Produktqualität auf.
Daher sind auch die Arten von (entworfenen) Verbindungskernen, die für Schläuche in verschiedenen Arbeitsumgebungen ausgewählt werden, unterschiedlich, und eine vernünftige Konstruktion kann das Auftreten von Fehlern vermeiden oder verringern.
(3) Gelenkkern der internen Verriegelungsstruktur, auch als Anti-Auszieh-Struktur bekannt.
Diese Art von Struktur wurde speziell entwickelt, um zu verhindern, dass der Schlauch aus der Schlauchverbindung herausgezogen wird, und die Dichtheit wird durch die rechteckige Struktur sichergestellt.
Daher ist der Verbindungskern der inneren Verriegelungsstruktur tatsächlich eine Kombination aus der Anti-Auszieh-Struktur und der rechteckigen Struktur.
Diese Art von Verbindung zeichnet sich durch hohe Zuverlässigkeit und lange Lebensdauer aus. Es wird hauptsächlich für Stahldrahtwicklungsschläuche mit ultrahohem Druck und großem Durchmesser sowie für dynamische Stahldrahtwickelschläuche unter rauen Arbeitsbedingungen verwendet.
2) Material, Typ und Eigenschaften der Außenkappe
Das Material des Außenmantels besteht im Allgemeinen aus 20 Stahl, und die gute plastische Verformung des Materials wird verwendet, um den extrudierten Gummischlauch des Außenmantelzahns und die Dichtungsdichtung des Verbindungskerns herzustellen.
Es gibt auch viele Arten von Außenkappen, hauptsächlich für verschiedene Verbindungskerne, verschiedene Arbeitsumgebungen, verschiedene spezifische Arbeitsbedingungen und verschiedene erforderliche Strukturformen.
Normalerweise besteht die Innenseite der Jacke aus einigen Rillen oder Zacken. Es gibt quadratische Rillen, Trapezoide, Zickzacke usw., die in Verbindung mit verschiedenen Arten von Verbindungskernen verwendet werden müssen.
Die üblicherweise verwendeten Strukturtypen von Außenkappen werden grob in die folgenden drei Typen unterteilt:
(1) Wellenförmiger Zahnrillenmantel. Die äußere Oberfläche des gewellten Mantels ist hauptsächlich ein glatter Zylinder, und der Winkel zwischen der Hypotenuse des inneren Zahns und der Achse beträgt 25 ° ~ 45 °.
Die radiale Seite und die Hypotenuse sind durch abgerundete Ecken von 0,2 bis 0,5 mm verbunden, die im Allgemeinen aus 3 bis 5 Innenzähnen bestehen. Hauptsächlich geeignet für nicht abblätternde Mittel- und Niederdruckschlauchleitungen, wie Harzrohre und geflochtene Stahldrahtschläuche; Es kann in Verbindung mit einer Sägezahnstruktur und einem Verbindungskern mit rechteckiger Struktur mit schwacher Ausziehfestigkeit und einfacher Verarbeitungstechnologie verwendet werden.
(2) Trapezzahnrillenmantel. Die Außenfläche ist ein glatter Zylinder, und die Innenfläche ist eine Nut mit einer bestimmten Anzahl von Trapezzähnen.
Der Winkel zwischen der Hypotenuse und der Achse beträgt 25 ° ~ 45 °, und jede Verzahnung ist eine rechteckige Rille. Die Oberseite der Verzahnung ist eine Ebene mit einer Breite von 1 bis 2 mm, und die scharfen Ecken werden mit einer abgerundeten Ecke von 0,2 mm überführt.
Es kann in Verbindung mit einem Verbindungskern mit rechteckiger Struktur verwendet werden, um einen effektiven Auszugswiderstand zu bilden, der zum Abisolieren von geflochtenen Rohren und Wickelrohren mit mittlerem und hohem Druck geeignet ist.
(3) Alveolarabdeckung. Die äußere Oberfläche ist eine T-förmige Rille, die der inneren Zahnversetzung entspricht, und die innere Oberfläche ist eine Rille mit einer bestimmten Anzahl von bilateralen trapezförmigen Zähnen.
Es ist für die Verwendung mit dem Verbindungskern der inneren Verriegelungsstruktur geeignet und wird für die Montage von Schläuchen mit ultrahohem Druck und großer Durchflussrate verwendet.
Mit der schrittweisen Entwicklung von Großbaumaschinen entwickelt sich auch das Hydrauliksystem ständig in Richtung Hochdruck, und die Anwendung dieser Strukturform wird immer umfangreicher.
2. Auswahl des Kräuselungsgrades der Verbindung
Je nach Schlauchtyp und Verbindungstyp ist die geeignete Crimpmenge auch ein Schlüsselfaktor, um sicherzustellen, dass die Schlauchleitung störungsfrei ist.
Das Ausmaß des Crimpen wirkt sich direkt auf die Dichtleistung, die Abzugsfestigkeit und die Lebensdauer aus.
Überprüfen Sie im Allgemeinen bei der Beurteilung der Qualität der Crimpverformung, ob der Spalt zwischen der inneren Zahnoberfläche der Außenhülse und der Zahnnut des Gelenkkerns durch den Gummischlauch gefüllt ist.
Nur wenn die Verformung erfüllt ist, kann der Auszugswiderstand und die Dichtleistung garantiert werden.
Im Allgemeinen sollte die Crimpmenge des inneren Gummischlauchs wie Nitrilkautschuk die innere Gummischichtkompression bewirken (40% ~ 45% für Stahldrahtgeflechtschlauch, 50% ~ 55% für vierschichtigen und sechsschichtigen Stahldrahtschlauch); Die Crimpmenge des Harzrohrs und des PTFE-Schlauchs stellt sicher, dass die Kompressionsmenge der inneren Gummischicht 25% bis 30% beträgt.
Bei der Sicherstellung der Versiegelung ist es umso besser, je geringer die Höhe der Quellensteuer ist. Durch Berechnung und Überprüfung wird ein bestimmter Betrag der Quellensteuer ausgewählt.
3. Fazit
Der Artikel beschreibt die Arten von Verbindungskernen und Außenkappen, die in der Quellenschlauchanordnung verwendet werden.
Wenn das Crimpen des Schlauchs Qualitätsprobleme und die Arten von Fehlern aufweist.
Analysierte die Gründe und die Verwendung einer angemessenen Crimpkonfiguration und Crimpverbindungen, um das Problem einer geringen Leistung der Schlauchleitung zu vermeiden, die durch eine unzumutbare Crimpstruktur des Schlauchs verursacht wird.
Verbessern und kontrollieren Sie effektiv die Zuverlässigkeit der Schlauchleitung und unterstützen Sie die schnelle Entwicklung verschiedener hydraulischer Maschinen.
Ikin-Fluid
—— Top-3-Hersteller in China, spezialisiert auf hydraulische Testpunkte
Vorteile, die Sie finden können In Ikin
Fabrikpreis und niedriges moq
zuverlässige Qualität, Lieferant für Eaton, Hawee und so weiter
100% Leckageinspektion Bevor Sie fertig sind
3 Jahre Garantie
10 Werktage für Massenversand
passend zu anderen Ausstattungen wie Minimess, Stauff und so weiter
Konusdichtungsdesignstruktur, stabile und lange Lebensdauer
Holen Sie sich Ihre kostenlose Probe
in 2 Tagen
*Wir respektieren Ihre Vertraulichkeit und alle Informationen sind geschützt.
Wartung und Verwaltung des Hydrauliksystems der Extrusionspresse
Wartung und Verwaltung des Hydrauliksystems der Extrusionspresse
Mit großen Aluminium-Extrusionspressen können hochspezifizierte Aluminium-Extrusionsprodukte wie Industrieprofile, Schienenverkehrsprofile und große Heizkörper hergestellt werden.
Es kann in der Luft- und Raumfahrt, im Schienenverkehr, in Automobilen, Schiffen, im Baugewerbe, im Maschinenbau, in der elektronischen Energieversorgung und in anderen Bereichen eingesetzt werden. Um die Arbeitsgenauigkeit und die hohe Leistung zu gewährleisten, muss beim Arbeitsprozess einer großen Aluminium-Extrusionspresse ein gewisses Maß an Stabilität gewährleistet sein. Sobald die Stabilität des Extruders nicht den Produktionsstandards entspricht, wird die Qualität der hergestellten Produkte stark beeinträchtigt. Und Unternehmen werden auch enorme wirtschaftliche Verluste erleiden.
一. Häufige Probleme des Hydrauliksystems einer großen Aluminium-Extrusionspresse und deren Lösungen
(一) Rohrleckage:
Die Schweißposition des Rohrs und des Flansches führt höchstwahrscheinlich zu Rohrleckagen. Darüber hinaus ist es sehr wahrscheinlich, dass die Installationsfläche des Rohrflansches und die Schraubenposition zu Rohrleckagen führen.
Das Auftreten von Rohrleckagen wird hauptsächlich durch das Lösen der Schrauben- und Rohrverbindungen im Langzeitbetrieb verursacht. Gleichzeitig wird der Dichtungsring beschädigt, nachdem die Dichtung der Flanschmontageoberfläche gealtert ist.
Unsachgemäßes Schweißen verursachte Poren und Risse, und es traten Leckagen auf. Darüber hinaus war die Nutzungsdauer zu lang, das Sicherheitsbewusstsein war nicht stark und es wurde keine rechtzeitige Wartung durchgeführt, was dazu führte, dass sich die Situation ausdehnte und schließlich zu Undichtigkeiten führte. Wir können Rohrvibrationen beseitigen und die Stabilität verbessern, indem wir Rohrschellen und -halterungen hinzufügen.
Wenn der Schweißvorgang nicht standardisiert ist, es Poren oder Risse gibt, können wir in der ursprünglichen Position polieren und nachdem der Schmutz entfernt wurde, können wir wieder schweißen.
(二) Ölleckage im Zylinder:
1. Die Häufigkeit von Ölzylinderleckagen ist relativ hoch. Aufgrund der Langzeitarbeitsbedingungen wird zwangsläufig eine große Menge an Schleifpartikeln verursacht. Gleichzeitig ist es unvermeidlich, dass eine große Menge Staub und Aluminiumpulver anhaftet, da die freiliegende Position der Kolbenstange für lange Zeit der Luft ausgesetzt ist.
In solchen Situationen wird normalerweise ein Staubring zum Herauskratzen verwendet. Angesichts der Wirkung des Staubrings ist es jedoch schwierig, vollständig abzukratzen, so dass die Kolbenstangendichtung beschädigt wird, was wiederum zu Undichtigkeiten führt. Daher werden normalerweise zwei Behandlungsmethoden für die Leckage von Ölzylindern angewendet: Reinigen Sie zuerst den Ölzylinder und ersetzen Sie die Dichtungen. Zweitens überprüfen Sie, ob die Oberflächenschicht der Kolbenstange abgenutzt ist oder nicht.
2. Die Achse des Zylinders verläuft nicht parallel zur Führungsschiene, und der Fehler überschreitet den Standardbereich: 0,04 bis 0,08 mm / m. Die Befestigungsschrauben der Endabdeckung wurden gelöst und die Dichtung versagte. Dann müssen wir die Parallelität aufrechterhalten und den Fehler innerhalb des Standardbereichs kontrollieren.
3. Die Dichtung ist gebrochen und die Ölleckage tritt aufgrund des Gegendrucks auf und die Druckeinstellung ist zu hoch. Das Siegel ist wiederum einem übermäßigen Druck ausgesetzt und das Siegel ist gebrochen. Dies erfordert das Zurücksetzen des Hydrauliksystemdrucks und das Testen der Hydrauliksteuerventilkomponenten.
4. Die Dichtungen sind stark abgenutzt und versagen, weil das Hydrauliköl stark verschmutzt ist und viele Verunreinigungen erzeugt. Wenn die Öltemperatur lange Zeit auf einer hohen Temperatur liegt, wird das Hydrauliköl allmählich oxidiert, was zur Bildung kolloidaler Ablagerungen führt. Wenn sich die Öltemperatur längere Zeit in einem Niedrigtemperaturzustand befindet, geht die Elastizität der Dichtung verloren. Die Alterung der Dichtung wird durch die Ansammlung einer großen Menge von Ölrückständen verursacht.
Dann müssen wir das Management von Hydrauliköl stärken und das Eindringen von Verschmutzungsquellen streng kontrollieren. Überprüfen Sie den Betriebszustand des Kühlsystems der Hydraulikausrüstung und stellen Sie den normalen Betrieb sicher. Die am besten geeignete Temperatur ist 30-45 ° C.
5. Wenn die geeignete Dichtung für die Dichtungsbehandlung nicht ausgewählt ist, wenn Sie die Dichtung auswählen. Um das Material, das Modell und die Rauheit der Dichtung zu berücksichtigen, tritt Ölleckage auf. Identifizieren Sie daher bei der Auswahl der Dichtungen sorgfältig die Eigenschaften der Dichtungen und wählen Sie die entsprechenden angemessenen Dichtungen aus.
(三) Leckage von Steuerventilkomponenten:
Interne Leckage tritt am häufigsten bei Leckagen von Steuerventilkomponenten auf. Die Hauptursache für interne Leckagen ist die große Ansammlung von hydraulischen Verunreinigungen, die wiederum die Steuerventilkomponenten blockieren. Darüber hinaus kann ein übermäßiger Verschleiß des Ventilkerns und ein unsachgemäßes Schließen zu Undichtigkeiten führen.
Übermäßiger Druck führt zu einer hydraulischen Klemmung der Spule, was ebenfalls zu Undichtigkeiten führt. Es wird empfohlen, das Steuerventil nach der Demontage wiederholt zu reinigen oder die Steuerventilkomponenten zu polieren. Um die Genauigkeit zu verbessern und das ursprüngliche Erscheinungsbild wiederherzustellen.
(四) Ausfall des Magnetventils: Der Ausfall des Magnetventils kann in folgende Typen unterteilt werden:
1. Die Spule bewegt sich nicht: (1) Ein Versagen des Elektromagneten in Kombination mit Vibration und Magnetfelderkennung zeigt, dass sich die Spule nicht bewegt. (2) Der Ventileinsatz ist festgeklemmt, das Öl wechselt und die Rückstellfeder ist defekt. Nach der Vibrationserkennung ist ein Versagen des Ventilkerns erkennbar.
2. Großer Druckverlust: (1) Der Durchfluss ist zu groß und die Größe ist falsch, was durch gemeinsame Inspektion von Vibration und Magnetfeld festgestellt werden kann. (2) Die Spule bewegt sich nicht an Ort und Stelle, und der Spulenstaufehler kann durch Vibrationserkennung erkannt werden.
3. Magnetflussleckage: Auf der Oberfläche der elektromagnetischen Spule treten Defekte auf, die durch Magnetfelderkennung erkannt werden können.
4. Schock (Vibration): Die Schließgeschwindigkeit der Spule ist zu hoch und die Schrauben sind locker, was durch die Vibrationserkennung erkennbar ist.
Ergreifen Sie angesichts der Ursachen der oben genannten Probleme entsprechende Maßnahmen, um das Problem zu lösen.
二. Wartung und Management des Hydrauliksystems einer großen Aluminium-Extrusionspresse
(一) Erstellen Sie einen täglichen Wartungsplan
(1) Reinigen Sie einige Geräte, die längere Zeit der Luft ausgesetzt waren, regelmäßig, um die freiliegenden Teile des Geräts sauber und frei von Verunreinigungen zu halten.
(2) Halten Sie die Betriebsumgebung sauber und ordentlich, um das Eindringen von Staub und Schmutz zu vermeiden und das Hydrauliksystem zu verschmutzen.
(3) Führen Sie Patrouilleninspektionen jederzeit durch, wenn die Ölleckrate relativ hoch ist, und ergreifen Sie nach ihrer Feststellung entsprechende Maßnahmen, um sie sofort zu beheben.
(4) Standardisieren Sie den Inspektionsprozess. Beschreiben Sie den Inspektionsweg und den höchsten Teil des Ölverschmutzungspunkts. Nach Abschluss einer bestimmten Phase der Inspektionsarbeiten wird diese dem Personal der nächsten Phase übergeben, und der Arbeitsfortschritt der vorherigen Phase wird ausführlich erläutert.
(5) Notieren Sie den ursprünglichen Betriebsstatus im Detail. Das Verständnis der normalen Arbeitsbedingungen des Hydrauliksystems kann dazu beitragen, Probleme rechtzeitig während des Inspektionsprozesses zu erkennen und zu lösen, die Arbeitseffizienz zu verbessern und Sicherheitsrisiken zu vermeiden.
(二) Entwickeln Sie ein regelmäßiges Wartungs- und Inspektionssystem und legen Sie einen Termin für die Kalibrierung verschiedener Instrumente des Hydrauliksystems fest. Stellen Sie sicher, dass das Messgerät ordnungsgemäß funktioniert und ein hohes Maß an Genauigkeit aufweist.
Gleichzeitig sollte das Hydrauliksystem druckgeprüft werden, um einen angemessenen Druckwert zur Aufrechterhaltung der normalen Temperatur einzustellen. Um ein Druckungleichgewicht zu vermeiden, ist die Temperatur zu niedrig oder zu hoch, was zu Undichtigkeiten führt. Reinigen und ersetzen Sie das Filterelement regelmäßig, um die Zusammensetzung von Schmutz und Hydraulikölverschmutzung zu bestimmen.
Überprüfen Sie den Verschleißgrad und das Verschleiß des Hydrauliksystems und prüfen und testen Sie das Hydrauliköl des Extruders alle drei Monate. Überprüfen Sie die Hydraulikölviskosität, den Säurewert, die Feuchtigkeit, Partikel und andere Gegenstände, damit angemessene Maßnahmen zur Lösung dieser Probleme getroffen werden können.
三. Fazit
Durch Analyse kann bestätigt werden, dass die Leckage des Hydrauliksystems der Aluminium-Extrusionspresse hauptsächlich durch die mangelnde Stabilität des Hydrauliksystems verursacht wird. Wir müssen also entsprechende Maßnahmen ergreifen.
Lösungen sind jedoch immer auf Abhilfemaßnahmen zurückzuführen und können keine vorbeugende Wirkung haben.
Daher ist es von großer Bedeutung, die notwendige Wartung und Verwaltung des Hydrauliksystems in der täglichen Arbeit zu übernehmen.
Ventile Flansche Fluid Design Produkte Hydraulik Flansch Armaturen bspp Hydraulik Armaturen Ventil Flansche Schnellkupplungen Fluid Ventil American Fluid Power Schnellkupplungen Hydraulik Test Armaturen Hydraulik Druck Test Armaturen Hydraulik Testschlauch Hyd Test Armaturen Hydraulik Test Anschluss Armaturen Katze Hydraulische Test Armaturen John Deere Hydraulische Test Armaturen hydraulische Prüfmanometeranschlüsse hydraulische Prüfschlauchanschlüsse hitachi hydraulische Prüfanschlüsse jcb hydraulische Prüfanschlüsse jic hydraulische Prüfanschlüsse hydraulische Prüfanschlüsse komatsu hydraulische Prüfanschlüsse metrische hydraulische Prüfanschlüsse hydraulische Prüfpunktanschlüsse hydraulische Prüfpunktanschlüsse Raupe ar hydraulische Prüfanschlussarmaturen Parker hydraulische Prüfanschlussarmaturen Parker hydraulische Prüfanschlüsse Parker hydraulische Prüfanschlüsse stauff hydraulische Prüfanschlüsse hydraulische Prüfanschlüsse volvo hydraulische Prüfanschlüsse Manometeranschluss Hydraulikflüssigkeitsprüfpunkt Parkeranschlüsse Verbindungsgewinde Prüfpunkt hydraulische Prüfanschlussarmaturen hydraulische Kupplung und Schlauchprüfung Kupplung Druckprüfpunkt Hydraulikzubehör Schlauchprüfbaugruppen Prüfpunktanschlüsse Prüfpunktschläuche Manometeranschlüsse Prüfkupplungen zur Druckprüfung
Was ist die Anwendung des hydraulischen Drehpunktes
Was ist die Anwendung des hydraulischen Drehpunktes
Das hydraulische Antriebssystem ist aufgrund seiner vielen Vorteile im industriellen Bereich weit verbreitet. Wenn das rotierende Gerät Hydraulikmedium als Übertragungsleistung verwenden muss, gibt es strenge Anforderungen an den Druck und die Steuergenauigkeit des Hydraulikmediums, normalerweise einen Druck über 30 MP, und einen zuverlässigen Betrieb.
Für die Entwicklung und Anwendung von Drehpunkten ist es notwendig, die Struktur der Ausrüstung zu vereinfachen und gleichzeitig eine bessere Umwandlungsfunktion zu erreichen. Die umfangreichste und typischste Anwendung von hydraulischen Drehpunkten sind die warmgewalzten Breitband-Stahlwickler von Stahlwalzgeräten. Und auf den Expansions- und Kontraktionszylindern von Abwicklern, Wicklern und anderen Geräten auf der Produktionslinie für kaltgewalzte Bänder.
1. Strukturprinzipanalyse des hydraulischen Drehpunktes
1.1 Struktur und Prinzip
Der hydraulische Drehpunkt hat zwei Steuerölanschlüsse und einen Ablassanschluss, die jeweils mit den festen Rohrleitungen des Hydrauliksystems verbunden sind. Jede externe Rohrleitung ist statisch mit der Hülle des Drehpunkts verbunden.
Die Schale des hydraulischen Drehpunkts ist auf der Schale der passenden Hauptausrüstung befestigt und bleibt relativ statisch mit der Basis der Hauptausrüstung, die über den Dorn mit der Hauptausrüstung verbunden ist. Der Abstand zwischen dem Außendurchmesser des Dorns und dem Innendurchmesser des hydraulischen Drehgelenks. Der Spalt zwischen dem Zylinderrohr und dem Kolben muss der gleiche sein wie der des Hydraulikzylinders, im Allgemeinen 0,04 mm ~ 0,07 mm. Wenn die Bedingungen dies zulassen, senken Sie den Grenzwert so weit wie möglich. Bei jedem Start des Hydrauliksystems bildet sich im passenden Spalt ein statischer Druckölfilm, der den Dorn und das hydraulische Drehgelenk vor Verschleiß schützt und eine Rolle bei der Abdichtung spielt.
Die rotierende Dichtung ist am Dorn des Geräts installiert. Ihre Hauptfunktion besteht darin, den Öleinlasshohlraum und den Ölrücklaufhohlraum zu isolieren, um zwei unabhängige abgedichtete Räume zu bilden. Die meisten Materialien sind verschleißfeste Verbundwerkstoffe oder Metallwerkstoffe. Rotationsdichtungen müssen hohen Drücken über 30 MP standhalten und müssen gegen Hochdruckstöße beständig sein, nicht leicht zu verformen sein und geringe Leckagen aufweisen. Die Rotationsdichtung und die Innenwand des Drehgelenks haben keinen Kontakt, und zwischen beiden besteht Flüssigkeitsreibung.
Die Vibrationen und Stöße, die durch den Hochgeschwindigkeitsbetrieb der Hauptausrüstung erzeugt werden, werden über den Dorn auf das hydraulische Drehgelenk übertragen, was zu einem gewissen Schwingen des Drehgelenks führt. Zwei Lager werden verwendet, um die Axialkraft und Radialkraft zu unterstützen, die durch das Schwingen des Drehgelenkgehäuses erzeugt werden, und um die genaue Positionierung der Gerätekernwelle und des Drehgelenks zu realisieren.
Die Endflächendichtung nimmt eine Skelettlippendichtung an, mit der das aus der rotierenden Dichtung austretende Öl abgedichtet wird. Der austretende Öldruck überschreitet im Allgemeinen nicht 0,3 MP. Sobald die Leckage zunimmt, kann die Enddichtung leicht beschädigt werden und das Hydrauliköl tritt nach außen aus. Der Ölanschluss der Drehgelenkschale ist mit dem Ölanschluss am Dorn des Geräts verbunden.
1.2 Analyse der inneren Dichtungsstruktur
Es gibt zwei Haupttypen von Rotationsdichtungen für Drehpunkte: Verbunddichtungen und Gleitringdichtungen. Die Dichtleistung der Dichtung aus Verbundmaterial ist relativ besser und wird dort eingesetzt, wo der Hydraulikzylinder eine Zwischenposition aufweist. Der mit Verbundwerkstoffen versiegelte Drehpunkt kann den Drehpunkt aufgrund der geringen Größe der Dichtung selbst kompakter und exquisiter machen. Die Kosten für die Verbunddichtung selbst sind viel günstiger als die für die Gleitringdichtung.
Die zusammengesetzte Rotationsdichtung besteht aus zwei Teilen, einer Kombination aus einem Außenring aus PTFE und einem O-Ring aus NBR. Der O-Ring spielt die Rolle des Tragens des Außenrings, wodurch die Installation der gesamten Rotationsdichtung erleichtert wird und zwischen dem Außenring und dem Gehäuse des Drehgelenks gleitet. Die Herstellung von Gleitringdichtungen ist komplizierter, die Präzisionsanforderungen sind ebenfalls relativ hoch und der relative Preis ist relativ hoch.
2. Installation und Wartung von hydraulischen Drehpunkten
Stellen Sie bei der Installation des hydraulischen Drehpunkts am Dorn des Hauptgeräts sicher, dass der Hohlraum des Drehgelenks und der Dorn des Hauptgeräts eine gute Koaxialität aufweisen. Im Allgemeinen ist es erforderlich, dass die Koaxialität zwischen der Achse des Drehgelenks und der Achse des Geräts innerhalb von ± 1 mm / m gesteuert wird. Eine Unkonzentriertheit führt dazu, dass der hydraulische Drehpunkt während einer Hochgeschwindigkeitsdrehung relativ große radiale Schwingungen erzeugt. Die Radialkraft bewirkt, dass das Drehgelenk und der Dorn periodisch in axialer Richtung gleiten. Nicht nur der dynamische Ölfilm wird zerstört und der Verschleiß der Passfläche erhöht, sondern auch die Endfläche der Dichtung wird abgenutzt. Gleichzeitig kann das Lager größeren äußeren Stößen standhalten. Eine schlechte Koaxialität führt daher zu einer großen Beschädigung der inneren rotierenden Dichtung und der Lager und beeinträchtigt die Lebensdauer.
Das Gehäuse des Drehgelenks ist so befestigt, dass es sich nicht synchron mit der Spindel dreht, solange verhindert werden kann, dass es sich im Kreis dreht.
Verwenden Sie keine weiteren Einschränkungen. Die auf die Schale wirkende Radial- oder Axialkraft wird durch die Schale auf das Lager des hydraulischen Drehgelenks und die interne rotierende Dichtung übertragen, wodurch das Lager oder die Dichtung zum Verschleiß oder zur Beschädigung gezwungen wird.
Beachten Sie beim Anschließen externer Ölleitungen strikt die Installationsspezifikationen für Hydraulikgeräte. Insbesondere muss die Sauberkeit jedes Ölanschlusses streng überprüft werden, um zu verhindern, dass äußere Verunreinigungen und bearbeitete Grate in das Drehgelenk gelangen. Aufgrund der komplexen inneren Struktur des Hydraulikdrehgelenks und des geringen Anpassungsspiels können beim Eindringen externer Verunreinigungen in das Hydraulikdrehgelenk leicht Ölfilme, Gleitringdichtungen und Lagerstaus sowie schwerwiegende Leckagen entstehen.
Die Skelettöldichtung des Drehgelenks dient zur Abdichtung des rotierenden Dorns, so dass das austretende Öl der Drehdichtung von der undichten Ölleitung zum Öltank abgelassen wird. Der Druckwiderstand der Öldichtung beträgt normalerweise nicht mehr als 3 bar, daher muss die undichte Ölleitung reibungslos zum Öl zurückgeführt werden.
Während der Installation darf der undichte Ölanschluss des Drehgelenks nicht blockiert werden. Befindet sich ein Ventil an der undichten Ölleitung, muss es vor dem Einbringen des Mediums geöffnet werden, da sonst die Öldichtung zwangsläufig herausgedrückt wird. Es ist auch nicht möglich, die undichte Ölleitung in die Ölrücklaufleitung einzubauen, da der Druck der Ölrücklaufleitung normalerweise 3 bar überschreitet. Installieren Sie keinen Filter an der undichten Ölleitung. Drehgelenke weisen normalerweise Undichtigkeiten auf, sodass sie nicht verwendet werden können, wenn Druck erforderlich ist. Die Leckage von Gleitringdichtungen ist größer.
Eine Servosteuerung kann in Betracht gezogen werden, wenn der Hub des Hydraulikzylinders gesteuert werden muss, um die Leckage auszugleichen. Wenn der Hydraulikzylinder nicht in der Mitte positioniert ist, ist das Problem einfacher, solange der Hydraulikzylinder das Medium weiter liefert, nachdem sich der Hydraulikzylinder in die Endposition bewegt hat.
Drehgelenke werden im Allgemeinen mit Medium geschmiert und gekühlt, so dass es nicht möglich ist, zu testen oder zu fahren, ohne das Medium zu passieren. Stellen Sie sicher, dass die undichte Ölleitung nach der Überholung des Drehgelenks oder der zugehörigen Ausrüstung geöffnet ist. Der Verschleiß oder die Beschädigung von hydraulischen Drehgelenken kann durch Messung der Leckage abgeschätzt werden. Die Leckage von Drehgelenken sollte regelmäßig überwacht und verfolgt werden, um die Betriebsbedingungen von Drehgelenken zu überwachen.
3. Häufige Fehler von hydraulischen Drehgelenken
Im tatsächlichen Gebrauch weisen hydraulische Drehgelenke hauptsächlich zwei Arten von Fehlern auf. Ein Fehler äußert sich in einer inneren Lagerschädigung des Drehgelenks und der andere in einer äußeren Leckage des Drehgelenks.
Analysieren Sie die Ursachen für interne Lagerschäden. Es gibt drei Hauptpunkte:
1) Das Hydrauliköl weist während des Einbaus oder während des Gebrauchs eine schlechte Sauberkeit und Körnigkeit auf, was zu ernsthaftem Verschleiß und Versagen der Wälzkörper des Lagers führt.
2) Wenn das Drehgelenk installiert ist, werden die Anforderungen an die Installationsgenauigkeit nicht erfüllt, was zu einer ungleichmäßigen Kraft unter dem statischen Lastzustand des Lagers und einem übermäßigen Vibrationswert unter dem dynamischen Lastzustand führt, wodurch das Lager beschädigt wird.
3) Das ausgewählte Design und die Fertigungsqualität des hydraulischen Drehgelenks entsprechen nicht den Anforderungen der Arbeitsbedingungen des Geräts. Die Gründe für eine Leckage außerhalb des Drehgelenks sind:
Die Bearbeitungsgenauigkeit der Passfläche der Installationsdichtung ist gering, was die Genauigkeitsanforderungen der Dichtung nicht erfüllen kann.
Die Auswahl und Installation der Dichtung ist nicht für die Anforderungen der Arbeitsbedingungen geeignet;
Die Einbaugenauigkeit des Drehgelenks ist schlecht, was zu übermäßigen Vibrationen und Schäden an der Dichtung führt.
4. Fazit
In praktischen Anwendungen aufgrund der komplexen Arbeitsbedingungen der Hauptausrüstung und der veränderlichen Umgebung. Bei der Auswahl einer bestimmten Anwendung sollte ein Drehgelenk ausgewählt werden, das für einen weiten Lastbereich geeignet ist und den jeweiligen Arbeitsbedingungen entspricht. Um die Anforderungen der Hauptausrüstung von Niederdruck und niedriger Geschwindigkeit bis zu hohem Druck und hoher Geschwindigkeit in einem weiten Bereich von Arbeitsbedingungen zu erfüllen. Das hochpräzise hydraulische Drehgelenk mit Gleitringdichtung kann den Zweck einer geringen Leckage, eines zuverlässigen und dauerhaften Betriebs besser verwirklichen.
Durch die Verbesserung der Verarbeitungsgenauigkeit und der technischen Anforderungen der Teile sowie die Verbesserung der Installationsgenauigkeit kann die Fähigkeit des Drehgelenks, sich an hohe Geschwindigkeit und hohen Druck anzupassen, erheblich verbessert und die Lebensdauer verlängert werden.
Hydraulischer Testpunkt Hydraulische Testkupplung DRUCKTESTKUPPLER Parker EMA-Kupplungen Testanschlusskupplungen Hydraulischer Testanschluss Hydraulischer Testadapter Kit Hydraulischer Testsatz Testkupplung Drucktestpunkt Hydraulisches Zubehör Schlauchprüfbaugruppen Testpunktanschlüsse Testpunkt Schläuche Manometeranschlüsse Testkupplungen für die Druckprüfung Tragbar Hydraulikinstrumente für die Druckprüfung Schlauch für Hochdruckarmaturen Schlauchendarmaturen HYDRAULISCHE PRÜFPUNKTKUPPLUNG Hydraulikzubehör Hersteller für Hydraulikarmaturen Standardhydraulikarmaturen Hydraulikteststecker Hydrauliktest-T-Stücke JIC-Testpunkt Hydraulische Passform tings Katalog Hydraulikarmaturen JIC Manometeranschluss Hydraulikflüssigkeit Testpunkt Parker Armaturen Verbindungsgewinde Testpunkt Hydraulikprüfanschluss Armaturen Hydraulikkupplung und Schlauch Mini-Hydraulikpressen Stoßventile Pressventile Flanschventil Testpunkt Fluid Hydraulik Flüssigkeitsanschlüsse Hydraulik-Schnellkupplungen